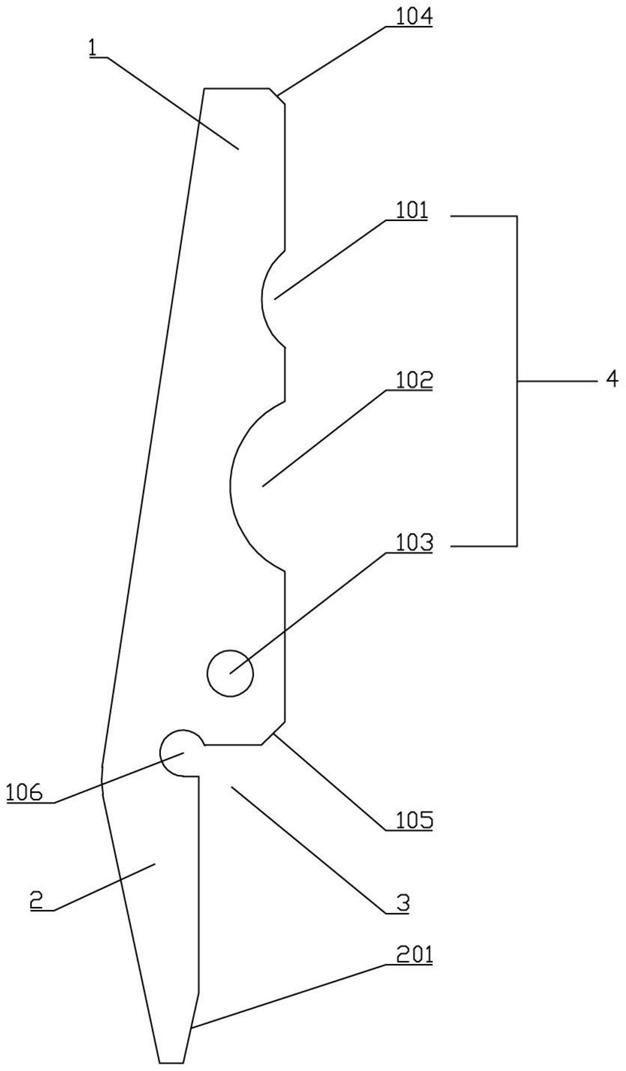
1.本实用新型属于悬架结构加强技术领域,具体涉及自卸半挂车底盘悬架外加强板。
背景技术:2.目前国内普通自卸半挂车底盘超过80%以上采用的是钢板簧平衡悬架。钢板悬架就是我们常见的钢板弹簧,全名是串接式钢板簧平衡悬架。主要由钢板弹簧、悬挂支座、连杆、u型螺栓等部分组成。这种悬挂最大的优点是价格便宜,可靠性好,维修方便。但实际应用中,由于超载等各种原因易出现悬架本体以及与底盘大梁焊接部位开裂现象,严重危及行车安全,具体的,半挂自卸车悬架采用的是与大梁直接焊接的连接方式,实际使用中出现焊缝及悬架本体开裂。其主要原因是车辆转弯时,悬架内外侧受力激增,但外侧没有受力支撑点,仅靠焊缝处承力,同时焊缝易产生应力集中造成疲劳破坏而开裂。
3.如图2所示,悬架b通过焊接连接在大梁a的下方,大梁a外侧上下设有边板。
技术实现要素:4.针对上述背景技术所提出的问题,本实用新型的目的是:旨在提供自卸半挂车底盘悬架外加强板。
5.为实现上述技术目的,本实用新型采用的技术方案如下:
6.自卸半挂车底盘悬架外加强板,包括一体化的梯形上部以及梯形下部,所述梯形上部与梯形下部均为直角梯形,所述梯形上部与梯形下部的底边相靠,斜腰边指向同一侧并在汇合处形成圆滑过渡,所述梯形上部和梯形下部之间形成直角避让空间,所述直角避让空间两直角边由梯形上部的底边、梯形下部的直角腰共同组成;
7.所述梯形上部设有组合减重孔;
8.所述梯形上部直角腰边一侧的顶角设有第一倒角,所述梯形上部直角腰边一侧的底角设有第二倒角;
9.所述梯形上部和梯形下部在直角避让空间处设有开放圆孔。
10.进一步限定,所述组合减重孔包括位于梯形上部直角边一侧的第一缺口,第二缺口以及位于梯形上部底部的减重圆孔,所述第一缺口靠近梯形上部的顶边,所述第二缺口位于第一缺口的下方,所述第二缺口的面积大于第一缺口的面积,这样的结构设计,通过第二缺口的面积大于第一缺口的面积,第一缺口在上,第二缺口在下,来合理的对梯形上部进行减重,通过减重圆孔在减重的同时,设置减重圆孔在梯形上部的底部,避免过度削弱梯形上部直角边的结构强度。
11.进一步限定,所述梯形下部直角腰边一侧的顶角设有第三倒角,这样的结构设计,通过第三倒角使梯形下部直角腰边内收,避免梯形下部与装配面干涉。
12.本实用新型的有益效果:
13.1.通过外加强板来解决行车过程中,车辆转弯时悬架内外侧受力激增,但外侧没
有受力支撑点,仅靠焊缝处承力,同时焊缝产生应力集中造成疲劳破坏而开裂,导致悬架以及与底盘大梁焊接部位开裂的问题;
14.2.外加强板结构简洁,加工方便。
附图说明
15.本实用新型可以通过附图给出的非限定性实施例进一步说明;
16.图1为本实用新型自卸半挂车底盘悬架外加强板实施例的结构示意图;
