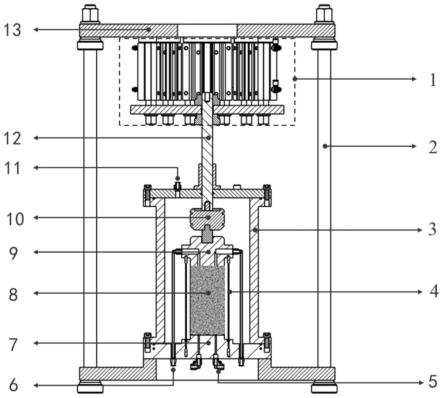
1.本发明属于岩土工程试验技术领域,涉及一种载荷保持绝对相位差的双向振动三轴仪及其使用方法。
背景技术:2.岩土工程基础和结构常遭受动态循环载荷。动态荷载可能是由于环境因素造成的,例如地震活动和波浪荷载,或人类活动造成的,例如交通荷载和机器振动。岩土基础在循环荷载作用下,无论是在变形方面,还是在强度方面,其动力特性比在静态荷载下更为复杂。
3.动三轴仪是目前测试土体动力特性最常用的仪器。按施加荷载方式不同,可分为单向动三轴仪与双向动三轴仪。单向动三轴仅对试样施加单向(轴向)循环荷载,而双向动三轴可以同时在轴向和径向施加循环荷载。双向动三轴仪能让试样处于更加贴近实际工况的应力状态,便于在真实的土体应力状态下开展研究。此外,将地震荷载对土体的作用简化为正应力保持不变,而剪应力做往复变化的动载荷工况,已成为一种共识。这种简化的载荷工况只能在双向振动三轴仪试验中获得,即采用双向激振,在轴向与径向施加同频率而相位差恒为180
°
动应力,可在试样45
°
斜面上获得法向应力恒定,剪应力往复变化的应力工况。然而,轴向与径向很难实现同频率而相位差恒为180
°
的动应力。由于动力作动器非绝对同步而造成输出存在滞后响应,以及试验仪器机电控制水平和传感器精度有限,实际输出的动应力与目标应力存在额外的相位差,特别是在高频振动荷载中尤为显著,进而很难继续模拟地震载荷对土体的影响。因此,急需一种严格控制轴、径向动荷载振幅和相位差的地震荷载双向振动模拟仪器。
技术实现要素:4.针对现有技术存在的问题,本发明提供一种载荷保持绝对相位差的双向振动三轴仪及其使用方法。
5.本发明的技术方案为:
6.1)基本原理
7.一种载荷保持绝对相位差的双向振动三轴仪,采用两个独立的压力源,如图1所示。轴向加载气缸的上端连接一个恒定压力源,活塞获得驱动力p0×
a(a是气缸活塞面积)驱动气缸活塞杆向下移动输出压力到试样上。压力控制器的输出压力同时连接压力室和轴向加载气缸的下端,分别提供径向应力p(或σ3)和活塞杆反向阻力p
×
a(忽略活塞杆面积)。试样受到活塞杆的压力为(p
0-p)
×
a。当p增加时,试样受到的压力减小;当p减小时,试样受到的压力增加;因此,试样的轴向应力(σ1)和径向应力(σ3)始终保持180
°
绝对相位差。不过,对调互换这俩压力源的接口,试样的轴向应力(σ1)和径向应力(σ3)也能始终保持0
°
绝对相位差。
8.2)仪器装置
9.一种载荷保持绝对相位差的双向振动三轴仪,包括主机架、压力室、轴向载荷气缸组1、恒压源和压力控制器,如图1所示。图2和图3分别展示了仪器装置总体图和纵向剖面图。
10.所述主机架包括主机架板13和连接上下两个主机架板13的主机架连杆2。所述压力室是一个密闭的压力室腔体3;所述压力室腔体3上安装围压输入阀11。所述试样8包裹在橡皮膜内,并放置在压力室腔体3底部的压力室底座7上,试样8上方放置试样帽9;所述压力室底座7有两个通孔,通孔一端连通试样8下方内部,另一端分别安装两个压力室底座连通阀5;所述试样帽9有两个通孔,通孔一端连通试样8上方内部,另一端分别安装两个试样帽连通阀6;所述试样帽9和压力室底座7之间固定两个直线位移传感器4,用来测量试样8的轴向压缩变形;所述试样帽9上端依次连接力传感器10和加载杆12;所述加载杆12是传递轴向载荷气缸组1的载荷到试样8;所示力传感器10是记录载荷的大小。
11.所述轴向载荷气缸组1包括一系列并排固定的气缸1e,所述气缸1e下端固定在气缸组输出板1a上,上端固定在主机架板13上(通过内六角螺钉1d固定);所述气缸1e有气缸上输入阀1b和气缸下输入阀1c;所述气缸活塞杆1f固定在气缸组输出板1a上;所述气缸组输出板1a通过螺纹与加载杆12连接传递载荷。
12.所述恒压源和压力控制器是外界的动力装置,分别连接到气缸1e上的气缸上输入阀1b和气缸下输入阀1c,为试样8提供绝对相位差的载荷;所述压力控制器同时连接到围压输入阀11,为试样8输入围压。
13.本发明的有益效果为:本发明能控制并保持绝对相位差的轴、径向动荷载振幅,模拟包括地震荷载作用下的多种应力工况。仪器结构简单,控制系统简单,能实现轴向应力和径向应力的应力式控制。在加载杆和试样截面面积相同的条件下,可开展主应力旋转、三轴伸长的双向循环荷载的三轴试验,对研究松散颗粒体(土体)材料在复杂应力工况下的变形特性具有意义。
附图说明
14.图1为绝对相位差双向振动载荷施加原理;
15.图2为仪器装置轴测图(左)和正视图(右);
16.图3为仪器装置纵向剖面图;
17.图4为气缸组组成图;
18.图5为气缸图;
