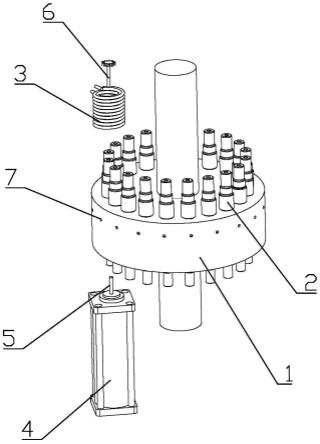
1.本实用新型属于零件淬火的技术领域,涉及一种高频淬火机床用自动转盘。
背景技术:2.企业在面对人力工资持续上涨、生产成本不断增大局面的时候,自动化设备的研发和投入已成为缓解人力问题的首选项。
3.小轴类零件的感应淬火通常情况是操作员工将需要加工的小轴类零件单个放到感应器线圈的顶尖部位,完成淬火工序后再手动拿下该零件,再重复下一个工作,如此需要一个员工持续在一台机器面前工作,不仅效率低下,也存在一定的安全风险。
技术实现要素:4.本实用新型针对现有技术的不足,提供了一种高频淬火机床用自动转盘,实现了轴类零件淬火的自动化,提高了工作效率,节省了人力成本。
5.为解决上述技术问题,本实用新型的目的通过下述技术方案得以实现:
6.一种高频淬火机床用自动转盘,包括转动设置在机床上的转盘,所述转盘上周向设置有若干上料工位,所述上料工位内放置有待淬火的轴类零件,所述轴类零件的轴线与转盘的轴线平行设置,所述转盘的上方设置有淬火工位,所述淬火工位包括对轴类零件进行淬火的感应线圈,转盘转动时上料工位依次经过淬火工位所对应的位置,所述转盘的下方设置有驱动轴类零件轴向移动至感应线圈内的驱动装置,所述驱动装置位于淬火工位所对应的位置。
7.在上述的一种高频淬火机床用自动转盘中,优选的,所述上料工位等间距设置。
8.在上述的一种高频淬火机床用自动转盘中,所述上料工位设置有轴向贯穿转盘的通孔,所述轴类零件穿设在通孔中。
9.在上述的一种高频淬火机床用自动转盘中,所述轴类零件上设置有台阶结构,所述通孔与台阶结构配合限位。
10.在上述的一种高频淬火机床用自动转盘中,所述驱动装置的执行单元上连接有与轴类零件下端匹配的下顶尖,驱动装置驱动下顶尖向上运动顶起轴类零件,所述感应线圈上方设置有与轴类零件上端匹配的上顶尖,上顶尖与下顶尖配合固定淬火的轴类零件,所述上顶尖由动力装置驱动旋转,并带动轴类零件同时旋转。
11.在上述的一种高频淬火机床用自动转盘中,所述驱动装置包括驱动气缸,所述驱动气缸竖直设置,所述下顶尖连接在其活塞杆上。所述驱动装置还可以使用电机等其他装置。
12.在上述的一种高频淬火机床用自动转盘中,所述转盘上设置有与每个上料工位对应的位置感应器。所述位置感应器采用本领域的通用感应器,例如角度感应器、接近感应器、对射感应器等。
13.在上述的一种高频淬火机床用自动转盘中,所述转盘的外周面设置有若干安装凹
槽,所述位置感应器设置在安装凹槽内。
14.在上述的一种高频淬火机床用自动转盘中,所述转盘的一侧设置有上下料机械手,机械手将待淬火的轴类零件转移至上料工位,已完成淬火的轴类零件转移至下道工序。
15.本实用新型和现有技术相比,具有如下有益效果:
16.本实用新型提供了一种对轴类零件进行自动淬火的装置,通过自动转盘将轴类零件依次送至淬火工位的对应位置,通过驱动装置将轴类零件移动至淬火工位的感应线圈内进行淬火。上述装置实现了轴类零件淬火的自动化,提高了工作效率,节省了人力成本。
附图说明
17.图1是本实用新型的结构示意图;
18.图2是本实用新型的轴向剖视图;
19.附图标记:1、转盘;2、轴类零件;3、感应线圈;4、驱动装置;5、下顶尖;6、上顶尖;7、位置传感器。
具体实施方式
20.下面结合附图以具体实施例对本实用新型作进一步描述,参见图1-2:
21.一种高频淬火机床用自动转盘1,包括转动设置在机床上的转盘1,所述转盘1上周向设置有若干上料工位,所述上料工位内放置有待淬火的轴类零件2,所述轴类零件2的轴线与转盘1的轴线平行设置,所述转盘1的上方设置有淬火工位,所述淬火工位包括对轴类零件2进行淬火的感应线圈3,转盘1转动时上料工位依次经过淬火工位所对应的位置,所述转盘1的下方设置有驱动轴类零件2轴向移动至感应线圈3内的驱动装置4,所述驱动装置4位于淬火工位所对应的位置。
22.优选的,所述上料工位等间距设置,使得上料工位上所放置的轴类零件2也具有相同的间距。
23.优选的,所述感应线圈3采用双圈结构。
24.上述转盘1固连有转盘1转轴,所述转盘1转轴与动力装置如电机传动连接,电机驱动转盘1转轴转动,转盘1随之转动。
25.上述上料工位设置有轴向贯穿转盘1的通孔,所述轴类零件2穿设在通孔中。
26.进一步的,所述轴类零件2上设置有台阶结构,所述通孔与台阶结构配合限位。上述结构使轴类零件2非常容易放置到上料工位中,且不需要任何夹紧装置,台阶结构可以使轴类零件2保持在转盘1上。