17.图2为本实用新型自卸半挂车底盘悬架外加强板实施例与大梁、悬架配合时的第一结构示意图;
18.图3为本实用新型自卸半挂车底盘悬架外加强板实施例与大梁、悬架配合时的第二的结构示意图;
19.主要元件符号说明如下:
20.梯形上部1、第一缺口101、第二缺口102、减重圆孔103、第一倒角104、第二倒角105、开放圆孔106、梯形下部2、第三倒角201、直角避让空间3、组合减重孔4。
具体实施方式
21.为了使本领域的技术人员可以更好地理解本实用新型,下面结合附图和实施例对本实用新型技术方案进一步说明。
22.如图1-3所示,本实用新型的自卸半挂车底盘悬架外加强板,包括一体化的梯形上部1以及梯形下部2,梯形上部1与梯形下部2均为直角梯形,梯形上部1与梯形下部2的底边相靠,斜腰边指向同一侧并在汇合处形成圆滑过渡,梯形上部1和梯形下部2之间形成直角避让空间3,直角避让空间3两直角边由梯形上部1的底边、梯形下部2的直角腰共同组成;
23.梯形上部1设有组合减重孔4;
24.梯形上部1直角腰边一侧的顶角设有第一倒角104,梯形上部1直角腰边一侧的底角设有第二倒角105;
25.梯形上部1和梯形下部2在直角避让空间3处设有开放圆孔106。
26.本案实施中,为了解决行车过程中,车辆转弯时悬架内外侧受力激增,但外侧没有受力支撑点,仅靠焊缝处承力,同时焊缝产生应力集中造成疲劳破坏而开裂,导致悬架b以及与底盘大梁a焊接部位开裂的问题;
27.外加强板通过梯形上部1与大梁a连接,通过梯形下部2与悬架b连接,在每个悬架b外侧焊接两块外加强板,车辆行驶时悬架b外侧受力可通过该加强板传递至大梁a,从而改善焊缝受力情况,外加强板具体连接结构如下:
28.梯形上部1的顶边与大梁a上侧的边板接触,梯形上部1的底边通过直角避让空间3与大梁a下侧的边板接触,梯形上部1的直角腰贴紧大梁a的侧面,梯形上部1的三边均与大梁a焊接固定,开放圆孔106用于容纳大梁a下侧的边板,避免外加强板连接大梁a、悬架b时,发生干涉,第一倒角104和第二倒角105用于避免梯形上部1贴紧大梁a时,与大梁a的内腔发生干涉,梯形下部2的直角腰边紧贴在悬架b的外侧并进行焊接固定。
29.优选,组合减重孔4包括位于梯形上部1直角边一侧的第一缺口101,第二缺口102以及位于梯形上部1底部的减重圆孔103,第一缺口101靠近梯形上部1的顶边,第二缺口102
位于第一缺口101的下方,第二缺口102的面积大于第一缺口101的面积,这样的结构设计,通过第二缺口102的面积大于第一缺口101的面积,第一缺口101在上,第二缺口102在下,来合理的对梯形上部1进行减重,通过减重圆孔103在减重的同时,设置减重圆孔103在梯形上部1的底部,避免过度削弱梯形上部1直角边的结构强度。实际上,也可以根据具体情况具体考虑组合减重孔4中第一缺口101、第二缺口102、减重圆孔103其它的结构形状以及位置分布。
