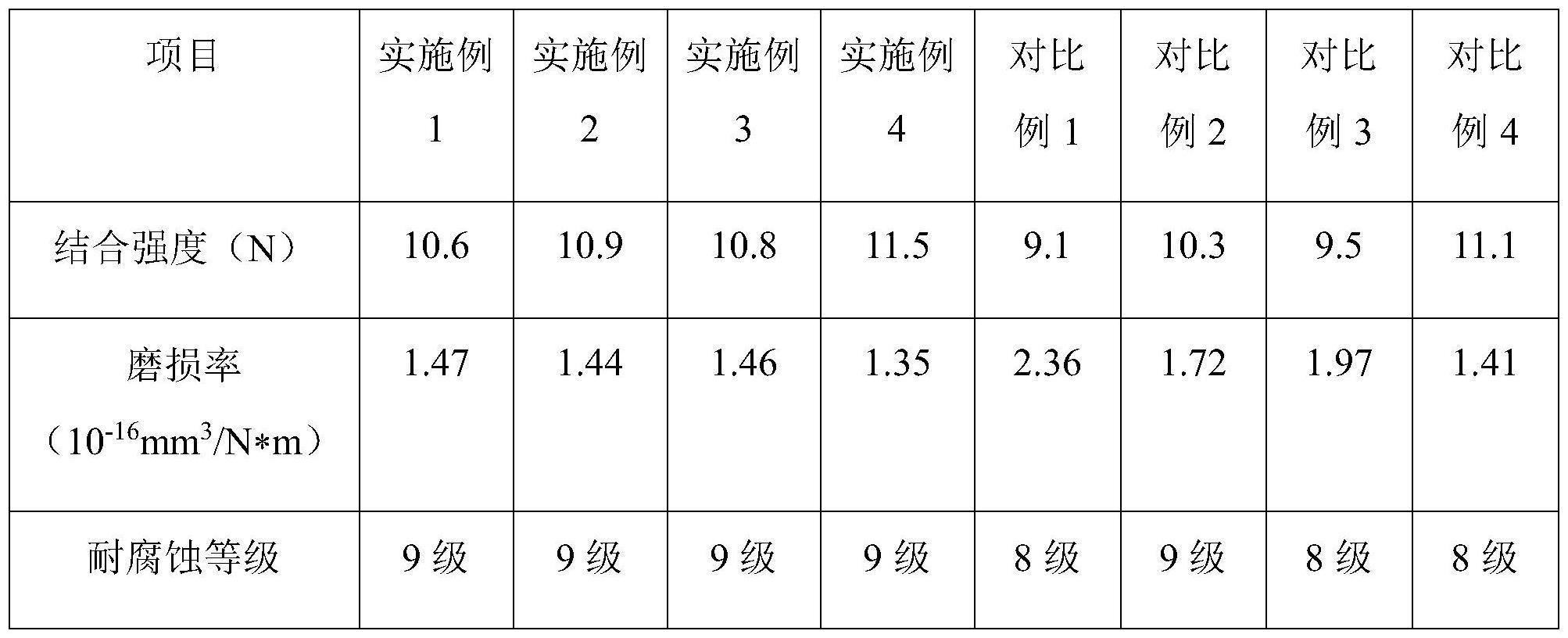
本发明涉及铝合金板材,具体为一种耐蚀铝合金板材及其加工工艺。
背景技术:
1、铝合金一般会在纯铝中加入一种或多种合金元素(如cu、zn、mg)和一些微量元素,使其成分和组织结构发生改变,从而使其具有优异的力学强度和耐腐蚀性能,加工成型性能优异,因此,相比于现有公开的其他合金材料,铝合金已经逐渐成为工业化产品的首选加工材料,在航空航天、海运、汽车、建筑等领域应用广泛。
2、由于铝合金自身机械强度较低,耐磨性差,因此现有研发人员会对其进行表面修饰,利用阳极氧化、热喷涂、激光熔覆、电镀等工艺提高铝合金产品的表面耐磨性能和耐腐蚀性能,而类金刚石薄膜(dlc膜)的沉积也是现有较为常用的修饰方法,但现有工艺所得到的产品依旧无法满足我们的实际需求。
3、因此,本申请公开了一种耐蚀铝合金板材及其加工工艺,以解决该技术问题。
技术实现思路
1、本发明的目的在于提供一种耐蚀铝合金板材及其加工工艺,以解决上述背景技术中提出的问题。
2、为了解决上述技术问题,本发明提供如下技术方案:
3、一种耐蚀铝合金板材的加工工艺,包括以下步骤:
4、(1)取铝合金基板,表面砂纸打磨,依次采用无水乙醇、去离子水超声清洗10~20min,吹干后表面通过氩气离子清洗5~10min,再以二氧化铈靶、铝靶、钛靶、铬靶共溅射,沉积底膜;
5、(2)在底膜表面进行离子渗氮处理;
6、(3)取步骤(2)处理后的铝合金基板,表面沉积dlc膜,去离子水超声清洗,真空干燥,得到成品。
7、较优化的方案,步骤(1)中,共溅射具体步骤为:
8、s1:腔体内通入氩气,维持腔体压强为0.5~1.0pa,先开启铬靶和铝靶,铬靶功率为1500~2000w,铝钯功率为300~500w,溅射10~20min;
9、s2:关闭铬靶,开启二氧化铈钯,二氧化铈钯功率为100~200w,铝钯功率调整为150~200w,继续溅射5~10min;
10、s3:重复s1~s2步骤2~3次,关闭二氧化铈钯;
11、s4:开启钛靶、铬靶,铬靶功率为1500~2000w,钛靶功率为1000~1200w,铝钯功率调整至为300~500w,以钛靶、铝钯、铬靶共溅射40~50min,关闭靶材,形成底膜。
12、较优化的方案,步骤(3)中,dlc膜沉积工艺参数为:乙炔流量为50~60ml/min,氩气流量为20~30ml/min,控制腔体内压强为2.0pa,基体温度为100~120℃,离子源功率4~5kw,沉积时间为2~3h。
13、较优化的方案,步骤(2)中,离子渗氮温度为460~480℃,渗氮时间为4~6h,渗氮压力为0.6~0.8pa。
14、较优化的方案,步骤(2)中,离子渗氮时在铝合金基板周围摆放海绵钛、硼铁混合料,实现钛硼氮复合渗。
15、较优化的方案,铝合金基板周围1mm2单位面积内放置8~10mg混合料,且混合料中海绵钛、硼铁的质量比为3:1。
