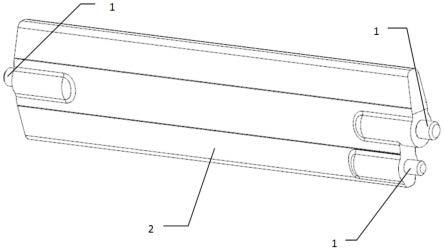
1.本发明属于飞机环控系统技术领域,具体涉及一种百叶窗结构中将金属小轴的一端与复合材料小叶片注塑为一体的加工方法。
背景技术:2.飞机座舱百叶窗可调式通风口是军用飞机中座舱中调节环控出风方向的重要附件,在飞机座舱中,原通风口为固定式整体百叶窗,环控风吹出时为固定风向,无法满足飞行员的舒适性需求。为满足该需求,将百叶窗设计为可调式结构,其中叶片为该类通风口的核心零件,通过调整叶片角度,达到调整环控出风风向的目的。
3.由于金属小轴的尺寸较小、重量较轻,同时复合材料小叶片尺寸也较小,在金属小轴与复合材料小叶片注塑为一体时,金属小轴在注塑过程中容易出现漂移,导致尺寸无法控制;另外在使用过程中金属小轴出现松动时,容易脱出或者旋转,为了能精准控制外露小轴尺寸,同时防止小轴在松动的情况下避免脱出或转动,需要对金属小轴结构进行改进,同时调整加工方法,达到并满足使用要求。
技术实现要素:4.本发明旨在提供一种金属小轴与复合材料小叶片注塑为一体的方法,将金属小轴的一端与复合材料小叶片注塑为一体,消除注塑过程中金属小轴的漂移现象,控制金属小轴的露出段尺寸和位置,防止金属小轴在使用中发生脱离和松动的问题,并形成标准化结构设计思路,提高百叶窗零件的使用安全性和可靠性,提高飞机标准化设计水平,减少新结构应用带来的研制风险。
5.本发明是通过如下技术方案予以实现的:
6.金属小轴与复合材料小叶片注塑为一体的方法,所述金属小轴和复合材料小叶片均为小尺寸、小重量的零件,注塑为一体的方法包括,
7.在金属小轴的非注塑(即金属小轴没有埋入复合材料小叶片中的部分)端延伸出一段相同材质的、易折断的尾段;
8.在金属小轴的注塑端(即金属小轴埋入复合材料小叶片中的部分)表面加工出槽口和平面,槽口能够增加金属小轴与复合材料小叶片的结合力,而平面能够改变复合材料小叶片与金属小轴表面之间的受力方式和方向,避免发生相对旋转;同时,该方案能够使金属小轴与复合材料之间结合更换;
9.当金属小轴从注塑开始到结束冷却过程中需要全程进行夹紧,防止金属小轴在注塑过程中漂移,同时防止在冷却过程中,由于冷却速度、收缩不同,导致金属小轴脱出。
10.当金属小轴满足上述条件后,在注塑模具的模腔外侧对应金属小轴的位置放置工装,调整金属小轴在工装上的夹持位置,开始注塑,注塑过程中始终保持工装夹持住金属小轴的尾段从而确保金属小轴外露在复合材料小叶片外侧的尺寸和位置,注塑完成后,折断金属小轴上多余的尾段。
11.作为一种选择,所述金属小轴上的尾段包括,
12.夹持在工装内的夹持部分;
13.易折断的断裂部分,断裂部分的外径远小于金属小轴注塑端外径以及夹持部分的外径,或者断裂部分的外径与夹持部分相同但表面开有折断槽口。
14.作为一种选择,所述金属小轴的注塑端表面槽口为沿着金属小轴周向表面分布的环形槽口,环形槽口至少有一条,增加环形槽口的数量可以提高金属小轴与复合材料小叶片的结合力。
15.作为一种选择,所述金属小轴的注塑端表面平面平行于金属小轴的轴线方向,且平面到金属小轴轴线的垂直距离小于金属小轴的半径,采用去除材料的方式在金属小轴上形成平面,简化加工过程。
16.作为一种选择,注塑时,所述金属小轴的注塑端表面平面末端对齐复合材料小叶片的端面,便于观察和判断金属小轴的外露尺寸和位置是否符合要求。
17.作为一种选择,所述金属小轴的注塑端表面的槽口和平面相交,形成同时防止金属小轴旋转和脱离的结构区域。
18.作为一种选择,为了避免金属小轴与复合材料小叶片连接界面因收缩系数不同而导致的局部裂纹,可以在工装上设计加热结构,对金属小轴进行加热,使得金属小轴的冷却速度尽量接近复合材料小叶片的冷却速度,或者说二者的冷却速度差异尽量较小。例如,在工装上增加发热电阻丝,在夹持金属小轴的同时进行加热。
19.与现有技术相比,本发明的注塑方法具备以下特点:
20.(1)在金属小轴的注塑部分表面加工槽口,确保金属小轴在复合材料小叶片配合位置松动时不会脱出;
21.(2)在金属小轴的注塑部分表面加工平面,确保金属小轴在复合材料小叶片配合位置松动时不会转动;
22.(3)在金属小轴的非注塑部分延长出一部分用于工装夹持,从而确保在注塑过程中金属小轴不会因为自重太轻而发生位置移动(漂移),确保金属小轴非注塑部分(外露部分)的尺寸和位置符合设计要求,同时,延长出的部分带有易折断结构,当完成注塑时,可方便的去除延长出的部分;
23.(4)当金属小轴的材质与复合材料小叶片的冷却速度差异较大时,考虑在夹持金属小轴的工装中增加加热结构,对金属小轴进行加热,控制金属小轴的冷却速度,使得二者在注塑冷却阶段不会因过大的温差导致连接界面产生裂纹。
附图说明
24.图1为金属小轴的一端与复合材料小叶片注塑为一体的最终百叶窗零件三维结构示意图;
