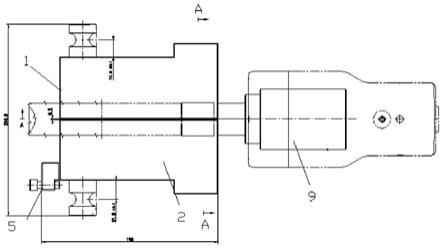
1.本发明属于直升机大管径导管胀形技术领域,尤其涉及一种直升机大管径导管端头胀形设备和方法。
背景技术:2.在现有的科研生产任务中存在许多大管径的钢管需要胀形成形,特别是在操纵系统中的驾驶杆尤为常见。
3.此类零件现有的胀形工艺主要为利用聚氨酯挤压成形,由于聚氨酯管套均为一次性使用,拆卸时与拉伸芯棒卡的较紧,操作时较为繁琐,且导管利用聚氨酯胀形时胀形力较小,需多次反复操作再配合后续导管工校形保证内外径尺寸要求,影响产品的外观质量的同时需花费大量时间,严重影响该类导管的产品交付进度。
4.其缺点具体如下;
5.1、聚氨酯容易导致导管内侧壁被挤划伤,影响导管内侧壁成形质量;
6.2、被挤压的聚氨酯环为一次性消耗品,由于尺寸根据导管要求,存在需要特制问题,成本居高不下;
7.3、导管利用聚氨酯胀形时需多次胀形,内外径尺寸无法一次胀形保证,后续需多次校形,费时费力;
8.4、每次成形后,均需要拆卸分模具各部件,尤其是被挤碎或卡紧,其操作复杂,工作量巨大,成形效率较低;
9.5、对应胀形长度要求大于40mm的大管径导管无法进行胀形,存在工艺缺陷。
技术实现要素:10.针对上述技术问题,本发明提供了一种直升机大管径导管端头胀形设备和方法,主要通过利用胀形模夹紧导管弯曲过渡部分,再利用芯棒分两次或多次胀形使导管内外径达到相关标准要求。
11.第一方面,本发明提供了一种直升机大管径导管端头胀形设备,所述胀形设备包括:
12.冷挤胀形模,具有弧形槽,所述弧形槽用于夹紧直升机大管径导管;其中,所述直升机大管径导管包括直线段和弧形段;
13.胀形芯棒,设置在数控管端成型机上,用于插入所述直升机大管径导管的直线段,并进行胀形;
14.其中,所述直升机大管径导管的直线段的轴心与所述胀形芯棒的轴心位于同一轴线。
15.优选地,所述弧形槽具有防滑槽,所述防滑槽呈鱼鳞状或环状。
16.优选地,所述胀形芯棒,还用于至少对所述直升机大管径导管进行两次胀形;其中,所述胀形芯棒的直径与所述直升机大管径导管的直径相匹配。
17.优选地,所述冷挤胀形模设置在数控管端成型机的平台上,所述冷挤胀形模包括:
18.第一冷挤胀形模,具有第一弧形槽;
19.第二冷挤胀形模,具有第二弧形槽;其中,所述第一弧形槽和所述第二弧形槽相互配合来夹持所述直升机大管径导管。
20.第二方面,本发明提供了一种直升机大管径导管端头胀形方法,所述方法包括:
21.用冷挤胀形模夹紧直升机大管径导管;其中,所述直升机大管径导管包括直线段和弧形段;
22.将胀形芯棒插入所述直升机大管径导管的直线段,并进行胀形;其中,所述胀形芯棒设置在数控管端成型机上;
23.其中,所述直升机大管径导管的直线段的轴心与所述胀形芯棒的轴心位于同一轴线。
24.优选地,所述弧形槽具有防滑槽,所述防滑槽呈鱼鳞状或环状。
25.优选地,所述方法还包括:
26.用胀形芯棒至少对所述直升机大管径导管进行两次胀形;其中,所述胀形芯棒的直径与所述直升机大管径导管的直径相匹配。
27.优选地,所述冷挤胀形模设置在数控管端成型机的平台上,所述冷挤胀形模包括:
28.第一冷挤胀形模,具有第一弧形槽;
29.第二冷挤胀形模,具有第二弧形槽;其中,所述第一弧形槽和所述第二弧形槽相互配合来夹持所述直升机大管径导管。
30.本发明的技术效果:
31.本发明提供了一种直升机大管径导管端头胀形设备,包括:冷挤胀形模,具有弧形槽,所述弧形槽用于夹紧直升机大管径导管;其中,所述直升机大管径导管包括直线段和弧形段;胀形芯棒,设置在数控管端成型机上,用于插入所述直升机大管径导管的直线段,并进行胀形;其中,所述直升机大管径导管的直线段的轴心与所述胀形芯棒的轴心位于同一轴线;本发明提升了胀形成形工艺,提高了产品的工作效率和合格率
附图说明
32.图1是本申请实施例提供的导管外形的结构示意图;
33.图2是本申请实施例提供导管端头胀形示意图的;
34.图3是本申请实施例提供的导管端头胀形时的剖视图;
35.图4是本申请实施例提供的导管端头胀形时的俯视图;
36.图5是本申请实施例提供的图4中a-a处的剖视图;
37.其中,1-第一冷挤胀形模、2-第二冷挤胀形模、5-压块、8-定位销、9-芯棒。
具体实施方式
38.本发明根据现有大管径导管类的外形尺寸要求,将现有利用聚氨酯收压成形的工艺更改外利用数控管端机冷挤成形。通过利用导管弯曲部分的外形进行夹持保证胀形过程中的夹紧力,再利用芯棒分两次或多次胀形使导管内外径以满足相关技术要求,提升胀形成形工艺,提高产品的工作效率和合格率。
39.本发明提供的一种大管径导管端头胀形工艺方法,具体实施方式如下:
