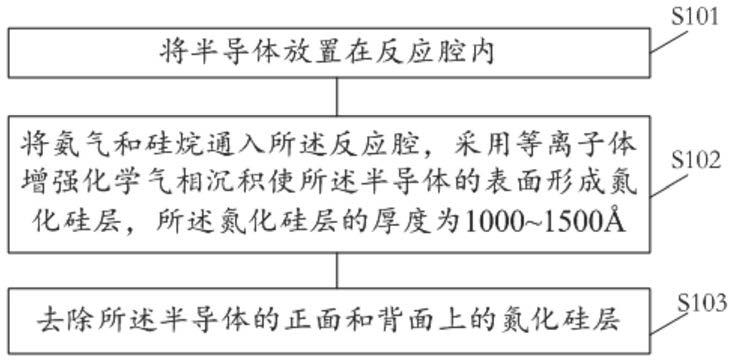
1.本发明涉及半导体技术领域,特别是涉及一种半导体的处理方法。
背景技术:2.半导体的正面和反面都是加工过程中主要控制部分,而半导体侧面的粗糙程度往往对半导体的工作性能产生巨大影响。粗糙的侧面主要是半导体在切割时形成,走刀位的光滑程度,取决于刀锋的锋利程度和切削速度,如果产生崩裂,就会造成工作时的掉落残渣的风险。另外,镍铁(nife)是半导体的核心部分,主要发挥着信息的处理功能,而表面情况对nife的磁性能有很大的影响,如果侧面特别粗糙,那么磁灵敏度和稳定性都会受到影响。
技术实现要素:3.本发明实施例的目的是提供一种半导体的处理方法,其能够避免现有的半导体由于切割工序等原因导致侧面粗糙造成掉落残渣的问题。
4.为了解决上述技术问题,本发明实施例提供一种半导体的处理方法,包括:
5.将半导体放置在反应腔内;
6.将氨气和硅烷通入所述反应腔,采用等离子体增强化学气相沉积使所述半导体的表面形成氮化硅层,所述氮化硅层的厚度为
7.去除所述半导体的正面和背面上的氮化硅层。
8.作为优选方案,在所述半导体的表面形成氮化硅层时,所述反应腔的温度为500~600℃,所述反应腔的压力为1.5torr。
9.作为优选方案,通入所述反应腔的硅烷的流量为100~180sccm。
10.作为优选方案,通入所述反应腔的硅烷的流量为120sccm,氨气的流量为1700sccm。
11.作为优选方案,所述反应腔的高频电源的功率为1500w。
12.作为优选方案,在所述半导体的表面形成氮化硅层的沉积时间为20分钟。
13.作为优选方案,通入所述反应腔的硅烷的流量为150sccm,氨气的流量为2000sccm。
14.作为优选方案,所述反应腔的高频电源的功率为1800~2000w。
15.作为优选方案,在所述半导体的表面形成氮化硅层的沉积时间为15分钟。
16.实施本发明实施例,具有如下有益效果:
17.本发明实施例提供一种半导体的处理方法,首先将半导体放置在反应腔内,并将氨气和硅烷通入所述反应腔,采用等离子体增强化学气相沉积使所述半导体的表面形成氮化硅层,所述氮化硅层的厚度为去除所述半导体的正面和背面上的氮化硅层,而所述半导体的侧面仍然保留氮化硅层,致密的氮化硅层作为保护膜,改善了半导体侧面的粗糙程度,避免了现有的半导体由于切割工序等原因导致侧面粗糙造成掉落残渣的问题,而且不会带来杂质颗粒,保证了半导体元件的质量。
附图说明
18.图1是本发明提供的半导体的处理方法的一个实施例的流程图。
具体实施方式
19.下面将结合本发明实施例中的附图,对本发明实施例中的技术方案进行清楚、完整地描述,显然,所描述的实施例仅仅是本发明一部分实施例,而不是全部的实施例。基于本发明中的实施例,本领域普通技术人员在没有作出创造性劳动前提下所获得的所有其他实施例,都属于本发明保护的范围。
20.请参阅图1,其是本发明提供的半导体的处理方法的一个实施例的流程图。
21.本发明实施例提供的半导体的处理方法包括:
22.步骤s101,将半导体放置在反应腔内;
23.步骤s102,将氨气和硅烷通入所述反应腔,采用等离子体增强化学气相沉积使所述半导体的表面形成氮化硅层,所述氮化硅层的厚度为
24.步骤s103,去除所述半导体的正面和背面上的氮化硅层。
25.在本发明实施例中,首先将半导体放置在反应腔内,并将氨气和硅烷通入所述反应腔,采用等离子体增强化学气相沉积使所述半导体的表面形成氮化硅层,所述氮化硅层的厚度为去除所述半导体的正面和背面上的氮化硅层,而所述半导体的侧面仍然保留氮化硅层,致密的氮化硅层作为保护膜,改善了半导体侧面的粗糙程度,避免了现有的半导体由于切割工序等原因导致侧面粗糙造成掉落残渣的问题,而且不会带来杂质颗粒,保证了半导体元件的质量。
