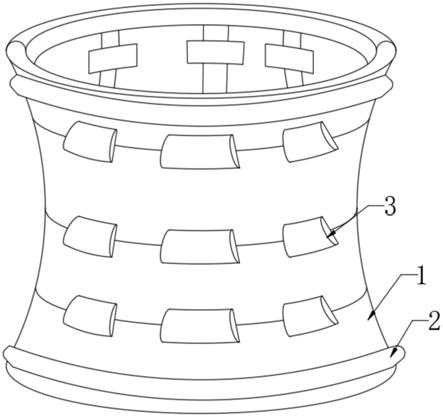
1.本实用新型属于车轮轮辋技术领域,特别涉及一种钢制车轮等强度轮辋。
背景技术:2.现有的钢制车轮在行驶时,轮胎传递到钢制车轮内部热量过高,容易导致轮胎外壁受到高温损害,影响车轮行驶效率,且很难保证不出现脱胎、跑胎的现象,因此,现在亟需一种钢制车轮等强度轮辋来解决这个问题。
技术实现要素:3.针对现有技术存在的不足,本实用新型目的是提供一种钢制车轮等强度轮辋,解决上述背景技术中提出的问题。
4.本实用新型通过以下的技术方案实现:一种钢制车轮等强度轮辋,包括钢制轮辋、连接凸起、散热板以及流动槽,所述钢制轮辋外圈表面开设有多个散热弧孔,多个所述散热弧孔呈环形分布在钢制轮辋的外圈表面,每个所述散热弧孔内均设置有一个散热板,每个所述散热板的内侧表面均开设有一个弧形槽,每个所述弧形槽内均设置有一个散热撑板,所述钢制轮辋内圈表面开设有多个流动槽,多个所述流动槽呈环形分布在钢制轮辋的内圈表面,所述流动槽与钢制轮辋上的散热弧孔连通,且所述流动槽贯穿散热板,所述钢制轮辋的外圈表面左端与右端均设置有一个连接凸起,且两个所述连接凸起对称设置在钢制轮辋的外圈表面左端与右端。
5.作为一优选的实施方式,所述连接凸起的截面在实际使用时呈三角形结构,且空腔设置在所述连接凸起的内部,橡胶垫板设置在所述连接凸起的朝下一侧表面。
6.作为一优选的实施方式,防护圆角设置在所述连接凸起的顶部边缘,且所述橡胶垫板的上端与连接凸起的下端面上侧连接处设置有圆角。
7.作为一优选的实施方式,所述流动槽的左端面截面在实际使用时呈喇叭状设计,且所述流动槽的右端面截面在实际使用时呈喇叭状设计,所述流动槽的左端与右端均沿着钢制轮辋内圈表面延伸至钢制轮辋的两端外侧。
8.作为一优选的实施方式,拱板设置在所述散热板的上端顶部,且所述拱板的上端置于钢制轮辋的外圈表面上侧,连接圆角设置在所述散热板的弧形槽上,所述散热板在实际使用时是一种铝板,且所述散热撑板在实际使用时是一种铝板。
9.作为一优选的实施方式,防滑圈设置在所述钢制轮辋内圈表面最左端与最右端,所述防滑圈表面设置有防滑纹。
10.采用了上述技术方案后,本实用新型的有益效果是:通过在钢制轮辋外圈表面左端以及右端分别设置有一个连接凸起,能够降低跑胎、脱胎的概率,且连接凸起上设置的橡胶垫板能够增大摩擦,并且设置的防护圆角以及圆角,可以在轮胎外侧发生摩擦或碰撞时,减少刮蹭带来的磨损,而设置的散热板、流动槽以及散热撑板,能够降低轮胎与钢制轮辋抵接处因为摩擦产生的热量,提高了散热性。
附图说明
11.为了更清楚地说明本实用新型实施例或现有技术中的技术方案,下面将对实施例或现有技术描述中所需要使用的附图作简单地介绍,显而易见地,下面描述中的附图仅仅是本实用新型的一些实施例,对于本领域普通技术人员来讲,在不付出创造性劳动性的前提下,还可以根据这些附图获得其他的附图。
12.图1为本实用新型一种钢制车轮等强度轮辋的整体结构示意图。
13.图2为本实用新型一种钢制车轮等强度轮辋的剖面示意图。
14.图3为本实用新型一种钢制车轮等强度轮辋的钢制轮辋的剖面示意图。
