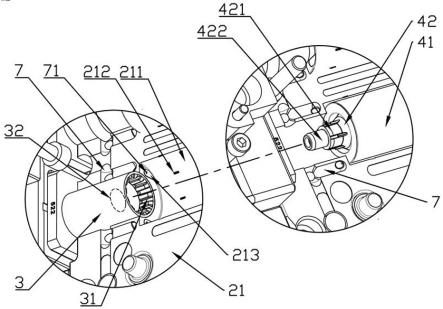
1.本实用新型涉及一种注塑模具研制,尤其涉及一种适用于单端外形结构复杂、同心度要求高的注塑成型管的成型模具设计,属于注塑加工制造领域。
背景技术:2.注塑加工生产是批量规模化定制各类异形件的有效方式,其工艺制程的发展由来已久且日渐高效、环保和高品质。注塑工艺是一种能满足各种非标异形件加工生产的优选工艺,较之于传统切削、冲铣加工作业方式,具有一次成型、可规模化生产的显著优势。然而,由于注塑产品的形状多样性,对应一件产品往往需要独立开发并反复试制,以达到产品的精度要求后方可投入规模化生产。
3.有一种注塑成型管产品,其不同于其它管件的结构特点如图1所示,该成型管1两端开口贯通,且外壁分布设有若干棘齿型凸点(功能省略)。作为模具设计所关注的成型管单端11,在端面内成型有内环13和凸齿型外环12相嵌套的一体成型结构,以满足管件后续装配应用,其中内环13分段相隔,在一定外力作用下可微微张口或闭合;而外环则向外分布设有用于保持同轴传动的凸齿;此外,端面成型有用于切胶口后排除胶口凸露部分的平槽14,成型管的管壁分布设有若干棘齿型凸点15。鉴于该复杂单端结构的成型管,依靠传统单一化模仁、模芯、抽芯的模具结构,将无法满足产品高精度的成型要求。
技术实现要素:4.本实用新型的目的旨在提出一种注塑成型管的单端成型模具,解决单端成型结构同轴度和精度要求高的问题。
5.本实用新型实现上述目的的技术解决方案是,包括受控启闭的上模、下模及其间的抽芯和若干滑块,所述上模和下模各自内设有模仁,模仁加工有对应成型管主体部分外壁的成型腔,且成型管的单端设为同心的内环和凸齿型的外环,其特征在于:紧挨模仁设有用于定型成型管单端外形的模芯,模芯内侧的第一成型面与外环相匹配;所述抽芯设为管轴嵌套组件,而内轴一端的第二成型面与内环相匹配,且模芯与内轴在接合成型腔的外侧设有趋向于同轴的对位轴孔组。
6.进一步地,所述模芯与模仁互相定位且一体装接于上模或下模,合模与开模状态下保持位置恒定。
7.进一步地,所述模芯靠近模仁的一端加工第一成型面,所述第一成型面的轴向深度对应外环的轴向长度,且周向分布设有用于成型凸齿的凸肋。
8.进一步地,对应上模、下模的两个模仁在模芯第一成型面的外围分布设有进胶口。
9.更进一步地,所述进胶口表面设有厚度小于0.5mm的垫台。
10.进一步地,所述对位轴孔组包括设于模芯中部的定位孔和设于内轴第二成型面轴向外端的对位柱,所述定位孔的檐口设有导向坡面,所述对位柱无缝接合于定位孔之中。
11.进一步地,所述下模对应成型管单端的另一端设有抽芯驱动单元和用于脱模的推
料单元。
12.应用本实用新型该成型模具,具有进步性的优点:在成型单端复杂外形的基础上,通过对位轴孔组实现了抽芯与注塑成型腔及各成型面的轴向对中,提高了内环和凸齿型外环的同心度和产品精度。
附图说明
13.图1是本实用新型生产对象之注塑成型管的立体结构示意图。
14.图2是本实用新型单端成型模具一部分的结构示意图。
15.图3是图2所示单端成型模具中对位轴孔组的细节结构示意图。
具体实施方式
16.以下便结合实施例附图,对本实用新型的具体实施方式作进一步的详述,以使本实用新型技术方案更易于理解、掌握,从而对本实用新型的保护范围做出更为清晰的界定。
17.有鉴于注塑成型管单端结构复杂且同心度、精度要求大的问题,本实用新型设计者结合长期模具开发之经验,创新提出了一种注塑成型管的单端成型模具,合模过程中自动同心对中的优化设置,改善成品品质。
18.如图2和图3所示,是本实用新型单端成型模具优选实施例部分整装及局部细节的结构示意图。从结构概述来看,与常规模具相同的部分是包括受控启闭的上模(未图示)、下模2及其间的抽芯4和若干滑块,上模和下模各自内设有模仁,模仁21加工有对应成型管主体部分外壁的成型腔211及成型棘齿型凸点的微型坑槽212。作为区别于传统模具的特殊结构改良,紧挨模仁21设有用于定型成型管单端外形的模芯3,模芯3内侧的第一成型面31与外环12相匹配;而抽芯4设为管轴嵌套组件,而内轴42一端的第二成型面421与内环13相匹配,且模芯3与内轴42在接合成型腔的外侧设有趋向于同轴的对位轴孔组。
19.需要说明的是,由此当合模并准备向进胶口注胶前,抽芯中的内轴与模芯以榫卯结合的方式接合,达到完全同心。而管轴嵌套的抽芯外管41,虽然对应成型管的内壁结构而设,但同样也得益于内轴42而实现整体的同心度校准。因此,注塑成型管的成品无论单端的复杂结构,还是内、外管壁都达到理想的同心度品质。
