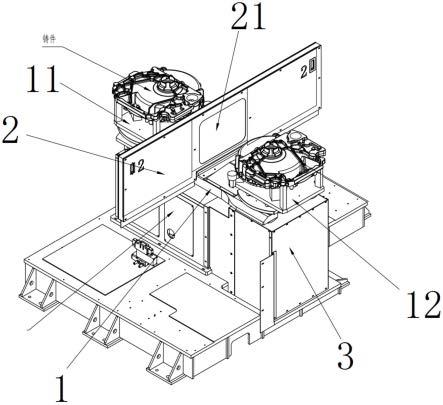
1.本实用新型属于铸件加工领域,尤其是涉及一种用于中大型铸件打磨的气动升降双工位旋转台机构。
背景技术:2.目前现有的铸件加工过程中,在对一个铸件加工完成后,需要将加工好的铸件取出后,在放入一个待加工铸件,这种方式造成了上下料时间过长,降低以打磨效率,因此针对上述的情况亟需一种可以提高打磨效率,节省上下料时间的加工装置。
技术实现要素:3.有鉴于此,本实用新型旨在提出一种用于中大型铸件打磨的气动升降双工位旋转台机构,极大的节省上下料时间,提高打磨效率。
4.为达到上述目的,本实用新型的技术方案是这样实现的:
5.一种用于中大型铸件打磨的气动升降双工位旋转台机构,包括旋转台板,旋转台板上设置有第一加工工位和第二加工工位,第一加工工位和第二加工工位分别设置在旋转台板的两端;
6.旋转台板下方设置有转动机构和升降机构,升降机构用于带动旋转台板提升,转动机构用于带动旋转台板转动。
7.进一步的,第一加工工位与第二加工工位之间还设置有旋转门,旋转门底部与旋转台板固定连接;
8.旋转门上设置有观察视窗。
9.进一步的,旋转台板底部设置有安装支架以及支撑板,支撑板设置在安装支架上方,旋转台板通过支撑板放置在安装支架上;
10.安装支架内部镂空,形成用于放置转动机构和升降机构的容纳空间。
11.进一步的,转动机构设置在旋转台板下方,包括电机安装支架、旋转电机,旋转电机的输出端朝上设置;
12.旋转电机设置在电机安装支架内;
13.旋转台板的底板设置有传动单元,传动单元与旋转台板固定连接,旋转电机的输出端通过带动传动单元间接带动旋转台板转动。
14.进一步的,升降机构设置在转动机构下方,用于带动转动机构以及旋转台板升降;
15.升降机构包括升降导向柱、气缸,还包括设置在电机安装支架侧方的直线轴承,电机安装支架边缘部位向两侧延伸形成用于安装直线轴承的耳板,直线轴承套设在升降导向柱上;
16.气缸的活动端朝上设置,活动端的端部与电机安装支架的底部固定连接。
17.进一步的,升降机构底部设置有安装底板,升降导向柱和气缸的底部设置在安装底板上。
18.进一步的,升降导向柱设有四个,电机安装支架边缘部位向两侧延伸形成用于安装直线轴承的耳板,所述耳板对应设置有四个。
19.进一步的,升降导向柱上还套设有导向柱防护套,用于防止导向柱上附着灰尘。
20.相对于现有技术,本实用新型所述的一种用于中大型铸件打磨的气动升降双工位旋转台机构具有以下有益效果:
21.(1)本实用新型所述的一种用于中大型铸件打磨的气动升降双工位旋转台机构中,双工位打磨工位完成工位互换,极大的节省上下料时间,提高打磨效率。
22.(2)本实用新型所述的一种用于中大型铸件打磨的气动升降双工位旋转台机构,针对升降机构进行优化设计,简化结构,代替原有的丝杠导轨机构因密封不严,进入粉尘而造成整个机构维修问题,维修成本高,而且增加不必要的时间成本。
附图说明
23.构成本实用新型的一部分的附图用来提供对本实用新型的进一步理解,本实用新型的示意性实施例及其说明用于解释本实用新型,并不构成对本实用新型的不当限定。在附图中:
24.图1为本实用新型实施例所述的整体结构示意图;
25.图2为本实用新型实施例所述的双工位局部示意图;
26.图3为本实用新型实施例所述的升降机构和转动机构平面示意图;
27.图4为本实用新型实施例所述的升降机构和转动机构立体示意图。
28.附图标记说明:
29.1-旋转台板;11-第一加工工位;13-第二加工工位;2-旋转门;21-观察视窗;3-安装支架;31-支撑板;4-转动机构;41-电机安装支架;42-旋转电机;43-传动单元;5-升降机构;51-升降导向柱;52-气缸;53-直线轴承;54-耳板;6-安装底板;7-导向柱防护套。
具体实施方式
30.需要说明的是,在不冲突的情况下,本实用新型中的实施例及实施例中的特征可以相互组合。
31.下面将参考附图并结合实施例来详细说明本实用新型。
32.本实用新型是一种用于中大型铸件打磨的气动升降双工位旋转台机构,主要针对一些中大型铸件较大冒口和合模线的切割和打磨,由双工位旋转台机构和气动升降旋转机构组成。双工位旋转机构可以实现第一加工工位11和第二加工工位13的互换,缩短上下料时间,提高打磨效率;气动升降旋转机构可以实现工装治具和铸件一起顶起并落回转台工位,而且顶起之后,可以实现工装夹具和铸件的360
°
旋转。气动升降机构5的优化设计,简化结构,代替原有的丝杠导轨机构因密封不严,进入粉尘而造成整个机构维修问题,维修成本高,而且增加不必要的时间成本。
33.旋转机构,可实现两个工位互换,主要包括双工位旋转台安装支架3,双工位旋转台支撑板31,双工位转台治具安装板、旋转门2,整个机构通过双工位旋转台安装支架3,通过双工位旋台支撑板31,将双工位旋转台机构固定,旋转台板1机构通过电机和减速机驱动,可将双工位旋转台板1上的两个工位旋转360
