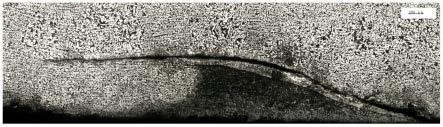
一种表征q345b的钢管折叠裂纹的显微分析方法
技术领域
1.本发明涉及金属材料检测领域,尤其涉及一种表征q345b的钢管折叠裂纹的显微分析方法。
背景技术:2.q345b无缝钢管属低合金高强度结构用钢,广泛用于制造结构件和机械零件,如石油钻杆、汽车传动轴、自行车架以及建筑施工中用的钢脚手架等。q345b无缝钢管的生产工艺为:铁水预处理-顶底复吹转炉-lf精炼炉-vd真空处理-弧形连铸机-管坯锯切-管坯加热-菌式穿孔机-pqf连轧机-定径机-冷床-精整。交货前,要求钢管的内外表面不允许有目视可见的裂纹、折叠、结疤、轧折和离层等缺陷。
3.某厂生产的q354b无缝钢管经φ430mm圆坯穿孔热轧成φ402mm
×
16mm,管外壁出现折叠裂纹缺陷,严重影响产品质量。
技术实现要素:4.为了解决上述技术问题,本发明的目的是提供一种表征q345b的钢管折叠裂纹的显微分析方法,将q345b钢管折叠裂纹的微观特征及其附近的金相组织特征一目了然的呈现出来,以判定折叠裂纹的产生原因。
5.为解决上述技术问题,本发明采用如下技术方案:
6.本发明一种表征q345b的钢管折叠裂纹的显微分析方法,主要包括以下步骤:
7.1)取样
8.根据折叠裂纹宏观形貌,判定裂纹源位置,从裂纹源处取金相试样;
9.2)金相制样
10.磨制试样裂纹源区域横向或纵向检测面,砂轮机倒角-粗磨-砂纸细磨-机械抛光,最后试样检测面呈镜面,无水渍、污渍;待非金属夹杂物、氧化圆点、氧化铁项目检测完成后,采用4%硝酸酒精溶液腐蚀试样,进行显微组织、晶粒度和脱碳项目的检测;
11.3)显微镜检测
12.将制好的金相试样倒置放在金相显微镜的载物台上,找到裂纹源位置,观察裂纹的深度、长度、裂纹处非金属夹杂物、显微组织及脱碳情况,使用采集图像软件进行拍照记录,并且标注标尺;
13.对于长度超长的折叠裂纹,采用图像拼接手段,将多个视场进行拼接,最后加载标尺;
14.对于试样边缘景深较大的折叠裂纹,采用景深扩展手段,将多个视场进行景深叠加,最后加载标尺;
15.4)综合分析
16.结合折叠裂纹产生的原始情况、裂纹宏观形貌、微观特征及检测数据,综合分析裂纹产生的原因,将产生原因反馈至生产单位,用于指导和优化生产工艺,减少裂纹产生率,
提高产品质量。
17.进一步的,所述步骤1),加工试样时要避免裂纹源区域受切割热影响区的影响。
18.进一步的,所述步骤3),金相显微镜为axio observer金相显微镜。
19.与现有技术相比,本发明的有益技术效果:
20.本发明提供了一种表征q345b钢管折叠裂纹的显微分析方法,使用金相显微镜图像采集功能、图像拼接、景深扩展等技术手段表征折叠裂纹的全貌,有利于分析裂纹的产生原因。
附图说明
21.下面结合附图说明对本发明作进一步说明。
22.图1为折叠裂纹宏观特征;
23.图2为裂纹处氧化圆点形貌;
24.图3为折叠裂纹全貌;
25.图4为裂纹近表面一侧异常组织;
26.图5为基体组织。
具体实施方式
27.实施例
28.某厂生产的q354b无缝钢管经φ430mm圆坯穿孔热轧成φ402mm
×
16mm,管外壁出现折叠裂纹缺陷,如图1所示。宏观观察,缺陷无规则分布,沿轧向扩展,为了找到折叠的产生原因,在缺陷处取样做微观检测分析。
