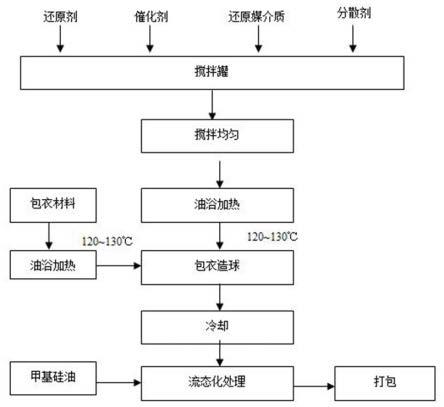
1.本发明属于废气处理技术领域,具体涉及的是一种石灰回转窑窑尾烟气脱硝用复合脱硝剂及其制备工艺。
背景技术:2.现有sncr工艺的反应温度窗口为800~1100℃,氨水作为还原剂的最佳脱硝温度为870℃,尿素作为还原剂的最佳反应温度为1000℃,当炉内温度低于800℃时,现有sncr的脱硝效率急剧下降。
3.石灰回转窑由于结构限制,安装sncr设备后,满足此反应要求的区域高度不足2米,流经此区域的烟气速度达11米/秒,能够提供反应条件的有效反应时间不足0.2秒。石灰回转窑烟气中95%的nox是以no的形式存在的,未脱硝处理前,氮氧化物浓度350-500mg/nm3,在没有催化剂条件下,反应时间0.2秒,脱硝效率低于30%。
4.因此,国内外石灰回转窑超低排放普遍采用投资运行费用高的scr工艺脱硝,而无法采用投资运行少的现有sncr设备脱硝。
技术实现要素:5.本发明的目的在于克服现有技术的缺点,解决现有sncr设备脱硝反应条件的有效反应时间不足的技术问题,提供一种石灰回转窑窑尾烟气脱硝用复合脱硝剂及其制备工艺,从而进一步实现以下目的:1、扩大原有工艺(sncr)的反应温度窗口至280℃-1100℃;2、在原有大生产工艺设备不变(含sncr工艺设备)的基础上,扩大反应区域和反应时间。反应区域从预热器溜槽扩展至窑尾除尘器前。反应区域长度从不足2米扩大至12米,反应窗口时间从不足0.2秒扩大至大于1秒;3、对复合脱硝剂进行均质化造球和流态化处理,减弱脱硝剂烧结堵输送管概率。
6.本发明通过以下技术方案予以实现:一种石灰回转窑窑尾烟气脱硝用复合脱硝剂,其成分及其重量配比为:还原剂85~90份,催化剂3~5份,还原媒介质3~5份,分散剂4~8份,包衣材料0.5份,流态化改质剂0.15份;所述还原剂为尿素或缩二胺中的一种或多种,对氮氧化物起还原作用;所述催化剂为含有fe、v、ti或者mn元素中一种或多种的、具有催化脱硝功能的钢渣,降低复合脱销剂的成本;所述还原媒介质为兰碳粉;还原媒介质使用兰碳粉替代常见脱硝剂用的烃、醇等能够提供co还原气氛的还原气氛材料,为反应提供co还原气氛,加强反应强度,降低复合脱销剂的成本;所述分散剂包括3~5份caco3和1~3份nahco3;分散剂被加热膨胀爆裂起疏散作用,粉碎搅动脱硝剂,扩大反应面积;
所述包衣材料为脲醛树脂,所述流态化改质剂为甲基硅油。
7.一种石灰回转窑窑尾烟气脱硝用复合脱硝剂的制备工艺,包括以下步骤:s1、将还原剂、催化剂、还原媒介质和分散剂按比例混合,加入搅拌罐搅拌均匀,并采用油浴方法加热至120℃~130℃;s2、将包衣材料加热至120℃~130℃,然后加入步骤s1制得的混合物料中,在搅拌罐内搅拌包裹覆膜,均质化处理成球状颗粒,冷却干燥待用;s3、将流态化改质剂加入步骤s2制得的混合物料中进行流态化处理,制得石灰回转窑窑尾烟气脱硝用复合脱硝剂。
8.进一步地,经步骤s3流态化处理后,石灰回转窑窑尾烟气脱硝用复合脱硝剂的形状为球状,粒径为mm 2~5mm。
9.与现有技术相比本发明的有益效果为:1、保证生产稳定的前提下,1000吨/天石灰回转窑生产线日喷复合脱硝剂1吨的条件下,脱硝后nox排放80-120 mg/nm3,脱硝效率达60%~80%,实现≤150mg/nm3达标排放,避免环保影响导致停产;2、本复合脱硝剂配合原有sncr工艺设备,克服原有sncr工艺的缺点,使sncr工艺在石灰回转窑烟气超低排放应用成为可能,实现了投资少,占地小,设备简单,运行维护方便;3、本复合脱硝剂自带还原气氛,不会导致so2氧化,so3浓度不增加,对设备腐蚀低,减少设备故障和事故产生;4、本复合脱硝剂配合原有sncr工艺设备,不需要对原有主体工艺烟气管道改造,烟气压力损失小,对生产影响小;5、本复合脱硝剂为干状球状颗粒,直喷法使用,安全可靠。
附图说明
10.图1为本发明复合脱硝剂制备工艺流程图。
具体实施方式
11.下面结合附图和实施例对本发明作进一步的详细描述。
