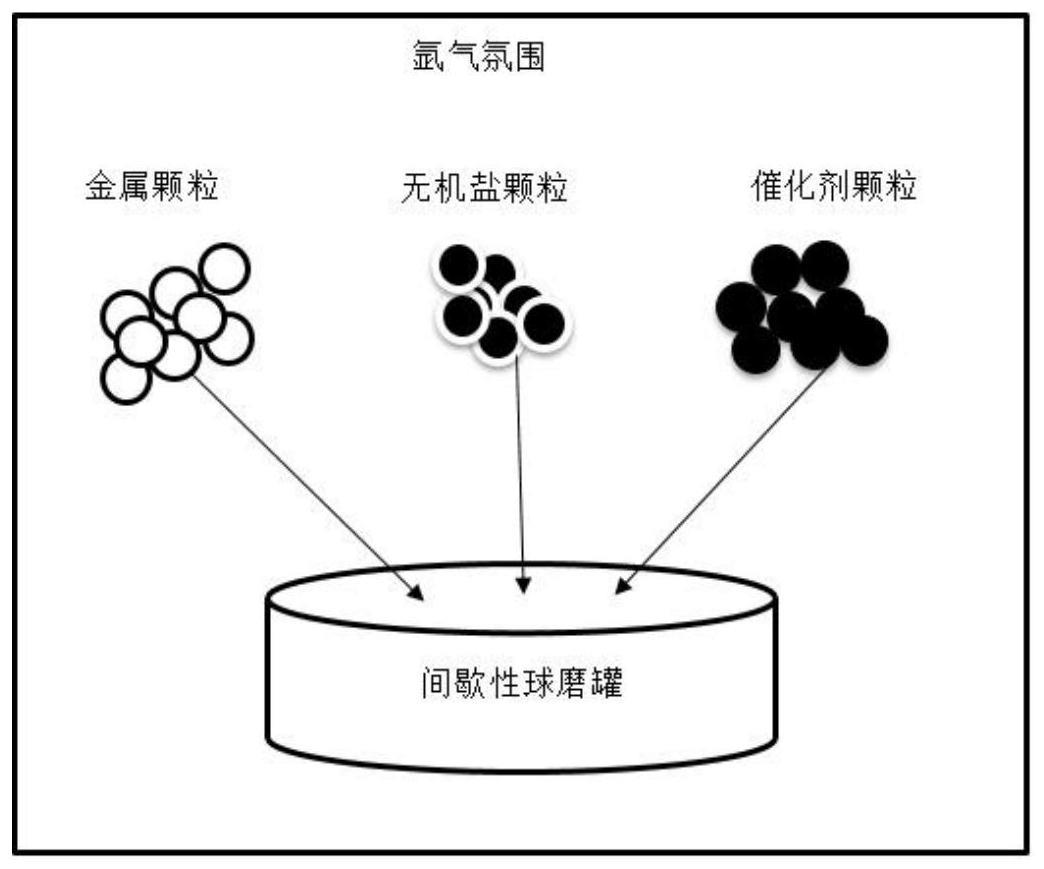
本发明属于属于甲醇重整制氢,具体涉及一种基于激光烧结制备多孔反应载体板的方法及其应用。
背景技术:
1、甲醇水蒸气重整制氢作为分布式制氢的主要实现方式,有温和的反应温度(200-300℃)、较少的杂质产(除h2外,仅含co2和少量co、ch4等)和较高的产氢率等诸多优点,是将氢能由实验研究转向产业化应用最具可行性的的途径之一。甲醇重整制氢微反应系统一般由供材单元、汽化蒸发单元、重整反应单元以及富氢气体后处理单元等多个模块组成。重整反应单元是微反应系统的核心,甲醇和水的混合溶液通过汽化蒸发单元形成的高温蒸汽在此单元进行重整反应产生富氢气体,该单元通常由具有微通道结构的催化剂载体、催化层和供热模块三部分组分。其中,具有微通道结构的催化剂载体为催化剂提供负载区域及支撑,为重整反应提供丰富的反应界面,可增强反应区域与外界的热量交换,提高物质的传输性能,被喻为重整反应的“骨骼”。催化层则是整个重整反应单元的核心,起到降低反应活化能、优化反应路径、提高h2选择性、降低co含量等重要作用,可称为重整反应的“灵魂”。
2、催化剂载体的微通道类型按照其空间形态可以分为二维和三维两类。二维结构微通道是在催化剂载体的表面加工出各种不同截面形状的平面化微槽;三维结构微通道是具有空间维度的立体式结构微通道,相较于二维结构微通道,三维结构微通道有着更强的传热传质性能,更高的催化剂负载面积和更长的反应停留时间,目前三维结构微通道催化剂载体的制造工艺主要是发泡工艺、烧结炉烧结等工艺,其对应主要多孔金属如:金属泡沫材料、金属烧结粉末材料、金属纤维材料等。现有的三维微通道结构都存在微通道分布随机性大、几何结构难以定向设计,系统压降较大等问题;且作为催化主体的催化剂需要经历浸渍、烘干等流程才能负载到三维微通道结构上进行制氢反应,使得整个制氢流程进行缓慢、效率低。为了提高催化剂催化作用、制氢效率、简化催化流程,应用中需要一种催化效果更好、效率更高、操作更简便的载体板制造方法。
技术实现思路
1、本发明的目的在于克服现有技术存在的缺陷,针对现有三维催化剂载体存在的机构结构无序且难以定向设计的特点以及传统制氢催化剂负载(金属泡沫载体板制造、催化剂溶液浸渍、烘干)存在效率低、催化剂负载强度低的问题,提供一种基于激光烧结制备甲醇重整制氢多孔催化反应板的方法,通过将催化剂与多孔载体直接烧结成多孔结构,并根据传质传热规律进行选区结构设计,提高催化剂利用率,省略催化剂负载流程,提高制氢效率。
2、为了实现以上目的,本发明的技术方案之一为:一种基于激光烧结制备多孔反应载体板的方法,具体包括如下步骤:
3、(1)将至少一组钯系催化剂颗粒与al粉末颗粒、水溶性无机盐颗粒按照体积比1-3:1-3:1-3进行混料,制得混合均匀的复合粉末;
