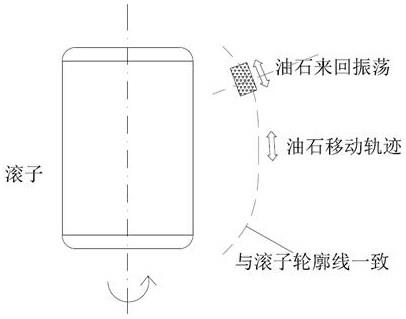
1.本发明涉及高铁轴承加工技术领域,具体涉及一种高铁轴承的对数曲线滚子加工的工艺。
背景技术:2.随着设备的发展和进步,各行各业对高精度对数曲线滚子的需求也越来越大,尤其是高铁轴承,目前中国高铁的轴承100%采用进口轴承,基本都被skf、fag、timken所垄断,因此国家提出在2023年高铁轴承国产化要达到30%,因此对高精度对数曲线滚子的需求也越来越多。
3.普通产品加工工艺:下料——车削——热处理——抛丸——粗磨外径——磨双端面——立式研磨端面——磨外径——细磨(切入磨)——终磨(切入磨)——光饰或超精——成品外观——包装。
4.终磨结束后,部分厂家通过超精或者光饰的方法来实现滚子对粗糙度和圆度的提升以及轮廓的修整。如采用传统的超精,则容易破坏对数曲线的轮廓,而使用光饰则容易产生磕碰伤等缺陷,并且粗糙度的一致性也很难得到保证。
技术实现要素:5.为了解决上述技术问题,本发明提出了一种高铁轴承的对数曲线滚子加工的工艺,设计工艺合理,提高产品质量。
6.本发明的技术方案如下:所述高铁轴承的对数曲线滚子加工的工艺的如下:下料——车削——热处理——抛丸——粗磨外径——磨双端面——立式研磨端面——磨外径1、2、3——切入磨/细磨——切入磨/终磨——超精——成品外观——包装;具体步骤如下,1)下料:利用四工位高速冷镦机将钢材拉丝后镦压成滚子毛坯。
7.2)车削:通过车床对滚子毛坯进行外径以及端面进行车削。
8.3)热处理:热处理是把车削后的滚子毛坯在固态范围内通过一定的加热、保温和冷却、清洗辅助完成对产品的淬、回火处理以改变其组织和性能。
9.4)抛丸:使用滚筒式抛丸机对热处理后的滚子进行抛丸处理,通过抛丸机内的钢沙喷到产品表面,将产品表面及凹穴和倒角上的氧化皮清理干净;同时通过滚筒的转动,将热处理结束的产品通过滚子之间碰撞、相互击打的方式释放产品表面的残余应力,使产品的机加工性能更稳定。
10.5)粗磨外径:磨削滚子的外径,去除部分磨量,使滚子的滚道面达到工艺尺寸要求,为后道磨外径1、2、3,切入磨/细磨,切入磨/终磨工序打下基础。
11.6)磨双端面:加工滚子的双端面,使其端面光滑平整。
12.7)立式研磨端面:滚子的双端面再次加工,提高滚子端面的粗糙度。
13.8)所述的磨外径1、2、3是指分三遍磨削,要求将滚子2
‑
15波圆度控制在0.5μm以
下,同时一遍又一遍的分开磨削。
14.9)所述切入磨/细磨:对于有对数曲线轮廓要求的高铁轴承的对数曲线滚子,细磨外径磨削线对轮廓的设计要求,细磨轮廓中间部分采用直线过渡,为了产品在终磨时滚子在刀板上呈线接触;同时为了避免烧伤的产生,细磨切入时两侧轮廓设为轮廓下限。
15.10)~11)所述切入磨/终磨——超精,本工艺采用切入时超精的方式对滚子的凸度进行加工,即滚子自转,将油石已恒定的压力压覆在滚子表面,而油石的震荡轨迹则按照产品对数曲线轮廓线移动,从而保证了每个面的切削量都一致,确保不会破坏滚子的轮廓形状。除此之外,二工位则采用砂带对滚子的表面进行抛光,进一步提高滚子的粗糙度和圆度,对于表面超精纹路有特殊要求的产品,可通过改变砂带震荡头的震荡频次和幅度来调整超精面的花纹形状,从而生产出交叉纹或者顺纹的产品。
16.12)成品外观:采用德国ibg生产的涡流探伤设备,对滚子的展开,从而进行100%涡流探伤,主要检测滚子表面的缺陷及内部组织的裂纹。
17.13)包装:为保障产品的一致性,同时为了避免磕碰伤的产生,本工艺采用自行研发的管式包装机对高精度产品进行管式包装。
18.本发明的优点是设计巧妙合理,提高滚子外径和端面的垂直度和圆度;细磨(切入磨)外径:产品在终磨时滚子在刀板上呈线接触,而非点接触,增加滚子在磨削过程中的稳定性,从而避免轮廓对圆度的影响;采用切入时超精的方式对滚子的凸度进行加工,保证了每个面的切削量都一致,确保不会破坏滚子的轮廓形状。
附图说明
19.图1是对数曲线轮廓示意图。
20.图2是中间直线过渡轮廓示意图。
21.图3是细磨切入时两侧轮廓设为轮廓下限的示意图。
22.图4是切入时超精的示意图。
具体实施方式
23.参照附图,高铁轴承的对数曲线滚子加工的工艺:下料——车削——热处理——抛丸——粗磨外径——磨双端面——立式研磨端面——磨外径1、2、3——细磨(切入磨)——终磨(切入磨)——超精——成品外观——包装。
