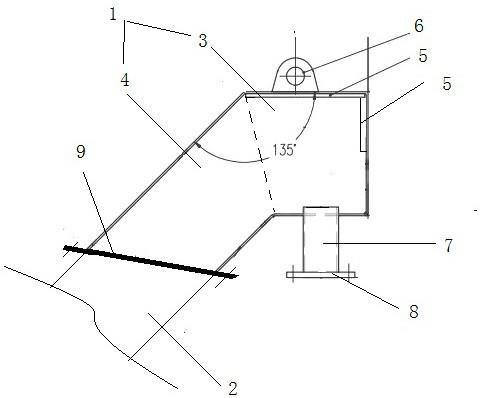
1.本实用新型公开了一种粉料输送的组合弯头,涉及混凝土搅拌站输料设备技术领域。
背景技术:2.混凝土搅拌站粉料输送工作过程中,通过管道向粉仓输送过程中,均会产生摩擦以及压力冲刷着管道壁,尤其在仓顶管道拐弯处的摩擦和压力最大。
3.如图1所示,现有技术中仓顶通过连接90度管道弯头以及横管进行粉料输送,90度管道弯头承受压力和摩擦大,管道弯头容易破损,且粉料输送效率低,且90度管道弯头成本过高。
技术实现要素:4.本实用新型针对上述背景技术中的缺陷,提供一种粉料输送的组合弯头,结构简单,结构稳定,节约成本。
5.为实现上述目的,本实用新型采用的技术方案如下:一种粉料输送的组合弯头,包括,第一卸料通道和与其连接的第二卸料通道,所述的第一卸料通道包括:转向部和斜向部,所述的转向部为一侧开口的箱式结构,所述的斜向部为两侧开口的的箱式结构,所述的第二卸料通道为两侧开口的的箱式结构,转向部的开口端连接斜向部的一端,斜向部的另一端连接第二卸料通道的一端,所述的转向部底端设置进口管,转向部底端设置进口管用于连接输送直管,所述的第二卸料通道用于连接仓顶,第二卸料通道部分连接在仓顶内部,部分设置在外部通过法兰与第一卸料通道连接。
6.进一步的,所述的转向部采用钢板焊接而成,所述的斜向部采用钢板焊接而成,第一卸料通道和与其连接的第二卸料通道均可以采用钢板焊接而成,钢板焊接简单且方便,同时相较于90度管道弯头,钢板焊接成本低。
7.进一步的,所述的转向部内壁焊接加强板,加强板设置于转向部的顶部和三个侧部的内壁上,采用焊接,对转向部的内壁进行加厚,提升转向部的耐磨损性能。
8.进一步的,所述的转向部顶部的外部上连接吊耳件,所述的吊耳件处于顶部的中心位置,方便进行吊装。
9.进一步的,所述的进口处连接进口管路,进口管路连接于转向部底部的中心,进口管路的自由端连接法兰盘,进口管路的下方连接在输送直管上,接收输送直管输送的粉料。
10.进一步的,所述的斜向部与进口管路之间的夹角呈锐角设置,斜向部倾斜向下,粉料经过转向部后,通过斜向部倾斜向下的结构,直接输料至仓顶。
11.有益效果:本实用新型改变了传统90度管道弯头的书送设计,采用箱式管道输送,增大内部空间,减小了管道内粉料对管道的冲击与磨损;同时第二卸料通道倾斜设置,改变了以往90度管道弯头中间连接横管输送方式,减少了输送压力以及指引输送路径提高输送效率;本实用新型在粉料输送一定的情况下,有效分配减小摩擦能力,高效进行粉料输送粉
料,并且不对管道弯头产生影响,增加弯头使用寿命,节约制造安装成本,简化更换维修。
附图说明
12.图1为现有技术结构示意图。
13.图2为本实用新型的结构示意图。
具体实施方式
14.下面结合附图对技术方案的实施作进一步的详细描述。以下实施例仅用于更加清楚地说明本实用新型的技术方案,而不能以此来限制本实用新型的保护范围。
15.如图2所示,一种粉料输送的组合弯头,包括,第一卸料通道1和与其连接的第二卸料通道2,所述的第一卸料通道1包括:转向部3和斜向部4,所述的转向部3为一侧开口的箱式结构,所述的斜向部4为两侧开口的的箱式结构,所述的第二卸料通道2为两侧开口的的箱式结构,转向部3的开口端连接斜向部4的一端,斜向部4的另一端连接第二卸料通道2的一端,所述的转向部3底端设置进口管,转向部3底端设置进口管用于连接输送直管,转向部3用于将从下方的输送直管进入的粉料输送方向从竖直向转为横向,斜向部4与第二卸料通道2的方向一致,所述的第二卸料通道2用于连接仓顶,第二卸料通道2部分连接在仓顶内部,部分设置在外部通过法兰9与第一卸料通道1连接。
16.所述的转向部3采用钢板焊接而成,所述的斜向部4采用钢板焊接而成,第一卸料通道1和与其连接的第二卸料通道2均可以采用钢板焊接而成,钢板焊接简单且方便,同时相较于90度管道弯头,钢板焊接成本低。
17.所述的转向部3内壁焊接加强板5,加强板5设置于转向部3的顶部和三个侧部的内壁上,采用焊接,进口管路7内部粉料输送过程中产生压力和摩擦力不断冲击第一卸料通道1内部,在第一卸料通道1内部顶部和内部侧面压力和摩擦最大,对转向部3的内壁进行加厚,从而提升转向部3的耐磨损性能。
