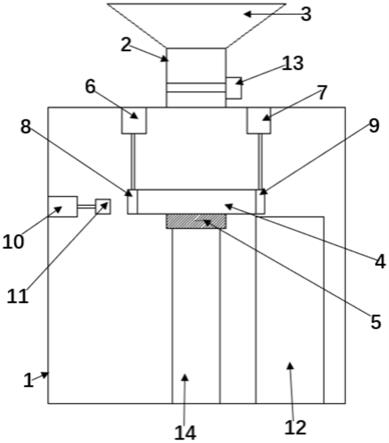
1.本实用新型涉及下料设备技术领域,尤其是一种铜排高温熔融自动化下料装置。
背景技术:2.铜排在生产过程中,特别是在高温熔炼工序里,熔炼物料的比例是相当严格的,物料不能投入过多或者过少,因此,在每次投料前均需对物料进行称量,但是,每次对物料进行称量耗费的时间较长,不利于生产效率的提高,而且,物料的称量工作一般采用人工操作,导致人工成本提高。为此,我们提出一种铜排高温熔融自动化下料装置,以解决现有技术的不足。
技术实现要素:3.针对现有技术的不足,本实用新型提供一种铜排高温熔融自动化下料装置,该装置不仅能够实现自动称量物料,称量的时间较快,而且,称量结束后,还可实现自动下料,自动化程度较高,进一步降低人工劳动力,节约人工成本,以及提高生产效率。
4.本实用新型的技术方案为:
5.一种铜排高温熔融自动化下料装置,其特征在于:它包括装置本体,所述装置本体的顶面中部固定安装有进料管,所述进料管的顶部焊接有进料漏斗,所述装置本体的内中部且正对进料管处设置有称量板,所述称量板的左侧面、右侧面以及顶面开口设置,所述称量板的底面固定安装有电子称,所述装置本体的内顶面左右两端分别安装有第一气缸和第二气缸,所述第一气缸和第二气缸上的推杆端分别焊接有左侧板和右侧板,所述装置本体的左侧面内壁且正对称量板处固定安装有第三气缸,所述第三气缸上的推杆端焊接有推板,所述装置本体的内部右侧固定安装有下料管。
6.进一步的,所述进料管上固定安装有蝶阀。通过安装蝶阀,进料管以及进料漏斗上的物料每次均能达到相对一致。
7.进一步的,所述电子称的底面通过立柱与装置本体的内底面固接。
8.进一步的,所述下料管位于称量板的下方。
9.进一步的,所述下料管上下中空设置,所述下料管的左侧面与称量板的右侧面齐平。
10.进一步的,所述下料管的前后长度大于称量板的前后长度。目的在于:推板推出的物料均能确保落在下料管处。
11.进一步的,所述装置本体的前侧面且正对电子称处设置有观察口,所述观察口处安装有透明玻璃。
12.本实用新型的有益效果为:本实用新型通过设有称量板、电子称、第一气缸、第二气缸、左侧板、右侧板、第三气缸、推板和下料管,不仅能够实现自动称量物料,称量的时间较快,而且,称量结束后,还可实现自动下料,自动化程度较高,进一步降低人工劳动力,节约人工成本,以及提高生产效率。
附图说明
13.图1为本实用新型的结构示意图。
14.图中,1、装置本体;2、进料管;3、进料漏斗;4、称量板;5、电子称;6、第一气缸;7、第二气缸;8、左侧板;9、右侧板;10、第三气缸;11、推板;12、下料管;13、蝶阀;14、立柱。
具体实施方式
15.下面结合附图对本实用新型的具体实施方式作进一步说明:
16.如图1所示,一种铜排高温熔融自动化下料装置,它包括装置本体1,所述装置本体1的顶面中部固定安装有进料管2,所述进料管2的顶部焊接有进料漏斗3,所述装置本体1的内中部且正对进料管2处设置有称量板4,所述称量板4的左侧面、右侧面以及顶面开口设置,所述称量板4的底面固定安装有电子称5,所述装置本体1的内顶面左右两端分别安装有第一气缸6和第二气缸7,所述第一气缸6和第二气缸7上的推杆端分别焊接有左侧板8和右侧板9,所述装置本体1的左侧面内壁且正对称量板4处固定安装有第三气缸10,所述第三气缸10上的推杆端焊接有推板11,所述装置本体1的内部右侧固定安装有下料管12。
17.所述进料管2上固定安装有蝶阀13。通过安装蝶阀13,进料管2以及进料漏斗3上的物料量每次均能达到相对一致。
18.所述电子称5的底面通过立柱14与装置本体1的内底面固接。
19.所述下料管12位于称量板4的下方。
20.所述下料管12上下中空设置,所述下料管12的左侧面与称量板4的右侧面齐平。
21.所述下料管12的前后长度大于称量板4的前后长度。目的在于:推板11推出的物料均能确保落在下料管12处。
22.所述装置本体1的前侧面且正对电子称5处设置有观察口,所述观察口处安装有透明玻璃。
