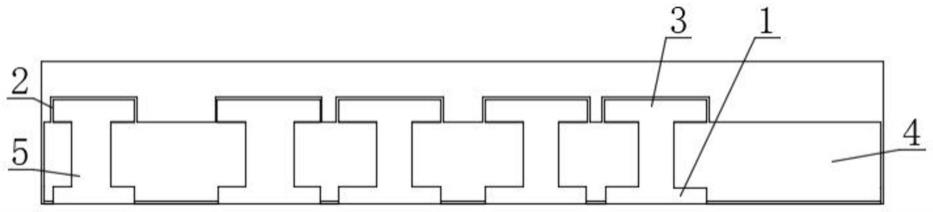
预注塑式无焊盘qfn封装基板
技术领域
1.本发明涉及封装基板领域,更具体地说,涉及预注塑式无焊盘qfn封装基板。
背景技术:2.封装基板是substrate(简称sub)。基板可为芯片提供电连接、保护、支撑、散热、组装等功效,以实现多引脚化,缩小封装产品体积、改善电性能及散热性、超高密度或多芯片模块化的目的。封装基板应该属于交叉学科的技术,它涉及到电子、物理、化工等知识。
3.现有的封装基板存在以下问题:1、现在qfn/dfn封装结构主要是通过蚀刻工艺做出芯片线路以及焊盘线路,封装工艺过程中需要把芯片固接到焊盘上面以及底部粘贴高温胶带防止塑封工艺过程中的漏胶问题。
4.2.现有封装结构因为有焊盘的存在,增加了封装体的尺寸,继续缩小封装体的尺寸变得不可能,背贴膜的工艺增加了封装成本,降低了封装效率。
技术实现要素:5.针对现有技术中存在的问题,本发明的目的在于提供预注塑式无焊盘qfn封装基板,以解决封装效率低、封装效果差与封装成本高的问题。
6.为解决上述问题,本发明采用如下的技术方案。
7.预注塑式无焊盘qfn封装基板,包括焊盘,所述焊盘上通过蚀刻得到焊线线路,所述焊线线路上设置有均与分布的引脚,相邻的两个所述引脚之间的间隙在0.07~0.1mm之间,所述引脚的数量与待封装芯片相匹配,所述焊盘上注塑有填充层,所述焊线线路与引脚的表面均电镀有铜金属层,所述铜金属层与焊线线路之间、焊线线路与填充层之间均粗糙连接。
8.作为上述技术方案的进一步描述:所述焊盘由合金铜材制成,所述填充层由环氧树脂注塑而成。
9.作为上述技术方案的进一步描述:所述合金铜材的厚度为6~8mil。
10.作为上述技术方案的进一步描述:本发明还提出了,该预注塑式无焊盘qfn封装基板的制造工艺,包括以下流程:步骤一、将合金铜材把芯片的线路图蚀刻出来,只是蚀刻部分材料,引脚间隙在0.07~0.1mm之间,具体的引脚数目取决于asic或者芯片的设计,形成焊盘;步骤二、用传递塑模的方法把具有优良特性的环氧树脂材料注塑到蚀刻部分铜材的线路表面,得到部分填充层;步骤三、通过打磨把已经被塑封胶料掩盖的线路磨出来;步骤四、把没有做过蚀刻工艺另外合金铜材作为焊盘的线路蚀刻出来,形成引脚;步骤五、用传统的塑封模的方法把具有优良特性的环氧树脂材料注塑到蚀刻剩余
铜材的焊线线路表面,形成完整填充层;步骤六、在整个焊线线路表面进行铜材料电镀,使其整个表面金属化;步骤七、在金属化的表面进行功能芯片封装线路的蚀刻;步骤八、进行功能芯片的封装和塑封保护;步骤九、单颗成型分切。
11.作为上述技术方案的进一步描述:所述步骤一中通过掩饰模的设计,完整覆盖到整个合金铜板上面,利用uv或者激光把线路覆盖膜活化形成线路结构。
12.作为上述技术方案的进一步描述:所述步骤二中在传塑过程中选用低于50um填充的化合物的材料以利于在复杂的asic设计中的超细引脚间填充充分的结构。
13.相比于现有技术,本发明的优点在于:(1)本方案,采用了多层蚀刻的技术,能够缩小引线间距和线宽到0.07~0.1mm之间,同时采用了预先注塑的工艺,在没有焊盘的情况下可以固晶缩小整体封装尺寸,同时也可以减掉背贴高温膜的工艺,降低成本和增加效率。