18.所述的转向部3顶部的外部上连接吊耳6件,所述的吊耳6件处于顶部的中心位置,方便进行吊装。
19.所述的进口处连接进口管路7,进口管路7连接于转向部3底部的中心,进口管路7的自由端连接法兰盘8,进口管路7的下方法兰盘连接在输送粉料的直管上,方便维修安装。
20.所述的斜向部4与进口管路7之间的夹角呈锐角设置,斜向部4倾斜向下,粉料经过转向部3后,通过斜向部4倾斜向下的结构,直接输料至粉仓内;将第二卸料通道2一部分插入粉仓仓顶并焊接固定,第一卸料通1与第二卸料通道2通过法兰盘9连接,第二卸料通道2与粉仓顶焊接连接,方便维修安装。
21.工作原理:本实用新型输粉料时,粉料经过输送直管到达第一卸料通道处,由于粉料是通过压力的输送方式,以及输送中压力大于粉料的重力,尤其拐弯处局部压力最大且产生高压区,摩擦力最大,以及会产生压力损失,影响粉料输送效率;所以将第一卸料通道1用箱体结构增大内部空间和内壁加厚,第二卸料通道2用箱体结构增大内部空间,第二卸料通道2与斜向部4倾斜向下方向,减少内部压力,减小了对内部的磨损,指引输送路径,高效进行粉料输送。
22.本实用新型对原来仓顶的结构改变影响较小,第二卸料通道先安装于仓顶,再通
过法兰连接第一卸料通道,以及将输送直管用法兰连接于第一卸料通道,完成整个装置的连接,方便安装维修。
23.本实用新型改变了传统90度管道弯头的输送设计,采用箱式管道输送,内部内部加厚,减小了粉料对管道的冲击与磨损;同时倾斜设置第二卸料通道,改变了以往90度管道弯头加中间连接横管输送方式,减少了输送压力以及指导输送路径;以及组合弯头顶部加入吊耳,易磨损部分用法兰连接,简化更换维修。本实用新型在粉料输送一定的情况下,有效分配减小摩擦能力,高效进行粉料输送粉料,并且不对管道弯头产生影响,增加弯头使用寿命,节约制造安装成本,简化更换维修。
24.以上所述仅是本实用新型的优选实施方式,应当指出,对于本技术领域的普通技术人员来说,在不脱离本实用新型技术原理的前提下,还可以做出若干改进和变形,这些改进和变形也应视为本实用新型的保护范围。
技术特征:1.一种粉料输送的组合弯头,其特征在于,包括,第一卸料通道和与其连接的第二卸料通道,所述的第一卸料通道包括:转向部和斜向部,所述的转向部为一侧开口的箱式结构,所述的斜向部为两侧开口的箱式结构,转向部的开口端连接斜向部的一端,斜向部的另一端连接第二卸料通道的一端,所述的转向部底端设置进口管。2.根据权利要求1所述的一种粉料输送的组合弯头,其特征在于,所述的转向部采用钢板焊接而成,所述的斜向部采用钢板焊接而成。3.根据权利要求1所述的一种粉料输送的组合弯头,其特征在于,所述的转向部内壁焊接加强板。4.根据权利要求1所述的一种粉料输送的组合弯头,其特征在于,所述的进口处连接进口管路,进口管路连接于转向部底部的中心,进口管路的自由端连接法兰盘;第一卸料通道和第二卸料通道之间采用法兰连接。5.根据权利要求4所述的一种粉料输送的组合弯头,其特征在于,所述的斜向部与进口管路之间的夹角呈锐角设置。6.根据权利要求1所述的一种粉料输送的组合弯头,其特征在于,所述的转向部顶部的外部上连接吊耳件,所述的吊耳件处于顶部的中心位置。
技术总结本实用新型公开了一种粉料输送的组合弯头,包括,第一卸料通道和与其连接的第二卸料通道,所述的第一卸料通道包括:转向部和斜向部,所述的转向部为一侧开口的箱式结构,所述的斜向部为两侧开口的的箱式结构,转向部的开口端连接斜向部的一端,斜向部的另一端连接第二卸料通道的一端,所述的转向部底端设置进口管。本实用新型改变了传统90度管道弯头的输送设计,采用箱式管道输送,减小了粉料对管道的冲击与磨损;同时第二卸料通道倾斜设置,改变了以往90度管道弯头中间连接横管输送方式,减少了输送压力,减少了粉料对管道冲击与磨损增加使用寿命,提高粉料输送效率以及简化安装维修。修。修。
技术研发人员:魏礼彬 刘学峰 李玉柱 尹洪贺 豆锐科
受保护的技术使用者:徐州徐工施维英机械有限公司
技术研发日:2022.01.21
技术公布日:2022/8/8