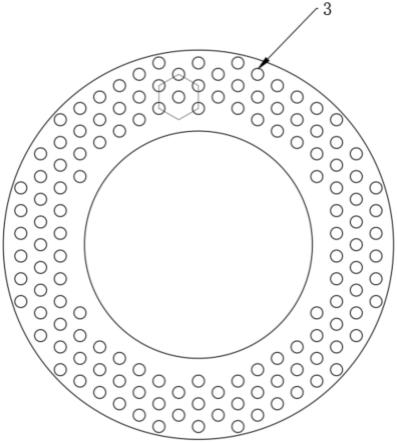
1.本实用新型涉及汽车零部件领域,尤其涉及一种刹车盘。
背景技术:2.刹车盘是车辆的必备部件,靠刹车片和刹车盘之间的摩擦力降低车辆的行驶速度,因此刹车盘工作过程中会因为摩擦产生巨大的热量,而且为了获得足够大的摩擦力,刹车片与刹车盘之间需要施加很大的压力,所以刹车盘还需要具有足够强的强度。
3.现有刹车盘一般通过设置两个背靠背的刹车面,刹车时,两个刹车片分别从相对方向施加压力到刹车盘上,对于刹车盘整体而言,刹车片施加的压力相当于对称的夹持力,以此避免刹车片的压力造成剪切力破坏刹车盘的结构。
4.两个刹车面之间一方面需要有牢固的连接结构,同时还必须设置合理的通风通道,以便尽快将摩擦产生的热量传递出去,实现方法基本是靠分散的筋条实现两个刹车面的连接,靠筋条之间的间隙作为气流通路实现热量的散逸渠道,但是现有的刹车盘筋的形状和排列一般是简单的圆周状排列,或者是放射线状排列等,在一些角度方向上通风受阻,通风不良,散热效果不佳,设置不合理还会导致刹车面结构强度低和受力不均匀的情况,在使用时两刹车面易产生贯穿性的裂纹。
技术实现要素:5.本实用新型所要解决的技术问题是:提供一种刹车盘。
6.为解决上述技术问题,本实用新型所采用的技术方案是:
7.一种刹车盘,包括刹车盘本体及两个背对设置的环形刹车面,其特征在于,两个所述环形刹车面通过设于其背面的豆筋固定连接在一起,围绕在任意一个所述豆筋周边的豆筋均在以被围绕豆筋为中心的正六边形的顶点处。
8.此处所述豆筋,是相对于连续布置的、条状的筋板而言,具体是指横截面呈圆型、椭圆形或其他团状,并呈点阵状排列的连接筋。
9.与现有技术相比,本实用新型具有如下技术效果:
10.筋条结构简单,排列方式规则稳固,在通风面上无阻挡,通风和散热效果好,能提高刹车面强度,使刹车面受力均匀。
11.在上述技术方案的基础上,本实用新型还可以做如下改进。
12.优选地,所述豆筋的直径小于相邻豆筋之间连线的长度;确保流出通风空间;
13.优选地,所述豆筋的直径为12mm-15mm;
14.优选地,相邻所述豆筋之间连线的距离为20-23mm;
15.优选地,所述豆筋沿所述环形刹车面圆周方向均分为6组,每组包括3层豆筋,最内侧还包括一层加强筋,所述加强筋的横截面为长圆形,所述长圆形加强筋长度方向的中心线的延长线经过所述环形刹车面的中心。
16.优选地,每组豆筋中位于最外侧的豆筋的边缘与所述刹车盘的外圆边之间的最小
距离大于3mm,小于5mm;
17.每组豆筋中位于最内侧的豆筋的边缘与所述刹车盘的内圆边之间的最小距离大于3mm,小于5mm。
18.优选地,所述豆筋满布所述刹车面的背面;
19.优选地,所述豆筋与所述刹车面背面交接处设有倒角。
20.采用上述进一步方案的有益效果是确保豆筋的连接强度。
附图说明
21.图1为刹车盘的基本结构;
22.图2为现有技术中豆筋的传统排列结构;
23.图3-图6为本实用新型实施例1的结构示意图;
24.图7为本实用新型实施例2的结构示意图;
25.图8为实施例1中豆筋与刹车盘外圆距离示意图;
26.图9为实施例2中加强筋与刹车盘内圆距离示意图。
27.在附图中,各标号所表示的部件名称列表如下:
28.1、刹车盘本体;2、刹车面;3、豆筋;4、刹车盘外圆;5、刹车盘内圆; d、筋与刹车盘边缘的距离;6、加强筋。
29.图3-图7中的正六边形是辅助线,用于更清晰的展现各筋点之间的位置关系。
具体实施方式
30.以下结合附图对本实用新型的原理和特征进行描述,所举实例只用于解释本实用新型,并非用于限定本实用新型的范围。