14.(2)本方案,预留半蚀刻的位置以及表面粗化的结构增加不同材料的界面结合性,增强封装基板之间不同层材料的结构连接稳定性,提高其使用寿命。
附图说明
15.图1为本发明的正视剖视结构示意图;图2为本发明的制备流程示意图。
16.图中标号说明:1、焊盘;2、焊线线路;3、引脚;4、填充层;5、铜金属层。
具体实施方式
17.下面将结合本发明实施例中的附图,对本发明实施例中的技术方案进行清楚、完整地描述;请参阅图1,本发明中,预注塑式无焊盘qfn封装基板,包括焊盘1,焊盘1上通过蚀刻得到焊线线路2,焊线线路2上设置有均与分布的引脚3,相邻的两个引脚3之间的间隙在0.07~0.1mm之间,引脚3的数量与待封装芯片相匹配,焊盘1上注塑有填充层4,焊线线路2与引脚3的表面均电镀有铜金属层5,铜金属层5与焊线线路2之间、焊线线路2与填充层4之间均粗糙连接。
18.请参阅图1,其中:焊盘1由合金铜材制成,填充层4由环氧树脂注塑而成。
19.请参阅图1,其中:合金铜材的厚度为6~8mil。
20.请参阅图1与图2,其中:该预注塑式无焊盘qfn封装基板的制造工艺,包括以下流程:步骤一、将合金铜材把芯片的线路图蚀刻出来,只是蚀刻部分材料,引脚3间隙在0.07~0.1mm之间,具体的引脚3数目取决于asic或者芯片的设计,形成焊盘1;步骤二、用传递塑模的方法把具有优良特性的环氧树脂材料注塑到蚀刻部分铜材
的线路表面,得到部分填充层4;步骤三、通过打磨把已经被塑封胶料掩盖的线路磨出来;步骤四、把没有做过蚀刻工艺另外合金铜材作为焊盘1的线路蚀刻出来,形成引脚3;步骤五、用传统的塑封模的方法把具有优良特性的环氧树脂材料注塑到蚀刻剩余铜材的焊线线路2表面,形成完整填充层4;步骤六、在整个焊线线路2表面进行铜材料电镀,使其整个表面金属化;步骤七、在金属化的表面进行功能芯片封装线路的蚀刻;步骤八、进行功能芯片的封装和塑封保护;步骤九、单颗成型分切。
21.请参阅图1与图2,其中:步骤一中通过掩饰模的设计,完整覆盖到整个合金铜板上面,利用uv或者激光把线路覆盖膜活化形成线路结构。
22.请参阅图1与图2,其中:步骤二中在传塑过程中选用低于50um填充的化合物的材料以利于在复杂的asic设计中的超细引脚3间填充充分的结构。
23.请参阅图1与图2,其中:所述步骤四中蚀刻完成后选择对焊盘1线路与引脚3的表面粗化处理。
24.请参阅图1与图2,其中:所述步骤五中注塑完成后对注塑表面进行打磨,所述步骤六中电镀完成后对电镀层表面进行打磨。
25.采用了多层蚀刻的技术,能够缩小引线间距和线宽到0.07~0.1mm之间,同时采用了预先注塑的工艺,在没有焊盘1的情况下可以固晶缩小整体封装尺寸,同时也可以减掉背贴高温膜的工艺,降低成本和增加效率,预留半蚀刻的位置以及表面粗化的结构增加不同材料的界面结合性,增强封装基板之间不同层材料的结构连接稳定性,提高其使用寿命。
26.以上所述,仅为本发明较佳的具体实施方式;但本发明的保护范围并不局限于此。任何熟悉本技术领域的技术人员在本发明揭露的技术范围内,根据本发明的技术方案及其改进构思加以等同替换或改变,都应涵盖在本发明的保护范围内。
