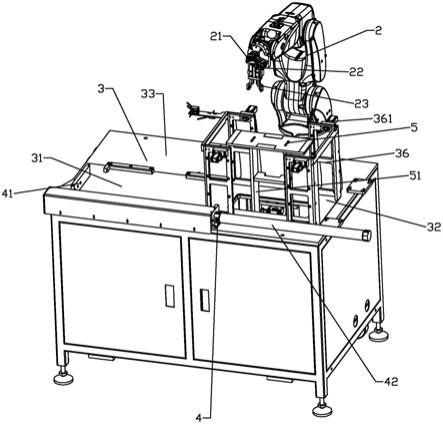
1.本实用新型涉及小型断路器自动装配设备领域,具体涉及一种小型断路器自动装配设备的双金属片总成装配装置。
背景技术:2.小型断路器是一种指能接通、承载以及分断正常电路条件下的电流,也能在规定的非正常电路条件下接通、承载一定时间和分断电流的机械开关电器。
3.为了提高小型断路器的装配效率,小型断路器的装配往往由流水线将内部零件逐个装入外壳内,特别是,受限于双金属片总成的复杂结构,双金属片总成局部由柔性的线缆连接,其与锁扣之间的装配只能依赖于人工进行装配,进而导致装配效率降低。
技术实现要素:4.针对现有技术存在的不足,本实用新型的目的在于提供一种在装配锁扣的同时自动装配双金属片总成,省去因人工将双金属片总成装装配于锁扣,从而提高装配效率的小型断路器自动装配设备的双金属片总成装配装置。
5.为实现上述目的,本实用新型提供了如下技术方案:包括料盘、装配机械臂及装配平台,所述的料盘设置有用于放置双金属片总成的取料槽,所述的装配平台设置有用于堆叠料盘并与装配机械臂位置相错的待装配位置、用于堆叠料盘并与装配机械臂位置相对的装配位置及用于堆叠空料盘的料盘回收位置,所述的装配机械臂前端设置有第一夹爪、第二夹爪及第三夹爪,所述的第一夹爪及第二夹爪分别用于夹持双金属片总成的两端,并将双金属片总成从装配位置夹持并装配至对应半成品,所述的第三夹爪限位于取料槽构成对料盘的夹持,将位于装配位置的空料盘转移至料盘回收位置,所述的装配平台设置有将料盘从待装配位置推移至装配位置的推移装置。
6.通过采用上述技术方案,由料盘作为双金属片总成的载体,由第一夹爪及第二夹爪进行配合的方式,稳定夹持双金属片总成的复杂结构,从而实现其转移及装配步骤,同时,装配平台还具有待装配位置、装配位置及料盘回收位置,待装配位置用于保证双金属片总成的及时补充,机械臂前端的第三夹爪则进一步将空料盘转移功能的集成于机械臂,在料盘的各个双金属片总成取走后及时将料盘转移,保证装配的高效。
7.本实用新型进一步设置为:所述的推移装置设置有位于待装配位置相对装配位置另一侧的推板及驱动推板沿待装配位置及装配位置排布方向移动的推板侧移机构,所述的待装配位置及装配位置两侧分别设置有对料盘移动进行导向的导向块,所述的装配平台位于装配位置相对待装配位置的另一侧设置有与料盘限位配合的限位块。
8.通过采用上述技术方案,导向块配合限位块,保证推板稳定推动俩盘从待装配位置至装配位置的同时能够准确到位,保证装配位置的料盘在取走后能够快速、补充后续的双金属片总成。
9.本实用新型进一步设置为:所述的装配平台位于装配位置设置有支撑于料盘底部
的顶升板及驱动顶升板升降的升降驱动机构,所述的导向块及限位块向上延伸形成供料盘上升的上升通道。
10.通过采用上述技术方案,堆叠的料盘在位于最上端的空料盘被取走后能够自动上升,减少机械臂在取下一双金属片总成的移动幅度,从而提高装配效率,合理利用导向块及限位块,延伸形成上升通道,提高料盘在上升过程中的稳定性。
11.本实用新型进一步设置为:所述的上升通道的顶部侧面设置有将料盘进行限位的限位气缸。
12.通过采用上述技术方案,增设限位气缸,对位于最高位置的料盘进行限位,保证机械臂能够稳定取走双金属片总成。
附图说明
13.图1为放置有双金属总成的料盘;
14.图2为本实用新型具体实施方式的立体图。
具体实施方式
[0015] 下面将结合附图对本发明的技术方案进行清楚、完整地描述, 显然,所描述的实施例是本发明一部分实施例,而不是全部的实施例。 基于本发明中的实施例,本领域普通技术人员在没有做出创造性劳动前提下所获得的所有其他实施例,都属于本发明保护的范围。
[0016]
在本发明的描述中,需要说明的是,术语“中心”、“上
”ꢀ
、“下
”ꢀ
、“左”、“右”、“竖直”、“水平”、“内”、“外”等指示的方位或位置关系为基于附图所示的方位或位置关系, 仅是为了便于描述本发明和简化描述,而不是指示或暗示所指的装置或元件必须具有特定的方位、以特定的方位构造和操作,因此不能理解为对本发明的限制。此外,术语
ꢀ“
第一”、“第二”、“第三
”ꢀ
仅用于描述目的,而不能理解为指示或暗示相对重要性。
[0017]
