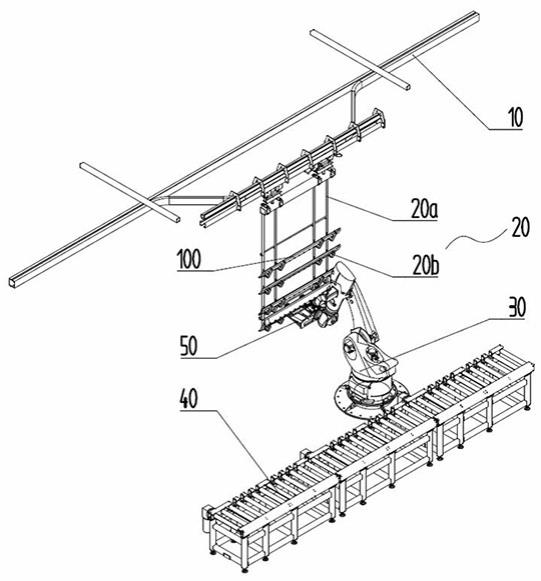
1.本发明涉及一种机械夹爪及应用其的弧形钢板自动取放系统,属于冶金制造的技术领域。
背景技术:2.在冶金生产现场,弧形钢板的夹持定位一直是实现其自动化运输的掣肘,目前,大多采用以下两种方案:一是人工操作行车吊运,需要工人手动扎好吊带用行车取放,该方法不符合无人智能化生产的定位要求,且行车吊运误差过大、吊运效率过低。
3.二是用电永磁吸取工件,但是该方法的明显缺陷是对产品表面油漆有损坏,适应性差,无法满足冶金智能工厂的需求。
4.同时,以上两种方案都无法实现弧形钢板的精确定位夹持。
技术实现要素:5.发明目的:针对上述问题,本发明的目的是提供一种机械夹爪及应用其的弧形钢板自动取放系统,实现对于弧形钢板的精准定位和夹持,提高作业效率,满足冶金智能工厂的需要。
6.技术方案:一种机械夹爪,包括夹爪本体、夹爪头、导杆气缸、包胶辊子、防护层、托垫,所述夹爪头呈l型,后端与所述夹爪本体固定、上端固定所述防护层、直角处固定所述托垫,所述防护层与所述托垫相邻,所述托垫上开设有圆弧槽,所述防护层上开设有卡槽,所述导杆气缸固定在夹爪本体上,所述包胶辊子固定在所述导杆气缸的输出端上,且与所述夹爪头对位设置,所述卡槽、圆弧槽、包胶辊子同向设置;所述卡槽用于卡设弧形钢板的顶边,所述圆弧槽用于抵靠所述弧形钢板的底边,所述导杆气缸推动所述包胶辊子按压在所述弧形钢板的凸面上,形成夹持固定。
7.本发明的原理是:夹持时,首先通过卡槽卡住弧形钢板的顶板,并将其底板置入圆弧槽内,之后,通过导杆气缸带动包胶辊子向弧形钢板移动,并按压在弧形钢板的凸面上,此时,弧形钢板的底边在包胶辊子的按压下沿圆弧槽滑动,直至限位固定,从而形成稳定的夹持结构。同时,由于弧形钢板的顶边位置已通过卡槽纤维,从而形成精确的夹持定位结构,为智能工厂的弧形钢板自动化作业提供了条件。
8.进一步,还包括检测开关,所述检测开关固定在所述夹爪本体上,且朝向所述夹爪头,用于在自动化作业时,检测弧形钢板是否夹持成功。
9.优选的,所述检测开关采用光电检测开关。
10.进一步,所述卡槽为多个,且呈锯齿状布置,以适应不同尺寸的弧形钢板的夹持。
11.进一步,所述夹爪头为多个,平行设置于所述夹爪本体前端。
12.优选的,所述防护层采用聚氨酯防护层。
13.优选的,所述托垫采用尼龙托垫。
14.一种弧形钢板自动取放系统,包括积放链轨道、挂具、机器人本体、辊道装置、如上所述的机械夹爪,所述机器人本体设置于所述积放链轨道与辊道装置之间,所述机械夹爪通过法兰连接所述机器人本体,所述挂具包括框架本体和挂钩,所述框架本体固定在所述积放链轨道上,且沿所述积放链轨道运动,所述挂钩成排的固定在所述框架本体上,用于放置弧形钢板;所述机械夹爪在所述机器人本体的驱动下,从所述挂钩上夹持所述弧形钢板,并放置到所述辊道装置上。
15.有益效果:与现有技术相比,本发明的优点是:1、通过多点定位,形成精确、稳定的弧形钢板夹持结构,为弧形钢板的自动化输送提供了条件;2、可适用于不同尺寸的弧形钢板夹持,实用性强。
