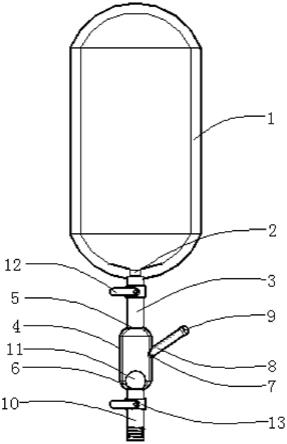
1.本实用新型涉及化学设备技术领域,具体涉及能有效防止下料过程中混入空气的助剂成品釜。
背景技术:2.成品釜的下料是化学生产中最常见的工序之一,现有的下料装置大多采用成品釜连接临时管进行下料,每次下料都需进行安装和拆卸,费时费力、效率低,下料时物料与空气接触会造成物料的变质,不利于快速、高效、无损地进行下料。
技术实现要素:3.鉴于现有技术中的上述缺陷或不足,期望提供能有效防止下料过程中混入空气的助剂成品釜。
4.根据本申请实施例提供的技术方案,能有效防止下料过程中混入空气的助剂成品釜,包括釜体、下料口、第一下料管、集气管、进液口、排液口、进水口、注水管、密封套、第二下料管、浮力球、第一阀门、第二阀门、支撑柱,所述釜体的底部中心处开设有所述下料口,所述下料口上通过焊接与所述第一下料管顶部固接,所述第一下料管底部通过焊接固接有所述集气管,所述集气管顶部中心处开设有所述进液口,所述进液口上通过焊接与所述第一下料管底部固接,所述集气管底部中心处开设有所述排液口,所述集气管的侧壁上开设有所述进水口,所述进水口通过焊接固接有所述注水管,所述注水管远离所述进水口这端套设有所述密封套,所述排液口上通过焊接固接有所述第二下料管,所述集气管内部设置有所述浮力球,所述浮力球的底部贴紧所述排液口,所述第一下料管设置有所述第一阀门,所述第二下料管上设置有所述第二阀门,所述釜体的底部通过焊接设置有所述支撑柱。
5.本实用新型中,所述集气管的顶部和底部为圆弧形结构,所述集气管的中部为一圆柱体结构。
6.本实用新型中,所述集气管和釜体同轴。
7.本实用新型中,所述进液口、排液口和下料口同轴且直径相等。
8.本实用新型中,所述注水管倾斜设置,且所述注水管顶部与所述集气管的顶部平齐。
9.本实用新型中,所述浮力球的底部为一平底结构,平底圆的直径大于所述排液口的直径。
10.本实用新型中,所述第二下料管的底部设置有螺纹。
11.综上所述,本申请的有益效果:本能有效防止下料过程中混入空气的助剂成品釜通过在下料口处固接第一下料管,第一下料管上设置有第一阀门,可以控制下料,第一下料管的底部固接集气管,集气管的顶部开设进液口,集气管底部开设有排液口,集气管内部设置有一浮力球,随着集气管内液体越来越多,浮力球由于受到液体浮力作用会上升,使液体可以从排液口流入第二下料管内,第二下料管通过螺旋套接在储料罐内,液体顺着第二下
料管进入储料罐内部,空气被隔绝在集气管内,在打开第一阀门进行下料前,需要先打开第二阀门,在注水管内部连续加水排出集气管以及第二下料管内的空气,再通过螺旋连接第二下料管与储料罐,本实用新型能有效的防止成品釜在下料过程中,物料内被混入空气,避免了下料时物料与空气接触造成物料的变质,有利于快速、高效、无损地进行下料。
附图说明
12.通过阅读参照以下附图所作的对非限制性实施例所作的详细描述,本申请的其它特征、目的和优点将会变得更明显:
13.图1为本能有效防止下料过程中混入空气的助剂成品釜半剖结构图;
14.图2为本能有效防止下料过程中混入空气的助剂成品釜整体结构示意图;
15.图3为本能有效防止下料过程中混入空气的助剂成品釜下料机构结构半剖图。
16.图中标号:釜体-1,下料口-2,第一下料管-3,集气管-4,进液口-5,排液口-6,进水口-7,注水管-8,密封套-9,第二下料管-10,浮力球-11,第一阀门-12,第二阀门-13,支撑柱-14;
具体实施方式
17.下面结合附图和实施例对本申请作进一步的详细说明。可以理解的是,此处所描述的具体实施例仅仅用于解释相关发明,而非对该发明的限定。另外还需要说明的是,为了便于描述,附图中仅示出了与发明相关的部分。
18.需要说明的是,在不冲突的情况下,本申请中的实施例及实施例中的特征可以相互组合。下面将参考附图并结合实施例来详细说明本申请。
19.如图1-图3所示,能有效防止下料过程中混入空气的助剂成品釜,包括釜体1、下料口2、第一下料管3、集气管4、进液口5、排液口6、进水口7、注水管8、密封套9、第二下料管10、浮力球11、第一阀门12、第二阀门13、支撑柱14,所述釜体1的底部中心处开设有所述下料口2,所述下料口2上通过焊接与所述第一下料管3顶部固接,所述第一下料管3底部通过焊接固接有所述集气管4,所述集气管4顶部中心处开设有所述进液口5,所述进液口5上通过焊接与所述第一下料管3底部固接,所述集气管4底部中心处开设有所述排液口6,所述集气管4的侧壁上开设有所述进水口7,所述进水口7通过焊接固接有所述注水管8,所述注水管8远离所述进水口7这端套设有所述密封套9,所述排液口6上通过焊接固接有所述第二下料管10,所述集气管4内部设置有所述浮力球11,所述浮力球11的底部贴紧所述排液口6,所述第一下料管3设置有所述第一阀门12,所述第二下料管10上设置有所述第二阀门13,所述釜体1的底部通过焊接设置有所述支撑柱14。所述集气管4的顶部和底部为圆弧形结构,所述集气管4的中部为一圆柱体结构。所述集气管4和釜体1同轴。所述进液口5、排液口6和下料口2同轴且直径相等。所述注水管8倾斜设置,且所述注水管8顶部与所述集气管4的顶部平齐。所述浮力球11的底部为一平底结构,平底圆的直径大于所述排液口6的直径。所述第二下料管10的底部设置有螺纹。
