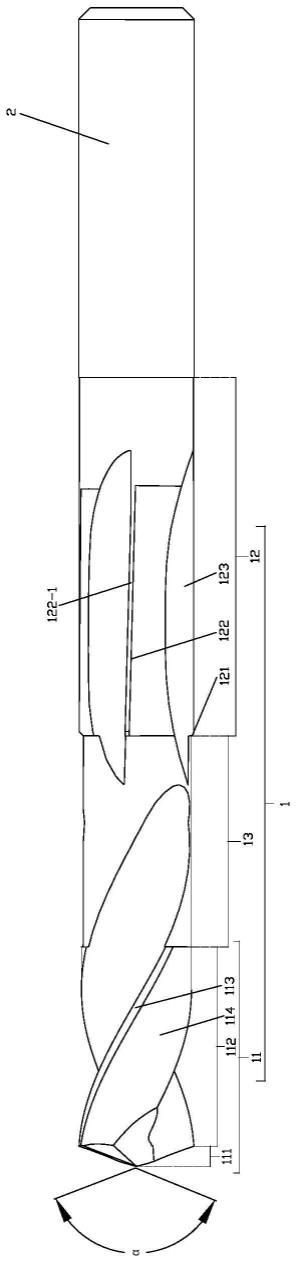
1.本实用新型涉及一种钻铰一体式复合刀具。
背景技术:2.在机械制造中,孔的加工一般是先用钻头钻孔,但是钻头钻孔通常毛刺较多、表面粗糙度大,所以还需要更换铰刀进行铰孔,使孔达到高的精度和低粗糙度。孔的加工至少需要用到两种刀具,分两次才能加工完成,加工复杂,而且牵涉到更换刀具,对孔加工的精度也有一定的影响,大大降低了生产效率。
技术实现要素:3.本实用新型要解决的技术问题是:克服现有技术中之不足,提供一种钻铰一体式复合刀具。
4.本实用新型解决其技术问题所采用的技术方案是:一种钻铰一体式复合刀具,包括一体结构的刀体和刀柄,所述刀体包括前部钻头段和后部铰刀段,所述钻头段由钻尖和钻身组成,所述钻尖设有双后角结构,自钻尖边沿向钻身外周延伸形成有钻头刃带,所述钻身沿圆周分布有两条螺旋槽,所述铰刀段包括引导锥和周刃,所述引导锥设置在铰刀段的前端,所述周刃分布在铰刀段的外周上,所述铰刀段的外周上还均匀分布有四条排屑沟槽。
5.该刀具同时融合了钻头和铰刀设计结构,刀体的前部为钻头结构,其后部为铰刀结构,可实现在不换刀的情况下同时完成钻孔及铰孔两道工序,节省刀具数量及换刀时间,且在加工时排屑顺畅,保证加工孔的精度要求。
6.进一步地限定,所述钻头段与铰刀段之间设有过渡段,所述螺旋槽的后部及排屑沟槽的前部均延伸至过渡段上,所述引导锥连接在过渡段的末端。
7.设置过渡段,在钻头段钻完孔后留一段距离便于钻孔的排屑,再进行铰孔,可以避免钻孔废屑影响后续的铰孔质量,引导锥能使得刀具快速准确进入铰刀段进行铰孔。
8.为了便于加工时的识别,更进一步地限定,所述过渡段的直径为钻身直径减少1mm。
9.为了起到较好地引导作用,且为了加工方便,进一步地限定,所述引导锥的角度为30
°
~60
°
。
10.为了保证钻身外周的切削强度,进一步地限定,所述钻头刃带的宽度为钻身直径的0.055。
11.进一步地限定,所述钻尖包括第一后角和第二后角,所述第一后角的角度为8
°
~12
°
,所述第二后角的角度为20
°
~30
°
。
12.如此设置,可以减少受力,达到减小磨损作用。
13.进一步地限定,所述钻尖的顶角为130
°
~140
°
,钻尖上设有长度小于0.1mm的横刃。
14.如此设置,钻尖的横刃短,定心好,适用于多种材料及加工工况。
15.为了保证铰刀外周的切削强度,进一步地限定,所述周刃具有宽度为铰刀段直径0.03的铰刀刃带。
16.本实用新型的有益效果是:本实用新型刀具同时融合了钻头和铰刀设计结构,刀体的前部为钻头结构,其后部为铰刀结构,可实现在不换刀的情况下同时完成钻孔及铰孔两道工序,节省刀具数量及换刀时间,且在加工时排屑顺畅,保证加工孔的精度要求,大大提高生产效率。
附图说明
17.下面结合附图和实施方式对本实用新型进一步说明。
18.图1是本实用新型钻铰一体式复合刀具的主视图。
19.图2是本实用新型钻铰一体式复合刀具的左视图。
20.图中:1.刀体,2.刀柄,11.钻头段,12.铰刀段,13.过渡段,111.钻尖,112.钻身,113.钻头刃带,114.螺旋槽,121.引导锥,122.周刃,123.排屑沟槽,111-1.第一后角,111-2.第二后角,111-3.横刃,122-1.铰刀刃带。
具体实施方式
21.现在结合附图对本实用新型作进一步的说明。这些附图均为简化的示意图仅以示意方式说明本实用新型的基本结构,因此其仅显示与本实用新型有关的构成。
22.如图1~2所示,一种钻铰一体式复合刀具,包括一体结构的刀体1和刀柄2,刀体1包括前部钻头段11和后部铰刀段12,钻头段11由钻尖111和钻身112组成,钻尖111设有双后角结构,自钻尖111边沿向钻身112外周延伸形成有钻头刃带113,钻身112沿圆周分布有两条螺旋槽114,铰刀段12包括引导锥121和周刃122,引导锥121设置在铰刀段12的前端,周刃122分布在铰刀段12的外周上,铰刀段12的外周上还均匀分布有四条排屑沟槽123。
