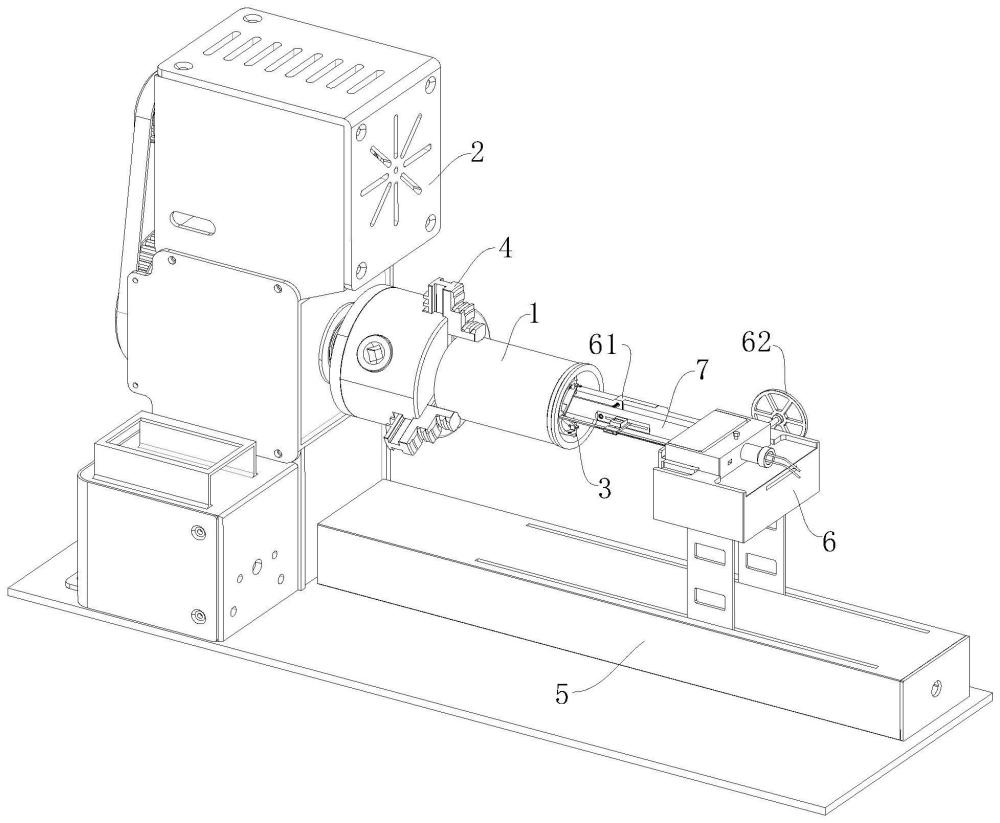
本发明涉及气缸套内孔测量,具体的说是一种大缸径船用柴油机零件气缸套内孔测量装置。
背景技术:
1、气缸套是一个圆筒形零件,置于机体的气缸体孔中,上由气缸盖压紧固定。活塞在其内孔作往复运动,其外有冷却水冷却;
2、机加工环节是气缸套加工的主要步骤。常用的机加工方法包括车削、镗孔、锥度加工等,其中,镗孔是一种常用的内孔加工方法。镗刀一般采用机器械式镗刀和手动式镗刀。在加工气缸套时,要注意工件固定、刀具的选择和加工速度,并在镗孔过程中对气缸套内孔直径进行测量,以保证尺寸精度需求,测量进行过程中,还需排除镗轴位置居中造成的空间狭小以及碎屑堆积造成的气缸套内壁或镗刀磨损过度的负面影响,以达到快速测量及精准测量的目的。
3、鉴于此,本发明提出了一种大缸径船用柴油机零件气缸套内孔测量装置,解决了上述技术问题。
技术实现思路
1、为了解决现有技术的不足,本发明提供了一种大缸径船用柴油机零件气缸套内孔测量装置;从而解决了传统测量工具难以对处于加工工位的气缸套进行准确的内孔直径测量,难以排除镗轴占用测量空间及碎屑堆积造成的测量误差增大所带来的负面影响的问题。
2、本发明解决其技术问题所采用的技术方案一种大缸径船用柴油机零件气缸套内孔测量装置,包括气缸套、机床、测量尺、移动机和排屑柱,所述机床上转动安装有三爪卡盘,气缸套固定安装于三爪卡盘内,测量尺位于气缸套内孔中。
3、所述移动机活动安装于机床的前部,移动机的上部固定安装有机座,机座中部滑动安装有镗轴,镗轴与三爪卡盘同轴心,镗轴前部贯穿气缸套内孔,三爪卡盘中部设置有与镗轴端部固定插接的卡槽,测量尺活动安装于镗轴上,镗轴后部为固定部,固定部固定安装于机座上,镗轴前部为滑动部,滑动部滑动安装于固定部上,排屑柱转动安装于滑动部的端部,排屑柱的端部固定安装有于三爪卡盘中部固定贴合的卡块,排屑柱的内侧设置有空腔,排屑柱朝向气缸套的一侧开设有与空腔相连通的排屑槽,镗轴固定部及滑动部相互贯通开设有与排屑柱内侧空腔相连通的内槽,且固定部端部安装有气管。
4、优选的,所述排屑柱内滑动安装有挡板,挡板中部与进气端口密封贴合,挡板的四周铰接安装有多个挡条,挡条与挡板之间连接有扭簧,且挡条侧壁与排屑槽密封贴合。
5、优选的,所述固定部的中部开设有调节槽,调节槽内固定安装有支板,支板端部滑动安装有推进尺,推进尺侧壁设置有第一刻度线,且支板端部安装有与第一刻度线相配合的指示片,测量尺固定安装于推进尺端部。
6、优选的,所述机座的一侧滑动安装有镗刀,机座上通过螺纹配合的方式安装有手轮,手轮与镗刀安装底座转动连接,固定部中部固定安装有分离尺,分离尺贯穿镗刀中部,且分离尺上印刻有第二刻度线。
7、优选的,所述机座上部安装有第一螺栓,第一螺栓端部抵靠于固定部的外壁,机座的一侧开设有与推进尺相适配的推进槽。
8、优选的,所述测量尺为“c”形结构,测量尺的中部固定安装于推进尺的端部,测量尺位于气缸套内孔与镗轴之间的间隙中,测量尺的两端对称安装有测量头,测量头轴线垂直于气缸套轴线。
