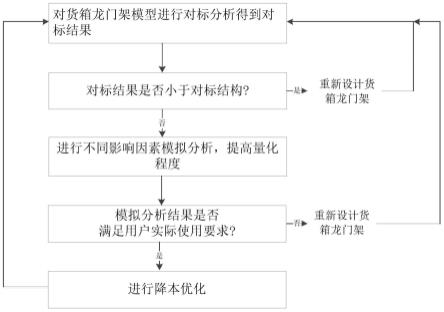
基于cae的货箱龙门架优化设计
技术领域
1.本发明涉及车辆技术领域,特别涉及基于cae的货箱龙门架优化设计。
背景技术:2.目前国内对商用车货箱强度,没有一个系统的校核分析方案,大部分以车型对标、实车路试等方式进行验证。但此方式试验周期长、试验成本高、用户还原度底、实际强度无法量化、单件成本难以控制。
技术实现要素:3.针对现有技术中商用车货箱强度校核周期较长的问题,本发明提出基于cae的货箱龙门架优化设计,通过对货箱龙门架模型进行对标分析和用户模拟分析,使结果刚强度可进行横向的与成熟车型对标处理,免去了试验验证的周期及费用,减少了校核周期。
4.为了实现上述目的,本发明提供以下技术方案:
5.基于cae的货箱龙门架优化设计,具体包括以下步骤:
6.s1:对货箱龙门架模型进行对标分析得到对标结果;
7.s2:若对标结果不小于对标结构,则进入s3,否则重新对初始货箱龙门架模型进行优化;
8.s3:进行不同影响因素模拟分析,提高量化程度;
9.s4:若模拟分析结果显示满足用户实际使用要求,则进行适当的降本优化;若模拟分析结果显示存在风险,则需重新设计货箱龙门架模型。
10.优选地,对标分析的方法为:应用有限元的方式将货箱龙门架的刚强度量化并进行横向对比,即在货箱龙门架相同高度施加强制位移,致使结构失稳,提取加载点反力,然后绘制加载过程中的反力曲线,得到最大反力。
11.优选地,所述s2中,对标结构为在设计货箱龙门架模型时预设的标准结构。
12.优选地,所述s3中,影响因素模拟包括用户装载习惯、减速度曲线、设置初速度,并施加1倍重力场。
13.优选地,采用cae对货箱龙门架模型进行对标分析。
14.综上所述,由于采用了上述技术方案,与现有技术相比,本发明至少具有以下有益效果:
15.本发明主要通过一个闭环的分析流程,在对标分析阶段对结果进行了初步的量化处理,使结果刚强度可进行横向的与成熟车型对标处理,免去了试验验证的周期及费用,减少了校核周期;
16.同时在接下来的用户模拟阶段,主要针对用户实际使用需求,尽可能在满足用户使用需求的情况下,进行降本优化,从而提升产品竞争力。
附图说明:
17.图1为根据本发明示例性实施例的基于cae的货箱龙门架优化设计示意图。
具体实施方式
18.下面结合实施例及具体实施方式对本发明作进一步的详细描述。但不应将此理解为本发明上述主题的范围仅限于以下的实施例,凡基于本发明内容所实现的技术均属于本发明的范围。
19.在本发明的描述中,需要理解的是,术语“纵向”、“横向”、“上”、“下”、“前”、“后”、“左”、“右”、“竖直”、“水平”、“顶”、“底”“内”、“外”等指示的方位或位置关系为基于附图所示的方位或位置关系,仅是为了便于描述本发明和简化描述,而不是指示或暗示所指的装置或元件必须具有特定的方位、以特定的方位构造和操作,因此不能理解为对本发明的限制。
20.如图1所示,本发明提供基于cae的货箱龙门架优化设计,具体包括以下步骤:
21.s1:对初始货箱龙门架模型进行对标分析得到对标结果。
22.本实施例中,初始货箱龙门架模型为在车辆设计阶段就已建立的模型,只需从数据库中调取即可。
23.对标分析的方法为:通过cae分析软件,应用有限元的方式将其刚强度量化进行横向对比,即在货箱龙门架相同高度施加强制位移,致使结构失稳,提取加载点反力,然后绘制加载过程中的反力曲线,对比最大反力判断结构优劣。