附图说明
16.图1为本发明机械夹爪的立体结构示意图;图2为本发明机械夹爪的侧面视图;图3为本发明弧形钢板自动取放系统的立体结构示意图。
具体实施方式
17.下面结合附图和具体实施例,进一步阐明本发明,这些实施例仅用于说明本发明而不用于限制本发明的范围。
18.一种机械夹爪,如附图1~2所示,包括夹爪本体1、夹爪头2、导杆气缸3、包胶辊子4、防护层5、托垫6、检测开关7。
19.夹爪头2呈l型,后端与夹爪本体1固定、上端固定防护层5、直角处固定托垫6,防护层5与托垫6相邻,托垫6上开设有圆弧槽a,防护层5上开设有卡槽b,导杆气缸3和检测开关7固定在夹爪本体1上,且朝向夹爪头2。包胶辊子4固定在导杆气缸3的输出端上,且与夹爪头2对位设置,卡槽b、圆弧槽a、包胶辊子4同向设置;卡槽b用于卡设弧形钢板100的顶边,圆弧槽a用于抵靠弧形钢板100的底边,导杆气缸3推动包胶辊子4按压在弧形钢板100的凸面上,形成夹持固定,并通过检测开关7检测弧形钢板100是否夹持成功。本实施例中,检测开关7优选采用光电检测开关,防护层5优选采用聚氨酯防护层,托垫6优选采用尼龙托垫。
20.本实施例中的“卡槽b、圆弧槽a、包胶辊子4同向设置”,是指卡槽b和圆弧槽a的开设方向,与包胶辊子4的辊子轴向为相同方向。
21.为便于适应不同尺寸的弧形钢板100夹持,本实施例中,卡槽b设置为多个,且呈锯齿状排列布置。
22.为保持夹持的稳定性,本实施例中,夹爪头2设置为多个,且平行设置于夹爪本体1前端。
23.本实施例还涉及一种弧形钢板自动取放系统,如附图3所示,包括积放链轨道10、挂具20、机器人本体30、辊道装置40、如上的机械夹爪50。
24.机器人本体30设置于积放链轨道10与辊道装置40之间,机械夹爪50通过法兰连接机器人本体30,挂具20包括框架本体20a和挂钩20b,框架本体20a固定在积放链轨道10上,且沿积放链轨道10运动,挂钩20b成排的固定在框架本体20a上,用于放置弧形钢板100;机械夹爪50在机器人本体30的驱动下,从挂钩20b上夹持弧形钢板100,并放置到辊道装置40
上。
25.本实施例的弧形钢板100自动取放系统使用前,首先将弧形钢板100储存在成排的挂钩20b上。使用时,积放链轨道10驱动挂具20沿其轨道运动,带动挂具20到达机器人本体30处,机器人本体30驱动机械夹爪50的夹爪头2探入挂钩20b之间,并通过导杆气缸3驱动包胶辊子4挤压弧形钢板100,将其顶边压入卡槽b、底边压入圆弧槽a,形成夹持固定,之后机器人本体30旋转,取出弧形钢板100,并到达辊道装置40上放,再之后,机器人本体30驱动机械夹爪50的夹爪头2探入辊道装置40的辊子之间,导杆气缸3撤回包胶辊子4,松开弧形钢板100,机器人本体30再驱动机械夹爪50抽离,完成弧形钢板100的转移过程。
26.本实施例的机械夹爪可通过多点定位,形成精确、稳定的弧形钢板夹持结构,为弧形钢板的自动化输送提供了条件。同时,通过呈锯齿状排列布置的卡槽,可适用于不同尺寸的弧形钢板夹持,实用性强。