12.一种石灰回转窑窑尾烟气脱硝用复合脱硝剂,其成分及其重量配比为:还原剂85kg,催化剂3kg,还原媒介质3 kg,分散剂4 kg,包衣材料0.5 kg,流态化改质剂0.15 kg;本具体实施方式中:所述还原剂为尿素;所述催化剂为含有fe、v、ti或者mn元素中一种或多种的、具有催化脱硝功能的钢渣;所述还原媒介质为兰碳粉;所述分散剂包括3 kg caco3和1 kg nahco3;所述包衣材料为脲醛树脂;所述流态化改质剂为甲基硅油。
13.如图1所示的一种石灰回转窑窑尾烟气脱硝用复合脱硝剂的制备工艺,包括以下
步骤:s1、原料准备:将还原剂、催化剂、还原媒介质和分散剂按比例混合,加入搅拌罐搅拌均匀,并采用油浴方法加热至120℃;s2、将包衣材料加热至120℃,然后加入步骤s1制得的混合物料中,在搅拌罐内搅拌包裹覆膜,均质化处理成球状颗粒,冷却干燥待用;s3、将流态化改质剂加入步骤s2制得的混合物料中进行流态化处理,制得石灰回转窑窑尾烟气脱硝用复合脱硝剂,形状为球状,粒径为2mm~5mm。
14.制得的复合脱硝剂的使用过程包括以下步骤:(1)、通过人工上料将复合脱硝剂储存于料仓;(2)、料仓通过计量器、分配器,以空气作载气,罗茨风机作为动力源,通过气力输送设备,将复合脱硝剂喷入反应区域,与烟气中的nox反应;(3)、风量风压要求:风流量:不小于8m3/min,风压力:不小于50kpa;从预热器溜槽喷出的复合脱硝剂与逆流而来的高温烟气反应,实现脱硝固硫;(4)、反应后物质通过通道气流过程包裹携带,以除尘灰形式统一收集。
15.使用本具体实施方式制备的符合脱硝剂稳定运行后,氮氧化物均值为80-120 mg/nm3。
16.以上所述,仅为本发明的具体实施方式,但本发明的保护范围并不局限于此,任何熟悉技术领域的技术人员在本发明揭露的技术范围内,可轻易想到的变化或替换,都应涵盖在本发明的保护范围之内。因此,本发明的保护范围应以所述权利要求的保护范围为准。
技术特征:1.一种石灰回转窑窑尾烟气脱硝用复合脱硝剂,其特征在于:所述复合脱硝剂的成分及其重量配比为:还原剂85~90份,催化剂3~5份,还原媒介质3~5份,分散剂4~8份,包衣材料0.5份,流态化改质剂0.15份;所述还原剂为尿素或缩二胺中的一种或多种;所述催化剂为含有fe、v、ti或者mn元素中一种或多种的、具有催化脱硝功能的钢渣;所述还原媒介质为兰碳粉;所述分散剂包括3~5份caco3和1~3份nahco3;所述包衣材料为脲醛树脂,所述流态化改质剂为甲基硅油。2.一种如权利要求1所述石灰回转窑窑尾烟气脱硝用复合脱硝剂的制备工艺,其特征在于,包括以下步骤:s1、将还原剂、催化剂、还原媒介质和分散剂按比例混合,加入搅拌罐搅拌均匀,并采用油浴方法加热至120℃~130℃;s2、将包衣材料加热至120℃~130℃,然后加入步骤s1制得的混合物料中,在搅拌罐内搅拌包裹覆膜,均质化处理成球状颗粒,冷却干燥待用;s3、将流态化改质剂加入步骤s2制得的混合物料中进行流态化处理,制得石灰回转窑窑尾烟气脱硝用复合脱硝剂。3.根据权利要求2所述的一种石灰回转窑窑尾烟气脱硝用复合脱硝剂的制备工艺,其特征在于:经步骤s3流态化处理后,石灰回转窑窑尾烟气脱硝用复合脱硝剂的形状为球状,粒径为2mm~5mm。
技术总结一种石灰回转窑窑尾烟气脱硝用复合脱硝剂及其制备工艺,属于废气处理技术领域,解决现有SNCR设备脱硝反应条件的有效反应时间不足的技术问题,复合脱硝剂的成分及其重量配比为:还原剂85~90份,催化剂3~5份,还原媒介质3~5份,分散剂4~8份,包衣材料0.5份,流态化改质剂0.15份;经均质化包衣造球和流态化处理后,制得石灰回转窑窑尾烟气脱硝用复合脱硝剂。本发明提供的复合脱硝剂能够在现有SNCR设备上使用,使SNCR设备在石灰回转窑烟气超低排放应用成为可能,在1kg/吨灰使用量条件下,脱硝后NOx排放80-120 mg/Nm3,脱硝效率达60%~80%,实现≤150mg/Nm3达标排放。达标排放。达标排放。
技术研发人员:蔡书云 王世杰 赵子华 马长禄
受保护的技术使用者:太原钢铁(集团)有限公司
技术研发日:2022.08.12
技术公布日:2022/12/1