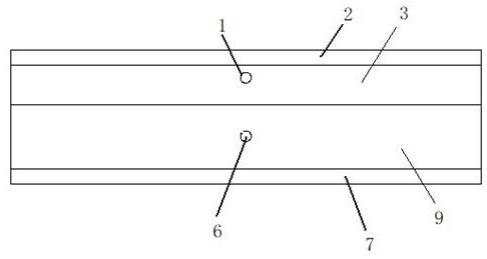
1.本发明涉及塑性成形加工技术领域,具体是一种深腔型复杂型面钛合金零件超塑成形模具。
背景技术:2.由于钛合金具有比强度高、耐腐蚀等特点,广泛应用于航空、航天、化工、船舶和医疗等领域。特别是近年来航空、航天领域对钛合金钣金零件的需求显著增加,因此对成形模具的需求也呈明显的上升趋势。钛合金在力学性能上具有屈强比高、弹性模量小等特点,反映在成形上为变形范围窄、易开裂、回弹大和尺寸精度难于保证。为克服上述钛合金成形难点,使用超塑成形技术对钛合金进行加工,本发明提供的超塑成形模具及成形方法使用气胀超塑成形,使深腔形复杂型面的钛合金板材零件经过一个超塑成形工序即可达到型面贴合、不起皱、厚度均匀的合格工件,解决了原有刚性上下模压制产生的褶皱、局部严重减薄和回弹大导致零件外形尺寸超差问题。
技术实现要素:3.为解决上述问题,本发明提供一种深腔型复杂型面钛合金零件超塑成形模具,通过产用气胀成形代替原有的刚性上下模压制,解决了原有方法易产生的褶皱、局部严重减薄和回弹大导致零件外形尺寸超差问题。
4.本发明采用的技术方案是:一种深腔型复杂型面钛合金零件超塑成形模具,包括上模和下模,所述上模前端设有一个进气孔,所述下模前端设有一个排气孔,所述上模压合面的短边处设有第一凹槽,所述第一凹槽处通过螺栓固定有导向板,所述下模压合面上设有与第一凹槽位置对应的第二凹槽,上下模合模时,通过导向板插入第二凹槽精确定位上下模相对位置。
5.优选的,所述上模压合面上设有毛料定位销孔,所述下模压合面上设有毛料定位挡销,所述毛料定位销孔和毛料定位挡销在成形过程中对毛料摆放位置进行定位。
6.优选的,所述上模的腔体底部沿着长边向外延伸形成上模压板槽,所述下模的腔体底部沿着长边向外延伸形成下模压板槽。
7.优选的,所述上模的侧端设有两个上模测温孔,用于升降温时监测上模的温度;所述下模的侧端设有两个下模测温孔,用于升降温时监测下模的温度。
8.优选的,所述上模压合面设有零件成形上模压边梗,所述下模压合面设有零件成形下模压边梗。
9.本发明的有益效果是:该超塑成形模具使深腔形复杂型面的钛合金板材零件经过一个超塑成形工序即可达到型面贴合、不起皱、厚度均匀的合格工件,解决了原有刚性上下模压制产生的褶皱、局部严重减薄和回弹大导致零件外形尺寸超差问题,大大提高了零件合格率。
附图说明
10.图1为超塑成形模具主视图;
11.图2为超塑成形模具侧视图;
12.图3为下模内部结构俯视图;
13.图4为上模内部结构俯视图。
具体实施方式
14.为了加深对本发明的理解,下面将结合实施例和附图对本发明作进一步详述,该实施例仅用于解释本发明,并不构成对本发明保护范围的限定。
15.实施例1
16.如图1至图4所示,本发明提供一种深腔型复杂型面钛合金零件超塑成形模具,包括上模3和下模9,上模3前端设有一个进气孔1用于超塑成形时通入氩气;下模9前端设有一个排气孔6,用于超塑成形时抽真空时排气使用;上模3的侧端设有两个上模测温孔5,用于升降温时监测上模的温度;下模9的侧端设有两个下模测温孔8,用于升降温时监测下模的温度。
17.上模3的腔体底部沿着长边向外延伸形成上模压板槽2,下模9的腔体底部沿着长边向外延伸形成下模压板槽7;上模压板槽2和下模压板槽7的设置,为了方便超塑成形机上的压板压紧,从而模具装夹固定在机床上。所述上模3压合面的短边处设有第一凹槽32,所述第一凹槽32处通过螺栓固定有导向板4,所述下模9压合面上设有与第一凹槽32位置对应的第二凹槽92,上下模合模时,通过导向板4插入第二凹槽精确定位上下模相对位置,上模3压合面设有零件成形上模压边梗33,下模9压合面设有零件成形下模压边梗93。
18.其中,上模3压合面上设有两个毛料定位销孔31(下陷一定深度,与下模定位销匹配),下模9压合面上设有两个毛料定位挡销91(突出一定高度),所述毛料定位销孔31和毛料定位挡销91在成形过程中对毛料摆放位置进行定位。