16、较优化的方案,步骤(1)中,铝合金基板各组分含量为:以质量分数计,zn:5.85~6.42%、mg:2.2~2.3%、cu:2.13~2.18%、fe:0.05~0.055%、si:0.02~0.041%、mn:0.01~0.019%、zr:0.094~0.12%、cr:0.003~0.01%,余量为al和不可避免的杂质。
17、较优化的方案,根据以上任意一项所述的一种耐蚀铝合金板材的加工工艺加工得到的铝合金板材。
18、与现有技术相比,本发明所达到的有益效果是:
19、本发明公开了一种耐蚀铝合金板材及其加工工艺,方案以铝合金基板作为基材,并在其表面进行溅射沉积膜层,以提高铝合金板材的耐腐蚀、耐磨性能,其中铝合金基板各组分含量为:以质量分数计,zn:5.85~6.42%、mg:2.2~2.3%、cu:2.13~2.18%、fe:0.05~0.055%、si:0.02~0.041%、mn:0.01~0.019%、zr:0.094~0.12%、cr:0.003~0.01%,余量为al和不可避免的杂质,以该配方加工形成的铝合金基板,其具有较优异的力学性能,可适用于方案实施。
20、在此基础上,方案先在铝合金基板表面砂纸打磨,无水乙醇、去离子水清洗后,利用氩气离子清洗,再以二氧化铈靶、铝靶、钛靶、铬靶作为靶材共溅射,以沉积形成底膜;溅射沉积时,本申请将方案设计为“铬靶、铝钯配合预先溅射沉积形成底层、铝钯、二氧化铈钯配合溅射过渡膜,再利用钛靶、铝钯、铬靶共溅射”,从而形成复合底膜,其所实现的技术效果为:由于铝合金板材最外层为硬质dlc膜层,而铝合金基材的硬度相比较低,因此底膜作为二者的过渡层,能够为外层dlc膜提供支撑,不仅能够提高铝合金基材与dlc膜层的结合强度,同时还能够提高铝合金板材的承载能力和表面耐磨性能。
21、此处需强调:本申请创造性限定了各个靶材的溅射顺序,并以此构建了复合底膜,相比于单一的钛膜或铬膜,其对于dlc膜、铝铝合金基板之间的结合强度的提升更为显著,同时铝合金板材的表面耐磨性也得到提升。
22、同时,本方案在溅射底膜后,进行离子渗氮处理步骤,其步骤目的为:促进铝基金属间化合物的生成,一方面提高底膜的表面硬度,从而提高其承载能力,提高其与外层dlc膜层的结合强度,另一方面,离子渗氮后,底膜整体的致密度得以增加,且晶粒细化,尺寸更为均匀,其作为物理阻挡层,能够有效阻碍腐蚀介质的进入,从而提高铝合金板材的耐腐蚀性能。此处方案还提供了另外的实施例,如引入硼、钛,以实现硼钛氮共渗,本方案在铝合金表面离子渗氮,因此其温度应低于铝合金的过烧温度,以避免晶粒过度粗化,限定为“460~480℃”,温度较低的情况下,硼钛的引入能够促进扩渗效率,并且优化扩渗效果,从而提高底膜与铝合金基材的结合性能。
23、在此基础上,方案在铝合金基板最外侧沉积dlc膜,并限定工艺参数为:乙炔流量为50~60ml/min,氩气流量为20~30ml/min,控制腔体内压强为2.0pa,基体温度为100~120℃,离子源功率4~5kw,沉积时间为2~3h,dlc膜具有高硬耐磨、减磨润滑与耐蚀等特性,能够有效保证铝合金板材的综合性能;且由于复合底膜、离子渗氮步骤的存在,dlc薄膜与铝合金基板的结合强度高,耐磨性能进一步提升。
