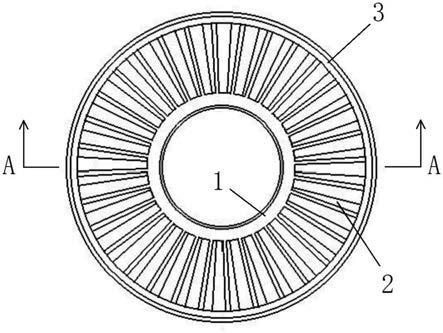
1.本实用新型涉及分子泵技术领域,具体涉及一种分子泵涡轮叶片。
背景技术:2.分子泵一方面朝着智能化方向发展,另一方面对泵体自身的结构优化、成本降低也是重要的环节。分子泵的涡轮叶片的外环连接有隔离环,目前分子泵的涡轮叶片和隔离环分别为两个独立的零件,需要独立生产加工,然后采用焊接连接为一体。其中,涡轮叶片和隔离环均是采用数控加工中心的机械进行加工制造的。其制造成本较为昂贵,消耗工时较长。
技术实现要素:3.因此,本实用新型要解决的技术问题在于克服现有技术中的分子泵涡轮叶片的制作成本较高,消耗工时较长的缺陷,从而提供一种分子泵涡轮叶片。
4.为了解决上述技术问题,本实用新型提供一种分子泵涡轮叶片,包括:内环、叶齿和外环,所述叶齿具有多个,多个所述叶齿的根部均匀连接在所述内环的外壁上,多个所述叶齿的尖部均匀连接在所述外环的内壁上;
5.所述内环、多个所述叶齿和所述外环为一体成型结构。
6.可选地,所述内环、多个所述叶齿和所述外环为通过铸造一体成型。
7.可选地,所述外环的宽度大于所述叶齿和所述内环的宽度。
8.可选地,所述外环上设有用于定位安装的定位台阶。
9.可选地,所述叶齿沿所述内环至所述外环的方向为变角度设计。
10.可选地,所述叶齿垂直于所述内环的切线。
11.可选地,所述叶齿具有前缘和后缘,所述前缘的厚度小于所述后缘的厚度。
12.本实用新型技术方案,具有如下优点:
13.1.本实用新型提供的分子泵涡轮叶片,将叶齿、内环和外环设计为一体结构,避免了后期的焊接工序,节约了涡轮叶片的制造时间,从而可降低生产成本。
14.2.本实用新型提供的分子泵涡轮叶片,采用铸造的方式使叶齿、内环和外环一体成型,相比于现有的机加工生产,其制作成本更低,从而进一步的降低了涡轮叶片的生产成本。
15.3.本实用新型提供的分子泵涡轮叶片,在外环上设计有定位台阶,通过该定位台阶用于便于涡轮叶片的整体安装,将涡轮叶片安装到设备上后,可防止其在径向方向的窜动。
16.4.本实用新型提供的分子泵涡轮叶片,由于叶齿是从内环朝向外环辐射出去的,因此设计叶齿为扭曲的变角度,可使叶齿之间的间隙分布均匀,以保证气体流通的顺畅性。
附图说明
17.为了更清楚地说明本实用新型具体实施方式或现有技术中的技术方案,下面将对具体实施方式或现有技术描述中所需要使用的附图作简单地介绍,显而易见地,下面描述中的附图是本实用新型的一些实施方式,对于本领域普通技术人员来讲,在不付出创造性劳动的前提下,还可以根据这些附图获得其他的附图。
18.图1为本实用新型的实施例的分子泵涡轮叶片的一种实施方式的俯视图。
19.图2为图1中沿a
‑
a线的剖视图。
20.图3为本实用新型的实施例的分子泵涡轮叶片的制造示意图。
21.图4为本实用新型的实施例的分子泵涡轮叶片的叶齿横截面的示意图。
22.附图标记说明:
23.1、内环;2、叶齿;3、外环;4、定位台阶;5、定模;6、动模。
具体实施方式
24.下面将结合附图对本实用新型的技术方案进行清楚、完整地描述,显然,所描述的实施例是本实用新型一部分实施例,而不是全部的实施例。基于本实用新型中的实施例,本领域普通技术人员在没有做出创造性劳动前提下所获得的所有其他实施例,都属于本实用新型保护的范围。
25.在本实用新型的描述中,需要说明的是,术语“中心”、“上”、“下”、“左”、“右”、“竖直”、“水平”、“内”、“外”等指示的方位或位置关系为基于附图所示的方位或位置关系,仅是为了便于描述本实用新型和简化描述,而不是指示或暗示所指的装置或元件必须具有特定的方位、以特定的方位构造和操作,因此不能理解为对本实用新型的限制。此外,术语“第一”、“第二”、“第三”仅用于描述目的,而不能理解为指示或暗示相对重要性。
26.在本实用新型的描述中,需要说明的是,除非另有明确的规定和限定,术语“安装”、“相连”、“连接”应做广义理解,例如,可以是固定连接,也可以是可拆卸连接,或一体地连接;可以是机械连接,也可以是电连接;可以是直接相连,也可以通过中间媒介间接相连,可以是两个元件内部的连通。对于本领域的普通技术人员而言,可以具体情况理解上述术语在本实用新型中的具体含义。