23.本实用新型的工作原理为:工作时,先向进料漏斗3处注满物料,由于设置有蝶阀13,进料管2以及进料漏斗3上的物料量每次均能达到相对一致,此时,将启动第一气缸6和第二气缸7,第一气缸6和第二气缸7将左侧板8和右侧板9往下推进,使得左侧板8和右侧板9分别与称量板4的左侧面和右侧面吻合(但是不相接触,之间的间隙为0.3
‑
0.5mm,能够确保不掉落物料,且不影响称量工作),接着,开启蝶阀13,使得物料全部落入称量板4内(由于称量板4位于进料管2的正下方),电子称5对物料进行称量后(由于进料管2以及进料漏斗3上的物料量每次均能达到相对一致,故此,物料量基本能够达到设定的范围值内,属于正常投入,极少可能会出现物料量不在范围值内,此时,通过人工在观察口观察可知,之后,将在进料漏斗3处投入少量物料,使其达到范围值内,该种可能极少出现,故而不影响整体的物料称量),第一气缸6和第二气缸7复位,打开称量板4左右侧面的通道,此时,将启动第三气缸10,第三气缸10推动推板11向右,将称量板4内的物料直接推进下料管12,通过下料管12完成后续的下料。
24.上述实施例和说明书中描述的只是说明本实用新型的原理和最佳实施例,在不脱离本实用新型精神和范围的前提下,本实用新型还会有各种变化和改进,这些变化和改进都落入要求保护的本实用新型范围内。
技术特征:1.一种铜排高温熔融自动化下料装置,其特征在于:它包括装置本体(1),所述装置本体(1)的顶面中部固定安装有进料管(2),所述进料管(2)的顶部焊接有进料漏斗(3),所述装置本体(1)的内中部且正对进料管(2)处设置有称量板(4),所述称量板(4)的左侧面、右侧面以及顶面开口设置,所述称量板(4)的底面固定安装有电子称(5),所述装置本体(1)的内顶面左右两端分别安装有第一气缸(6)和第二气缸(7),所述第一气缸(6)和第二气缸(7)上的推杆端分别焊接有左侧板(8)和右侧板(9),所述装置本体(1)的左侧面内壁且正对称量板(4)处固定安装有第三气缸(10),所述第三气缸(10)上的推杆端焊接有推板(11),所述装置本体(1)的内部右侧固定安装有下料管(12)。2.根据权利要求1所述的一种铜排高温熔融自动化下料装置,其特征在于:所述进料管(2)上固定安装有蝶阀(13)。3.根据权利要求2所述的一种铜排高温熔融自动化下料装置,其特征在于:所述电子称(5)的底面通过立柱(14)与装置本体(1)的内底面固接。4.根据权利要求3所述的一种铜排高温熔融自动化下料装置,其特征在于:所述下料管(12)位于称量板(4)的下方。5.根据权利要求4所述的一种铜排高温熔融自动化下料装置,其特征在于:所述下料管(12)上下中空设置,所述下料管(12)的左侧面与称量板(4)的右侧面齐平。6.根据权利要求5所述的一种铜排高温熔融自动化下料装置,其特征在于:所述下料管(12)的前后长度大于称量板(4)的前后长度。7.根据权利要求6所述的一种铜排高温熔融自动化下料装置,其特征在于:所述装置本体(1)的前侧面且正对电子称(5)处设置有观察口,所述观察口处安装有透明玻璃。
技术总结本实用新型涉及下料设备技术领域,尤其是一种铜排高温熔融自动化下料装置,它包括装置本体,所述装置本体的顶面中部固定安装有进料管,所述进料管的顶部焊接有进料漏斗,所述装置本体的内中部且正对进料管处设置有称量板,所述称量板的底面固定安装有电子称,所述装置本体的内顶面左右两端分别安装有第一气缸和第二气缸,所述第一气缸和第二气缸上的推杆端分别焊接有左侧板和右侧板;本实用新型通过设有称量板、电子称、第一气缸、第二气缸、左侧板、右侧板、第三气缸、推板和下料管,不仅能够实现自动称量物料,称量的时间较快,而且,称量结束后,还可实现自动下料,自动化程度较高,进一步降低人工劳动力,节约人工成本,以及提高生产效率。效率。效率。
技术研发人员:邓正国 梁坚华
受保护的技术使用者:广州市国隆实业有限公司
技术研发日:2021.04.14
技术公布日:2021/11/30