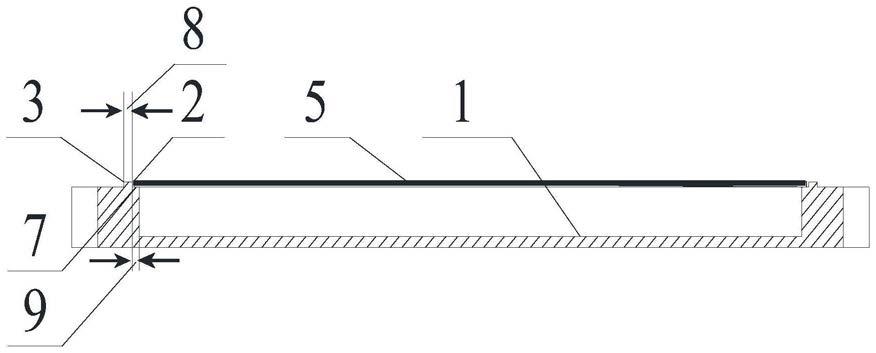
1.本实用新型涉及一种管壳封装结构,具体是涉及一种实现硅铝管壳激光封焊不同焊接面的结构,属于封装结构部件技术领域。
背景技术:2.随着微波混合集成电路向“小型化、轻量化、多功能、高可靠性”方向发展,ltcc基板作为能够内置元件的基板得到了广泛的应用。但ltcc基板由于其陶瓷特性,热膨胀系数较小,需搭配热膨胀系数匹配的管壳,且管壳应具有良好的导热性能。硅铝合金作为一种以铝为基体,以硅为增强体的人工合成复合材料,具有易加工、高导热、高强度、低密度等优点,较好地适合作为ltcc基板的管壳。同时微波混合集成电路小型化的设计过程中,须使用大量的裸片,为保证其长期可靠性,需要将其封装起来。激光封焊具有局部加热,焊缝窄,腔体内气氛可控等优点,是目前硅铝管壳气密封装的最常用方法。
3.王松等人在《微波组件用硅铝合金的激光封焊工艺研究》,徐骁等人在《电子封装用硅铝合金激光气密焊接研究》等文献中对硅铝合金的激光封焊工艺均进行了研究,并都提出为阻止封焊过程中管壳表面焊接热裂纹的产生,应对管壳焊接面的结构应进行优化,焊缝中心距管壳边缘的距离控制在0.8mm。但这种设计对微波组件的连接器安装结构及安装角的设计造成了较大的困难。为保证硅铝合金管壳安装角结构设计的强度及连接器安装结构的设计,同时,避免封焊过程中热裂纹的产生,急需提出一种新的封焊结构。
技术实现要素:4.为解决上述问题,本实用新型公开了一种实现硅铝管壳激光封焊不同焊接面的结构,该技术方案的硅铝结构加工简单、易于实现,封焊完成后的焊缝质量有保证。
5.为了实现上述目的,本实用新型的技术方案如下:
6.提供一种实现硅铝管壳激光封焊不同焊接面的结构,硅铝管壳和盖板,所述硅铝管壳包括焊接面、应力槽、焊接面与台阶, 所述硅铝管壳结构的周边设置宽度不同的预留边,所述硅铝管壳结构还设置水平的台阶,在所述预留边和所述台阶之间设置应力槽,所述应力槽高出预留边和台阶且具备设定宽度,所述应力槽高出台阶的部位形成焊接面,所述硅铝管壳结构的焊接面为激光封焊时的焊接区域,所述硅铝管壳的应力槽用于封焊过程中管壳形变时的应力缓冲,所述焊接面与盖板搭接处的台阶用于盖板封焊时的定位。
7.进一步地,所述硅铝管壳材料为al50si,所述盖板的材料为al27si。
8.进一步地,所述硅铝管壳还包括安装孔,所述安装孔设置在预留边中相对宽度较宽的边。
9.进一步地,所述台阶宽度的不低于0.8mm。
10.进一步地,所述应力槽宽度等于所述硅铝管壳预留边中窄边的宽度。
11.进一步地,所述盖板的长宽不超过80
×
80cm,所述盖板厚度不低于0.5mm。
12.进一步地,所述应力槽的厚度不低于盖板的厚度。
13.本实用新型所取得的有益技术效果:1)该方案加工简单、易于实现。通过设置应力槽和台阶这种优化结构,优化后的硅铝管壳的封焊质量一致性可以得到保证;2)通过该方案封焊的硅铝管壳漏率满足gjb 360b工艺112条件c所要求的2.03