24.s2:对标结果(最大反力)不下于对标结构(预设值),则进入s3,否则重新对初始货箱龙门架模型进行优化。
25.本实施例中,在设计货箱龙门架时,为保证安全性,一般都会提前输入预设值,当s1中的最大反力等于或大于预设值时,表明设计的货箱龙门架合格,可进入s3;若s1中的最大反力小于预设值时,表明设计的货箱龙门架不合格,需要重新设计。本发明不涉及货箱龙门架的设计,只需要快速对货箱龙门架的性能进行测试。
26.s3:进行不同影响因素模拟分析,提高量化程度。
27.本实施例中,主要针对用户实际使用需求,尽可能在满足用户使用需求的情况下,进行降本优化,从而提升产品竞争力。
28.影响因素模拟包括用户装载习惯综合评估后制定货物模拟方式、根据制动试验数据提取减速度曲线、设置特定初速度,并施加1倍重力场、综合各因素设置分析工况,由最大塑性应变判断结构可行性。
29.s4:若模拟分析结构显示满足用户实际使用要求,则可进行适当的降本优化(例如选用价格便宜的材料),并重复s1-s4;若结构显示存在一定风险,则证明对标车设计状态存在一定风险,提高性能目标以提高产品竞争力。
30.本发明主要阐述了一个闭环的分析流程,并对其中对标分析与用户模拟分析进行了详细介绍。对货箱龙门架设计开发进行了一个闭环的管控。在对标分析阶段对结果进行了初步的量化处理,使结果刚强度可进行横向的与成熟车型对标处理,免去了试验验证的周期及费用。
31.本领域的普通技术人员可以理解,上述各实施方式是实现本发明的具体实施例,
而在实际应用中,可以在形式上和细节上对其作各种改变,而不偏离本发明的精神和范围。
技术特征:1.基于cae的货箱龙门架优化设计,其特征在于,具体包括以下步骤:s1:对货箱龙门架模型进行对标分析得到对标结果;s2:若对标结果不小于对标结构,则进入s3,否则重新对初始货箱龙门架模型进行优化;s3:进行不同影响因素模拟分析,提高量化程度;s4:若模拟分析结果显示满足用户实际使用要求,则进行适当的降本优化;若模拟分析结果显示存在风险,则需重新设计货箱龙门架模型。2.如权利要求1所述的基于cae的货箱龙门架优化设计,其特征在于,所述s1中,对标分析的方法为:应用有限元的方式将货箱龙门架的刚强度量化并进行横向对比,即在货箱龙门架相同高度施加强制位移,致使结构失稳,提取加载点反力,然后绘制加载过程中的反力曲线,得到最大反力。3.如权利要求1所述的基于cae的货箱龙门架优化设计,其特征在于,所述s2中,对标结构为在设计货箱龙门架模型时预设的标准结构。4.如权利要求1所述的基于cae的货箱龙门架优化设计,其特征在于,所述s3中,影响因素模拟包括用户装载习惯、减速度曲线、设置初速度,并施加1倍重力场。5.如权利要求2所述的基于cae的货箱龙门架优化设计,其特征在于,采用cae对货箱龙门架模型进行对标分析。
技术总结本发明公开基于CAE的货箱龙门架优化设计,包括S1:对货箱龙门架模型进行对标分析得到对标结果;S2:若对标结果不小于对标结构,则进入S3,否则重新对初始货箱龙门架模型进行优化;S3:进行不同影响因素模拟分析,提高量化程度;S4:若模拟分析结果显示满足用户实际使用要求,则进行适当的降本优化;若模拟分析结果显示存在风险,则需重新设计货箱龙门架模型。则需重新设计货箱龙门架模型。则需重新设计货箱龙门架模型。
技术研发人员:韩鸣 王强 马雪坤 王千浩
受保护的技术使用者:重庆长安跨越车辆有限公司
技术研发日:2022.04.18
技术公布日:2022/6/17