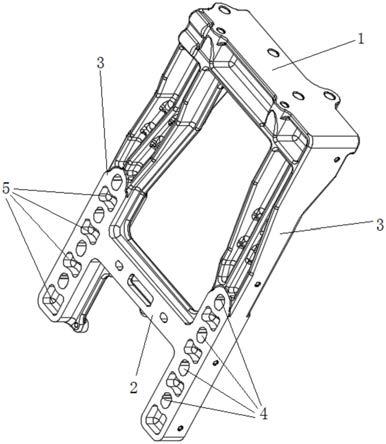
1.本实用新型涉及一种商用车排放支架,特别是涉及一种用于支撑尾气处理机构的商用车排放支架。
背景技术:2.商用车是一种用于运送人员或者货物的汽车,商用车排放支架用于固定尾气处理机构与车体的连接。由于商用车排放支架用于支撑的尾气处理机构重量较大,使得商用车排放支架的重量较重、体积较大。
3.商用车排放支架在使用过程中除了高载荷承重,还需要兼顾因路况环境复杂带来的高频率震动,使用环境的复杂多变使其对铸件内在质量有较高的技术要求。现有商用车排放支架为厚大件,其整体采用铸造工艺加工,厚大件在铸造过程中存在组织不致密,易出现缩松,导致商用车在使用过程中出现从缩松位置开始断裂的风险,断裂一旦产生将会引起交通事故。
技术实现要素:4.为了解决现有商用车排放支架存在重量较大、组织不致密,铸造中易出现缩松,导致商用车在使用过程中出现从缩松位置断裂的技术问题,本实用新型提供了一种用于支撑尾气处理机构的商用车排放支架。
5.为实现上述目的,本实用新型提供的技术方案是:
6.一种用于支撑尾气处理机构的商用车排放支架,包括平行设置的主梁和辅梁,以及平行设置的两个侧梁,所述主梁的两端分别与两个侧梁的一端连接;所述辅梁的两端分别与两个侧梁内侧连接,其特殊之处在于:还包括设置在两个侧梁上远离主梁一端的多个应力释放孔和多个减重孔;
7.每个侧梁上的多个应力释放孔和多个减重孔沿侧梁的长度方向间隔排列;
8.所述应力释放孔的形状为椭圆形,且应力释放孔的长轴方向与侧梁的长度方向一致;
9.所述减重孔的形状为矩形,且与应力释放孔相对应的侧边向内收缩为弧形。
10.进一步地,每个侧梁上,所述应力释放孔和减重孔的数量均为4个,且侧梁远离主梁的一端最外侧为减重孔。
11.进一步地,4个应力释放孔沿侧梁的长度方向均匀设置;
12.4个减重孔沿侧梁的长度方向均匀设置。
13.进一步地,所述应力释放孔的尺寸为12.5
×
17.5mm。
14.进一步地,相邻应力释放孔短轴间的距离为50mm。
15.进一步地,所述辅梁与两个侧梁连接处设有倒弧角。
16.与现有技术相比,本实用新型的优点是:
17.1、本实用新型商用车排放支架通过在侧梁上远离主梁一端设置应力释放孔和减
重孔,应力释放孔用于分散热节,同时作为连接孔,通过紧固螺栓穿过该应力释放孔后与尾气处理机构螺纹连接,实现尾气处理机构和商用车排放支架的固定;本实用新型应力释放孔的形状为椭圆形,用于释放应力,可避免铸造过程缩松缺陷,保证商用车排放支架的使用安全性;减重孔为矩形孔,且与应力释放孔相对应的侧边为向内收缩的弧形,保证应力释放孔的外周为等壁厚,以满足强度要求。
18.2、本实用新型商用车排放支架上的应力释放孔和减重孔均可降低产品的重量,进而降低产品的成本。
19.3、本实用新型商用车排放支架在两个侧梁总共打8个应力释放孔,铸件内部质量有极大提升,避免缩松缺陷。
20.4、本实用新型在辅梁与两个侧梁连接处设有倒弧角,防止连接处断裂。
附图说明
21.图1为本实用新型用于支撑尾气处理机构的商用车排放支架结构示意图。
22.其中,附图标记如下:
[0023]1‑
主梁,2
‑
辅梁,3
‑
侧梁,4
‑
应力释放孔,5
‑
减重孔。
具体实施方式
[0024]
下面结合附图和实施例对本实用新型作进一步的详细说明。
[0025]
如图1所示,一种用于支撑尾气处理机构的商用车排放支架,包括平行设置的主梁1和辅梁2,以及平行设置的两个侧梁3,主梁1的两端分别与两个侧梁3的一端连接,且侧梁3的一端端面设置在主梁1的一端端部,侧梁3的侧面与主梁3的端面处于同一平面,主梁1与两个侧梁3形成龙门结构;辅梁2的两端分别与两个侧梁3内侧连接,在两个侧梁3上远离主梁1一端设置多个应力释放孔4和多个减重孔5;在每个侧梁3上,多个应力释放孔4和多个减重孔5沿侧梁3的长度方向间隔排列。由于现有商用车排放支架较为厚大,处于孤立的液相区域,冒口补缩的有效半径对其无法覆盖,因此本实用新型通过打孔(多个应力释放孔4)分散热节,同时优化产品结构(多个减重孔5),降低产品重量和成本。
[0026]
本实施例通过多轮的试制,对应力释放孔4的形状进行确定。由最初的半径r12.5圆形孔,根据厚大位置的尺寸比例,不断试制最终确定应力释放孔4的形状为近似椭圆形,尺寸为12.5
