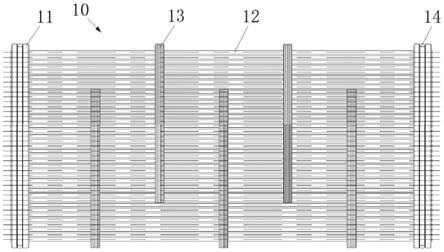
1.本申请属于换热器技术领域,特别涉及一种可拆卸燃滑油散热器芯体及燃滑油散热器。
背景技术:2.随着航空发动机燃滑油散热器滑油使用温度的提升,使得耐高温铝合金散热管因自身硬度高,给传统的胀接工艺参数选取带来较大挑战。同时,燃滑油散热器长时间工作后,散热管外表面的滑油结焦以及污垢沉积会影响散热器的热传导率,进而降低燃滑油散热器的散热性能,而传统的胀接工艺生产的燃滑油散热器芯体散热管不可拆卸,当前只能通过更换新的散热器芯体来恢复燃滑油散热器性能。
3.耐高温的铝合金散热管胀接工艺难度大,胀接后的散热器芯体在随后的气密检查过程中,若发现渗漏将导致整个散热器芯体的报废;胀接后的铝合金散热管长期工作后外表面滑油结焦和污垢沉积会导致燃滑油散热器性能下降,当前只能通过更换散热器芯体来恢复燃滑油散热器性能。
4.尽管当前通过胀接工艺使用的胀杆选材和强化处理,散热管胀接过程中难以避免出现胀接不紧密导致端面泄漏、胀头胀杆受力过大被拉断的情况;另外,长期工作后外表面滑油结焦和污垢沉积导致燃滑油散热器性能下降,只能通过更换散热器芯体来恢复燃滑油散热器性能。
技术实现要素:5.本申请的目的是提供了一种可拆卸燃滑油散热器芯体,以解决或减轻上述至少一个问题。
6.在一方面,本申请提供了一种可拆卸燃滑油散热器芯体,所述芯体包括:由形状记忆合金制成的端板和由多个散热管构成的散热管簇,所述端板上设有按规则排布的散热管安装孔,所述散热管簇安装于所述散热管安装孔内,其中,所述散热器安装孔的孔径在较高的第一温度下小于所述散热管的外径,而散热器安装孔的孔径在较低的第二温度下大于散热管的外径,使得所述端板与所述散热管簇在不低于第一温度下形成紧固密封,而在第二温度下能够进行拆卸。
7.进一步的,所述散热器安装孔的孔径在第二温度下与所述散热管的外径差值大于所述散热器安装孔的孔径在第一温度下与所述散热管的外径差值。
8.进一步的,所述散热管采用2a16铝合金材料制成。
9.进一步的,所述形状记忆合金在不低于第一温度下能够产生相变形变,该相性形变所提供的回复应力与所述散热管的拉伸强度相同或相近。
10.进一步的,还包括:折流板,所述折流板与所述端板平行设置,使得两端板之间能够形成散热介质流动的折返通道。
11.进一步的,所述折流板的长度小于所述端板的长度。
12.进一步的,所述端板的端面设有密封圈,用于与散热器壳体进行密封。
13.此外,本申请还提供了一种燃滑油散热器,所述燃滑油散热器包括:
14.如上任一所述的可拆卸燃滑油散热器芯体;以及
15.包裹在所述可拆卸燃滑油散热器芯体外侧的散热器壳体,所述散热器壳体与所述端板固定密封。
附图说明
16.为了更清楚地说明本申请提供的技术方案,下面将对附图作简单地介绍。显而易见地,下面描述的附图仅仅是本申请的一些实施例。
17.图1为本申请的可拆卸燃滑油散热器芯体结构示意图。
18.图2为本申请的端板结构示意图。
具体实施方式
19.为使本申请实施的目的、技术方案和优点更加清楚,下面将结合本申请实施例中的附图,对本申请实施例中的技术方案进行更加详细的描述。
20.如图1和图2所示,本申请提供的燃滑油散热器芯体10包括:采用形状记忆合金制成的左右两端各一个的端板11以替代现有技术中的铝合金端板和由多个散热器管12构成的散热管簇,在端板11上设有按一定规则排布的散热管安装孔,散热管簇安装在散热管安装孔内,其中,端板11上的散热管安装孔可在常温下进行加工,在常温下的散热管安装孔孔径比散热管12的外径小约4%,而端板11的散热管安装孔在极低的液氮温度下扩径约8%从而大于散热管12的外径尺寸,这就使得端板11与散热管12在常温或高于常温的工作环境下,端板11与散热管12形成紧固密封,而在液氮环境下可将端板11与散热管12进行拆卸。
21.在本申请优选实施例中,散热器安装孔的孔径在较低温度下与散热管12的外径差值大于较高温度下散热器安装孔的孔径与散热管12的外径差值。
22.在本申请一实施例中,散热管12采用2a16铝合金材料制成。在将散热管12与端板11进行装配时,随着温度的升高,记忆合金材料的端板11产生相变形变,该相变形变足以产生较高的回复应力,该回复应力高达约350mpaa,这与上述实施例中的2a16铝合金散热管12的拉伸强度350mpa基本一致,这就使得形状记忆合金材料的端板11与散热管簇可以形成紧固密封。同样的,在将散热管12与端板11进行拆卸时,可将散热器芯体10置于液氮环境中,形状记忆合金材料的端板11上的散热管安装孔孔径将扩径约8%,此时可将散热管12从端板11拆下。进行清洗后,可按上述装配过程重新恢复装配,从而解决了现有技术中燃滑油散热器芯体上散热管无法清洗的现状,大大提升了燃滑油散热器芯体的经济性。