9、优选的,所述测量头上下两端对称安装有测量柱,测量柱同轴线,测量头端部开设有与测量柱滑动配合的槽孔,测量头内侧转动安装有齿轮杆,两个测量柱分别位于齿轮杆的两侧,且测量柱的侧面均设置有与齿轮杆相啮合的齿槽。
10、优选的,所述测量尺的端部内侧滑动安装有齿环,齿环的外轮廓与齿轮杆相啮合。
11、优选的,所述测量尺的中部倾斜固定安装有加强板,加强板为“v”形结构,且加强板的的两端分别卡接于上下两个测量头的中部,加强板上螺纹配合安装有第二螺栓,第二螺栓的端部抵靠在其中一个测量柱的侧壁上。
12、优选的,所述加强板中部转动安装有计数轮,计数轮滚动贴合于测量柱的外壁上,支板的中部固定安装有显示器,分离尺、推进尺及测量尺三者分别与显示器电性连接。
13、本发明的有益效果:
14、(1)在本发明中,通过气流的吹送作用,在加速镗孔工作区域冷却的同时,将产生的碎屑携带排出,倾斜打开状态的挡条,其与气缸套内壁之间保持倾斜夹角,气流由排屑槽位置排出的过程中,其流向受通道倾斜程度影响始终倾斜指向气缸套的外部端口方向,进而使得受其吹送的碎屑朝向气缸套的前部端口方向移动排出,以此实现碎屑的集中收集处理,避免过度分散造成清理难度增加。
15、(2)在本发明中,镗孔工作时通过推进尺带动测量尺向远离气缸套的方向进行移动,使测量尺与气缸套之间保持适当的间隔距离,从而便于碎屑的排出,测量工作进行时,无需将气缸套取出,通过推动推进尺前进的方式,可使测量尺到达气缸套内侧,进行缸径的测量工作,快速便捷且省时省力,避免了气缸套频繁取出造成的测量尺寸误差增大。
16、(3)在本发明中,“c”形测量尺可于镗轴和气缸套内孔之间的间隙进入,充分适应工况需求,测量工具的测量柱是标准的千分测量单元,以此实现对气缸套内孔直径的精确测量,通过传感器进行的电性连接,显示器可分别对计数轮滚动周期、分离尺及推进尺刻度进行识别读取,进而实现对气缸套内孔预定深度与预定孔径进行测量,满足多种测量需求,且测量精度可调可控,数据读取方便。
技术特征:1.一种大缸径船用柴油机零件气缸套内孔测量装置,包括气缸套(1)、机床(2)和测量尺(3),所述机床(2)上转动安装有三爪卡盘(4),气缸套(1)固定安装于三爪卡盘(4)内,测量尺(3)位于气缸套(1)内孔中,其特征在于,还包括
2.根据权利要求1中所述的一种大缸径船用柴油机零件气缸套内孔测量装置,其特征在于:所述排屑柱(8)内滑动安装有挡板(83),挡板(83)中部与进气端口密封贴合,挡板(83)的四周铰接安装有多个挡条(84),挡条(84)与挡板(83)之间连接有扭簧,且挡条(84)侧壁与排屑槽(82)密封贴合。
3.根据权利要求1中所述的一种大缸径船用柴油机零件气缸套内孔测量装置,其特征在于:所述固定部(71)的中部开设有调节槽(73),调节槽(73)内固定安装有支板(74),支板(74)端部滑动安装有推进尺(75),推进尺(75)侧壁设置有第一刻度线,且支板(74)端部安装有与第一刻度线相配合的指示片(741),测量尺(3)固定安装于推进尺(75)端部。