技术特征:1.一种机械夹爪,其特征在于:包括夹爪本体(1)、夹爪头(2)、导杆气缸(3)、包胶辊子(4)、防护层(5)、托垫(6),所述夹爪头(2)呈l型,后端与所述夹爪本体(1)固定、上端固定所述防护层(5)、直角处固定所述托垫(6),所述防护层(5)与所述托垫(6)相邻,所述托垫(6)上开设有圆弧槽(a),所述防护层(5)上开设有卡槽(b),所述导杆气缸(3)固定在夹爪本体(1)上,所述包胶辊子(4)固定在所述导杆气缸(3)的输出端上,且与所述夹爪头(2)对位设置,所述卡槽(b)、圆弧槽(a)、包胶辊子(4)同向设置;所述卡槽(b)用于卡设弧形钢板的顶边,所述圆弧槽(a)用于抵靠所述弧形钢板的底边,所述导杆气缸(3)推动所述包胶辊子(4)按压在所述弧形钢板的凸面上,形成夹持固定。2.根据权利要求1所述的机械夹爪,其特征在于:还包括检测开关(7),所述检测开关(7)固定在所述夹爪本体(1)上,且朝向所述夹爪头(2)。3.根据权利要求2所述的机械夹爪,其特征在于:所述检测开关(7)采用光电检测开关。4.根据权利要求1所述的机械夹爪,其特征在于:所述卡槽(b)为多个,且呈锯齿状布置。5.根据权利要求1所述的机械夹爪,其特征在于:所述夹爪头(2)为多个,平行设置于所述夹爪本体(1)前端。6.根据权利要求1所述的机械夹爪,其特征在于:所述防护层(5)采用聚氨酯防护层。7.根据权利要求1所述的机械夹爪,其特征在于:所述托垫(6)采用尼龙托垫。8.一种弧形钢板自动取放系统,其特征在于:包括积放链轨道(10)、挂具(20)、机器人本体(30)、辊道装置(40)、如权利要求1~7任一所述的机械夹爪(50),所述机器人本体(30)设置于所述积放链轨道(10)与辊道装置(40)之间,所述机械夹爪(50)通过法兰连接所述机器人本体(30),所述挂具(20)包括框架本体(20a)和挂钩(20b),所述框架本体(20a)固定在所述积放链轨道(10)上,且沿所述积放链轨道(10)运动,所述挂钩(20b)成排的固定在所述框架本体(20a)上,用于放置弧形钢板;所述机械夹爪(50)在所述机器人本体(30)的驱动下,从所述挂钩(20b)上夹持所述弧形钢板,并放置到所述辊道装置(40)上。
技术总结本发明公开了一种机械夹爪,包括夹爪本体、夹爪头、导杆气缸、包胶辊子、防护层、托垫,夹爪头呈L型,后端与夹爪本体固定、上端固定防护层、直角处固定托垫,防护层与托垫相邻,托垫上开设有圆弧槽,防护层上开设有卡槽,导杆气缸固定在夹爪本体上,包胶辊子固定在导杆气缸的输出端上,且与夹爪头对位设置,卡槽、圆弧槽、包胶辊子同向设置;卡槽用于卡设弧形钢板的顶边,圆弧槽用于抵靠弧形钢板的底边,导杆气缸推动包胶辊子按压在弧形钢板的凸面上,形成夹持固定。本发明的优点是:通过多点定位,形成精确、稳定的弧形钢板夹持结构,为弧形钢板的自动化输送提供了条件。的自动化输送提供了条件。的自动化输送提供了条件。
技术研发人员:陈尧 魏云吉 张楠 赵善政
受保护的技术使用者:江苏金恒信息科技股份有限公司
技术研发日:2020.10.12
技术公布日:2022/4/12