15.图4为本实用新型一种钢制车轮等强度轮辋的a处放大示意图。
16.图中,1-钢制轮辋、11-散热弧孔、2-连接凸起、21-橡胶垫板、22-防护圆角、23-空腔、3-散热板、31-散热撑板、32-连接圆角、33-拱板、4-流动槽。
具体实施方式
17.下面将结合本实用新型实施例中的附图,对本实用新型实施例中的技术方案进行清楚、完整地描述,显然,所描述的实施例仅仅是本实用新型一部分实施例,而不是全部的实施例。基于本实用新型中的实施例,本领域普通技术人员在没有作出创造性劳动前提下所获得的所有其他实施例,都属于本实用新型保护的范围。
18.请参阅图1至图4,本实用新型提供一种技术方案:一种钢制车轮等强度轮辋,包括钢制轮辋1、连接凸起2、散热板3以及流动槽4,钢制轮辋1外圈表面开设有多个散热弧孔11,多个散热弧孔11呈环形分布在钢制轮辋1的外圈表面,每个散热弧孔11内均设置有一个散热板3,每个散热板3的内侧表面均开设有一个弧形槽,每个弧形槽内均设置有一个散热撑板31,钢制轮辋1内圈表面开设有多个流动槽4,多个流动槽4呈环形分布在钢制轮辋1的内圈表面,流动槽4与钢制轮辋1上的散热弧孔11连通,且流动槽4贯穿散热板3,钢制轮辋1的外圈表面左端与右端均设置有一个连接凸起2,且两个连接凸起2对称设置在钢制轮辋1的外圈表面左端与右端。
19.连接凸起2的截面在实际使用时呈三角形结构,且空腔23设置在连接凸起2的内部,橡胶垫板21设置在连接凸起2的朝下一侧表面,三角形结构稳定性高,橡胶垫板21能够增大摩擦,能够防止轮胎脱落。
20.防护圆角22设置在连接凸起2的顶部边缘,且橡胶垫板21的上端与连接凸起2的下端面上侧连接处设置有圆角,能够防止对轮胎内侧造成磨损,且能够分散应力。
21.流动槽4的左端面截面在实际使用时呈喇叭状设计,且流动槽4的右端面截面在实际使用时呈喇叭状设计,流动槽4的左端与右端均沿着钢制轮辋1内圈表面延伸至钢制轮辋1的两端外侧,便于空气的流动,且宽度的减小能够增大空气流速,提高散热效果。
22.拱板33设置在散热板3的上端顶部,且拱板33的上端置于钢制轮辋1的外圈表面上侧,连接圆角32设置在散热板3的弧形槽上,散热板3在实际使用时是一种铝板,且散热撑板31在实际使用时是一种铝板,铝板的导热性能好,便于散热,拱板33的设计能够降低对轮胎造成的损伤。
23.防滑圈设置在钢制轮辋1内圈表面最左端与最右端,防滑圈表面设置有防滑纹,能够增大钢制轮辋1与轮胎之间的摩擦,防止轮胎的脱落。
24.作为本实用新型的一个实施例:在实际使用时,通过在钢制轮辋1外圈表面左端以及右端分别设置有一个连接凸起2,能够降低跑胎、脱胎的概率,且连接凸起2上设置的橡胶垫板21能够增大摩擦,并且设置的防护圆角22以及圆角,可以在轮胎外侧发生摩擦或碰撞时,减少刮蹭带来的磨损,而设置的散热板3、流动槽4以及散热撑板31,能够降低轮胎与钢制轮辋1骨架抵接处因为摩擦产生的热量,提高了散热性,散热板3与散热撑板31能够对钢制轮辋1上的热量进行吸附,在钢制轮辋1转动时,会有一定的气流沿着流动槽4流动,由于流动槽4与散热板3上的弧形槽连通,从而将散热板3以及散热撑板31上的热量带走,以此达到散热功能。
