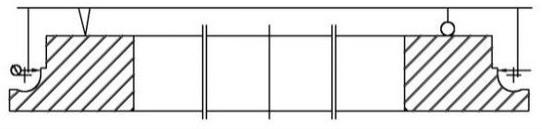
1.本发明涉及一种轴承的中心距测量方法,具体是涉及双排异径球式转盘轴承车加工滚道中心距检测方法,属于轴承加工领域。
背景技术:2.双排异径球式转盘轴承滚道弧面约为整沟的四分之一,在检测滚道中心距时,因滚道曲率截面低于滚道中心点导致无法控制滚道中心距加工准确性,常规检测方式采用线切割样板进行滚道中心距检测,因样板制作过程中存在一定误差,无法实现滚道精准测量,经常造成滚道下工序加工时中心距超差问题;而现有的常规检测方法的具体检测方式,分别如图5和图6所示:图5,将线切割样板做成整体,利用线切割样板进行滚道中心距及滚道曲率检测。
3.图6,将线切割样板做成半截,线切割样板以内径定位,利用线切割样板测量滚道一半中心距及曲率。
4.上述两种方式存在的缺点是:首先样板为线切割样板,制作过程中有0.2mm左右误差,其次车加工后内径尺寸散差较大,用内径定位后影响滚道中心距测量;因此解决双排异径球式转盘轴承滚道车加工检测势在必行。
技术实现要素:5.鉴于上述常规检测方法存在的技术问题,本发明的目的是提供了一种双排异径球式转盘轴承车加工滚道中心距检测方法,解决的是双排异径球式转盘轴承车加工时滚道中心距检测问题。
6.为了实现上述目的,本发明所采用的技术方案是:一种双排异径球式转盘轴承车加工滚道中心距检测方法,包括具体步骤如下:1、以轴承内圈为测量对象,在车加工滚道时,通过增加圆弧滚道面积,使之高出滚道中心,沿着滚道径向最小直径尺寸相切方向进行向上延伸,最终车工形成截面滚道曲线段和截面滚道直线段;2、通过碳纤维尺对表并测量滚道径向直径尺寸;3、通过计算公式,滚道径向直径尺寸=滚道中心距-2倍滚道曲率,可知,滚道中心距=步骤2测量的滚道径向直径尺寸+2倍滚道曲率;4、车加工结束测量中心距合格后,将截面滚道直线段按图纸工艺要求去除,从而得到实际滚道中心距。
7.进一步的,步骤1中的沿着滚道径向直径尺寸切线方向向上延伸的直线段是使超过滚道中心3-5mm;滚道截面直线段为滚道径向直径测量区域a;所述截面滚道曲线段和截面滚道直线段是车刀一个工序加工形成并且呈一体式过渡;这样截面滚道直线段的误差与截面滚道曲线段误差等同,进而通过控制截面滚道直线段的误差来保证截面滚道曲线段的误差;
进一步的,所述步骤3中所述的滚道曲率为截面滚道曲线段的曲率;本发明步骤3中所述的滚道曲率是一个具体数值,是设计图纸规定名义的标准数值。
8.本发明的原理在于滚道中心距与滚道径向直径及曲率关系并充分运用,实质上是通过车加工设定的滚道的基础上沿滚道径向最小直径切线方向多预留一个加工段,这种设计方式完全不同于现有的滚道中心距测量方式。
9.本发明的有益效果是:相比于现有的线切割样板方式,克服了制作样板的测量误差,利用的是滚道中心距与滚道径向直径及曲率关系,优化滚道车加工加工工艺,实现滚道中心距精准测量。
附图说明
10.图1为本发明需要检测的双排异径球式转盘轴承结构图。
11.图2为图1的轴承内圈需要检测中心距(沟心距)的示意图。
12.图3本发明的检测方法的示意图。
13.图4为本发明检测方法中体现滚道径向直径测量区域的示意图。
14.图5为现有的利用整体线切割样板方式测量滚道中心距的结构图。
15.图6为现有的利用半截线切割样板方式测量滚道中心距的结构图。
16.图中,a、滚道径向直径测量区域、b、滚道中心、d0、沟心距。
具体实施方式
17.为使本发明的上述目的、特征和优点能够更加明显易懂,下面结合附图对本发明的具体实施方式做详细的说明。在下面的描述中阐述了很多具体细节以便于充分理解本发明。但是本发明能够以很多不同于在此描述的其它方式来实施,本领域技术人员可以在不违背本发明内涵的情况下做类似改进,因此本发明不受下面公开的具体实施例的限制。