4.根据权利要求1中所述的一种大缸径船用柴油机零件气缸套内孔测量装置,其特征在于:所述机座(6)的一侧滑动安装有镗刀(61),机座(6)上通过螺纹配合的方式安装有手轮(62),手轮(62)与镗刀(61)安装底座转动连接,固定部(71)中部固定安装有分离尺(712),分离尺(712)贯穿镗刀(61)中部,且分离尺(712)上印刻有第二刻度线。
5.根据权利要求3中所述的一种大缸径船用柴油机零件气缸套内孔测量装置,其特征在于:所述机座(6)上部安装有第一螺栓(63),第一螺栓(63)端部抵靠于固定部(71)的外壁,机座(6)的一侧开设有与推进尺(75)相适配的推进槽(64)。
6.根据权利要求3中所述的一种大缸径船用柴油机零件气缸套内孔测量装置,其特征在于:所述测量尺(3)为“c”形结构,测量尺(3)的中部固定安装于推进尺(75)的端部,测量尺(3)位于气缸套(1)内孔与镗轴(7)之间的间隙中,测量尺(3)的两端对称安装有测量头(31),测量头(31)轴线垂直于气缸套(1)轴线。
7.根据权利要求6中所述的一种大缸径船用柴油机零件气缸套内孔测量装置,其特征在于:所述测量头(31)上下两端对称安装有测量柱(32),测量柱(32)同轴线,测量头(31)端部开设有与测量柱(32)滑动配合的槽孔,测量头(31)内侧转动安装有齿轮杆(33),两个测量柱(32)分别位于齿轮杆(33)的两侧,且测量柱(32)的侧面均设置有与齿轮杆(33)相啮合的齿槽(321)。
8.根据权利要求7中所述的一种大缸径船用柴油机零件气缸套内孔测量装置,其特征在于:所述测量尺(3)的端部内侧滑动安装有齿环(34),齿环(34)的外轮廓与齿轮杆(33)相啮合。
9.根据权利要求7中所述的一种大缸径船用柴油机零件气缸套内孔测量装置,其特征在于:所述测量尺(3)的中部倾斜固定安装有加强板(35),加强板(35)为“v”形结构,且加强板(35)的两端分别卡接于上下两个测量头(31)的中部,加强板(35)上螺纹配合安装有第二螺栓(351),第二螺栓(351)的端部抵靠在其中一个测量柱(32)的侧壁上。
10.根据权利要求6或9任一项中所述的一种大缸径船用柴油机零件气缸套内孔测量装置,其特征在于:所述加强板(35)中部转动安装有计数轮(352),计数轮(352)滚动贴合于测量柱(32)的外壁上,支板(74)的中部固定安装有显示器(742),分离尺(712)、推进尺(75)及测量尺(3)三者分别与显示器(742)电性连接。
技术总结本发明涉及气缸套内孔测量技术领域,具体的说是一种大缸径船用柴油机零件气缸套内孔测量装置,包括气缸套、机床、测量尺、移动机和排屑柱,气缸套是一个圆筒形零件,置于机体的气缸体孔中,机加工环节是气缸套加工的主要步骤。常用的机加工方法包括车削、镗孔、锥度加工等,其中,镗孔是一种常用的内孔加工方法。镗刀一般采用机器械式镗刀和手动式镗刀。在加工气缸套时,要注意工件固定、刀具的选择和加工速度,并在镗孔过程中对气缸套内孔直径进行测量,以保证尺寸精度需求,测量进行过程中,还需排除镗轴位置居中造成的空间狭小以及碎屑堆积造成的气缸套内壁或镗刀磨损过度的负面影响,以达到快速测量及精准测量的目的。
技术研发人员:孙云忠,卿尧,张俊峰
受保护的技术使用者:纽龙船舶动力(阜南)有限公司
技术研发日:技术公布日:2024/8/20