×
10
‑2pa
·
cm3/s的要求;3)通过本实用新型设计的结构,管壳的安装角及连接器在设计时更加容易,可以避免因硅铝材料脆性导致的安装开裂等可靠性问题;4)该方案加工过程成本较低,有助于进一步的推广。
附图说明
14.图1是实施例提供的实现硅铝管壳激光封焊不同焊接面结构的装配连接示意图;
15.图2是实施例提供的实现硅铝管壳激光封焊不同焊接面结构的装配连接示意放大图;
16.图3是实施例提供的实现硅铝管壳激光封焊不同焊接面结构的管壳示意图。
17.图4是实施例提供的实现硅铝管壳激光封焊不同焊接面结构封焊后的焊缝示意图;
18.图中:1、硅铝管壳;2、表面设计有焊接面;3、应力槽;4、安装孔;5、盖板;6、焊缝;7、台阶;8、应力槽的宽度;9、台阶宽度;10、硅铝壳体的窄边;11、硅铝壳体的窄边宽度;12、硅铝壳体的宽边;13、应力槽的厚度。
具体实施方式
19.下面结合附图和具体实施方式,进一步阐明本实用新型,应理解下述具体实施方式仅用于说明本实用新型而不用于限制本实用新型的范围。
20.实施例1:参见图1
‑
3,本实用新型涉及一种实现硅铝管壳激光封焊不同焊接面的结构的装配连接示意图和管壳示意图,如图所示,所述包括:硅铝管壳1和盖板5,所述硅铝管壳1包括焊接面2、应力槽3、焊接面2与盖板5搭接处的台阶7, 所述硅铝管壳结构的周边设置宽度不同的预留边,所述预留边如图所示包括硅铝壳体的窄边10、其宽度见硅铝壳体的窄边宽度11和硅铝壳体的宽边12;所述硅铝管壳1结构还设置水平的台阶7,在所述预留边和所述台阶7之间设置应力槽3,所述应力槽3高出预留边和台阶7且具备设定宽度,所述应力槽3高出台阶7的部位形成焊接面2,所述硅铝管壳1用于激光密封,所述硅铝管壳结构1的焊接面2为激光封焊时的焊接区域,所述硅铝管壳的应力槽3用于封焊过程中管壳形变时的应力缓冲,所述焊接面2与盖板5搭接处的台阶7用于盖板5封焊时的定位。所述焊接面2的焊缝中心距管壳边缘的距离不相同,便于管壳设计时的安装角及连接器的设计。
21.本实施例中,所述硅铝管壳1壳体材料为al50si,适合微波组件中与陶瓷基板及gaas单片热膨胀系数的匹配,所述盖板5材料为al27si,材料中有更多的金属相,更好的的塑性变形能力,用于抵消封焊过程中的热应力。
22.台阶宽度9不低于0.8mm,防止封焊过程中激光击穿至管壳内部。应力槽的宽度8等于所述硅铝管壳1预留边中窄边的宽度11,该宽度不超过1mm。所述应力槽3的厚度13不低于盖板5的厚度,便于封焊过程中管壳形变时的应力缓冲。本实施例中所述硅铝管壳1中盖板5的长宽不超过80
×
80cm,所述盖板5厚度不低于0.5mm,防止因盖板5变形对焊缝产生较大的机械应力。
23.实施例2:在实施例1的基础上,本实施例提供的一种实现硅铝管壳激光封焊不同焊接面的结构,所述硅铝管壳1还包括安装孔4,所述安装孔设置在预留边中相对宽度较宽的边。安装孔4用于硅铝管壳与其他产品的互连。