27.此外,下面所描述的本实用新型不同实施方式中所涉及的技术特征只要彼此之间未构成冲突就可以相互结合。
28.本实施例提供一种分子泵涡轮叶片的具体实施方式,如图1所示,包括:内环1、叶齿2和外环3,所述叶齿2具有多个,多个所述叶齿2的根部均匀连接在所述内环1的外壁上,多个所述叶齿2的尖部均匀连接在所述外环3的内壁上,且叶齿2垂直于所述内环1的切线,使叶齿2呈辐射状从内环1连接至外环3;其中,所述内环1、多个所述叶齿2和所述外环3为一体成型结构,具体地,所述内环1、多个所述叶齿2和所述外环3为通过铸造一体成型的结构。上述涡轮叶片,将叶齿2、内环1和外环3设计为一体结构,避免了后期的焊接工序,节约了涡轮叶片的制造时间,从而可降低生产成本。
29.如图1、图3所示,所述叶齿2沿所述内环1至所述外环3的方向为变角度设计,由于叶齿2是从内环1朝向外环3辐射出去的,因此设计叶齿2为扭曲的变角度,可使叶齿2之间的间隙分布均匀,以保证气体流通的顺畅性。
30.如图2所示,所述外环3的宽度大于所述叶齿2和所述内环1的宽度,在进行涡轮叶片的安装时,可通过外环3进行定位。所述外环3上设有用于定位安装的定位台阶4,通过该定位台阶4卡在设备壳体上,可防止涡轮叶片的轴向窜动。
31.如图3所示,在进行制造时,采用定模5和动模6对涡轮叶片进行整体铸造成型,所述涡轮叶片的材料采用金属,在进行浇注时采用高压浇注,以保证金属液体填充完全。
32.如图4所示,所述叶齿2具有前缘和后缘,所述前缘(图4中叶齿上端部分)的厚度小于所述后缘(图4中叶齿下端部分)的厚度。在进行抽真空时,通过叶齿2将朝向前缘方向转动,进而使空气从上向下流动。叶齿2采用上薄下厚的结构,更有利于气体的压缩,进而提升分子泵的压缩比。
33.显然,上述实施例仅仅是为清楚地说明所作的举例,而并非对实施方式的限定。对于所属领域的普通技术人员来说,在上述说明的基础上还可以做出其它不同形式的变化或变动。这里无需也无法对所有的实施方式予以穷举。而由此所引伸出的显而易见的变化或变动仍处于本实用新型的保护范围之中。
技术特征:1.分子泵涡轮叶片,其特征在于,包括:内环(1)、叶齿(2)和外环(3),所述叶齿(2)具有多个,多个所述叶齿(2)的根部均匀连接在所述内环(1)的外壁上,多个所述叶齿(2)的尖部均匀连接在所述外环(3)的内壁上;所述内环(1)、多个所述叶齿(2)和所述外环(3)为一体成型结构。2.根据权利要求1所述的分子泵涡轮叶片,其特征在于,所述内环(1)、多个所述叶齿(2)和所述外环(3)为通过铸造一体成型。3.根据权利要求1所述的分子泵涡轮叶片,其特征在于,所述外环(3)的宽度大于所述叶齿(2)和所述内环(1)的宽度。4.根据权利要求3所述的分子泵涡轮叶片,其特征在于,所述外环(3)上设有用于定位安装的定位台阶(4)。5.根据权利要求1所述的分子泵涡轮叶片,其特征在于,所述叶齿(2)沿所述内环(1)至所述外环(3)的方向为变角度设计。6.根据权利要求1所述的分子泵涡轮叶片,其特征在于,所述叶齿(2)垂直于所述内环(1)的切线。7.根据权利要求1
‑
6中任一项所述的分子泵涡轮叶片,其特征在于,所述叶齿(2)具有前缘和后缘,所述前缘的厚度小于所述后缘的厚度。
技术总结本实用新型提供一种分子泵涡轮叶片,属于分子泵技术领域,包括:内环、叶齿和外环,所述叶齿具有多个,多个所述叶齿的根部均匀连接在所述内环的外壁上,多个所述叶齿的尖部均匀连接在所述外环的内壁上;所述内环、多个所述叶齿和所述外环为一体成型结构;本实用新型的分子泵涡轮叶片,将叶齿、内环和外环设计为一体结构,避免了后期的焊接工序,节约了涡轮叶片的制造时间,从而可降低生产成本。从而可降低生产成本。从而可降低生产成本。
技术研发人员:陈林 王浩为 邓高飞
受保护的技术使用者:中科九微科技有限公司
技术研发日:2021.04.20
技术公布日:2021/12/7