25.以上所述仅为本实用新型的较佳实施例而已,并不用以限制本实用新型,凡在本实用新型的精神和原则之内,所作的任何修改、等同替换、改进等,均应包含在本实用新型的保护范围之内。
技术特征:1.一种钢制车轮等强度轮辋,包括:钢制轮辋(1)、连接凸起(2)、散热板(3)以及流动槽(4),所述钢制轮辋(1)外圈表面开设有多个散热弧孔(11),多个所述散热弧孔(11)呈环形分布在钢制轮辋(1)的外圈表面,其特征在于,每个所述散热弧孔(11)内均设置有一个散热板(3),每个所述散热板(3)的内侧表面均开设有一个弧形槽,每个所述弧形槽内均设置有一个散热撑板(31),所述钢制轮辋(1)内圈表面开设有多个流动槽(4),多个所述流动槽(4)呈环形分布在钢制轮辋(1)的内圈表面,所述流动槽(4)与钢制轮辋(1)上的散热弧孔(11)连通,且所述流动槽(4)贯穿散热板(3),所述钢制轮辋(1)的外圈表面左端与右端均设置有一个连接凸起(2),且两个所述连接凸起(2)对称设置在钢制轮辋(1)的外圈表面左端与右端。2.如权利要求1所述的一种钢制车轮等强度轮辋,其特征在于:所述连接凸起(2)的截面呈三角形结构,且所述连接凸起(2)的内部设置有空腔(23),所述连接凸起(2)的朝下一侧表面设置有橡胶垫板(21)。3.如权利要求2所述的一种钢制车轮等强度轮辋,其特征在于:所述连接凸起(2)的顶部边缘设置有防护圆角(22),且所述橡胶垫板(21)的上端与连接凸起(2)的下端面上侧连接处设置有圆角。4.如权利要求1所述的一种钢制车轮等强度轮辋,其特征在于:所述流动槽(4)的左端面截面呈喇叭状设计,且所述流动槽(4)的右端面截面呈喇叭状设计,所述流动槽(4)的左端与右端均沿着钢制轮辋(1)内圈表面延伸至钢制轮辋(1)的两端外侧。5.如权利要求1所述的一种钢制车轮等强度轮辋,其特征在于:所述散热板(3)的上端顶部设置有拱板(33),且所述拱板(33)的上端置于钢制轮辋(1)的外圈表面上侧,所述散热板(3)的弧形槽上设置有连接圆角(32),所述散热板(3)是一种铝板,且所述散热撑板(31)是一种铝板。6.如权利要求1所述的一种钢制车轮等强度轮辋,其特征在于:所述钢制轮辋(1)内圈表面最左端与最右端均设置有防滑圈,所述防滑圈表面设置有防滑纹。
技术总结本实用新型提供一种钢制车轮等强度轮辋,每个所述散热弧孔内均设置有一个散热板,每个所述散热板的内侧表面均开设有一个弧形槽,每个所述弧形槽内均设置有一个散热撑板,所述钢制轮辋内圈表面开设有多个流动槽,多个所述流动槽呈环形分布在钢制轮辋的内圈表面,所述流动槽与钢制轮辋上的散热弧孔连通,所述钢制轮辋的外圈表面左端与右端均设置有一个连接凸起,且两个所述连接凸起对称设置在钢制轮辋的外圈表面左端与右端,与现有技术相比,本实用新型具有如下的有益效果:通过设置的连接凸起,能够降低跑胎、脱胎的概率,连接凸起上设置的橡胶垫板能够增大摩擦,能够降低轮胎与钢制轮辋骨架抵接处因为摩擦产生的热量,提高了散热性。热性。热性。
技术研发人员:夏旭平 刘步蟾 方琴 冯娟 崔昱
受保护的技术使用者:张家港今日精锻有限公司
技术研发日:2022.04.13
技术公布日:2022/9/20