19.本发明的具体超塑成形过程如下:图3超塑成形模具的下模通过超塑成形机固定平台上的压板压紧模具上的下模压板槽7固定在超塑成形机床平台上,图4上模通过超塑成形机上可以升降的面上的压板压紧模具上上模压板槽2固定在上方,首先对模具上下模具合起升温,待模具升温到钛合金零件所需700℃后(温度以tc4材料为例),开启超塑成形机床炉门,上模升起,把零件毛料从图3的前端放入下模中,通过定位挡销91定位毛料放置位置(即放到图3的91定位销挡住的位置),毛料放置到位后关闭机床炉门,预热一定时间(10分钟左右)后进行合模,合模时通过上下模合模导向板4(如图2)精确定位上下模相对位置,合模后采用气源控制系统进行抽真空,使气体从下模的排气孔6排出,待真空度达到小于0.01mpa后,由上模进气孔1往模腔10中通入流动氩气,使上下模腔中氩气保持在0.1mpa,模具继续升温至850℃后加载成形压力曲线,加载完成后采用最大压力保压10分钟,保压结束后进行泄压,泄压后模具开始降温,待温度降至650℃以下取出零件,待零件冷却后在切割设备上将成形好的的零件切除余量后即可得到最终零件。
20.采用本发明的超塑成形模具进行气胀成形,使深腔形复杂型面的钛合金板材零件经过一个超塑成形工序即可达到型面贴合、不起皱、厚度均匀的合格工件,解决了原有刚性上下模压制产生的褶皱、局部严重减薄和回弹大导致零件外形尺寸超差问题,大大提高了
零件合格率。而且利用钛合金超塑胀形技术制造的航空结构件,既提高了结构的抗疲劳、抗腐蚀特性,又满足质量轻、强度高的目标。
21.在本申请的描述中,需要理解的是,术语“上”、“下”、“前”、“后”、“左”、“右”、“竖直”、“水平”、“顶”、“底”、“内”、“外”等指示的方位或位置关系为基于附图所示的方位或位置关系,仅是为了便于描述本申请和简化描述,而不是指示或暗示所指的装置或元件必须具有特定的方位、以特定的方位构造和操作,因此不能理解为对本申请的限制。
22.以上对本发明的具体实施例进行了描述。需要理解的是,本发明并不局限于上述特定实施方式,本领域技术人员可以在权利要求的范围内做出各种变化或修改,这并不影响本发明的实质内容。在不冲突的情况下,本申请的实施例和实施例中的特征可以任意相互组合。
技术特征:1.一种深腔型复杂型面钛合金零件超塑成形模具,其特征在于,包括上模(3)和下模(9),所述上模(3)前端设有一个进气孔(1),所述下模(9)前端设有一个排气孔(6),所述上模(3)压合面的短边处设有第一凹槽(32),所述第一凹槽(32)处通过螺栓固定有导向板(4),所述下模(9)压合面上设有与第一凹槽(32)位置对应的第二凹槽(92 ),上下模合模时,通过导向板(4)插入第二凹槽精确定位上下模相对位置。2.根据权利要求1所述的一种深腔型复杂型面钛合金零件超塑成形模具,其特征在于,所述上模(3)压合面上设有毛料定位销孔(31),所述下模(9)压合面上设有毛料定位挡销(91),所述毛料定位销孔(31)和毛料定位挡销(91)在成形过程中对毛料摆放位置进行定位。3.根据权利要求1所述的一种深腔型复杂型面钛合金零件超塑成形模具,其特征在于,所述上模(3)的腔体底部沿着长边向外延伸形成上模压板槽(2),所述下模(9)的腔体底部沿着长边向外延伸形成下模压板槽(7)。4.根据权利要求1所述的一种深腔型复杂型面钛合金零件超塑成形模具,其特征在于,所述上模(3)的侧端设有两个上模测温孔(5),用于升降温时监测上模的温度;所述下模(9)的侧端设有两个下模测温孔(8),用于升降温时监测下模的温度。5.根据权利要求1所述的一种深腔型复杂型面钛合金零件超塑成形模具,其特征在于,所述上模(3)压合面设有零件成形上模压边梗(33),所述下模(9)压合面设有零件成形下模压边梗(93)。
技术总结本发明公开了一种深腔型复杂型面钛合金零件超塑成形模具,包括上模和下模,所述上模前端设有一个进气孔,所述下模前端设有一个排气孔,所述上模压合面的短边处设有第一凹槽,所述第一凹槽处通过螺栓固定有导向板,所述下模压合面上设有与第一凹槽位置对应的第二凹槽,上下模合模时,通过导向板插入第二凹槽精确定位上下模相对位置。该超塑成形模具使深腔形复杂型面的钛合金板材零件经过一个超塑成形工序即可达到型面贴合、不起皱、厚度均匀的合格工件,解决了原有刚性上下模压制产生的褶皱、局部严重减薄和回弹大导致零件外形尺寸超差问题,大大提高了零件合格率。大大提高了零件合格率。大大提高了零件合格率。
技术研发人员:万丹 束飞 王丙杰 张冬兵 汪洋华 陈朋举 拓建峰 尹恩贝 张允佟 徐龙
受保护的技术使用者:江西洪都航空工业集团有限责任公司
技术研发日:2022.03.29
技术公布日:2022/8/16