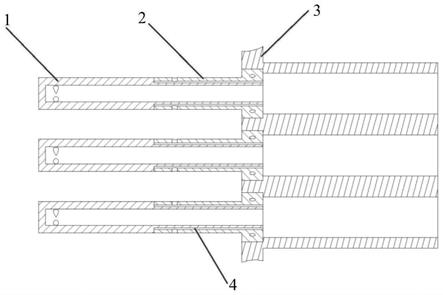
1.本发明涉及一种预燃室隔板喷嘴结构,属于液体火箭发动机领域。
背景技术:2.在早期的液体火箭发动机设计过程中,高频燃烧稳定性问题一般是推力室需要面对的重要问题,而预燃室面对的主要是低频燃烧稳定性问题。但随着航天活动规模的不断扩大,液体火箭发动机的推力不断提高,这使得预燃室的结构尺寸、流量、压力也随之提高,预燃室在设计过程中也需要面对高频燃烧稳定性问题。同时,在保证燃烧稳定的基础上,预燃室还需要保证燃烧的高效、出口燃气的温度均匀。
3.隔板能改变燃烧室内的声学特性,作为抑制高频不稳定燃烧的重要手段,在液体火箭发动机中应用广泛。目前,国内外预燃室中的隔板一般只流通作为冷却剂的燃料,同时喷注氧化剂和燃料的隔板尚未见到在预燃室中应用。
技术实现要素:4.本发明要解决的技术问题是:克服现有技术的不足,提供一种预燃室隔板喷嘴结构,通过隔板喷嘴结构的合理设计,有效抑制不稳定燃烧的发生,同时保证高燃烧效率和良好的出口燃气温度均匀性。
5.本发明所采用的技术方案是:一种预燃室隔板喷嘴,包括氧化剂喷嘴、燃料喷嘴、一底;
6.氧化剂喷嘴一端伸入燃料喷嘴中,与燃料喷嘴之间构成环形间隙;所述的隔板套筒在面板上面沿圆周方向均布若干列;所述的面板和隔板套筒一体成型构成一底;一底上在设置有隔板套筒的位置处安装燃料喷嘴;隔板套筒上设置沿纵向的隔板通孔,隔板通孔与燃料喷嘴一一对应并相互导通;燃料喷嘴安装在一底的一端端头设置旋流孔,旋流孔将端头的两个端面连通,燃料喷嘴与氧化剂喷嘴连接的一端设置径向孔。
7.所述的一底采用铜合金材料。
8.所述的隔板套筒的宽度l1与相邻隔板通孔中心间的距离l2相等。
9.所述的隔板套筒两端的圆弧半径r为相邻隔板通孔中心间的距离l2的一半。
10.所述的燃料喷嘴上面的径向孔的总面积为环形间隙的面积的1.5~3倍。
11.所述的径向孔至少为一排,每排径向孔均匀分布。
12.所述的旋流孔的轴线与燃料喷嘴轴线的夹角α为15
°
~35
°
。
13.旋流孔的入口倒圆角的半径为0.1~0.2;旋流孔沿圆周均匀分布3~6个。
14.所述的旋流孔的总面积为径向孔的总面积的1~2.5倍。
15.所述的隔板套筒在面板上面沿圆周方向均布三列。
16.氧化剂经氧化剂喷嘴喷入到隔板通孔中;燃料分为两路,一路经燃料喷嘴上面的径向孔进入到环形间隙中,然后喷入到隔板通孔中,与氧化剂掺混燃烧形成燃气;另一路经燃料喷嘴上面的旋流孔直接进入隔板通孔中,形成冷却气膜,用于冷却隔板套筒;冷却气膜
和燃气经隔板通孔的出口直接喷入到燃烧室,二者在燃烧室内掺混,形成温度均匀的燃气。
17.本发明与现有技术相比的优点在于:
18.(1)本发明的隔板喷嘴沿燃烧室周向均布三列构成三径隔板形式,用于抑制切向不稳定燃烧,拓宽预燃室的稳定工作范围。
19.(2)本发明的隔板套筒和面板一体成型构成一底,一底采用铜合金,在保证隔板喷嘴具备良好冷却特性的前提下,避免了焊接结构,增强了隔板喷嘴的结构可靠性。
