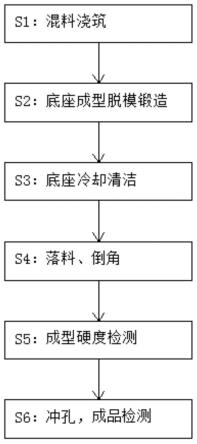
50min,然后对底座的表面进行清洁。
19.优选的,所述s4中,对底座进行落料固定,使用机器对底座的四边进行倒角,加工c角,倒角时间为5-10min。
20.优选的,所述s5中,利用硬度检测器对成型的底座进行硬度检测,保证莫氏硬度值在4-5。
21.优选的,所述s6中,将底座固定然后冲孔,完成成品后对孔径进行检测,保证孔径偏差在0.01-0.05cm之间。
22.与现有技术相比,本发明的优点在于:
23.本发明将底座采用钼粉、碳粉、铁粉、铜粉、铬粉、钛粉和铝粉混合,可以提高底座的硬度;在底座中加入石英和石墨烯,可以提高底座的耐高温性能;
24.本发明将落料、成型、冲孔、车加工c角中的车加工c角去掉,更换在落料时进行倒角,缩减工序,减少人工与设备使用,提高生产效率,提高了产品的合格率。
附图说明
25.图1为本发明提出的一种可提高生产效率的底座加工工艺的流程图。
具体实施方式
26.下面将结合本发明实施例中的附图,对本发明实施例中的技术方案进行清楚、完整地描述,显然,所描述的实施例仅仅是本发明一部分实施例,而不是全部的实施例。
27.实施例一
28.参照图1,一种可提高生产效率的底座加工工艺,包括以下工艺步骤:
29.s1:混料浇筑;混合底座原料,并进行熔炼浇筑,底座原料包括以下成分的重量百分比:钼粉22%、碳粉10%、铁粉15%、铜粉3%、铬粉2%、钛粉2%、石英1%、石墨烯0.5%以及其余的铝粉;
30.s2:底座成型脱模锻造;对成型后的底座进行脱模锻造;
31.s3:底座冷却清洁;
32.s4:落料、倒角;对底座进行落料固定,使用机器进行倒角;
33.s5:成型硬度检测;
34.s6:冲孔,成品检测。
35.本实施例中,s1中,将底座原料进行混合,将钼粉、碳粉、铁粉、铜粉、铬粉、钛粉、石英、石墨烯以及其余的铝粉依次加入混合器中,采用温度65℃,转速3000r/min,混合30min,得到混合料。
36.本实施例中,s1中,将混合后的底座原料进行熔炼,采用熔炼炉并设置1200℃进行熔炼,熔炼后的底座原料成为金属液导入模型内冷却成型。
37.本实施例中,s2中,底座成型后进行脱模锤炼,锤炼时间为1h,锤炼温度为500℃。
38.本实施例中,s3中,锤炼完成后,采用风冷的方式对底座进行冷却,冷却时间为40min,然后对底座的表面进行清洁。
39.本实施例中,s4中,对底座进行落料固定,使用机器对底座的四边进行倒角,加工c角,倒角时间为5min。
40.本实施例中,s5中,利用硬度检测器对成型的底座进行硬度检测,保证莫氏硬度值在4。
41.本实施例中,s6中,将底座固定然后冲孔,完成成品后对孔径进行检测,保证孔径偏差在0.01cm。
42.实施例二
43.参照图1,一种可提高生产效率的底座加工工艺,包括以下工艺步骤:
44.s1:混料浇筑;混合底座原料,并进行熔炼浇筑,底座原料包括以下成分的重量百分比:钼粉28%、碳粉13%、铁粉18%、铜粉4.5%、铬粉3.5%、钛粉4%、石英2%、石墨烯1.3%以及其余的铝粉;
45.s2:底座成型脱模锻造;对成型后的底座进行脱模锻造;
46.s3:底座冷却清洁;
47.s4:落料、倒角;对底座进行落料固定,使用机器进行倒角;
48.s5:成型硬度检测;
49.s6:冲孔,成品检测。
50.本实施例中,s1中,将底座原料进行混合,将钼粉、碳粉、铁粉、铜粉、铬粉、钛粉、石英、石墨烯以及其余的铝粉依次加入混合器中,采用温度70℃,转速320r/min,混合35min,得到混合料。
51.本实施例中,s1中,将混合后的底座原料进行熔炼,采用熔炼炉并设置1350℃进行熔炼,熔炼后的底座原料成为金属液导入模型内冷却成型。
52.本实施例中,s2中,底座成型后进行脱模锤炼,锤炼时间为1.5h,锤炼温度为550℃。
53.本实施例中,s3中,锤炼完成后,采用风冷的方式对底座进行冷却,冷却时间为45min,然后对底座的表面进行清洁。
54.本实施例中,s4中,对底座进行落料固定,使用机器对底座的四边进行倒角,加工c角,倒角时间为8min。
55.本实施例中,s5中,利用硬度检测器对成型的底座进行硬度检测,保证莫氏硬度值在4.5。
56.本实施例中,s6中,将底座固定然后冲孔,完成成品后对孔径进行检测,保证孔径偏差在0.03cm。
57.实施例三
58.参照图1,一种可提高生产效率的底座加工工艺,包括以下工艺步骤:
59.s1:混料浇筑;混合底座原料,并进行熔炼浇筑,底座原料包括以下成分的重量百分比:钼粉35%、碳粉15%、铁粉20%、铜粉6%、铬粉6%、钛粉6%、石英3%、石墨烯2%以及其余的铝粉;
60.s2:底座成型脱模锻造;对成型后的底座进行脱模锻造;
61.s3:底座冷却清洁;
62.s4:落料、倒角;对底座进行落料固定,使用机器进行倒角;
