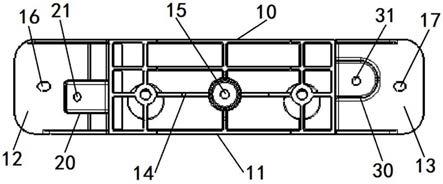
1.本实用新型涉及汽车设计与制造的技术领域,更具体地说,本实用新型涉及一种传动轴安装支架。
背景技术:2.如图1a、1b所示,在现有技术中,传动轴安装组件为由左侧支架1、右侧支架2、传动轴支架3、排气挂钩4和油箱安装支架5等5个钣金件焊接而成的组合支架结构。所述传动轴安装组件涉及的部件数量多,管理成本高;上述钣金件的制备需4套冲压磨具及一套挤压成型模具,制造成本高,且不利于轻量化。组件焊接组装工艺复杂,涉及3种(20个点焊、5处凸焊、4处mig焊)焊接工艺,焊接成本高。上述传动轴安装组件与地板下横梁6采用点焊(31个)形式进行刚性连接形成如图2a、2b所示的地板下横梁总成,焊接层级复杂,焊接、运输、部品管理成本高。
技术实现要素:3.为解决现有技术中存在的上述技术问题,本实用新型的目的在于提供一种传动轴安装支架。
4.本实用新型的传动轴安装支架,为一体铸造成型结构,包括支架本体,所述支架本体由中心部、左端部和右端部构成;所述中心部为中空结构且前表面上设置加强筋,所述中心部的中心设置有y向的主定位安装圆孔,所述左端部上设置有第一y向长圆安装孔,所述右端部上设置有第二y向长圆安装孔;所述中心部的上表面和下表面上设置有z向长圆安装孔;所述中心部上还设置有z向贯通的排气管挂钩安装孔。
5.其中,所述中心部的左侧设置有斜面凸台;并且所述斜面凸台上加工有隔热板安装螺纹孔。
6.其中,所述中心部的右侧设置有柱形凸台;并且所述柱形凸台上设置有油箱安装螺纹孔。
7.其中,所述加强筋具有纵横交错的结构。
8.与现有技术相比,本实用新型的传动轴安装支架具有以下有益效果:
9.本实用新型的传动轴安装支架为铸造单件,与地板下横梁的连接形式由焊接改为螺接,实现了节约成本、提高轻量化水平的效果。
附图说明
10.图1a为现有技术中的传动轴安装组件的主视图。
11.图1b为现有技术中的传动轴安装组件的俯视图。
12.图2a为现有技术中的地板下横梁总成的主视图。
13.图2b为现有技术中的地板下横梁总成的俯视图。
14.图3a为本实用新型的传动轴安装支架的主视图。
15.图3b为本实用新型的传动轴安装支架的侧视图。
16.图3c为本实用新型的传动轴安装支架的俯视图。
17.图4为本实用新型的地板下横梁总成的俯视图。
18.图5为图4沿着a
‑
a方向的截面结构示意图。
19.图6为图4沿着b
‑
b方向的截面结构示意图。
20.图7为图4沿着c
‑
c方向的截面结构示意图。
具体实施方式
21.以下将结合具体实施例对本实用新型的传动轴安装支架做进一步的阐述,以帮助本领域的技术人员对本实用新型的技术方案有更完整、准确和深入的理解。
22.实施例1
23.如图3a、3b、3c所示,本实施例的传动轴安装支架为一体铸造成型结构,其包括支架本体10,所述支架本体10由中心部11、左端部12和右端部13构成。所述中心部11的左侧设置有斜面凸台20,所述斜面凸台20上加工有隔热板安装螺纹孔21,所述中心部11的右侧设置有柱形凸台30,所述柱形凸台30上设置有油箱安装螺纹孔31。所述中心部11为中空结构且前表面上设置有纵横交错的加强筋14,所述中心部11的中心设置有y向的主定位安装圆孔15,所述左端部12上设置有第一y向长圆安装孔16,所述右端部上设置有第二y向长圆安装孔17。所述中心部11的上表面和下表面上设置有z向长圆安装孔19,而且所述中心部11上还设置有z向贯通的排气管挂钩安装孔18。本实施例的传动轴安装支架变更为铸铝支架,减少了部品数量,降低了部品管理成本。
24.图4
‑
