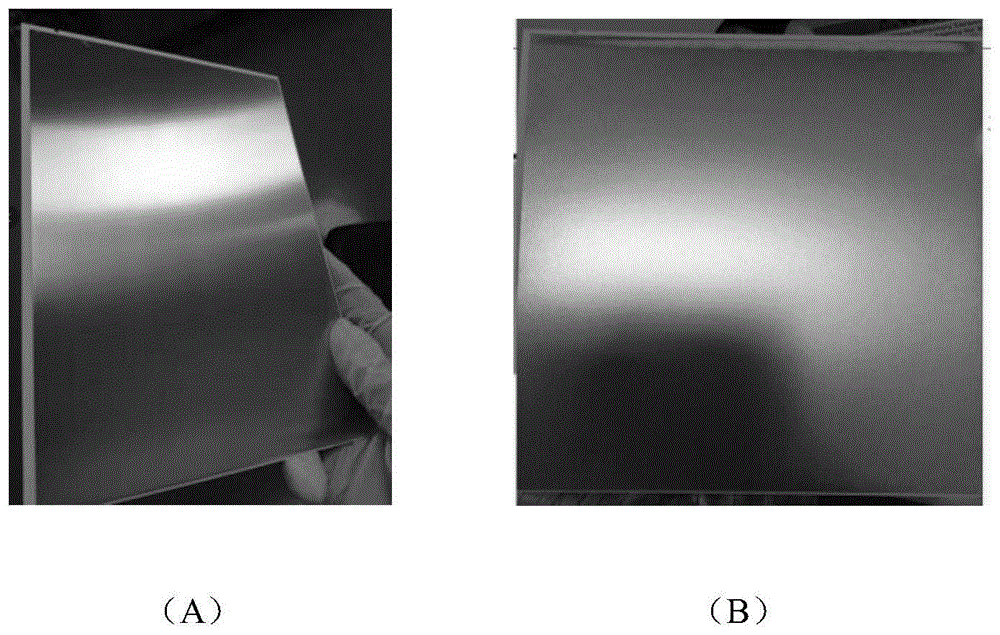
本发明属于dcb基板制备技术领域,具体涉及半导体制冷器、led、功率半导体等的dbc基板产品皱皮疙瘩不良的方法。
背景技术:
铜片氧化工艺是铜直接键合(directbondedcopper,简称dbc)技术的一道关键工艺,使铜片与al2o3陶瓷牢固键合。在铜片氧化烧结工艺中,由于环境洁净度的限制,过程中易带入污染,这种污染有可能是原材料本身的,也有可能是过程中引入的,在氧化工艺(800℃左右)过程中,会放大铜氧化过程中的不良缺陷,主要表现为非氧化面的氧化不均,亮圈亮点,异物等。
所有的不良缺陷在微观下主要表现为中间黑色异物,edx分析主要成分为ni、cr、c、o等。铜片非氧化面的不良经烧结工艺1065℃左右,会进一步放大缺陷,主要表现为色差、皱皮以及疙瘩。色差、皱皮主要是由于铜片非氧化面的氧化不均,部分区域氧化过浅(色差),局部氧化过深导致,疙瘩是由于过程中的带入的污染导致。分布上,色差浮于表面,疙瘩、皱皮主要集中在表面8μm左右。
技术实现要素:
本发明是为解决上述不足进行的,针对产品表面皱皮疙瘩,提供了一种减少dcb产品皱皮疙瘩不良的方法,降低dcb产品不良率。
本发明的改进思路如下:根据研磨工序具备切削量的特性,可以完全去除表面的色差,绝大多数的疙瘩皱皮缺陷,回归原始铜表面的光洁;再经烧结工艺形成晶粒,使得产品晶粒和粗糙度与正常产品相当,焊接和打线性能和正常产品相当,可以大大降低色差、疙瘩及皱皮缺陷,一定程度上提升良率。
为了实现上述目的,本发明所采用的技术方案如下:
本发明提供了一种减少dcb产品皱皮疙瘩不良的方法,包括如下步骤:
a、研磨
采用刷辊对带有皱皮疙瘩的一面进行研磨,速度设置为0.8~1.0m/min,研磨量控制在7~12μm范围内,还原原始铜片表面的光亮,而后经纯水超声清洗去除研磨下来的异物;
b、烧结再结晶
将步骤a处理后得到的产品置于烧结炉内,并通入氮气和氧气混合气,在1075~1083℃条件下烧结,使铜片表面再结晶。
本发明中,在研磨阶段,控制研磨速度利于实现研磨均一性,研磨量既不能过大也不能过小,过大容易损伤产品正常表面,过小容易导致疙瘩去除不完全。在烧结再结晶阶段,氮气和氧气混合气作为模拟空气,烧结温度既不能过高也不能过低,过低难以实现结晶,过高则容易导致结晶度增高、粒径变大,与周边产品表面区别明显。
优选的,步骤a中,刷辊为不织布刷辊,目数分别为600、1500、2000、2000目四组。操作时,采用低目数至高目数刷辊依次进行操作,先去除大部分疙瘩,然后进行精细修饰。
优选的,步骤a中,进行研磨操作时,研磨电流为0.8-1.2a。