26.在本发明实施例中,在所述步骤s102中,采用等离子体增强化学气相沉积的方法使所述半导体的表面沉积氮化硅,以使致密的氮化硅层作为保护膜完全包覆半导体,即在镀膜的时候是整体镀膜,后续将半导体正面和背面的保护膜去掉,只留下侧面的膜。在具体实施当中,所述半导体上设有多个凹槽,在半导体的表面沉积氮化硅层,使得氮化硅层覆盖凹槽底部和凹槽侧壁,改善了凹槽的粗糙程度,避免了凹槽掉落残渣,并且不会带来杂质颗粒,保证了半导体元件的质量。此外,每一凹槽的深度和宽度均为5um,而凹槽侧壁上的氮化硅层的厚度为远远小于凹槽的深度和宽度。
27.优选地,在所述半导体的表面形成氮化硅层时,所述反应腔的温度为500~600℃,所述反应腔的压力为1.5torr。另外,为了确保沉积氮化硅的速度,所述步骤s102中通入所述反应腔的硅烷的流量为100~180sccm。在通常情况下,硅烷的流量小于100sccm或大于180sccm会降低镀膜的速度,而在100~180sccm可以确保沉积氮化硅的速度。
28.在一种可选的实施方式中,所述步骤s102中通入所述反应腔的硅烷的流量为120sccm,氨气的流量为1700sccm,所述反应腔的高频电源的功率为1500w,在所述半导体的表面形成氮化硅层的沉积时间为20分钟。
29.在另一种可选的实施方式中,所述步骤s102中通入所述反应腔的硅烷的流量为150sccm,氨气的流量为2000sccm,所述反应腔的高频电源的功率为1800~2000w,在所述半导体的表面形成氮化硅层的沉积时间为15分钟。
30.综上,本发明实施例提供一种半导体的处理方法,首先将半导体放置在反应腔内,并将氨气和硅烷通入所述反应腔,采用等离子体增强化学气相沉积使所述半导体的表面形
成氮化硅层,所述氮化硅层的厚度为去除所述半导体的正面和背面上的氮化硅层,而所述半导体的侧面仍然保留氮化硅层,致密的氮化硅层作为保护膜,改善了半导体侧面的粗糙程度,避免了现有的半导体由于切割工序等原因导致侧面粗糙造成掉落残渣的问题,而且不会带来杂质颗粒,保证了半导体元件的质量。
31.以上所述仅是本发明的优选实施方式,应当指出,对于本技术领域的普通技术人员来说,在不脱离本发明技术原理的前提下,还可以做出若干改进和替换,这些改进和替换也应视为本发明的保护范围。
技术特征:1.一种半导体的处理方法,其特征在于,包括:将半导体放置在反应腔内;将氨气和硅烷通入所述反应腔,采用等离子体增强化学气相沉积使所述半导体的表面形成氮化硅层,所述氮化硅层的厚度为去除所述半导体的正面和背面上的氮化硅层。2.如权利要求1所述的半导体的处理方法,其特征在于,在所述半导体的表面形成氮化硅层时,所述反应腔的温度为500~600℃,所述反应腔的压力为1.5torr。3.如权利要求1或2所述的半导体的处理方法,其特征在于,通入所述反应腔的硅烷的流量为100~180sccm。4.如权利要求3所述的半导体的处理方法,其特征在于,通入所述反应腔的硅烷的流量为120sccm,氨气的流量为1700sccm。5.如权利要求4所述的半导体的处理方法,其特征在于,所述反应腔的高频电源的功率为1500w。6.如权利要求4所述的半导体的处理方法,其特征在于,在所述半导体的表面形成氮化硅层的沉积时间为20分钟。7.如权利要求3所述的半导体的处理方法,其特征在于,通入所述反应腔的硅烷的流量为150sccm,氨气的流量为2000sccm。8.如权利要求7所述的半导体的处理方法,其特征在于,所述反应腔的高频电源的功率为1800~2000w。9.如权利要求7所述的半导体的处理方法,其特征在于,在所述半导体的表面形成氮化硅层的沉积时间为15分钟。
技术总结本发明涉及半导体技术领域,公开了一种半导体的处理方法,首先将半导体放置在反应腔内,并将氨气和硅烷通入所述反应腔,采用等离子体增强化学气相沉积使所述半导体的表面形成氮化硅层,所述氮化硅层的厚度为去除所述半导体的正面和背面上的氮化硅层,而所述半导体的侧面仍然保留氮化硅层,致密的氮化硅层作为保护膜,改善了半导体侧面的粗糙程度,避免了现有的半导体由于切割工序等原因导致侧面粗糙造成掉落残渣的问题,而且不会带来杂质颗粒,保证了半导体元件的质量。的质量。的质量。的质量。
技术研发人员:黄德权
受保护的技术使用者:东莞新科技术研究开发有限公司
技术研发日:2020.02.18
技术公布日:2021/9/2