25.图2为将金属小轴的一端与复合材料小叶片注塑时未去除尾段的模型示意图;
26.图3为将金属小轴的一端与复合材料小叶片注塑过程中的模型示意图;
27.图中,1-金属小轴;2-复合材料小叶片;3-金属小轴尾段;4-工装;5-注塑模具。
具体实施方式
28.下面结合附图和具体实施例对本发明作进一步的说明,但不应就此理解为本发明所述主题的范围仅限于以下的实施例,在不脱离本发明上述技术思想情况下,凡根据本领域普通技术知识和惯用手段做出的各种修改、替换和变更,均包括在本发明的范围内。
29.针对金属小轴1埋入复合材料小叶片2进行注塑时易漂移,注塑后易脱离或旋转的问题,本发明的基本思路是将金属小轴1埋入复合材料小叶片2内的圆柱面部分中部设计环形槽(增加复合材料小叶片2与金属小轴1的结合表面),同时在圆柱面上设计出局部平面(该平面用于防止金属小轴1旋转,局部平面与环形槽可以相交,也可以不相交),将露出复合材料小叶片2的金属小轴1端部设计出有折断槽(折断槽类似一个切口或者说截面急剧减小的结构)的尾段3,在注塑时,将金属小轴1的尾段3夹于工装4中,注塑段放入复合材料小叶片2注塑模具5中,注塑完成待叶片冷却后,取出整体叶片,去除金属小轴1的尾段3,完成百叶窗零件的注塑工作。
30.如图1所示,是本发明将金属小轴1的一端与复合材料小叶片后的注塑为一体后的最终百叶窗零件图;该结构主要由金属小轴1、复合材料小叶片2注塑为一体并切除尾段3后实现。
31.如图2所示,是本发明将带有尾段3的金属小轴1的一端与复合材料小叶片2注塑前的模型示意图,该图中主要表达了金属小轴1上尾段3、环形槽和平面结构。
32.如图3所示,是本发明将金属小轴1的一端与复合材料小叶片2进行注塑的过程模型示意图,该图中金属小轴1的尾段3被工装4夹紧放入注塑模具5中。
33.上述实施例并不用于限定本发明的保护范围,凡在本发明的技术方案基础上所做出的变形、修饰或等同替换等,均应落入本发明的保护范围内。
技术特征:1.金属小轴与复合材料小叶片注塑为一体的方法,所述金属小轴(1)和复合材料小叶片(2)均为小尺寸、小重量的零件,其特征在于:注塑为一体的方法包括,在金属小轴(1)的非注塑端延伸出一段相同材质的、易折断的尾段(3);在金属小轴(1)的注塑端表面加工出槽口和平面;当金属小轴(1)满足上述条件后,在注塑模具(5)的模腔外侧对应金属小轴(1)的位置放置工装(4),调整金属小轴(1)在工装(4)上的夹持位置,开始注塑,注塑过程中始终保持工装(4)夹持住金属小轴(1)的尾段(3)从而确保金属小轴(1)外露在复合材料小叶片(2)外侧的尺寸和位置,注塑完成后,折断金属小轴(1)上多余的尾段(3)。2.根据权利要求1所述的金属小轴与复合材料小叶片注塑为一体的方法,其特征在于:所述金属小轴(1)上的尾段(3)包括,夹持在工装(4)内的夹持部分;易折断的断裂部分,断裂部分的外径远小于金属小轴(1)注塑端外径以及夹持部分的外径,或者断裂部分的外径与夹持部分相同但表面开有折断槽口。3.根据权利要求1所述的金属小轴与复合材料小叶片注塑为一体的方法,其特征在于:所述金属小轴(1)的注塑端表面槽口为沿着金属小轴(1)周向表面分布的环形槽口,环形槽口至少有一条。4.根据权利要求1所述的金属小轴与复合材料小叶片注塑为一体的方法,其特征在于:所述金属小轴(1)的注塑端表面平面平行于金属小轴(1)的轴线方向,且平面到金属小轴(1)轴线的垂直距离小于金属小轴(1)的半径。5.根据权利要求1所述的金属小轴与复合材料小叶片注塑为一体的方法,其特征在于:注塑时,所述金属小轴(1)的注塑端表面平面末端对齐复合材料小叶片(2)的端面。6.根据权利要求1所述的金属小轴与复合材料小叶片注塑为一体的方法,其特征在于:所述金属小轴(1)的注塑端表面的槽口和平面相交。
技术总结本发明公开了一种金属小轴与复合材料小叶片注塑为一体的方法,在金属小轴的非注塑端延伸出一段相同材质的、易折断的尾段,在金属小轴的注塑端表面加工出槽口和平面,在注塑模具的模腔外侧对应金属小轴的位置放置工装,调整金属小轴在工装上的夹持位置,开始注塑,注塑过程中始终保持工装夹持住金属小轴的尾段,注塑后去除尾段。本发明将金属小轴的一端准确地与复合材料小叶片端部注塑为一整体,同时保证了金属小轴长度方向露出复合材料小叶片端部符合规定长度,以及保证了金属小轴在使用过程中不会因出现结合部位松动导致在复合材料小叶片内旋转或脱出复合材料小叶片,从而使金属小轴与复合材料小叶片形成整体百叶窗叶片。属小轴与复合材料小叶片形成整体百叶窗叶片。属小轴与复合材料小叶片形成整体百叶窗叶片。
技术研发人员:施发国 胡琼琼 杨骁 孟媛
受保护的技术使用者:贵州永红航空机械有限责任公司
技术研发日:2022.10.17
技术公布日:2023/1/17