7示出了本实施例的传动轴安装支架与地板下横梁50以及排气管挂钩70采用螺栓60连接的连接结构,得到的地板下横梁总成的焊接数量由29处(20个点焊、5处凸焊、4处二保焊)变更为4处cmt焊,大大的降低了焊接成本。采用铝铸件替代现有的钣金结构,重量由3.2kg变为2.3kg,减重约1kg,提升了轻量化水平。本实施例的传动轴安装支架采用铸造结构,在需加强的重要部位设计工艺加强筋,其余部分可中空处理,进一步实现了减重效果;而且本实施例的传动轴安装支架更方便安装点的集成,自身结构设计再辅助以机加工艺(铣削安装面及攻丝螺纹孔)即可满足功能部品的安装需求,不需要单独设计零部件再焊接成组件集成,减少设计成本和制造成本。单件结构只需要一套注塑模具辅助以机加工艺即可满足功能性及装配要求,与现有技术相比大大降低了制造成本。本实施例的传动轴安装支架以螺接的形式与地板下横梁连接,降低了管理及制造成本。在铸铝件本体上自攻螺纹安装孔,不需要另外焊接凸焊螺母,可进一步降低制造成本。本实施例的传动轴安装支架开设有5个安装孔用于与地板下横梁通过螺栓实现刚性连接。五个安装孔分别为y向的主定位安装圆孔(孔径可设计为φ8.2),所述左端部上的第一y向长圆安装孔,右端部上的第二y向长圆安装孔,规格为φ9
×
13,可以吸收来自y方向的组装公差。所述中心部的上表面和下表面上设置有z向长圆安装孔,可以吸收来自z方向的组装公差;以满足组装精度的同时方便安装。本实施例的传动轴安装支架对应传动轴的安装面设有安装台,通过机加工的方式铣削安装配合面,以达到配合平面的平坦度要求,并在安装台上钻孔攻丝,用于传动轴的螺接安装。斜面凸台上加工有m8螺纹孔,用于排气管的隔热罩安装;排气管挂钩以cmt焊的连接形式形成刚性连接;柱形凸台上加工有m8螺纹孔,用于油箱的安装。
25.对于本领域的普通技术人员而言,具体实施例只是对本实用新型进行了示例性描述,显然本实用新型具体实现并不受上述方式的限制,只要采用了本实用新型的方法构思及技术方案进行的各种非实质性的改进,均在本实用新型的保护范围之内。
技术特征:1.一种传动轴安装支架,其特征在于:所述安装支架为一体铸造成型结构,其包括支架本体,所述支架本体由中心部、左端部和右端部构成;所述中心部为中空结构且前表面上设置加强筋,所述中心部的中心设置有y向的主定位安装圆孔,所述左端部上设置有第一y向长圆安装孔,所述右端部上设置有第二y向长圆安装孔;所述中心部的上表面和下表面上设置有z向长圆安装孔;所述中心部上还设置有z向贯通的排气管挂钩安装孔。2.根据权利要求1所述的传动轴安装支架,其特征在于:所述中心部的左侧设置有斜面凸台。3.根据权利要求2所述的传动轴安装支架,其特征在于:所述斜面凸台上加工有隔热板安装螺纹孔。4.根据权利要求1所述的传动轴安装支架,其特征在于:所述中心部的右侧设置有柱形凸台。5.根据权利要求4所述的传动轴安装支架,其特征在于:所述柱形凸台上设置有油箱安装螺纹孔。6.根据权利要求1所述的传动轴安装支架,其特征在于:所述加强筋具有纵横交错的结构。
技术总结本实用新型涉及一种传动轴安装支架,属于汽车设计与制造的技术领域。本实用新型的传动轴安装支架,所述安装支架为一体铸造成型结构,其包括支架本体,所述支架本体由中心部、左端部和右端部构成;所述中心部为中空结构且前表面上设置加强筋,所述中心部的中心设置有Y向的主定位安装圆孔,所述左端部上设置有第一Y向长圆安装孔,所述右端部上设置有第二Y向长圆安装孔;所述中心部的上表面和下表面上设置有Z向长圆安装孔;所述中心部上还设置有Z向贯通的排气管挂钩安装孔。本实用新型的传动轴安装支架为铸造单件,与地板下横梁的连接形式由焊接改为螺接,实现了节约成本、提高轻量化水平的效果。平的效果。平的效果。
技术研发人员:窦健楠 陈树宏 罗少伟
受保护的技术使用者:广州阿尔特汽车科技有限公司
技术研发日:2021.01.05
技术公布日:2021/12/7