18.如图1-4所示的一种双排异径球式转盘轴承车加工滚道中心距检测方法,包括具体步骤如下:1、以轴承内圈(轴圈)为测量对象,在车加工滚道时,通过增加滚道圆弧面积,使之高出滚道中心,沿着滚道径向最小直径尺寸相切方向进行向上延伸,最终车工形成截面滚道曲线段和截面滚道直线段;2、通过碳纤维尺对表并测量滚道径向直径尺寸;3、通过计算公式,滚道径向直径尺寸=滚道中心距-2倍滚道曲率,可知,滚道中心距d0=步骤2测量的滚道径向直径尺寸+2倍滚道曲率;4、车加工结束测量中心距合格后,将截面滚道直线段按图纸工艺要求去除,从而得到实际滚道中心距。
19.得到的实际滚道的形状与图纸要求形状保持一致;本实施例的轴承为双排异径球式转盘轴承,其结构由座圈01、第一轴圈02、第二轴圈22、第一排滚道钢球04、第二排滚道钢球24组成;在本实施例中,步骤1中的沿着滚道径向最小直径尺寸切线方向向上延伸的直线段是使超过滚道中心b3-5mm;滚道截面直线段为滚道径向直径测量区域a;
所述截面滚道曲线段和截面滚道直线段是车刀一个工序加工形成。
20.所述步骤3中所述的滚道曲率为截面滚道曲线段的曲率;本发明步骤3中所述的滚道曲率是设计图纸规定名义的标准数值。
21.本发明的关键点充分理解滚道中心距与滚道径向直径及曲率关系并充分运用,优化滚道车加工加工工艺,实现滚道中心距精准测量。
技术特征:1.一种双排异径球式转盘轴承车加工滚道中心距检测方法,其特征在于,包括具体步骤如下:(1)以轴承内圈为测量对象,在车加工滚道时,通过增加滚道圆弧面积,沿着滚道径向最小直径尺寸相切方向进行向上延伸,最终车工形成截面滚道曲线段和截面滚道直线段;(2)通过碳纤维尺对表并测量滚道径向直径尺寸;(3)通过计算公式,滚道径向直径尺寸=滚道中心距-2倍滚道曲率,可知,滚道中心距=步骤2测量的滚道径向直径尺寸+2倍滚道曲率;(4)车加工结束测量中心距合格后,将截面滚道直线段按图纸工艺要求去除,从而得到实际滚道中心距。2.根据权利要求1所述的一种双排异径球式转盘轴承车加工滚道中心距检测方法,其特征在于:步骤(1)中的沿着滚道径向最小直径尺寸切线方向向上延伸的直线段是使超过滚道中心3-5mm;滚道截面直线段为滚道径向直径测量区域a。3.根据权利要求1所述的一种双排异径球式转盘轴承车加工滚道中心距检测方法,其特征在于:所述截面滚道曲线段和截面滚道直线段是车刀一个工序加工形成并且呈一体式过渡。4.根据权利要求1所述的一种双排异径球式转盘轴承车加工滚道中心距检测方法,其特征在于:所述步骤(3)中所述的滚道曲率为截面滚道曲线段的曲率。
技术总结本发明涉及一种轴承的中心距测量方法,具体是涉及双排异径球式转盘轴承车加工滚道中心距检测方法,包括具体步骤如下:以轴承内圈为测量对象,在车加工滚道时,通过增加圆弧滚道面积,使之高出滚道中心,沿着滚道径向最小直径尺寸相切方向进行向上延伸,最终车工形成截面滚道曲线段和截面滚道直线段;通过碳纤维尺对表并测量滚道径向直径尺寸;通过计算公式,可知,滚道中心距=步骤2测量的滚道径向直径尺寸+2倍滚道曲率;车加工结束测量中心距合格后,将截面滚道直线段按图纸工艺要求去除,从而得到实际滚道中心距。本发明相比于现有的线切割样板方式,克服了制作样板的测量误差,优化滚道车加工加工工艺,实现滚道中心距精准测量。测量。测量。
技术研发人员:王曼 张海燕 何春艳 高秀娥
受保护的技术使用者:瓦房店轴承集团国家轴承工程技术研究中心有限公司
技术研发日:2022.10.28
技术公布日:2023/1/11