20.(3)本发明将隔板喷嘴中的燃料分为两路,一路与来自氧化剂喷嘴的氧化剂快速掺混,形成高混合比混合物,保证燃烧效率;一路形成冷却气膜,对隔板套筒进行冷却,然后喷入燃烧室与隔板通孔中心处的高温燃气快速掺混,保证预燃室出口燃气的温度均匀性。
附图说明
21.图1为隔板喷嘴示意图;
22.图2为一底示意图;
23.图3为隔板套筒尺寸标注图;
24.图4为燃料喷嘴示意图;
25.图5为燃料喷嘴剖视图。
具体实施方式
26.结合附图对本发明进行说明。
27.如图1~5所示,本发明的一种预燃室隔板喷嘴主要由氧化剂喷嘴1、燃料喷嘴2、一底3组成。其中,氧化剂喷嘴1一端伸入燃料喷嘴2中,与燃料喷嘴2之间构成环形间隙4。
28.所述的隔板套筒6在面板5上面沿圆周方向均布3列。所述的面板5和隔板套筒6一体成型构成一底3。一底3上在设置有隔板套筒6的位置处安装燃料喷嘴2;
29.所述的一底3采用铜合金材料。
30.所述的隔板套筒6的宽度l1与相邻隔板通孔7中心间的距离l2相等。
31.所述的隔板套筒6两端的圆弧半径r为相邻隔板通孔7中心间的距离l2的一半。
32.燃料喷嘴2安装在一底3的一端端头设置旋流孔9,旋流孔9将端头的两个端面连通,燃料喷嘴2与氧化剂喷嘴1连接的一端设置径向孔8;所述的燃料喷嘴2上面的径向孔8的总面积为环形间隙4的面积的1.5~3倍。
33.所述的径向孔8可以多排均匀分布。
34.所述的旋流孔9的轴线与燃料喷嘴2轴线的夹角α为15
°
~35
°
。
35.所述的旋流孔9的入口倒圆角的半径为0.1~0.2。
36.所述的旋流孔9沿圆周均匀分布3~6个。
37.所述的旋流孔9的总面积为径向孔8的总面积的1~2.5倍。
38.隔板喷嘴工作过程如下:
39.氧化剂经氧化剂喷嘴1喷入到隔板通孔7中。燃料分为两路,一路经燃料喷嘴2上面的径向孔8进入到环形间隙4中,然后喷入到隔板通孔7中,与氧化剂快速掺混燃烧形成高温燃气;另一路经燃料喷嘴2上面的旋流孔9直接进入隔板通孔7中,形成冷却气膜,用于冷却隔板套筒6。冷却气膜和高温燃气经隔板通孔7的出口直接喷入到燃烧室,二者在燃烧室内
快速掺混,形成温度均匀的燃气。
40.隔板喷嘴沿燃烧室周向均布三列构成三径隔板形式,用于抑制切向不稳定燃烧,拓宽预燃室的稳定工作范围。隔板套筒6和面板5一体成型构成一底3,避免了焊接结构,增强了隔板喷嘴的结构可靠性,同时一底3采用铜合金,使得隔板喷嘴具有良好的冷却特性。燃料喷嘴2将流经的燃料分为两路,一路由径向孔进入环形间隙后喷入到隔板通孔,与来自氧化剂喷嘴1的氧化剂形成高混合比混合物后快速燃烧,保证了较高的燃烧效率;一路由旋流孔进入到隔板通孔7后形成气膜,对隔板套筒6进行冷却,然后喷入到燃烧室内与隔板通孔中心处的高温燃气快速掺混均匀,形成均匀燃气。在上述隔板喷嘴的方案下,一方面既拓宽了预燃室的稳定工作范围,另一方面又保证了氧化剂与燃料间的高效燃烧以及预燃室出口燃气的温度均匀性。
41.本发明未详细说明部分属于本领域技术人员公知技术。