24.控制要点:细磨外径1、2、3要求将滚子2
‑
15波圆度控制在0.5μm以下,同时一遍又一遍的分开磨削是为了提高滚子外径和端面的垂直度和圆度。
25.细磨(切入磨)外径:如图1对于有对数曲线轮廓要求的产品,细磨外径磨削线对轮廓的设计区别于其他产品,细磨轮廓中间部分采用直线过渡【图2所示】,而非采用直接的对数曲线参数,目的是为了产品在终磨时滚子在刀板上呈线接触,而非点接触,增加滚子在磨削过程中的稳定性,从而避免轮廓对圆度的影响。同时为了避免烧伤的产生,如图3,细磨切入时两侧轮廓设为轮廓下限。
26.终磨结束后,部分厂家通过超精或者光饰的方法来实现滚子对粗糙度和圆度的提升以及轮廓的修整。如采用传统的超精,则容易破坏对数曲线的轮廓,而使用光饰则容易产生磕碰伤等缺陷,并且粗糙度的一致性也很难得到保证。
27.本工艺采用切入时超精的方式对滚子的凸度进行加工,即滚子自转,如图4中,左侧是滚子,右侧是油石以及油石运行轨迹,操作时将油石已恒定的压力压覆在滚子表面,而油石的震荡轨迹则按照产品对数曲线轮廓线移动,从而保证了每个面的切削量都一致,确保不会破坏滚子的轮廓形状。除此之外,二工位则采用砂带对滚子的表面进行抛光,进一步提高滚子的粗糙度和圆度,对于表面超精纹路有特殊要求的产品,可通过改变砂带震荡头的震荡频次和幅度来调整超精面的花纹形状,从而生产出交叉纹或者顺纹的产品。
技术特征:1.高铁轴承的对数曲线滚子加工的工艺,其特征在于,所述高铁轴承的对数曲线滚子加工的工艺的如下:下料——车削——热处理——抛丸——粗磨外径——磨双端面——立式研磨端面——磨外径1、2、3——切入磨/细磨——切入磨/终磨——超精——成品外观——包装;所述的磨外径1、2、3是指分三遍磨削,要求将滚子2
‑
15波圆度控制在0.5μm以下,同时一遍又一遍的分开磨削;所述切入磨/细磨:对于有对数曲线轮廓要求的高铁轴承的对数曲线滚子,细磨外径磨削线对轮廓的设计要求,细磨轮廓中间部分采用直线过渡,为了产品在终磨时滚子在刀板上呈线接触;同时为了避免烧伤的产生,细磨切入时两侧轮廓设为轮廓下限;所述切入磨/终磨——超精,本工艺采用切入时超精的方式对滚子的凸度进行加工,即滚子自转,将油石已恒定的压力压覆在滚子表面,而油石的震荡轨迹则按照产品对数曲线轮廓线移动,从而保证了每个面的切削量都一致,确保不会破坏滚子的轮廓形状;除此之外,二工位则采用砂带对滚子的表面进行抛光,进一步提高滚子的粗糙度和圆度,对于表面超精纹路有特殊要求的产品,可通过改变砂带震荡头的震荡频次和幅度来调整超精面的花纹形状,从而生产出交叉纹或者顺纹的产品。2.根据权利要求1所述的高铁轴承的对数曲线滚子加工的工艺,其特征在于,具体步骤如下,1)下料:利用四工位高速冷镦机将钢材拉丝后镦压成滚子毛坯;2)车削:通过车床对滚子毛坯进行外径以及端面进行车削;3)热处理:热处理是把车削后的滚子毛坯在固态范围内通过一定的加热、保温和冷却、清洗辅助完成对产品的淬、回火处理以改变其组织和性能;4)抛丸:使用滚筒式抛丸机对热处理后的滚子进行抛丸处理,通过抛丸机内的钢沙喷到产品表面,将产品表面及凹穴和倒角上的氧化皮清理干净;同时通过滚筒的转动,将热处理结束的产品通过滚子之间碰撞、相互击打的方式释放产品表面的残余应力,使产品的机加工性能更稳定,5)粗磨外径:磨削滚子的外径,去除部分磨量,使滚子的滚道面达到工艺尺寸要求,为后道磨外径1、2、3,切入磨/细磨,切入磨/终磨工序打下基础;6)磨双端面:加工滚子的双端面,使其端面光滑平整;7)立式研磨端面:滚子的双端面再次加工,提高滚子端面的粗糙度;8)~11)采用权利要求1中所述的步骤,12)成品外观:采用德国ibg生产的涡流探伤设备,对滚子的展开,从而进行100%涡流探伤,主要检测滚子表面的缺陷及内部组织的裂纹;13)包装:为保障产品的一致性,同时为了避免磕碰伤的产生,本工艺采用自行研发的管式包装机对高精度产品进行管式包装。
技术总结本发明涉及一种高铁轴承的对数曲线滚子加工的工艺,如下:磨外径1、2、3分三遍磨削,要求将滚子2
技术研发人员:苏银建 郭凡钢 从远东
受保护的技术使用者:江苏力星通用钢球股份有限公司
技术研发日:2021.06.23
技术公布日:2021/9/13