19.图中:1轴向载荷气缸组;2主机架连杆;3压力室腔体;4直线位移传感器;5压力室底座连通阀;6试样帽连通阀;7压力室底座;8试样;9试样帽;10力传感器;11围压输入阀;12加载杆;13主机架板;1a气缸组输出板;1b气缸上输入阀;1c气缸下输入阀;1d内六角螺钉;1e气缸;1f气缸活塞杆。
具体实施方式
20.以下结合说明书附图对本发明做进一步阐述。
21.采用上述载荷保持绝对相位差的双向振动三轴仪开展试验,包括以下步骤:
22.第一步,根据轴向和径向压力保持0
°
相位差或180
°
相位差的试验设计,布置压力
源与气缸1e的连通形式。比如,若连接恒压源到气缸上输入阀1b,连接压力控制器到气缸下输入阀1c,气缸1e输出的轴向力与压力控制器的压力保持0
°
相位差;若对换上述两个压力的输入连接,则气缸1e输出的轴向力与压力控制器的压力保持180
°
相位差。
23.第二步,连接恒压源和压力控制器的压力到轴向载荷气缸组1,确定轴向载荷。根据不同试验设置的需要,可选择需要连通的气缸1e个数,根据连通的气缸1e个数来调整轴向输出载荷与围压的载荷比。
24.第三步,安装土试样和压力室腔体3。试样8制备过程按照试验规程即可。连接压力控制器到围压输入阀11,提供与压力控制器中压力同步的循环围压。
25.第四步,实验开始,采集各传感器的读数。需要记录的试验数据有,直线位移传感器4,力传感器10,压力控制器压力,恒定压力源提供的压力。
技术特征:1.一种载荷保持绝对相位差的双向振动三轴仪,其特征在于,包括主机架、压力室、轴向载荷气缸组(1)、恒压源和压力控制器;所述主机架包括主机架板(13)和连接上下两个主机架板(13)的主机架连杆(2);所述压力室是一个密闭的压力室腔体(3);所述压力室腔体(3)上安装围压输入阀(11);所述试样(8)包裹在橡皮膜内,并放置在压力室腔体(3)底部的压力室底座(7)上,试样(8)上方放置试样帽(9);所述压力室底座(7)有两个通孔,通孔一端连通试样(8)下方内部,另一端分别安装两个压力室底座连通阀(5);所述试样帽(9)有两个通孔,通孔一端连通试样(8)上方内部,另一端分别安装两个试样帽连通阀(6);所述试样帽(9)和压力室底座(7)之间固定两个直线位移传感器(4),用来测量试样(8)的轴向压缩变形;所述试样帽(9)上端依次连接力传感器(10)和加载杆(12);所述加载杆(12)是传递轴向载荷气缸组(1)的载荷到试样(8);所示力传感器(10)是记录载荷的大小;所述轴向载荷气缸组(1)包括一系列并排固定的气缸(1e),所述气缸(1e)下端固定在气缸组输出板(1a)上,上端固定在主机架板(13)上;所述气缸(1e)有气缸上输入阀(1b)和气缸下输入阀(1c);所述气缸活塞杆(1f)固定在气缸组输出板(1a)上;所述气缸组输出板(1a)通过螺纹与加载杆(12)连接传递载荷;所述恒压源和压力控制器是外界的动力装置,分别连接到气缸(1e)上的气缸上输入阀(1b)和气缸下输入阀(1c),为试样(8)提供绝对相位差的载荷;所述压力控制器同时连接到围压输入阀(11),为试样(8)输入围压。2.权利要求1所述的一种载荷保持绝对相位差的双向振动三轴仪的使用方法,其特征在于,包括以下步骤:第一步,根据轴向和径向压力保持0
°
相位差或180
°
相位差的试验设计,布置压力源与气缸(1e)的连通形式;若连接恒压源到气缸上输入阀(1b),连接压力控制器到气缸下输入阀(1c),气缸(1e)输出的轴向力与压力控制器的压力保持0
°
相位差;若对换上述两个压力的输入连接,则气缸(1e)输出的轴向力与压力控制器的压力保持180
°
相位差;第二步,连接恒压源和压力控制器的压力到轴向载荷气缸组(1),确定轴向载荷;根据不同试验设置的需要,可选择需要连通的气缸(1e)个数,根据连通的气缸(1e)个数来调整轴向输出载荷与围压的载荷比;第三步,安装试样(8)和压力室腔体(3);试样(8)制备过程按照试验规程即可;连接压力控制器到围压输入阀(11),提供与压力控制器中压力同步的循环围压;第四步,实验开始,采集各传感器的读数;需要记录的试验数据有,直线位移传感器(4),力传感器(10),压力控制器压力,恒定压力源提供的压力。
技术总结本发明公开了一种载荷保持绝对相位差的双向振动三轴仪及其使用方法,属于岩土工程试验技术领域。本发明能控制并保持绝对相位差的轴、径向动荷载振幅,模拟包括地震荷载作用下的多种应力工况。仪器结构简单,控制系统简单,能实现轴向应力和径向应力的应力式控制。在加载杆和试样截面面积相同的条件下,可开展主应力旋转、三轴伸长的双向循环荷载的三轴试验,对研究松散颗粒体(土体)材料在复杂应力工况下的变形特性具有意义。下的变形特性具有意义。下的变形特性具有意义。
技术研发人员:夏平心 付青青 邓文
受保护的技术使用者:常州大学
技术研发日:2022.10.10
技术公布日:2023/1/5