30.优选,梯形下部2直角腰边一侧的顶角设有第三倒角201,这样的结构设计,通过第三倒角201使梯形下部2直角腰边内收,避免梯形下部2与装配面干涉。实际上,也可以根据具体情况具体考虑避免梯形下部2直角腰边与装配面发生干涉的其它结构。
31.上述实施例仅示例性说明本实用新型的原理及其功效,而非用于限制本实用新型。任何熟悉此技术的人士皆可在不违背本实用新型的精神及范畴下,对上述实施例进行修饰或改变。因此,凡所属技术领域中具有通常知识者在未脱离本实用新型所揭示的精神与技术思想下所完成的一切等效修饰或改变,仍应由本实用新型的权利要求所涵盖。
技术特征:1.自卸半挂车底盘悬架外加强板,其特征在于:包括一体化的梯形上部(1)以及梯形下部(2),所述梯形上部(1)与梯形下部(2)均为直角梯形,所述梯形上部(1)与梯形下部(2)的底边相靠,斜腰边指向同一侧并在汇合处形成圆滑过渡,所述梯形上部(1)和梯形下部(2)之间形成直角避让空间(3),所述直角避让空间(3)两直角边由梯形上部(1)的底边、梯形下部(2)的直角腰共同组成;所述梯形上部(1)设有组合减重孔(4);所述梯形上部(1)直角腰边一侧的顶角设有第一倒角(104),所述梯形上部(1)直角腰边一侧的底角设有第二倒角(105);所述梯形上部(1)和梯形下部(2)在直角避让空间(3)处设有开放圆孔(106)。2.根据权利要求1所述的自卸半挂车底盘悬架外加强板,其特征在于:所述组合减重孔(4)包括位于梯形上部(1)直角边一侧的第一缺口(101),第二缺口(102)以及位于梯形上部(1)底部的减重圆孔(103),所述第一缺口(101)靠近梯形上部(1)的顶边,所述第二缺口(102)位于第一缺口(101)的下方,所述第二缺口(102)的面积大于第一缺口(101)的面积。3.根据权利要求2所述的自卸半挂车底盘悬架外加强板,其特征在于:所述梯形下部(2)直角腰边一侧的顶角设有第三倒角(201)。
技术总结本实用新型公开了自卸半挂车底盘悬架外加强板,包括一体化的梯形上部以及梯形下部,梯形上部与梯形下部均为直角梯形,梯形上部与梯形下部的底边相靠,斜腰边指向同一侧并在汇合处形成圆滑过渡,梯形上部和梯形下部之间形成直角避让空间,直角避让空间两直角边由梯形上部的底边、梯形下部的直角腰共同组成;梯形上部设有组合减重孔;梯形上部直角腰边一侧的顶角设有第一倒角,梯形上部直角腰边一侧的底角设有第二倒角;梯形上部和梯形下部在直角避让空间处设有开放圆孔。让空间处设有开放圆孔。让空间处设有开放圆孔。
技术研发人员:陈善辉 胡忠泽 冯军
受保护的技术使用者:重庆耐德永铃专用汽车有限公司
技术研发日:2021.11.08
技术公布日:2022/4/5