40.1.基于导管外形尺寸,合理设计冷挤胀形模。
41.2.将冷挤胀形模安装至数控管端成型机;
42.3.利用和导管内径相匹配的胀形芯棒进行多次胀形,一般首次胀形控制芯棒的外径相对需胀形尺寸外径小0.1mm,再利用最终尺寸的芯棒进行胀形,胀形后尺寸保证相关技术要求。
43.请参阅附图1,对应为一种大管径导管的外形示意图,材料为15crmnmova,退火,g36x1,gjb5111(或z9-0130),外形需胀形一端长度为105mm,另一端需胀形长度为35mm,胀形以后的导管内径需保证为φ35.2,导管两圆弧部分通过直线段长度为70mm的直管进行连接。
44.请参阅附图2,对应为一种大管径导管需胀形一端将部分弯曲弧度和需胀形部分的导管装夹在冷挤胀形模,在夹紧大管径导后芯棒深入导管内壁进行挤胀胀形。
45.请参阅附图3,对应为一种大管径导管在胀形时的剖视图,大管径导管部分弯曲弧度和需胀形部分的导管装夹在冷挤胀形模,芯棒装通过外形装夹在数控管端机,胀形时大管径导管的直线段的轴心与胀形芯棒9的轴心位于同一轴线。
46.请参阅附图4,对应为一种大管径导管在胀形时的俯视图,大管径导管部分弯曲弧度和需胀形部分的导管装夹在冷挤胀形模,冷挤胀形模利用工装的外形装夹在数控管端成形机上,通过导正销、压块5固定在管端成形机上,其中导正销保证装夹在数控管端机的第一冷挤胀形模和第二冷挤胀形模处于同一相对位置。
47.请参阅附图5,对应为实施例提供的大管径导管在胀形时的俯视图中的a-a处的剖视图,表示胀形过程中第一冷挤胀形模1和第二冷挤胀形模2在夹紧时通过定位销8保证大管径导管需夹持的圆弧部分和冷挤胀形模装夹时的弧形槽(包括第一弧形槽和第二弧形槽)外形一致,确保大管径导管不被夹伤或者无法夹紧的情况发生。
技术特征:1.一种直升机大管径导管端头胀形设备,其特征在于,所述胀形设备包括:冷挤胀形模,具有弧形槽,所述弧形槽用于夹紧直升机大管径导管;其中,所述直升机大管径导管包括直线段和弧形段;胀形芯棒,设置在数控管端成型机上,用于插入所述直升机大管径导管的直线段,并进行胀形;其中,所述直升机大管径导管的直线段的轴心与所述胀形芯棒的轴心位于同一轴线。2.根据权利要求1所述的直升机大管径导管端头胀形设备,其特征在于,所述弧形槽具有防滑槽,所述防滑槽呈鱼鳞状或环状。3.根据权利要求2所述的直升机大管径导管端头胀形设备,其特征在于,所述胀形芯棒,还用于至少对所述直升机大管径导管进行两次胀形;其中,所述胀形芯棒的直径与所述直升机大管径导管的直径相匹配。4.根据权利要求3所述的直升机大管径导管端头胀形设备,其特征在于,所述冷挤胀形模设置在数控管端成型机的平台上,所述冷挤胀形模包括:第一冷挤胀形模,具有第一弧形槽;第二冷挤胀形模,具有第二弧形槽;其中,所述第一弧形槽和所述第二弧形槽相互配合来夹持所述直升机大管径导管。5.一种直升机大管径导管端头胀形方法,其特征在于,所述方法包括:用冷挤胀形模夹紧直升机大管径导管;其中,所述直升机大管径导管包括直线段和弧形段;将胀形芯棒插入所述直升机大管径导管的直线段,并进行胀形;其中,所述胀形芯棒设置在数控管端成型机上;其中,所述直升机大管径导管的直线段的轴心与所述胀形芯棒的轴心位于同一轴线。6.根据权利要求5所述的直升机大管径导管端头胀形方法,其特征在于,所述弧形槽具有防滑槽,所述防滑槽呈鱼鳞状或环状。7.根据权利要求6所述的直升机大管径导管端头胀形方法,其特征在于,所述方法还包括:用胀形芯棒至少对所述直升机大管径导管进行两次胀形;其中,所述胀形芯棒的直径与所述直升机大管径导管的直径相匹配。8.根据权利要求7所述的直升机大管径导管端头胀形方法,其特征在于,所述冷挤胀形模设置在数控管端成型机的平台上,所述冷挤胀形模包括:第一冷挤胀形模,具有第一弧形槽;第二冷挤胀形模,具有第二弧形槽;其中,所述第一弧形槽和所述第二弧形槽相互配合来夹持所述直升机大管径导管。
技术总结本发明提供了一种直升机大管径导管端头胀形设备,包括:冷挤胀形模,具有弧形槽,所述弧形槽用于夹紧直升机大管径导管;其中,所述直升机大管径导管包括直线段和弧形段;胀形芯棒,设置在数控管端成型机上,用于插入所述直升机大管径导管的直线段,并进行胀形;其中,所述直升机大管径导管的直线段的轴心与所述胀形芯棒的轴心位于同一轴线;同时,本发明还提供了一种直升机大管径导管端头胀形方法;本发明提升了胀形成形工艺,提高了产品的工作效率和合格率。和合格率。和合格率。
技术研发人员:罗挺 姚臻 谢忠华 张有富 杨陆军 凌国彬
受保护的技术使用者:昌河飞机工业(集团)有限责任公司
技术研发日:2021.11.26
技术公布日:2022/4/12