23.在本实施例中,钻头段11与铰刀段12之间设有过渡段13,螺旋槽114的后部及排屑沟槽123的前部均延伸至过渡段13上,引导锥121连接在过渡段13的末端。过渡段13的直径为钻身112直径减少1mm。引导锥121的角度为30
°
~60
°
。
24.在本实施例中,钻头刃带113的宽度为钻身112直径的0.055。钻尖111包括第一后角111-1和第二后角111-2,第一后角111-1的角度为8
°
~12
°
,第二后角111-2的角度为20
°
~30
°
。钻尖111的顶角α为130
°
~140
°
,钻尖111上设有长度小于0.1mm的横刃111-3。
25.在本实施例中,周刃122具有宽度为铰刀段直径0.03的铰刀刃带122-1。
26.本实施例的刀具通过将刀体的前部设为钻头结构,其后部设为铰刀结构,实现了钻孔铰孔一体,有效减少加工过程中换刀次数和断刀检测次数,大大提高了生产效率;通过在钻头段11与铰刀段12之间设有过渡段13,保证钻孔的排屑不影响后续的铰孔,再加上引导锥121,可以很顺利地由钻孔进入铰孔作业,不存在卡塞停顿,大大提高了生产效率的优点。
27.上述实施方式只为说明本实用新型的技术构思及特点,其目的在于让熟悉此项技术的人士能够了解本实用新型的内容并加以实施,并不能以此限制本实用新型的保护范围,凡根据本实用新型精神实质所作的等效变化或修饰,都应涵盖在本实用新型的保护范围内。
技术特征:1.一种钻铰一体式复合刀具,包括一体结构的刀体和刀柄,其特征在于:所述刀体包括前部钻头段和后部铰刀段,所述钻头段由钻尖和钻身组成,所述钻尖设有双后角结构,自钻尖边沿向钻身外周延伸形成有钻头刃带,所述钻身沿圆周分布有两条螺旋槽,所述铰刀段包括引导锥和周刃,所述引导锥设置在铰刀段的前端,所述周刃分布在铰刀段的外周上,所述铰刀段的外周上还均匀分布有四条排屑沟槽。2.根据权利要求1所述的钻铰一体式复合刀具,其特征在于:所述钻头段与铰刀段之间设有过渡段,所述螺旋槽的后部及排屑沟槽的前部均延伸至过渡段上,所述引导锥连接在过渡段的末端。3.根据权利要求2所述的钻铰一体式复合刀具,其特征在于:所述过渡段的直径为钻身直径减少1mm。4.根据权利要求2所述的钻铰一体式复合刀具,其特征在于:所述引导锥的角度为30
°
~60
°
。5.根据权利要求1所述的钻铰一体式复合刀具,其特征在于:所述钻头刃带的宽度为钻身直径的0.055。6.根据权利要求1所述的钻铰一体式复合刀具,其特征在于:所述钻尖包括第一后角和第二后角,所述第一后角的角度为8
°
~12
°
,所述第二后角的角度为20
°
~30
°
。7.根据权利要求1所述的钻铰一体式复合刀具,其特征在于:所述钻尖的顶角为130
°
~140
°
,钻尖上设有长度小于0.1mm的横刃。8.根据权利要求1所述的钻铰一体式复合刀具,其特征在于:所述周刃具有宽度为铰刀段直径0.03的铰刀刃带。
技术总结本实用新型涉及一种钻铰一体式复合刀具,包括一体结构的刀体和刀柄,所述刀体包括前部钻头段和后部铰刀段,所述钻头段由钻尖和钻身组成,所述钻尖设有双后角结构,自钻尖边沿向钻身外周延伸形成有钻头刃带,所述钻身沿圆周分布有两条螺旋槽,所述铰刀段包括引导锥和周刃,所述引导锥设置在铰刀段的前端,所述周刃分布在铰刀段的外周上,所述铰刀段的外周上还均匀分布有四条排屑沟槽。本实用新型刀具同时融合了钻头和铰刀设计结构,刀体的前部为钻头结构,其后部为铰刀结构,可实现在不换刀的情况下同时完成钻孔及铰孔两道工序,节省刀具数量及换刀时间,且在加工时排屑顺畅,保证加工孔的精度要求,大大提高生产效率。大大提高生产效率。大大提高生产效率。
技术研发人员:邱威宇
受保护的技术使用者:元韬(常州)精密切削技术有限公司
技术研发日:2021.10.01
技术公布日:2022/8/2