23.如图1所示,本申请的散热器芯体还包括折流板13,折流板13的数量可以为1个或多个,其与端板11平行设置,从而可以使散热器内形成换热介质的流通通道,增加换热效率。进一步的,折流板13的长度应小于端板11的长度,从而使折流板13与散热器壳体(未示出)之间存在间隙,该间隙为换热介质的流通空间。
24.此外,本申请的散热器芯体中,端板11的端面设有密封圈14,当散热器芯体10与散热器壳体固定连接之后,该密封圈14可用于实现散热器芯体10与散热器壳体之间的密封。
25.最后,本申请中还提供了一种燃滑油散热器,该燃滑油散热器包括上述中散热器
芯体和散热器壳体,散热器壳体包裹在散热器芯体外侧,且散热器壳体与散热器芯体的端板固定连接且密封,从而在散热器壳体内可以形成散热空间。
26.本申请所提供的散热器芯体中通过采用形状记忆合金制造端板而替代原技术中的铝合金端板,利用记忆合金在不同温度下的相变所产生的形变实现端板和散热管簇之间的紧固密封及拆卸,解决了耐高温的铝合金散热管胀接工艺难度大的问题,还可以避免因胀接造成散热器芯体气密检查发现渗漏后导致的整个散热器芯体的报废,同时散热管簇能够从端板上拆下并清洗因长期工作后外表面滑油结焦和沉积污垢,进而恢复燃滑油散热器的性能,避免以往只能将散热器芯体报废带来的经济损失。
27.以上所述,仅为本申请的具体实施方式,但本申请的保护范围并不局限于此,任何熟悉本技术领域的技术人员在本申请揭露的技术范围内,可轻易想到的变化或替换,都应涵盖在本申请的保护范围之内。因此,本申请的保护范围应以所述权利要求的保护范围为准。
技术特征:1.一种可拆卸燃滑油散热器芯体,其特征在于,所述芯体包括:由形状记忆合金制成的端板(11)和由多个散热管(12)构成的散热管簇,所述端板(11)上设有按规则排布的散热管安装孔,所述散热管簇安装于所述散热管安装孔内,其中,所述散热器安装孔的孔径在较高的第一温度下小于所述散热管(12)的外径,而散热器安装孔的孔径在较低的第二温度下大于散热管(12)的外径,使得所述端板(11)与所述散热管簇在不低于第一温度下形成紧固密封,而在第二温度下能够进行拆卸。2.如权利要求1所述的可拆卸燃滑油散热器芯体,其特征在于,所述散热器安装孔的孔径在第二温度下与所述散热管(12)的外径差值大于所述散热器安装孔的孔径在第一温度下与所述散热管(12)的外径差值。3.如权利要求1所述的可拆卸燃滑油散热器芯体,其特征在于,所述散热管(12)采用2a16铝合金材料制成。4.如权利要求3所述的可拆卸燃滑油散热器芯体,其特征在于,所述形状记忆合金在不低于第一温度下能够产生相变形变,该相性形变所提供的回复应力与所述散热管(12)的拉伸强度相同或相近。5.如权利要求1所述的可拆卸燃滑油散热器芯体,其特征在于,还包括:折流板(13),所述折流板(13)与所述端板(11)平行设置,使得两端板(11)之间能够形成散热介质流动的折返通道。6.如权利要求5所述的可拆卸燃滑油散热器芯体,其特征在于,所述折流板(13)的长度小于所述端板(11)的长度。7.如权利要求1所述的可拆卸燃滑油散热器芯体,其特征在于,所述端板(11)的端面设有密封圈(14),用于与散热器壳体进行密封。8.一种燃滑油散热器,其特征在于,所述燃滑油散热器包括:如权利要求1至7任一所述的可拆卸燃滑油散热器芯体;以及包裹在所述可拆卸燃滑油散热器芯体外侧的散热器壳体,所述散热器壳体与所述端板(11)固定密封。
技术总结本申请提供了一种可拆卸燃滑油散热器芯体,所述芯体包括:由形状记忆合金制成的端板和由多个散热管构成的散热管簇,所述端板上设有按规则排布的散热管安装孔,所述散热管簇安装于所述散热管安装孔内,其中,所述散热器安装孔的孔径在较高的第一温度下小于所述散热管的外径,而散热器安装孔的孔径在较低的第二温度下大于散热管的外径,使得所述端板与所述散热管簇在不低于第一温度下形成紧固密封,而在第二温度下能够进行拆卸。本申请中通过采用形状记忆合金制造端板而替代原技术中的铝合金端板,利用记忆合金在不同温度下的相变所产生的形变实现端板和散热管簇之间的紧固密封及拆卸,解决了耐高温的铝合金散热管胀接工艺问题及散热管拆卸问题。问题及散热管拆卸问题。问题及散热管拆卸问题。
技术研发人员:周志宏 董云 谷俊
受保护的技术使用者:中国航发沈阳发动机研究所
技术研发日:2021.11.29
技术公布日:2022/3/11