63.s5:成型硬度检测;
64.s6:冲孔,成品检测。
65.本实施例中,s1中,将底座原料进行混合,将钼粉、碳粉、铁粉、铜粉、铬粉、钛粉、石英、石墨烯以及其余的铝粉依次加入混合器中,采用温度75℃,转速350r/min,混合40min,得到混合料。
66.本实施例中,s1中,将混合后的底座原料进行熔炼,采用熔炼炉并设置1500℃进行熔炼,熔炼后的底座原料成为金属液导入模型内冷却成型。
67.本实施例中,s2中,底座成型后进行脱模锤炼,锤炼时间为2h,锤炼温度为600℃。
68.本实施例中,s3中,锤炼完成后,采用风冷的方式对底座进行冷却,冷却时间为50min,然后对底座的表面进行清洁。
69.本实施例中,s4中,对底座进行落料固定,使用机器对底座的四边进行倒角,加工c角,倒角时间为10min。
70.本实施例中,s5中,利用硬度检测器对成型的底座进行硬度检测,保证莫氏硬度值在5。
71.本实施例中,s6中,将底座固定然后冲孔,完成成品后对孔径进行检测,保证孔径偏差在0.05cm。
72.综上,实施例二为最佳实施例。
73.以上所述,仅为本发明较佳的具体实施方式,但本发明的保护范围并不局限于此,任何熟悉本技术领域的技术人员在本发明揭露的技术范围内,根据本发明的技术方案及其发明构思加以等同替换或改变,都应涵盖在本发明的保护范围之内。
技术特征:1.一种可提高生产效率的底座加工工艺,其特征在于,包括以下工艺步骤:s1:混料浇筑;混合底座原料,并进行熔炼浇筑,底座原料包括以下成分的重量百分比:钼粉22-35%、碳粉10-15%、铁粉15-20%、铜粉3-6%、铬粉2-6%、钛粉2-6%、石英1-3%、石墨烯0.5-2%以及其余的铝粉;s2:底座成型脱模锻造;对成型后的底座进行脱模锻造;s3:底座冷却清洁;s4:落料、倒角;对底座进行落料固定,使用机器进行倒角;s5:成型硬度检测;s6:冲孔,成品检测。2.根据权利要求1所述的一种可提高生产效率的底座加工工艺,其特征在于,所述s1中,底座原料包括以下成分的重量百分比:钼粉25-30%、碳粉12-14%、铁粉17-19%、铜粉4-5%、铬粉3-5%、钛粉3-5%、石英1.5-2.5%、石墨烯1-1.5%以及其余的铝粉。3.根据权利要求1所述的一种可提高生产效率的底座加工工艺,其特征在于,所述s1中,底座原料包括以下成分的重量百分比:钼粉28%、碳粉13%、铁粉18%、铜粉4.5%、铬粉3.5%、钛粉4%、石英2%、石墨烯1.3%以及其余的铝粉。4.根据权利要求1所述的一种可提高生产效率的底座加工工艺,其特征在于,所述s1中,将底座原料进行混合,将钼粉、碳粉、铁粉、铜粉、铬粉、钛粉、石英、石墨烯以及其余的铝粉依次加入混合器中,采用温度65-75℃,转速300-350r/min,混合30-40min,得到混合料。5.根据权利要求1所述的一种可提高生产效率的底座加工工艺,其特征在于,所述s1中,将混合后的底座原料进行熔炼,采用熔炼炉并设置1200-1500℃进行熔炼,熔炼后的底座原料成为金属液导入模型内冷却成型。6.根据权利要求1所述的一种可提高生产效率的底座加工工艺,其特征在于,所述s2中,底座成型后进行脱模锤炼,锤炼时间为1-2h,锤炼温度为500-600℃。7.根据权利要求1所述的一种可提高生产效率的底座加工工艺,其特征在于,所述s3中,锤炼完成后,采用风冷的方式对底座进行冷却,冷却时间为40-50min,然后对底座的表面进行清洁。8.根据权利要求1所述的一种可提高生产效率的底座加工工艺,其特征在于,所述s4中,对底座进行落料固定,使用机器对底座的四边进行倒角,加工c角,倒角时间为5-10min。9.根据权利要求1所述的一种可提高生产效率的底座加工工艺,其特征在于,所述s5中,利用硬度检测器对成型的底座进行硬度检测,保证莫氏硬度值在4-5。10.根据权利要求1所述的一种可提高生产效率的底座加工工艺,其特征在于,所述s6中,将底座固定然后冲孔,完成成品后对孔径进行检测,保证孔径偏差在0.01-0.05cm之间。
技术总结本发明属于底座加工技术领域,尤其是一种可提高生产效率的底座加工工艺,针对现有的底座硬度质量差,加工工艺复杂,占用设备人工多,效率低,劳动强度大的问题,现提出如下方案,其包括以下工艺步骤:S1:混料浇筑;混合底座原料,并进行熔炼浇筑;S2:底座成型脱模锻造;对成型后的底座进行脱模锻造;S3:底座冷却清洁;S4:落料、倒角;对底座进行落料固定,使用机器进行倒角;S5:成型硬度检测;S6:冲孔,成品检测。本发明可以提高底座的硬度;在底座中加入石英和石墨烯,可以提高底座的耐高温性能;缩减工序,减少人工与设备使用,提高生产效率,提高了产品的合格率。高了产品的合格率。高了产品的合格率。
技术研发人员:张勤明
受保护的技术使用者:无锡市正隆祥机械制造有限公司
技术研发日:2022.03.11
技术公布日:2022/6/4