×
17.5mm,深度为39.3mm(贯穿孔)。应力释放孔4的长轴方向与侧梁3的长度方向一致,应力释放孔4的短轴直径与紧固螺栓匹配,通过紧固螺栓穿过该应力释放孔4后与尾气处理机构螺纹连接,实现尾气处理机构和商用车排放支架的固定。
[0027]
减重孔5的形状为矩形,且与应力释放孔4相对应的侧边向内收缩为弧形,该弧形与应力释放孔4相适配,保证应力释放孔的外周为等壁厚,以满足强度要求。
[0028]
本实例应力释放孔4和减重孔5的数量均为4个,侧梁3上从远离主梁1的一端向靠近主梁1的一端依次布置减重孔5、应力释放孔4、减重孔5、应力释放孔4、减重孔5、应力释放孔4、减重孔5和应力释放孔4;4个应力释放孔4沿侧梁3的长度方向均匀设置,相邻应力释放孔4短轴间的距离为50mm;4个减重孔5也沿侧梁3的长度方向均匀设置,且最外侧的减重孔5尺寸较大。
[0029]
本实施例在辅梁2与两个侧梁3连接处设有倒弧角,防止连接处断裂。
[0030]
本实施例商用车排放支架在两个侧梁3总共打8个应力释放孔4后,铸件内部质量有极大提升,将原有缺陷率10%(由于缩松引起的缺陷率)几乎降为零缺陷;打应力释放孔4后,每个应力释放孔的部位减少铸件重量0.21kg,8个位置共计减少1.68kg,商用车排放支架铸件总重量为14.2kg,减重比例为12%,直接降低的成本接近10%。因此本实施例商用车排放支架可避免铸造过程缩松缺陷,保证商用车排放支架的使用安全性,同时具有降低成本的特点。
[0031]
以上仅是对本实用新型的优选实施方式进行了描述,并不将本实用新型的技术方案限制于此,本领域技术人员在本实用新型主要技术构思的基础上所作的任何公知变形都属于本实用新型所要保护的技术范畴。
技术特征:1.一种用于支撑尾气处理机构的商用车排放支架,包括平行设置的主梁(1)和辅梁(2),以及平行设置的两个侧梁(3),所述主梁(1)的两端分别与两个侧梁(3)的一端连接;所述辅梁(2)的两端分别与两个侧梁(3)内侧连接,其特征在于:还包括设置在两个侧梁(3)上远离主梁(1)一端的多个应力释放孔(4)和多个减重孔(5);每个侧梁(3)上的多个应力释放孔(4)和多个减重孔(5)沿侧梁(3)的长度方向间隔排列;所述应力释放孔(4)的形状为椭圆形,且应力释放孔(4)的长轴方向与侧梁(3)的长度方向一致;所述减重孔(5)的形状为矩形,且与应力释放孔(4)相对应的侧边向内收缩为弧形。2.根据权利要求1所述用于支撑尾气处理机构的商用车排放支架,其特征在于:每个侧梁(3)上,应力释放孔(4)和减重孔(5)的数量均为4个,且侧梁(3)远离主梁(1)的一端最外侧为减重孔(5)。3.根据权利要求2所述用于支撑尾气处理机构的商用车排放支架,其特征在于:4个应力释放孔(4)沿侧梁(3)的长度方向均匀设置;4个减重孔(5)沿侧梁(3)的长度方向均匀设置。4.根据权利要求1或2或3所述用于支撑尾气处理机构的商用车排放支架,其特征在于:所述应力释放孔(4)的尺寸为12.5
×
17.5mm。5.根据权利要求4所述用于支撑尾气处理机构的商用车排放支架,其特征在于:相邻应力释放孔(4)短轴间的距离为50mm。6.根据权利要求5所述用于支撑尾气处理机构的商用车排放支架,其特征在于:所述辅梁(2)与两个侧梁(3)连接处设有倒弧角。
技术总结本实用新型提供了一种用于支撑尾气处理机构的商用车排放支架,解决现有商用车排放支架存在重量较大、组织不致密,铸造中易出现缩松,导致商用车在使用过程中出现从缩松位置断裂的问题。该支架包括平行设置的主梁和辅梁,以及平行设置的两个侧梁,主梁的两端分别与两个侧梁的一端连接;辅梁的两端分别与两个侧梁内侧连接,在两个侧梁上远离主梁一端的多个应力释放孔和多个减重孔;每个侧梁上的多个应力释放孔和多个减重孔沿侧梁的长度方向间隔排列;应力释放孔的形状为椭圆形,且应力释放孔的长轴方向与侧梁的长度方向一致;减重孔的形状为矩形,且与应力释放孔相对应的侧边向内收缩为弧形。缩为弧形。缩为弧形。
技术研发人员:陈征 汪裕炉 郭飞
受保护的技术使用者:陕西万达汽车配件制造有限公司
技术研发日:2020.11.27
技术公布日:2021/11/2