技术特征:1.一种预燃室隔板喷嘴,其特征在于,包括氧化剂喷嘴(1)、燃料喷嘴(2)、一底(3);氧化剂喷嘴(1)一端伸入燃料喷嘴(2)中,与燃料喷嘴(2)之间构成环形间隙(4);所述的隔板套筒(6)在面板(5)上面沿圆周方向均布若干列;所述的面板(5)和隔板套筒(6)一体成型构成一底(3);一底(3)上在设置有隔板套筒(6)的位置处安装燃料喷嘴(2);隔板套筒(6)上设置沿纵向的隔板通孔(7),隔板通孔(7)与燃料喷嘴(2)一一对应并相互导通;燃料喷嘴(2)安装在一底(3)的一端端头设置旋流孔(9),旋流孔(9)将端头的两个端面连通,燃料喷嘴(2)与氧化剂喷嘴(1)连接的一端设置径向孔(8)。2.根据权利要求1所述的一种预燃室隔板喷嘴,其特征在于,所述的一底(3)采用铜合金材料。3.根据权利要求1或2所述的一种预燃室隔板喷嘴,其特征在于,所述的隔板套筒(6)的宽度l1与相邻隔板通孔(7)中心间的距离l2相等。4.根据权利要求3所述的一种预燃室隔板喷嘴,其特征在于,所述的隔板套筒(6)两端的圆弧半径r为相邻隔板通孔(7)中心间的距离l2的一半。5.根据权利要求4所述的一种预燃室隔板喷嘴,其特征在于,所述的燃料喷嘴(2)上面的径向孔(8)的总面积为环形间隙(4)的面积的1.5~3倍。6.根据权利要求5所述的一种预燃室隔板喷嘴,其特征在于,所述的径向孔(8)至少为一排,每排径向孔(8)均匀分布。7.根据权利要求6所述的一种预燃室隔板喷嘴,其特征在于,所述的旋流孔(9)的轴线与燃料喷嘴(2)轴线的夹角α为15
°
~35
°
。8.根据权利要求7所述的一种预燃室隔板喷嘴,其特征在于,旋流孔(9)的入口倒圆角的半径为0.1~0.2;旋流孔(9)沿圆周均匀分布3~6个;所述的旋流孔(9)的总面积为径向孔(8)的总面积的1~2.5倍。9.根据权利要求8所述的一种预燃室隔板喷嘴,其特征在于,所述的隔板套筒(6)在面板(5)上面沿圆周方向均布三列。10.根据权利要求9所述的一种预燃室隔板喷嘴,其特征在于,氧化剂经氧化剂喷嘴(1)喷入到隔板通孔(7)中;燃料分为两路,一路经燃料喷嘴(2)上面的径向孔(8)进入到环形间隙(4)中,然后喷入到隔板通孔(7)中,与氧化剂掺混燃烧形成燃气;另一路经燃料喷嘴(2)上面的旋流孔(9)直接进入隔板通孔(7)中,形成冷却气膜,用于冷却隔板套筒(6);冷却气膜和燃气经隔板通孔(7)的出口直接喷入到燃烧室,二者在燃烧室内掺混,形成温度均匀的燃气。
技术总结一种预燃室隔板喷嘴,包括氧化剂喷嘴、燃料喷嘴、一底;氧化剂喷嘴一端伸入燃料喷嘴中,与燃料喷嘴之间构成环形间隙;隔板套筒在面板上面沿圆周方向均布若干列;面板和隔板套筒一体成型构成一底;一底上在设置有隔板套筒的位置处安装燃料喷嘴;隔板套筒上设置沿纵向的隔板通孔,隔板通孔与燃料喷嘴一一对应并相互导通;燃料喷嘴安装在一底的一端端头设置旋流孔,旋流孔将端头的两个端面连通,燃料喷嘴与氧化剂喷嘴连接的一端设置径向孔。本发明通过隔板喷嘴结构的合理设计,有效抑制不稳定燃烧的发生,同时保证高燃烧效率和良好的出口燃气温度均匀性。温度均匀性。温度均匀性。
技术研发人员:潘刚 牛旭东 刘倩 张晋博 石珊珊 潘亮 韩长霖 孔维鹏 郭洪坤 刘红珍 张亚 郑孟伟 孙纪国
受保护的技术使用者:北京航天动力研究所
技术研发日:2021.11.16
技术公布日:2022/3/11