优选的,步骤a中,纯水超声清洗的工艺条件为:将产品放于插架中,依次通过两个槽体进行纯水超声清洗去除表面残留的异物,清洗时,使用45khz的超声震动,每次60s,而后烘干、冷却,去除粘附在硅片表面的异物。
优选的,步骤b中,氮气和氧气混合气中,氮气和氧气的体积比为2:8。
优选的,步骤b中,烧结温度优选为1080±2℃,温度控制越精确,再结晶状态越好。
本发明的有益效果如下:
本发明采用刷辊对存在异物的一面进行研磨,可以完全去除表面的色差,绝大多数的疙瘩皱皮缺陷,回归原始铜表面的光洁;然后在氧气和氮气混合气体氛围下,严格控制烧结温度在在1075~1083℃之间,实现产品晶粒和粗糙度与正常产品相当,焊接和打线性能和正常产品相当,可大大降低色差、疙瘩及皱皮缺陷,一定程度上提升良率,降低了产品报废率。
附图说明
图1为研磨后以及再结晶后铜片表面的状态图,a为研磨后,b为再结晶后。
具体实施方式
下面结合本发明的附图和实施例对本发明的实施作详细说明,以下实施例是在以本发明技术方案为前提下进行实施,给出了详细的实施方式和具体操作过程,但本发明的保护范围不限于下述的实施例。
实施例1减少dcb产品皱皮疙瘩不良的方法
a、研磨
采用刷辊对带有皱皮疙瘩的一面进行研磨,速度设置为0.8~1.0m/min,研磨电流为0.8-1.2a,研磨量控制在7~12μm范围内,还原原始铜片表面的光亮,而后经纯水超声清洗去除研磨下来的残留异物。
采用的刷辊为不织布刷辊,目数分别为600、1500、2000、2000目四组。操作时,采用低目数至高目数刷辊依次进行操作,先去除大部分疙瘩,然后进行精细修饰,既能去除大部分疙瘩缺陷,又能尽可能降低对疙瘩下铜片表面的缺陷。
纯水超声清洗的工艺条件为:将产品放于插架中,依次通过两个槽体进行纯水超声清洗去除表面残留的异物,清洗时,使用45khz的超声震动,每次60s,而后烘干、冷却,去除粘附在硅片表面的异物。
b、烧结再结晶
将步骤a处理后得到的产品置于烧结炉内,并通入体积比为2:8的氮气和氧气混合气,在1075~1083℃条件下烧结,使铜片表面再结晶。
该步骤中,烧结温度优选设定为1080℃,误差控制在±2℃,温度控制越精确,再结晶状态越好。
本实施例中,在研磨阶段,控制研磨速度利于实现研磨均一性,研磨量既不能过大也不能过小,过大容易损伤产品正常表面,过小容易导致疙瘩去除不完全。在烧结再结晶阶段,氮气和氧气混合气作为模拟空气,烧结温度既不能过高也不能过低,过低难以实现结晶,过高则容易导致结晶度增高、粒径变大,与周边产品表面区别明显。
根据图1,采用上述处理方法对带有皱皮疙瘩的dcb产品进行处理,研磨后铜片表面的皱皮疙瘩不良基本被去除,该处铜片表面光亮被还原(图1a);烧结再结晶后,该处铜片表面被重新形成晶粒,无论面观还是显微镜下观察,与周边正常铜片表面均无异,实现产品晶粒和粗糙度与正常产品相当(图1b)。