°
,等第一加工工位11的铸件打磨完后,第
二加工工位13转件旋转360
°
,旋转至打磨工位,开始打磨工序。双工位打磨工位完成工位互换,极大的节省上下料时间,提高打磨效率。
34.气动升降旋转机构,主要由气动升降机构5和旋转机构组成,气动升降机构5由升降气缸52安装板,升降导向柱51、直线轴承53、气缸52、导向柱防护套7组成,直线轴承53安装在升降导向柱51上,通过气缸52升降,将旋转机构顶起和落回,完成整个升降动作,导向柱防护套7对导向柱进行密封,防止粉尘进入,保证其工作平稳性。整个机构的优化设计,使结构更加简单,维护简单、方便,结构灵活,实用性强。
35.最后应说明的是:以上各实施例仅用以说明本实用新型的技术方案,而非对其限制;尽管参照前述各实施例对本实用新型进行了详细的说明,本领域的普通技术人员应当理解:其依然可以对前述各实施例所记载的技术方案进行修改,或者对其中部分或者全部技术特征进行等同替换;而这些修改或者替换,并不使相应技术方案的本质脱离本实用新型各实施例技术方案的范围,其均应涵盖在本实用新型的权利要求和说明书的范围当中。
36.以上所述仅为本实用新型的较佳实施例而已,并不用以限制本实用新型,凡在本实用新型的精神和原则之内,所作的任何修改、等同替换、改进等,均应包含在本实用新型的保护范围之内。
技术特征:1.一种用于中大型铸件打磨的气动升降双工位旋转台机构,其特征在于:包括旋转台板(1),旋转台板(1)上设置有第一加工工位(11)和第二加工工位(13),第一加工工位(11)和第二加工工位(13)分别设置在旋转台板(1)的两端;旋转台板(1)下方设置有转动机构(4)和升降机构(5),升降机构(5)用于带动旋转台板(1)提升,转动机构(4)用于带动旋转台板(1)转动。2.根据权利要求1所述的一种用于中大型铸件打磨的气动升降双工位旋转台机构,其特征在于:第一加工工位(11)与第二加工工位(13)之间还设置有旋转门(2),旋转门(2)底部与旋转台板(1)固定连接;旋转门(2)上设置有观察视窗(21)。3.根据权利要求1所述的一种用于中大型铸件打磨的气动升降双工位旋转台机构,其特征在于:旋转台板(1)底部设置有安装支架(3)以及支撑板(31),支撑板(31)设置在安装支架(3)上方,旋转台板(1)通过支撑板(31)放置在安装支架(3)上;安装支架(3)内部镂空,形成用于放置转动机构(4)和升降机构(5)的容纳空间。4.根据权利要求1所述的一种用于中大型铸件打磨的气动升降双工位旋转台机构,其特征在于:转动机构(4)设置在旋转台板(1)下方,包括电机安装支架(41)、旋转电机(42),旋转电机(42)的输出端朝上设置;旋转电机(42)设置在电机安装支架(41)内;旋转台板(1)的底板设置有传动单元(43),传动单元(43)与旋转台板(1)固定连接,旋转电机(42)的输出端通过带动传动单元(43)间接带动旋转台板(1)转动。5.根据权利要求4所述的一种用于中大型铸件打磨的气动升降双工位旋转台机构,其特征在于:升降机构(5)设置在转动机构(4)下方,用于带动转动机构(4)以及旋转台板(1)升降;升降机构(5)包括升降导向柱(51)、气缸(52),还包括设置在电机安装支架(41)侧方的直线轴承(53),电机安装支架(41)边缘部位向两侧延伸形成用于安装直线轴承(53)的耳板(54),直线轴承(53)套设在升降导向柱(51)上;气缸(52)的活动端朝上设置,活动端的端部与电机安装支架(41)的底部固定连接。6.根据权利要求5所述的一种用于中大型铸件打磨的气动升降双工位旋转台机构,其特征在于:升降机构(5)底部设置有安装底板(6),升降导向柱(51)和气缸(52)的底部设置在安装底板(6)上。7.根据权利要求5所述的一种用于中大型铸件打磨的气动升降双工位旋转台机构,其特征在于:升降导向柱(51)设有四个,电机安装支架(41)边缘部位向两侧延伸形成用于安装直线轴承(53)的耳板(54),所述耳板(54)对应设置有四个。8.根据权利要求5所述的一种用于中大型铸件打磨的气动升降双工位旋转台机构,其特征在于:升降导向柱(51)上还套设有导向柱防护套(7),用于防止导向柱上附着灰尘。
技术总结本实用新型提供了一种用于中大型铸件打磨的气动升降双工位旋转台机构,包括旋转台板,旋转台板上设置有第一加工工位和第二加工工位,第一加工工位和第二加工工位分别设置在旋转台板的两端;旋转台板下方设置有转动机构和升降机构,升降机构用于带动旋转台板提升,转动机构用于带动旋转台板转动。本实用新型有益效果:一种用于中大型铸件打磨的气动升降双工位旋转台机构中,双工位打磨工位完成工位互换,极大的节省上下料时间,提高打磨效率。提高打磨效率。提高打磨效率。
技术研发人员:徐丽娜 侯体辉 侯保敏
受保护的技术使用者:天津中屹铭科技有限公司
技术研发日:2021.12.31
技术公布日:2022/6/6