24、本申请公开了一种耐蚀铝合金板材及其加工工艺,整体工艺设计合理,通过限定靶材的溅射顺序沉积并形成复合底膜,离子渗氮后进行dlc膜沉积,制备得到的铝合金板材具有优异的耐腐蚀性能,表面硬度高,耐磨性能优异,具有较高的实用性。
技术特征:1.一种耐蚀铝合金板材的加工工艺,其特征在于:包括以下步骤:
2.根据权利要求1所述的一种耐蚀铝合金板材的加工工艺,其特征在于:步骤(1)中,共溅射具体步骤为:
3.根据权利要求1所述的一种耐蚀铝合金板材的加工工艺,其特征在于:步骤(3)中,dlc膜沉积工艺参数为:乙炔流量为50~60ml/min,氩气流量为20~30ml/min,控制腔体内压强为2.0pa,基体温度为100~120℃,离子源功率4~5kw,沉积时间为2~3h。
4.根据权利要求1所述的一种耐蚀铝合金板材的加工工艺,其特征在于:步骤(2)中,离子渗氮温度为460~480℃,渗氮时间为4~6h,渗氮压力为0.6~0.8pa。
5.根据权利要求4所述的一种耐蚀铝合金板材的加工工艺,其特征在于:步骤(2)中,离子渗氮时在铝合金基板周围摆放海绵钛、硼铁混合料,实现钛硼氮复合渗。
6.根据权利要求5所述的一种耐蚀铝合金板材的加工工艺,其特征在于:铝合金基板周围1mm2单位面积内放置8~10mg混合料,且混合料中海绵钛、硼铁的质量比为3:1。
7.根据权利要求5所述的一种耐蚀铝合金板材的加工工艺,其特征在于:步骤(1)中,铝合金基板各组分含量为:以质量分数计,zn:5.85~6.42%、mg:2.2~2.3%、cu:2.13~2.18%、fe:0.05~0.055%、si:0.02~0.041%、mn:0.01~0.019%、zr:0.094~0.12%、cr:0.003~0.01%,余量为al和不可避免的杂质。
8.根据权利要求1~7中任意一项所述的一种耐蚀铝合金板材的加工工艺加工得到的铝合金板材。
技术总结本发明涉及铝合金板材技术领域,具体为一种耐蚀铝合金板材及其加工工艺。方案以铝合金基板作为基材,并在其表面进行溅射沉积膜层,以提高铝合金板材的耐腐蚀、耐磨性能,其中铝合金基板各组分含量为:以质量分数计,Zn:5.85~6.42%、Mg:2.2~2.3%、Cu:2.13~2.18%、Fe:0.05~0.055%、Si:0.02~0.041%、Mn:0.01~0.019%、Zr:0.094~0.12%、Cr:0.003~0.01%,余量为Al和不可避免的杂质,以该配方加工形成的铝合金基板,其具有较优异的力学性能,可适用于方案实施。本申请通过限定靶材的溅射顺序沉积并形成复合底膜,离子渗氮后进行DLC膜沉积,制备得到的铝合金板材具有优异的耐腐蚀性能,表面硬度高,耐磨性能优异,具有较高的实用性。
技术研发人员:余加明,符金柱,黄添星
受保护的技术使用者:江苏世豪合金科技有限公司
技术研发日:技术公布日:2024/1/11