4、(2)将步骤(1)制得的复合粉末铺在基板特定区域得到预制粉末层,然后进行激光烧结得到实体结构;
5、(3)将经过步骤(2)烧结得到的实体结构静置冷却,随后进行超声振动处理;
6、(4)将经步骤(3)处理的实体结构进行水浴处理,以去除造孔剂及粘结不牢的粉末颗粒并烘干得到多孔反应载体板。
7、在本发明一优选实施方案中,所述步骤(1)中的钯系催化剂、al粉末颗粒和水溶性无机盐颗粒的粒径为50-200um。
8、在本发明一优选实施方案中,所述步骤(1)中通改变水溶性无机盐颗粒体积占比来调控孔隙率,孔隙率与水溶性无机盐颗粒体积占比相同。
9、在本发明一优选实施方案中,所述步骤(1)中通过改变水溶性无机盐颗粒粒径来调控孔隙尺寸,孔隙尺寸与水溶性无机盐颗粒粒径相同。
10、在本发明一优选实施方案中,所述步骤(2)中的激光烧结工艺为激光功率20-80w、扫描速度10-30mm/s、频率50-70khz。
11、在本发明一优选实施方案中,所述步骤(2)中的复合粉末铺在基板特定区域得到预制粉末层,具体可以是一组复合粉末在基板特定区域同一位置铺设单层或多层或在不同位置铺设单层或多层,也可以是多组复合粉末在同一位置叠加多层或不同位置铺设单层或叠加多层。
12、在本发明一优选实施方案中,所述步骤(2)中的基板特定区域是设在基板上的甲醇水溶液的扩散区。
13、进一步的,所述甲醇水溶液的扩散区两端外侧分别设有入口和出口,扩散区近入口处区域铺设的复合粉末粒径比近出口处区域的粒径要大。
14、在入口处甲醇水溶液浓度最大,随着反应进行,甲醇水向出口扩散但浓度降低,需要更多的催化剂使其反应充分提高反应效率。
15、甲醇水扩散区是在基板上经过铣削加工出来的一个凹槽,通过基板叠加形成的,甲醇水通过蒸发后从入口进入,在入口出口压力差的作用下向出口开始扩散。
16、钯系催化剂不易溶于水;铝金属颗粒熔点约为660℃;无机盐颗粒熔点约为800℃,易溶于水。
17、为了实现以上目的,本发明的技术方案之二为:一种基于激光烧结制备多孔反应载体板的方法制得的多孔催化反应板。
18、为了实现以上目的,本发明的技术方案之三为:一种多孔反应载体板在甲醇重整制氢微反应器中的应用。
19、在本发明一优选实施方案中,所述应用是将多孔反应载体板装入甲醇重整制氢微反应器进行制氢。
20、与现有技术相比,本发明的有益效果在于:
21、1、本发明将催化剂直接制成多孔反应载体板,集催化剂、多孔结构、反应板为一体,减去了催化剂负载流程,使得制氢过程更为简便;
22、2、本发明制备的多孔反应载体板主要为催化剂本身,催化剂含量高,催化作用显著,能有效提高反应的效率;
23、3、本发明制备的多孔反应载体板的大小可以根据铺粉面积、铺粉层数自定义;