20.从更具体的细节方面来掌握该实施例,上述模芯3与模仁21互相定位且一体装接于上模或下模,合模与开模状态下保持位置恒定。即模仁21中所设成型腔211的凹弧面与模芯所设的第一成型面在装配精度保障下默认为同轴设置。该第一成型面31在模芯3靠近模仁21的一端加工而成,且第一成型面31的轴向深度对应外环的轴向长度,周向分布设有用于成型凸齿的凸肋。
21.上述改良重点之对位轴孔组,包括设于模芯3中部的定位孔32和设于内轴42第二成型面421轴向外端的对位柱422。为合模过程中的防呆设置,该定位孔32的檐口及对位柱422的端部均设有导向坡面(未表示及细节图示),则对位柱422随合模动作而无缝接合于定位孔32之中。
22.作为该注塑成型管另一工艺参数要求,其端面要求平整度极高。由于对应上模、下模的两个模仁在模芯周边设置胶道7,并在第一成型面31的外围分布设有进胶口71。为便于切胶口后保障端面平整度,该模仁21在进胶口表面优选设有厚度小于0.5mm的垫台213,则
在成型管的端面形成反向内凹、排除切胶口后排除胶口凸露部分的平槽14。
23.此外,作为常规模具的必要性设置,该下模对应成型管单端的另一端设有抽芯驱动单元5和用于脱模的推料单元6,上模则对应留出适量空间以适配两个单元的导向移动,从而使得成型管成品良性退模。
24.综上关于本实用新型单端成型模具的实施例详述及图示可见,其具备进步性:在成型单端复杂外形的基础上,通过对位轴孔组实现了抽芯与注塑成型腔及各成型面的轴向对中,提高了内环和凸齿型外环的同心度和产品精度。
25.以上详细描述旨在加深对本实用新型注塑模具设计的理解,并非以此限制本专利应用实施的范围及多变性。故凡是相对于本实用新型上述实施例等效或近似的结构变换,可以实现本实用新型目的设计方案,均应该被视为属于本实用新型专利保护的范畴。
技术特征:1.一种注塑成型管的单端成型模具,包括受控启闭的上模、下模及其间的抽芯和若干滑块,所述上模和下模各自内设有模仁,模仁加工有对应成型管主体部分外壁的成型腔,且成型管的单端设为同心的内环和凸齿型的外环,其特征在于:紧挨模仁设有用于定型成型管单端外形的模芯,模芯内侧的第一成型面与外环相匹配;所述抽芯设为管轴嵌套组件,而内轴一端的第二成型面与内环相匹配,且模芯与内轴在接合成型腔的外侧设有趋向于同轴的对位轴孔组。2.根据权利要求1所述注塑成型管的单端成型模具,其特征在于:所述模芯与模仁互相定位且一体装接于上模或下模,合模与开模状态下保持位置恒定。3.根据权利要求1所述注塑成型管的单端成型模具,其特征在于:所述模芯靠近模仁的一端加工第一成型面,所述第一成型面的轴向深度对应外环的轴向长度,且周向分布设有用于成型凸齿的凸肋。4.根据权利要求1所述注塑成型管的单端成型模具,其特征在于:对应上模、下模的两个模仁在模芯第一成型面的外围分布设有进胶口。5.根据权利要求4所述注塑成型管的单端成型模具,其特征在于:所述进胶口表面设有厚度小于0.5mm的垫台。6.根据权利要求1所述注塑成型管的单端成型模具,其特征在于:所述对位轴孔组包括设于模芯中部的定位孔和设于内轴第二成型面轴向外端的对位柱,所述定位孔的檐口设有导向坡面,所述对位柱无缝接合于定位孔之中。7.根据权利要求1所述注塑成型管的单端成型模具,其特征在于:所述下模对应成型管单端的另一端设有抽芯驱动单元和用于脱模的推料单元。
技术总结本实用新型揭示了一种注塑成型管的单端成型模具,包括受控启闭的上模、下模及其间的抽芯和若干滑块,上模和下模各自内设有模仁,模仁加工有对应成型管主体部分外壁的成型腔,且成型管的单端设为同心的内环和凸齿型的外环。特别的模具设计为:紧挨模仁设有用于定型成型管单端外形的模芯,模芯内侧的第一成型面与外环相匹配;该抽芯设为管轴嵌套组件,而内轴一端的第二成型面与内环相匹配,且模芯与内轴在接合成型腔的外侧设有趋向于同轴的对位轴孔组。应用本实用新型该单端成型模具,在成型单端复杂外形的基础上,通过对位轴孔组实现了抽芯与注塑成型腔及各成型面的轴向对中,提高了内环和凸齿型外环的同心度和产品精度。高了内环和凸齿型外环的同心度和产品精度。高了内环和凸齿型外环的同心度和产品精度。
技术研发人员:刘亚良
受保护的技术使用者:江苏朗佑精密部件制造有限公司
技术研发日:2021.12.08
技术公布日:2022/9/6