29.磨制缺陷试样的横向面,抛光后金相显微镜下观察,缺陷处可见一条与表面约呈30
°
、尾端近似平行表面的裂纹伸向钢基。裂纹内充满氧化铁,附近有氧化圆点,如图2所示,裂纹内及周围无异常非金属夹杂物。采用4%硝酸酒精腐蚀后,镜下观察裂纹处组织脱碳,裂纹处存在异常马氏体组织。
30.由于金相显微镜的视场有限,无法采用一个视场完整表达裂纹的全貌。因此,使用图像拼接手段,形成折叠裂纹的全部形貌照片,加载标尺后,估算裂纹长约4.2mm,深约0.7mm。同时,裂纹近表面一侧的异常组织与基体组织的差异、裂纹附近的晶粒度不均匀(即混晶)现象也都非常明显的表征出来,如图3-5所示。这为判定折叠裂纹的产生原因提供了详细、准确的数据。
31.综合分析,裂纹附近有氧化铁、氧化圆点及脱碳等高温氧化特征。表明钢坯表面存在微裂纹,经加热炉加热后裂纹周围高温氧化,在后续轧制过程中进一步扩展形成外壁折叠缺陷。外壁折叠裂纹近表面一侧的异常马氏体组织是由裂纹处积水产生的急冷而造成的。
32.以上所述的实施例仅是对本发明的优选方式进行描述,并非对本发明的范围进行限定,在不脱离本发明设计精神的前提下,本领域普通技术人员对本发明的技术方案做出的各种变形和改进,均应落入本发明权利要求书确定的保护范围内。
技术特征:1.一种表征q345b的钢管折叠裂纹的显微分析方法,其特征在于:主要包括以下步骤:1)取样根据折叠裂纹宏观形貌,判定裂纹源位置,从裂纹源处取金相试样;2)金相制样磨制试样裂纹源区域横向或纵向检测面,砂轮机倒角-粗磨-砂纸细磨-机械抛光,最后试样检测面呈镜面,无水渍、污渍;待非金属夹杂物、氧化圆点、氧化铁项目检测完成后,采用4%硝酸酒精溶液腐蚀试样,进行显微组织、晶粒度和脱碳项目的检测;3)显微镜检测将制好的金相试样倒置放在金相显微镜的载物台上,找到裂纹源位置,观察裂纹的深度、长度、裂纹处非金属夹杂物、显微组织及脱碳情况,使用采集图像软件进行拍照记录,并且标注标尺;对于长度超长的折叠裂纹,采用图像拼接手段,将多个视场进行拼接,最后加载标尺;对于试样边缘景深较大的折叠裂纹,采用景深扩展手段,将多个视场进行景深叠加,最后加载标尺;4)综合分析结合折叠裂纹产生的原始情况、裂纹宏观形貌、微观特征及检测数据,综合分析裂纹产生的原因,将产生原因反馈至生产单位,用于指导和优化生产工艺,减少裂纹产生率,提高产品质量。2.根据权利要求1所述的表征q345b的钢管折叠裂纹的显微分析方法,其特征在于:所述步骤1),加工试样时要避免裂纹源区域受切割热影响区的影响。3.根据权利要求1所述的表征q345b的钢管折叠裂纹的显微分析方法,其特征在于:所述步骤3),金相显微镜为axio observer金相显微镜。
技术总结本发明公开了一种提供一种表征Q345B的钢管折叠裂纹的显微分析方法,使用金相显微镜图像采集功能、图像拼接、景深扩展等技术手段表征折叠裂纹的全貌,将Q345B钢管折叠裂纹的微观特征及其附近的金相组织特征一目了然的呈现出来,以判定折叠裂纹的产生原因。以判定折叠裂纹的产生原因。以判定折叠裂纹的产生原因。
技术研发人员:寇沙沙 李文亚 刘莉 石晓霞
受保护的技术使用者:包头钢铁(集团)有限责任公司
技术研发日:2022.11.21
技术公布日:2023/3/21