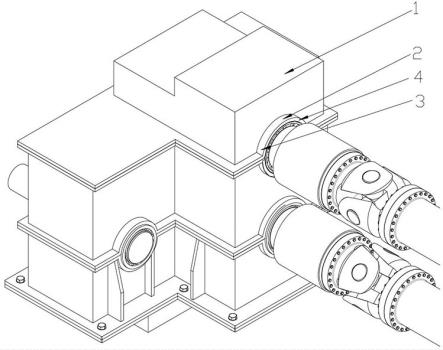
1.本发明属于冶金行业板带轧机主传动系统故障诊断技术领域,具体涉及一种高速精密带钢冷轧机主传动齿轮箱故障诊断系统。
背景技术:2.随着冶金技术的不断发展,轧机设备的精密程度和自动化水平越来越高。对于像轧机这样要求高效率重载荷的大型机械一旦运行过程中出现设备故障,不但会造成高昂的维修费用以及较长时间的被迫停产等重大的经济损失,甚至可能会导致现场人员的受伤。由此,人们希望在保证设备不停产检修的前提下,提前掌握设备的运行情况,判断出设备故障的准确位置及形成因素,从而防止设备的进一步损坏,为企业和社会带来巨大的经济效益。
3.齿轮箱作为传动系统的重要组成部件,其内部元件往往程非线性化和复杂化,再加之箱体结构种类众多,使得齿轮箱往往也存在一定的复杂映射关系,齿轮箱的故障损伤常常多发于齿轮和轴承两部分,其中齿轮的故障多表现为齿面胶合、齿面磨损以及轮齿疲劳断裂等,而齿轮箱轴承的多发故障则大多表现为轴承外圈点蚀、轴承内圈点蚀、滚动体偏心以及保持架故障等。目前对轴承类零部件的故障诊断的研究很多,依赖于其结构的标准型往往可以对轴承的常见故障做出比较准确的判断。而针对齿轮箱整体的故障诊断由于齿轮箱复杂的结构以及映射关系目前并没有一套较为成熟的方案综上所述,如何开发出一套完整的针对轧机齿轮箱故障诊断系统对其进行及时有效的在线监测并正确判断其零部件故障位置及其失效形式是目前冶金行业从业人员亟需解决的问题。
技术实现要素:4.本发明的目的是提出一种高速精密带钢冷轧机主传动齿轮箱在线故障智能诊断系统,为板带轧机主传动系统齿轮箱失效部位提供在线监测与故障诊断。
5.一种高速精密带钢冷轧机主传动齿轮箱故障诊断系统,包括:加速度传感器、多路数据采集器和处理器系统,处理器系统包括数据采集模块、数据分析模块、故障诊断模块和训练升级模块,加速度传感器连接在齿轮箱上,用于采集齿轮箱运行过程中的振动信号;多路数据采集器用于将加速度传感器采集到的振动信号汇总并提供给处理器系统;数据采集模块,用于接收多路数据采集器输送的数据,并输送给数据分析模块;数据分析模块,用于将振动信号进行分解处理为多个频段的能量组成特征向量,并提取分解后的多个频段的能量组成特征向量,并将特征向量输送至故障诊断模块;训练升级模块,用于生成故障诊断模块的故障诊断分类模型;故障诊断模块,通过故障诊断分类模型对齿轮箱各故障对应的振动信号分解的特
征向量进行分类识别,得到故障诊断结果。
6.所述加速度传感器有多个,分别连接在齿轮箱轴承座的水平方向、垂直方向、轴向以及齿轮箱箱体处。
7.所述还包括人机交互系统,用于显示处理器系统得到的故障诊断结果,并向处理器系统内输入数据。
8.所述处理器系统还包括数据存储模块,用于存储处理器系统接收和输出的数据。
9.所述训练升级模块,还在使用过程中采集的信号对故障诊断分类模型进行训练升级。
10.所述数据采集模块采样频率为2000hz,每段信号采样点数为5000。
11.本发明的有益效果在于:通过采集齿轮箱的振动信号,处理分析后通过振动信号的特征,匹配各种运行状态中齿轮箱产生的振动信号特征,来识别当前齿轮箱的工作状态,节省了人工成本,填补了轧机设备故障诊断领域的空白,检测灵敏度高,检测结果更为准确。
附图说明
12.图1为系统构架图;图2为加速度传感器布置位置示意图;图中1、机壳测点;2、轴承垂直方向测点;3、轴承水平方向测点;4、轴承轴向测点;以下将结合附图及实施例对本发明做进一步详细说明。
具体实施方式
13.【实施例1】如图1所示,一种高速精密带钢冷轧机主传动齿轮箱故障诊断系统,包括:加速度传感器、多路数据采集器和处理器系统,处理器系统包括数据采集模块、数据分析模块、故障诊断模块和训练升级模块,加速度传感器连接在齿轮箱上,用于采集齿轮箱运行过程中的振动信号;多路数据采集器用于将加速度传感器采集到的振动信号汇总并提供给处理器系统;数据采集模块,用于接收多路数据采集器输送的数据,并输送给数据分析模块;数据分析模块,用于将振动信号进行分解处理为多个频段的能量组成特征向量,并提取分解后的多个频段的能量组成特征向量,并将特征向量输送至故障诊断模块;具体的,将振动信号分解为8个频段的能量组成特征向量。
14.训练升级模块,用于生成故障诊断模块的故障诊断分类模型;故障诊断模块,通过故障诊断分类模型对齿轮箱各故障对应的振动信号分解的特征向量进行分类识别,得到故障诊断结果。
15.所述加速度传感器有多个,分别连接在齿轮箱轴承座的水平方向、垂直方向、轴向以及齿轮箱箱体处。