20.本能有效防止下料过程中混入空气的助剂成品釜通过在下料口处固接第一下料管,第一下料管上设置有第一阀门,可以控制下料,第一下料管的底部固接集气管,集气管的顶部开设进液口,集气管底部开设有排液口,集气管内部设置有一浮力球,随着集气管内
液体越来越多,浮力球由于受到液体浮力作用会上升,使液体可以从排液口流入第二下料管内,第二下料管通过螺旋套接在储料罐内,液体顺着第二下料管进入储料罐内部,空气被隔绝在集气管内,在打开第一阀门进行下料前,需要先打开第二阀门,在注水管内部连续加水排出集气管以及第二下料管内的空气,再通过螺旋连接第二下料管与储料罐,本实用新型能有效的防止成品釜在下料过程中,物料内被混入空气,避免了下料时物料与空气接触造成物料的变质,有利于快速、高效、无损地进行下料。
21.以上描述仅为本申请的较佳实施例以及对所运用技术原理等方案的说明。同时,本申请中所涉及的发明范围,并不限于上述技术特征的特定组合而成的技术方案,同时也应涵盖在不脱离所述发明构思的情况下,由上述技术特征或其等同特征进行任意组合而形成的其它技术方案。例如上述特征与本申请中公开的(但不限于)具有类似功能的技术特征进行互相替换而形成的技术方案。
技术特征:1.能有效防止下料过程中混入空气的助剂成品釜,包括釜体(1)、下料口(2)、第一下料管(3)、集气管(4)、进液口(5)、排液口(6)、进水口(7)、注水管(8)、密封套(9)、第二下料管(10)、浮力球(11)、第一阀门(12)、第二阀门(13)、支撑柱(14),其特征是:所述釜体(1)的底部中心处开设有所述下料口(2),所述下料口(2)上通过焊接与所述第一下料管(3)顶部固接,所述第一下料管(3)底部通过焊接固接有所述集气管(4),所述集气管(4)顶部中心处开设有所述进液口(5),所述进液口(5)上通过焊接与所述第一下料管(3)底部固接,所述集气管(4)底部中心处开设有所述排液口(6),所述集气管(4)的侧壁上开设有所述进水口(7),所述进水口(7)通过焊接固接有所述注水管(8),所述注水管(8)远离所述进水口(7)这端套设有所述密封套(9),所述排液口(6)上通过焊接固接有所述第二下料管(10),所述集气管(4)内部设置有所述浮力球(11),所述浮力球(11)的底部贴紧所述排液口(6),所述第一下料管(3)设置有所述第一阀门(12),所述第二下料管(10)上设置有所述第二阀门(13),所述釜体(1)的底部通过焊接设置有所述支撑柱(14)。2.根据权利要求1所述的能有效防止下料过程中混入空气的助剂成品釜,其特征是:所述集气管(4)的顶部和底部为圆弧形结构,所述集气管(4)的中部为一圆柱体结构。3.根据权利要求1所述的能有效防止下料过程中混入空气的助剂成品釜,其特征是:所述集气管(4)和釜体(1)同轴。4.根据权利要求1所述的能有效防止下料过程中混入空气的助剂成品釜,其特征是:所述进液口(5)、排液口(6)和下料口(2)同轴且直径相等。5.根据权利要求1所述的能有效防止下料过程中混入空气的助剂成品釜,其特征是:所述注水管(8)倾斜设置,且所述注水管(8)顶部与所述集气管(4)的顶部平齐。6.根据权利要求1所述的能有效防止下料过程中混入空气的助剂成品釜,其特征是:所述浮力球(11)的底部为一平底结构,平底圆的直径大于所述排液口(6)的直径。7.根据权利要求1所述的能有效防止下料过程中混入空气的助剂成品釜,其特征是:所述第二下料管(10)的底部设置有螺纹。
技术总结本实用新型公开了能有效防止下料过程中混入空气的助剂成品釜,包括釜体、下料口、第一下料管、集气管、进液口、排液口、进水口、注水管、密封套、第二下料管、浮力球、第一阀门、第二阀门、支撑柱,所述釜体的底部中心处开设有所述下料口,所述下料口上通过焊接与所述第一下料管顶部固接,所述第一下料管底部通过焊接固接有所述集气管,所述集气管顶部中心处开设有所述进液口,所述注水管远离所述进水口这端套设有所述密封套。本实用新型能有效的防止成品釜在下料过程中,物料内被混入空气,避免了下料时物料与空气接触造成物料的变质,有利于快速、高效、无损地进行下料。无损地进行下料。无损地进行下料。
技术研发人员:孙成波
受保护的技术使用者:香河宝冠塑业助剂有限公司
技术研发日:2021.06.18
技术公布日:2022/1/11