技术特征:1.预注塑式无焊盘qfn封装基板,其特征在于:包括焊盘(1),所述焊盘(1)上通过蚀刻得到焊线线路(2),所述焊线线路(2)上设置有均与分布的引脚(3),相邻的两个所述引脚(3)之间的间隙在0.07~0.1mm之间,所述引脚(3)的数量与待封装芯片相匹配,所述焊盘(1)上注塑有填充层(4),所述焊线线路(2)与引脚(3)的表面均电镀有铜金属层(5),所述铜金属层(5)与焊线线路(2)之间、焊线线路(2)与填充层(4)之间均粗糙连接。2.根据权利要求1所述的预注塑式无焊盘qfn封装基板,其特征在于:所述焊盘(1)由合金铜材制成,所述填充层(4)由环氧树脂注塑而成。3.根据权利要求2所述的预注塑式无焊盘qfn封装基板,其特征在于:所述合金铜材的厚度为6~8mil。4.根据权利要求1-3任一所述的预注塑式无焊盘qfn封装基板,其特征在于:该预注塑式无焊盘qfn封装基板的制造工艺,包括以下流程:步骤一、将合金铜材把芯片的线路图蚀刻出来,只是蚀刻部分材料,引脚(3)间隙在0.07~0.1mm之间,具体的引脚(3)数目取决于asic或者芯片的设计,形成焊盘(1);步骤二、用传递塑模的方法把具有优良特性的环氧树脂材料注塑到蚀刻部分铜材的线路表面,得到部分填充层(4);步骤三、通过打磨把已经被塑封胶料掩盖的线路磨出来;步骤四、把没有做过蚀刻工艺另外合金铜材作为焊盘(1)的线路蚀刻出来,形成引脚(3);步骤五、用传统的塑封模的方法把具有优良特性的环氧树脂材料注塑到蚀刻剩余铜材的焊线线路(2)表面,形成完整填充层(4);步骤六、在整个焊线线路(2)表面进行铜材料电镀,使其整个表面金属化;步骤七、在金属化的表面进行芯片封装线路的蚀刻;步骤八、进行功能芯片的封装和塑封保护;步骤九、单颗成型分切。5.根据权利要求4所述的预注塑式无焊盘qfn封装基板,其特征在于:所述步骤一中通过掩饰模的设计,完整覆盖到整个合金铜板上面,利用uv或者激光把线路覆盖膜活化形成线路结构。6.根据权利要求4所述的预注塑式无焊盘qfn封装基板,其特征在于:所述步骤二中在传塑过程中选用低于50um填充的化合物的材料以利于在复杂的asic设计中的超细引脚(3)间填充充分的结构。7.根据权利要求4所述的预注塑式无焊盘qfn封装基板,其特征在于:所述步骤四中蚀刻完成后选择对焊盘(1)线路与引脚(3)的表面粗化处理。8.根据权利要求4所述的预注塑式无焊盘qfn封装基板,其特征在于:所述步骤五中注塑完成后对注塑表面进行打磨,所述步骤六中电镀完成后对电镀层表面进行打磨。
技术总结本发明公开了预注塑式无焊盘QFN封装基板,属于封装基板领域,预注塑式无焊盘QFN封装基板,包括焊盘,所述焊盘上通过蚀刻得到焊线线路,所述焊线线路上设置有均与分布的引脚,相邻的两个所述引脚之间的间隙在0.07~0.1mm之间,所述引脚的数量与带封装芯片相匹配,所述焊盘上注塑有填充层,所述焊线线路与引脚的表面均电镀有铜金属层,所述铜金属层与焊线线路之间、焊线线路与填充层之间均粗糙连接。本发明,采用了多层蚀刻的技术,能够缩小引线间距和线宽到0.07~0.1mm之间,同时采用了预先注塑的工艺,在没有焊盘的情况下可以固晶缩小整体封装尺寸,同时也可以减掉背贴高温膜的工艺,降低成本和增加效率。降低成本和增加效率。降低成本和增加效率。
技术研发人员:银光耀
受保护的技术使用者:深圳市唯亮光电科技有限公司
技术研发日:2021.11.26
技术公布日:2022/2/11