16.所述还包括人机交互系统,用于显示处理器系统得到的故障诊断结果,并向处理器系统内输入数据。
17.所述处理器系统还包括数据存储模块,用于存储处理器系统接收和输出的数据。
18.所述训练升级模块,还在使用过程中采集的信号对故障诊断分类模型进行训练升级。
19.所述数据采集模块采样频率为2000hz,每段信号采样点数为5000,即每采集5000个采样点为一段信号。
20.如图2所示,加速度传感器从齿轮箱的机壳测点1、轴承垂直方向测点2、轴承水平方向测点3、轴承轴向测点4,四个位置采集齿轮箱运行过程中的振动信号,并通过多路数据采集器将这些数据汇总发送给处理器系统的数据采集模块。
21.数据采集模块对信号进行采样,采样频率为2000hz,每段信号采样点数为5000。
22.工作时,将加速度传感器放在指定四个位置采集齿轮箱工作时的振动信号,并将这些信号发送给数据采集模块,按照采样频率为2000hz,每段信号采样点数为5000,对振动信号进行采样,采样后数据分析模块对信号进行分解处理成多个频段的能量组成特征向量,提取分解后的多个频段的能量组成特征向量输入给故障诊断模块,故障诊断模块则通过这些特征向量与之前采集的各种运行状态中齿轮箱振动信号的特征向量对比,来看符合哪种状态齿轮箱的特征向量,从而确定是否故障,故障类型是什么。
23.例如当前振动信号的特征向量,与之前采集的齿面磨损状态振动信号的特征向量相匹配,则就可以确定当前齿轮箱故障状态为齿面磨损。
24.人机交互系统则包括输出和输入,输出例如显示器,用于显示结果,或者特征向量等中间数据。输入例如键盘、鼠标等,用于向处理器系统写入数据。
25.数据存储模块则用来储存运行过程中接收或输出的数据,例如接收的特征向量,输出的诊断结果等数据。
26.训练升级模块则是建立故障诊断模型供故障诊断模块使用,并根据工作过程中的数据带入故障诊断模型中,对故障诊断模型进行升级优化。
技术特征:1.一种高速精密带钢冷轧机主传动齿轮箱故障诊断系统,其特征在于,包括:加速度传感器、多路数据采集器和处理器系统,处理器系统包括数据采集模块、数据分析模块、故障诊断模块和训练升级模块,加速度传感器连接在齿轮箱上,用于采集齿轮箱运行过程中的振动信号;多路数据采集器用于将加速度传感器采集到的振动信号汇总并提供给处理器系统;数据采集模块,用于接收多路数据采集器输送的数据,并输送给数据分析模块;数据分析模块,用于将振动信号进行分解处理为多个频段的能量组成特征向量,并提取分解后的多个频段的能量组成特征向量,并将特征向量输送至故障诊断模块;训练升级模块,用于生成故障诊断模块的故障诊断分类模型;故障诊断模块,通过故障诊断分类模型对齿轮箱各故障对应的振动信号分解的特征向量进行分类识别,得到故障诊断结果。2.根据权利要求1所述的一种高速精密带钢冷轧机主传动齿轮箱故障诊断系统,其特征在于:所述加速度传感器有多个,分别连接在齿轮箱轴承座的水平方向、垂直方向、轴向以及齿轮箱箱体处。3.根据权利要求1所述的一种高速精密带钢冷轧机主传动齿轮箱故障诊断系统,其特征在于:所述还包括人机交互系统,用于显示处理器系统得到的故障诊断结果,并向处理器系统内输入数据。4.根据权利要求1所述的一种高速精密带钢冷轧机主传动齿轮箱故障诊断系统,其特征在于:所述处理器系统还包括数据存储模块,用于存储处理器系统接收和输出的数据。5.根据权利要求1所述的一种高速精密带钢冷轧机主传动齿轮箱故障诊断系统,其特征在于:所述训练升级模块,还在使用过程中采集的信号对故障诊断分类模型进行训练升级。6.根据权利要求1所述的一种高速精密带钢冷轧机主传动齿轮箱故障诊断系统,其特征在于:所述数据采集模块采样频率为2000hz,每段信号采样点数为5000。
技术总结本发明公开了一种高速精密带钢冷轧机主传动齿轮箱故障诊断系统,包括加速度传感器、多路数据采集器和处理器系统,处理器系统包括数据采集模块、数据分析模块、故障诊断模块和训练升级模块,加速度传感器,用于采集齿轮箱运行过程中的振动信号;多路数据采集器用于将振动信号汇总并提供给处理器系统;数据采集模块,用于接收多路数据采集器输送的数据;故障诊断模块,通过故障诊断分类模型对振动信号分解的特征向量进行分类识别,得到故障诊断结果。通过对振动信号进行处理,来判断齿轮箱状态,节省了人工成本,填补了轧机设备故障诊断领域的空白,检测灵敏度高,检测结果更为准确。检测结果更为准确。检测结果更为准确。
技术研发人员:计江 王社昌 刘松 孙建亮 王涛 孙杰
受保护的技术使用者:中国重型机械研究院股份公司
技术研发日:2022.10.18
技术公布日:2022/12/23