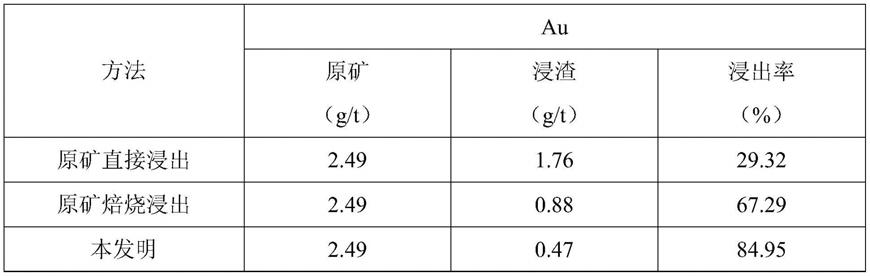
1.本发明属于含金矿石的选冶方法,尤其涉及一种多硫化物微细粒浸染型含金矿石选冶联合方法。
背景技术:2.目前国内外在难处理金矿资源领域,普遍采用含金矿石预处理、氰化提金的选冶工艺,预处理的目的主要是解决硫化矿物包裹金的问题,预处理技术主要为生物氧化、热压氧化、焙烧氧化三种,根据原料的差异及国家地区具体情况而采用相应的处理技术,预处理后的矿物提金技术均为传统的氰化提金技术。任何单一工艺都具有一定的局限性,随着环保意识的提高,矿产资源的日益匮乏,需要开发一种针对于多硫化物微细粒浸染型含金矿石的联合工艺,达到综合经济效益高、矿石有价元素利用率高的目的。
3.长春黄金研究院有限公司开发的cg505系列浸金剂采用中国专利cn105032622b《一种选矿药剂的两段合成方法》、通过两段合成工艺制备,产品品质高,杂质少,具有浸金能力强、药剂毒性低、适应性广的特点,生产工艺安全环保,且能满足黄金矿山严苛的环保要求,该浸金剂通过“协同浸出”与“原位治理”作用,不仅可替代氰化物实现金的高效浸出,同时可使浸出尾液达到国家排放标准。
技术实现要素:4.本发明提供一种多硫化物微细粒浸染型含金矿石选冶联合方法,用于处理多硫化物微细粒浸染型含金矿石。
5.本发明采取的技术方案是,包括下列步骤:
6.(一)、焙烧:在-0.074mm含量占80%~90%条件下,在600℃~700℃条件下对进行焙烧,焙烧时间1h~3h;
7.(二)、制酸:利用焙烧产生的so2烟气制硫酸;
8.(三)、酸浸:以硫酸产率与焙砂产率的比值确定硫酸用量,按照矿浆浓度50%,将焙砂与酸液混合,酸浸矿浆温度保持在80℃,酸浸时间2h;
9.(四)、浸出:酸浸矿浆压滤后,酸液回用,酸渣调碱ph至11.5,进行浸出工艺。
10.本发明所述步骤(一)中矿石为多硫化物微细粒浸染型含金矿石。
11.本发明所述步骤(四)中浸出工艺采用cg505系列浸金剂。
12.本发明与现行的常规选冶方法相比,优点是:可有效地提高多硫化物微细粒浸染型含金矿石的金浸出率;无环保治理压力,综合利用多硫化物微细粒浸染型含金矿石中的有价元素,有价元素综合利用率高,经济效益显著。
附图说明
13.图1是本发明的流程图。
具体实施方式
14.实施例1
15.包括下列步骤:
16.(一)、焙烧:在-0.074mm含量占80%条件下,在600℃条件下对矿石进行焙烧,焙烧时间1h;
17.(二)、制酸:利用焙烧产生的so2烟气制硫酸;
18.(三)、酸浸:以硫酸产率与焙砂产率的比值确定硫酸用量,按照矿浆浓度50%,将焙砂与酸液混合,酸浸矿浆温度保持在80℃,酸浸时间2h;
19.(四)、浸出:酸浸矿浆压滤后,酸液回用,酸渣调碱ph至11.5,采用cg505系列浸金剂进行浸出工艺。
20.实施例2
21.(一)、焙烧:在-0.074mm含量占85%条件下,在650℃条件下对矿石进行焙烧,焙烧时间2h;
22.(二)、制酸:利用焙烧产生的so2烟气制硫酸;
23.(三)、酸浸:以硫酸产率与焙砂产率的比值确定硫酸用量,按照矿浆浓度50%,将焙砂与酸液混合,酸浸矿浆温度保持在80℃,酸浸时间2h;
24.(四)、浸出:酸浸矿浆压滤后,酸液回用,酸渣调碱ph至11.5,采用cg505系列浸金剂进行浸出工艺。
25.实施例3
26.(一)、焙烧:在-0.074mm含量占90%条件下,在700℃条件下对矿石进行焙烧,焙烧时间3h;
27.(二)、制酸:利用焙烧产生的so2烟气制硫酸;