通过后续流程操作验证,通过本方法处理后的dcb不良产品,焊接和打线性能和正常产品相当,一定程度上提升良率,降低了产品报废率。
以上已对本发明创造的较佳实施例进行了具体说明,但本发明创造并不限于所述实施例,熟悉本领域的技术人员在不违背本发明创造精神的前提下还可作出种种的等同的变型或替换,这些等同的变型或替换均包含在
本技术:
权利要求所限定的范围内。
技术特征:1.一种减少dcb产品皱皮疙瘩不良的方法,其特征在于,包括如下步骤,
a、研磨
采用刷辊对带有皱皮疙瘩的一面进行研磨,速度设置为0.8~1.0m/min,研磨量控制在7~12μm范围内,而后经纯水超声清洗去除研磨下来的异物;
b、烧结再结晶
将步骤a处理后得到的产品置于烧结炉内,并通入氮气和氧气混合气,在1075~1083℃条件下烧结,使铜片表面再结晶。
2.根据权利要求1所述的减少dcb产品皱皮疙瘩不良的方法,其特征在于:
其中,步骤a中,所述刷辊为不织布刷辊,目数分别为600、1500、2000、2000目四组。
3.根据权利要求1所述的减少dcb产品皱皮疙瘩不良的方法,其特征在于:
其中,步骤a中,进行研磨操作时,研磨电流为0.8-1.2a。
4.采用权利要求1中的减少dcb产品皱皮疙瘩不良的方法,其特征在于:
其中,纯水超声清洗的工艺条件为:将产品放于插架中,依次通过两个槽体进行纯水超声清洗去除表面残留的异物,清洗时,使用45khz的超声震动,每次60s,而后烘干、冷却。
5.根据权利要求1所述的减少dcb产品皱皮疙瘩不良的方法,其特征在于:
其中,步骤b中,氮气和氧气混合气中,氮气和氧气的体积比为2:8。
6.根据权利要求1所述的减少dcb产品皱皮疙瘩不良的方法,其特征在于:
其中,步骤b中,烧结温度为1080±2℃。
技术总结本发明涉及一种减少DCB产品皱皮疙瘩不良的方法,包括如下步骤:A、研磨:采用刷辊对带有皱皮疙瘩的一面进行研磨,速度设置为0.8~1.0m/min,研磨量控制在7~12μm范围内,还原原始铜片表面的光亮,而后经纯水超声清洗去除研磨下来的异物;B、烧结再结晶:将步骤A处理后得到的产品置于烧结炉内,并通入氮气和氧气混合气,在1075~1083℃条件下烧结,使铜片表面再结晶。研磨可以完全去除表面的色差,绝大多数的疙瘩皱皮缺陷,回归原始铜表面的光洁;再结晶实现产品晶粒和粗糙度与正常产品相当,焊接和打线性能和正常产品相当,一定程度上提升良率,降低了产品报废率。
技术研发人员:蔡俊;贺贤汉;马敬伟;陈元华
受保护的技术使用者:江苏富乐德半导体科技有限公司
技术研发日:2021.03.17
技术公布日:2021.08.06