31.如图1所示是现有刹车盘1的常规结构,包括刹车盘1本体及背对背设置的两个环形刹车面2,两个环形刹车面2背面靠连接筋连接在一起。
32.请参照图2所示,其为现有的刹车盘1的结构示意图。豆筋3均布在以刹车盘1圆心为圆心的若干同心圆上,一般仅做交错布置,并无其他特殊规则限制。
33.实施例1:
34.如图3所示,一种刹车盘1,包括刹车盘1本体及两个背对设置的环形刹车面2,两个所述环形刹车面2通过设于其背面的豆筋3固定连接在一起,所述豆筋3沿所述环形刹车面2圆周方向均分为6组,如图4所示,其为其中一组的豆筋3分布细节,包括3层豆筋3,豆筋3的直径为12mm,相邻两个豆筋3 中心连线的距离为20mm,紧密围绕在任意一个豆筋3周边的豆筋3均在以被围绕豆筋3为中心的同一个正六边形的顶点处,图4、图5、图6中在不同位置分别连接绘制了示意性的正六边形,以更形象的展现相邻豆筋3之间的位置关系。
35.如图8所示,位于最外侧的豆筋的外边缘与刹车盘外圆4之间的距离,即筋与刹车盘边缘的距离d为3mm。
36.实施例2:
37.如图7所示,区别于实施例1,本例中,还包括一层加强筋6,所述加强筋 6位于三层豆筋的内侧,所述加强筋的横截面为长圆形,所述长圆形加强筋长度方向的中心线的延长线经过所述环形刹车面2的中心,加强筋远离刹车面2 中心点的一端的端部中心位于前述
正六边形的顶点处。
38.如图9所示,位于最内侧的加强筋的外边缘与刹车盘内圆5之间的距离,即筋与刹车盘边缘的距离d为5mm
39.以上所述仅为本实用新型的较佳实施例,并不用以限制本实用新型,凡在本实用新型的精神和原则之内,所作的任何修改、等同替换、改进等,均应包含在本实用新型的保护范围之内。
技术特征:1.一种刹车盘,包括刹车盘本体及两个背对设置的环形刹车面,其特征在于,两个所述环形刹车面通过设于其背面的豆筋固定连接在一起,紧邻在任意一个所述豆筋周边的豆筋均在以被围绕豆筋为中心的同一个正六边形的顶点处。2.根据权利要求1所述的刹车盘,其特征在于,所述豆筋的直径小于相邻豆筋之间连线的长度。3.根据权利要求1或2所述的刹车盘,其特征在于,所述豆筋的直径为12mm-15mm。4.根据权利要求3所述的刹车盘,其特征在于,相邻所述豆筋之间连线的距离为20-23mm。5.根据权利要求1所述的刹车盘,其特征在于,所述豆筋沿所述环形刹车面圆周方向均分为6组,每组包括至少3层豆筋。6.根据权利要求5所述的刹车盘,其特征在于,每组豆筋中位于最外侧的豆筋的边缘与所述刹车盘的外圆边之间的最小距离大于3mm,小于5mm;每组豆筋中位于最内侧的豆筋的边缘与所述刹车盘的内圆边之间的最小距离大于3mm,小于5mm。7.根据权利要求6所述的刹车盘,其特征在于,所述豆筋满布所述刹车面的背面。8.根据权利要求7所述的刹车盘,其特征在于,所述豆筋与所述刹车面背面交接处设有倒角。9.根据权利要求5所述的刹车盘,还包括加强筋,所述加强筋位于三层豆筋的内侧,所述加强筋的横截面为长圆形,所述长圆形加强筋长度方向的中心线的延长线经过所述环形刹车面的中心。
技术总结本实用新型公开了一种刹车盘,包括刹车盘本体及两个背对设置的环形刹车面,其特征在于,两个所述环形刹车面通过设于其背面的豆筋固定连接在一起,紧邻在任意一个所述豆筋周边的豆筋均在以被围绕豆筋为中心的同一个正六边形的顶点处。由此,本实用新型的刹车盘。本实用新型的刹车盘。本实用新型的刹车盘。
技术研发人员:张志英 高凤艳 秦丽丽
受保护的技术使用者:烟台宏田汽车零部件股份有限公司
技术研发日:2021.12.28
技术公布日:2023/1/3