28.(三)、酸浸:以硫酸产率与焙砂产率的比值确定硫酸用量,按照矿浆浓度50%,将焙砂与酸液混合,酸浸矿浆温度保持在80℃,酸浸时间2h;
29.(四)、浸出:酸浸矿浆压滤后,酸液回用,酸渣调碱ph至11.5,采用cg505系列浸金剂进行浸出工艺。
30.上述实施例中,所述步骤(一)中矿石为多硫化物微细粒浸染型含金矿石。
31.cg505系列浸金剂采用中国专利cn105032622b《一种选矿药剂的两段合成方法》制备。
32.下边通过具体实例来进一步说明本发明。
33.选用某矿业有限公司的多硫化物微细粒浸染型含金矿石,其成分au 2.49g/t,ag 2.12g/t,as 0.824%、cu 0.019%、pb 0.005%、zn 0.14%、fe 10.25%、sb 0.005%、c 2.55%、s 9.95%。
34.一、焙烧
35.在矿石细度为-0.074mm含量80%,焙烧温度600℃,焙烧时间1.5h的条件下,焙砂、烟尘产率分别为77.32%、14.64%,烟气so2含量109000mg/m3;
36.二、制酸
[0037]“两吸两转”制酸工艺,产出98%浓硫酸250kg/t
混合砂
;
[0038]
三、硫酸酸浸
[0039]
采取酸液循环使用的方式,按照矿浆浓度50%,将焙砂与酸液混合,保持酸浸矿浆温度80℃,酸浸2h;
[0040]
四、浸出:
[0041]
酸浸矿浆压滤后,酸液回用,酸渣调碱ph至11.5,采用cg505浸出。
[0042]
五、分析结果
[0043]
浸出结束后,将浸渣进行洗涤,抽滤,烘干后,送分析室测定金含量,计算金的浸出率。其结果如表1所示。
[0044]
表1试验结果
[0045][0046]
可见本发明金的浸出率得到有效地提高,浸渣中的金含量相对最低。
技术特征:1.一种多硫化物微细粒浸染型含金矿石选冶联合方法,其特征在于,包括下列步骤:(一)、焙烧:在-0.074mm含量占80%~90%条件下,在600℃~700℃条件下对进行焙烧,焙烧时间1h~3h;(二)、制酸:利用焙烧产生的so2烟气制硫酸;(三)、酸浸:以硫酸产率与焙砂产率的比值确定硫酸用量,按照矿浆浓度50%,将焙砂与酸液混合,酸浸矿浆温度保持在80℃,酸浸时间2h;(四)、浸出:酸浸矿浆压滤后,酸液回用,酸渣调碱ph至11.5,进行浸出工艺。2.根据权利要求1所述的一种多硫化物微细粒浸染型含金矿石选冶联合方法,其特征在于:所述步骤(一)中矿石为多硫化物微细粒浸染型含金矿石。3.根据权利要求1所述的一种多硫化物微细粒浸染型含金矿石选冶联合方法,其特征在于:所述步骤(四)中浸出工艺采用cg505系列浸金剂。
技术总结本发明涉及一种多硫化物微细粒浸染型含金矿石选冶联合方法,属于含金矿石的选冶方法。在-0.074mm含量占80%~90%条件下,在600℃~700℃条件下对进行焙烧,焙烧时间1h~3h;利用焙烧产生的SO2烟气制硫酸;以硫酸产率与焙砂产率的比值确定硫酸用量,按照矿浆浓度50%,将焙砂与酸液混合,酸浸矿浆温度保持在80℃,酸浸时间2h;酸浸矿浆压滤后,酸液回用,酸渣调碱pH至11.5,进行浸出工艺。优点是:可有效地提高多硫化物微细粒浸染型含金矿石的金浸出率;无环保治理压力,综合利用多硫化物微细粒浸染型含金矿石中的有价元素,有价元素综合利用率高,经济效益显著。经济效益显著。
技术研发人员:王鹏 郝福来 李健
受保护的技术使用者:长春黄金研究院有限公司
技术研发日:2021.11.09
技术公布日:2022/3/25