27.上述驱动装置4的执行单元上连接有与轴类零件2下端匹配的下顶尖5,驱动装置4驱动下顶尖5向上运动顶起轴类零件2,所述感应线圈3上方设置有与轴类零件2上端匹配的上顶尖6,上顶尖6与下顶尖5配合固定淬火的轴类零件2,所述上顶尖6由动力装置驱动旋转,并带动轴类零件2同时旋转。所述上顶尖6与下顶尖5的轴线均与轴类零件2的轴线平行。
28.上述驱动装置4包括驱动气缸,所述驱动气缸竖直设置,所述下顶尖5连接在其活塞杆上。驱动气缸的活塞杆向上移动时带动下顶尖5同时向上移动,所述驱动装置4还可以使用电机等其他装置。
29.上述转盘1上设置有与每个上料工位对应的位置感应器,通过位置感应器可以使
上料工位精准的移动到淬火工位所对应的位置。所述位置感应器采用本领域的通用感应器,例如角度感应器、接近感应器、对射感应器等。当使用角度感应器时,通过角度感应器感应上料工位的转动角度,当转动角度为淬火工位所在角度时,上料工位到达设定位置;当使用接近感应器时,可以将金属部分设置在转盘1上,将检测部分设置在固定位置,当转盘1转动到一定位置时,接近感应器检测到信号,上料工位到达设定位置。
30.进一步的,所述转盘1的外周面设置有若干安装凹槽,所述位置感应器设置在安装凹槽内。
31.为了进一步提高自动化程度,所述转盘1的一侧设置有上下料机械手,机械手将待淬火的轴类零件2转移至上料工位,已完成淬火的轴类零件2转移至下道工序。
32.本实施例的工作过程是:机械手将待淬火的轴类零件2转移至上料工位,转盘1转动依次输送轴类零件2,当位置传感器7发出信号时,转盘1停止,驱动装置4驱动下顶针带动轴类零件2向上移动,同时配合上顶针夹紧轴类零件2,之后进行淬火作业,淬火完成后,下顶针向下复位,轴类零件2同时复位到上料工位中,转盘1重新开始转动,直到下个上料工位到达设定位置,如此循环作业,机械手将淬火好的轴类零件2取下。
33.上述实施例仅为本实用新型的较佳实施例,并非依此限制本实用新型的保护范围,故:凡依本实用新型的结构、形状、原理所做的等效变化,均应涵盖于本实用新型的保护范围之内。
技术特征:1.一种高频淬火机床用自动转盘,其特征在于,包括转动设置在机床上的转盘(1),所述转盘(1)上周向设置有若干上料工位,所述上料工位内放置有待淬火的轴类零件(2),所述轴类零件(2)的轴线与转盘(1)的轴线平行设置,所述转盘(1)的上方设置有淬火工位,所述淬火工位包括对轴类零件(2)进行淬火的感应线圈(3),转盘(1)转动时上料工位依次经过淬火工位所对应的位置,所述转盘(1)的下方设置有驱动轴类零件(2)轴向移动至感应线圈(3)内的驱动装置(4),所述驱动装置(4)位于淬火工位所对应的位置。2.根据权利要求1所述的一种高频淬火机床用自动转盘,其特征在于,所述上料工位设置有轴向贯穿转盘(1)的通孔,所述轴类零件(2)穿设在通孔中。3.根据权利要求2所述的一种高频淬火机床用自动转盘,其特征在于,所述轴类零件(2)上设置有台阶结构,所述通孔与台阶结构配合限位。4.根据权利要求1所述的一种高频淬火机床用自动转盘,其特征在于,所述驱动装置(4)的执行单元上连接有与轴类零件(2)下端匹配的下顶尖(5),驱动装置(4)驱动下顶尖(5)向上运动顶起轴类零件(2),所述感应线圈(3)上方设置有与轴类零件(2)上端匹配的上顶尖(6),所述上顶尖(6)由动力装置驱动旋转。5.根据权利要求4所述的一种高频淬火机床用自动转盘,其特征在于,所述驱动装置(4)包括驱动气缸,所述驱动气缸竖直设置,所述下顶尖(5)连接在其活塞杆上。6.根据权利要求1所述的一种高频淬火机床用自动转盘,其特征在于,所述转盘(1)上设置有与每个上料工位对应的位置传感器(7)。7.根据权利要求6所述的一种高频淬火机床用自动转盘,其特征在于,所述转盘(1)的外周面设置有若干安装凹槽,所述位置传感器(7)设置在安装凹槽内。8.根据权利要求1所述的一种高频淬火机床用自动转盘,其特征在于,所述转盘(1)的一侧设置有上下料机械手。
技术总结本实用新型属于零件淬火的技术领域,涉及一种高频淬火机床用自动转盘,包括转动设置在机床上的转盘,所述转盘上周向设置有若干上料工位,所述上料工位内放置有待淬火的轴类零件,所述轴类零件的轴线与转盘的轴线平行设置,所述转盘的上方设置有淬火工位,所述淬火工位包括对轴类零件进行淬火的感应线圈,转盘转动时上料工位依次经过淬火工位所对应的位置,所述转盘的下方设置有驱动轴类零件轴向移动至感应线圈内的驱动装置,所述驱动装置位于淬火工位所对应的位置。本实用新型提供的高频淬火机床用自动转盘,实现了轴类零件淬火的自动化,提高了工作效率,节省了人力成本。节省了人力成本。节省了人力成本。
技术研发人员:罗永敏
受保护的技术使用者:台州市索立机械有限公司
技术研发日:2021.12.28
技术公布日:2022/8/16