24.本结构在焊接时先采用超声波清洗机进行硅铝管壳激光密封前的清洗,然后采用激光封焊系统用于硅铝管壳的真空烘烤、激光密封,利用压力工装用于点焊前盖板与管壳的固定。封焊出的焊缝6示意图见图4。
25.本实用新型方案所公开的技术手段不仅限于上述实施方式所公开的技术手段,还包括由以上技术特征任意组合所组成的技术方案。应当指出,对于本技术领域的普通技术人员来说,在不脱离本实用新型原理的前提下,还可以做出若干改进和润饰,这些改进和润饰也视为本实用新型的保护范围。
技术特征:1.一种实现硅铝管壳激光封焊不同焊接面的结构,其特征在于,包括:硅铝管壳和盖板,所述硅铝管壳包括焊接面、应力槽、焊接面与台阶,所述硅铝管壳结构的周边设置宽度不同的预留边,所述硅铝管壳结构还设置水平的台阶,在所述预留边和所述台阶之间设置应力槽,所述应力槽高出预留边和台阶且具备设定宽度,所述应力槽高出台阶的部位形成焊接面,所述硅铝管壳结构的焊接面为激光封焊时的焊接区域,所述硅铝管壳的应力槽用于封焊过程中管壳形变时的应力缓冲,所述焊接面与盖板搭接处的台阶用于盖板封焊时的定位。2.根据权利要求1所述的一种实现硅铝管壳激光封焊不同焊接面的结构,其特征在于,所述硅铝管壳材料为al50si,所述盖板的材料为al27si。3.根据权利要求1所述的一种实现硅铝管壳激光封焊不同焊接面的结构,其特征在于,所述硅铝管壳还包括安装孔,所述安装孔设置在预留边中相对宽度较宽的边。4.根据权利要求1所述的一种实现硅铝管壳激光封焊不同焊接面的结构,其特征在于,所述台阶宽度的不低于0.8mm。5.根据权利要求1所述的一种实现硅铝管壳激光封焊不同焊接面的结构,其特征在于,所述应力槽宽度等于所述硅铝管壳预留边中窄边的宽度。6.根据权利要求1所述的一种实现硅铝管壳激光封焊不同焊接面的结构,其特征在于,所述盖板的长宽不超过80
×
80cm,所述盖板厚度不低于0.5mm。7.根据权利要求1所述的一种实现硅铝管壳激光封焊不同焊接面的结构,其特征在于,所述应力槽的厚度不低于盖板的厚度。
技术总结本实用新型公开一种实现硅铝管壳激光封焊不同焊接面的结构,包括:硅铝管壳和盖板,硅铝管壳包括焊接面、应力槽、焊接面与盖板搭接处的台阶,硅铝管壳结构的周边设置宽度不同的预留边,硅铝管壳结构还设置水平的台阶,在预留边和台阶之间设置应力槽,应力槽高出预留边和台阶且具备设定宽度,应力槽高出台阶的部位形成焊接面,硅铝管壳结构的焊接面为激光封焊时的焊接区域,硅铝管壳的应力槽用于封焊过程中管壳形变时的应力缓冲,焊接面与盖板搭接处的台阶用于盖板封焊时的定位。本实用新型公开一种实现硅铝管壳激光封焊不同焊接面的结构加工简单、易于实现,并且封焊质量一致性可以得到保证。得到保证。得到保证。
技术研发人员:李益兵 董昌慧
受保护的技术使用者:南京恒电电子有限公司
技术研发日:2021.02.09
技术公布日:2021/11/14