24、4、本发明制备的多孔反应载体板,本身是具有多孔结构的,且多孔结构的孔隙大小、孔隙数量和孔隙位置可以根据控制粉末径粒大小、粉末配比、铺粉位置和铺粉方式定制,能进一步提高催化剂利用率,降低成本。
技术特征:1.一种基于激光烧结制备多孔反应载体板的方法,其特征在于,包括如下步骤:
2.如权利要求1所述的制备多孔反应载体板的方法,其特征在于,所述步骤(1)中的钯系催化剂、al粉末颗粒颗粒和无机盐颗粒的粒径为50-200um。
3.如权利要求1所述的制备多孔反应载体板的方法,其特征在于,所述步骤(1)中通过改变水溶性无机盐颗粒体积占比来调控孔隙率,孔隙率与水溶性无机盐颗粒体积占比相同。
4.如权利要求1所述的制备多孔反应载体板的方法,其特征在于,所述步骤(1)中通过改变水溶性无机盐颗粒粒径来调控孔隙尺寸,孔隙尺寸与水溶性无机盐颗粒粒径相同。
5.如权利要求1所述的制备多孔反应载体板的方法,其特征在于,所述步骤(2)中的激光烧结工艺为激光功率20-80w、扫描速度10-30mm/s、频率50-70khz。
6.如权利要求1所述的制备多孔反应载体板的方法,其特征在于,所述步骤(2)中的复合粉末铺在基板特定区域得到预制粉末层,为一组复合粉末在同一位置铺设单层或多层或在不同位置铺设单层或多层,或多组复合粉末在同一位置叠加多层或不同位置铺设单层或叠加多层。
7.如权利要求1所述的制备多孔反应载体板的方法,其特征在于,所述步骤(2)中的基板特定区域为设在基板上的甲醇水溶液的扩散区。
8.如权利要求7所述的制备多孔反应载体板的方法,其特征在于,所述甲醇水溶液的扩散区两端外侧分别设有入口和出口,扩散区近入口处区域铺设的复合粉末粒径比近出口处区域的粒径要大。
9.一种多孔反应载体板由权利要求1-8任一项所述的制备多孔反应载体板的方法制得。
10.一种如权利要求9所述的多孔反应载体板在甲醇重整制氢微反应器中的应用。
技术总结本发明公开了一种基于激光烧结制备多孔反应载体板的方法及其应用,制备方法包括如下步骤:(1)将至少一组钯系催化剂颗粒与Al粉末颗粒、水溶性无机盐颗粒按照体积比1‑3:1‑3:1‑3进行混料,制得混合均匀的复合粉末;(2)将复合粉末铺在基板特定区域得到预制粉末层,然后进行激光烧结得到实体结构;(3)实体结构静置冷却,随后进行超声振动处理;(4)将实体结构进行水浴处理去除造孔剂及粘结不牢的粉末颗粒并烘干得到多孔反应载体板。本发明通过将催化剂与多孔载体直接烧结成多孔结构,并根据传质传热规律进行选区结构设计,提高催化剂利用率,省略催化剂负载流程,提高制氢效率。
技术研发人员:褚旭阳,陈智全,周可升,周姝判,林伟铭,夏虎,周伟
受保护的技术使用者:厦门大学
技术研发日:技术公布日:2024/1/13