如图1—图2所示,本实用新型公开了一种小型断路器自动装配设备的双金属片总成装配装置,包括料盘1、装配机械臂2及装配平台3,料盘1设置有用于放置双金属片总成的取料槽11,装配平台3设置有用于堆叠料盘1并与装配机械臂2位置相错的待装配位置31、用于堆叠料盘1并与装配机械臂2位置相对的装配位置32及用于堆叠空料盘1的料盘回收位置33,装配机械臂2前端设置有第一夹爪21、第二夹爪22及第三夹爪23,第一夹爪21及第二夹爪22分别用于夹持双金属片总成的两端,并将双金属片总成从装配位置32夹持并装配至对应半成品,第三夹爪23限位于取料槽11构成对料盘1的夹持,将位于装配位置32的空料盘1转移至料盘回收位置33,装配平台3设置有将料盘1从待装配位置31推移至装配位置32的推移装置4,由料盘1作为双金属片总成的载体,由第一夹爪21及第二夹爪22进行配合的方式,稳定夹持双金属片总成的复杂结构,从而实现其转移及装配步骤,同时,装配平台3还具有待装配位置31、装配位置32及料盘回收位置33,待装配位置31用于保证双金属片总成的及时补充,机械臂前端的第三夹爪23则进一步将空料盘1转移功能的集成于机械臂,在料盘1的各个双金属片总成取走后及时将料盘1转移,保证装配的高效。
[0018]
推移装置4设置有位于待装配位置31相对装配位置32另一侧的推板41及驱动推板41沿待装配位置31及装配位置32排布方向移动的推板侧移机构42,侧移机构选择气缸,待
装配位置31及装配位置32两侧分别设置有对料盘1移动进行导向的导向块34,装配平台3位于装配位置32相对待装配位置31的另一侧设置有与料盘1限位配合的限位块35,导向块34配合限位块35,保证推板41稳定推动俩盘从待装配位置31至装配位置32的同时能够准确到位,保证装配位置32的料盘1在取走后能够快速、补充后续的双金属片总成。
[0019]
装配平台3位于装配位置32设置有支撑于料盘1底部的顶升板5及驱动顶升板5升降的升降驱动机构51,升降驱动机构51选择气缸,导向块34及限位块35向上延伸形成供料盘1上升的上升通道36,堆叠的料盘1在位于最上端的空料盘1被取走后能够自动上升,减少机械臂在取下一双金属片总成的移动幅度,从而提高装配效率,合理利用导向块34及限位块35,延伸形成上升通道36,提高料盘1在上升过程中的稳定性。
[0020]
上升通道36的顶部侧面设置有将料盘进行限位的限位气缸361,增设限位气缸361,对位于最高位置的料盘进行限位,保证机械臂能够稳定取走双金属片总成。
技术特征:1.一种小型断路器自动装配设备的双金属片总成装配装置,其特征在于:包括料盘、装配机械臂及装配平台,所述的料盘设置有用于放置双金属片总成的取料槽,所述的装配平台设置有用于堆叠料盘并与装配机械臂位置相错的待装配位置、用于堆叠料盘并与装配机械臂位置相对的装配位置及用于堆叠空料盘的料盘回收位置,所述的装配机械臂前端设置有第一夹爪、第二夹爪及第三夹爪,所述的第一夹爪及第二夹爪分别用于夹持双金属片总成的两端,并将双金属片总成从装配位置夹持并装配至对应半成品,所述的第三夹爪限位于取料槽构成对料盘的夹持,将位于装配位置的空料盘转移至料盘回收位置,所述的装配平台设置有将料盘从待装配位置推移至装配位置的推移装置。2.根据权利要求1所述的小型断路器自动装配设备的双金属片总成装配装置,其特征在于:所述的推移装置设置有位于待装配位置相对装配位置另一侧的推板及驱动推板沿待装配位置及装配位置排布方向移动的推板侧移机构,所述的待装配位置及装配位置两侧分别设置有对料盘移动进行导向的导向块,所述的装配平台位于装配位置相对待装配位置的另一侧设置有与料盘限位配合的限位块。3.根据权利要求2所述的小型断路器自动装配设备的双金属片总成装配装置,其特征在于:所述的装配平台位于装配位置设置有支撑于料盘底部的顶升板及驱动顶升板升降的升降驱动机构,所述的导向块及限位块向上延伸形成供料盘上升的上升通道。4.根据权利要求3所述的小型断路器自动装配设备的双金属片总成装配装置,其特征在于:所述的上升通道的顶部侧面设置有将料盘进行限位的限位气缸。
技术总结本实用新型涉及一种小型断路器自动装配设备的双金属片总成装配装置,包括料盘、装配机械臂及装配平台,料装配平台设置有待装配位置、装配位置及料盘回收位置,装配机械臂前端设置有第一夹爪、第二夹爪及第三夹爪,第一夹爪及第二夹爪分别用于夹持双金属片总成的两端,并将双金属片总成从装配位置夹持并装配至对应半成品,第三夹爪限位于取料槽构成对料盘的夹持,将位于装配位置的空料盘转移至料盘回收位置,装配平台设置有推移装置。采用上述方案,本实用新型提供一种在装配锁扣的同时自动装配双金属片总成,省去因人工将双金属片总成装装配于锁扣,从而提高装配效率的小型断路器自动装配设备的双金属片总成装配装置。自动装配设备的双金属片总成装配装置。自动装配设备的双金属片总成装配装置。
技术研发人员:张辉
受保护的技术使用者:浙江华术自动化科技有限公司
技术研发日:2021.03.03
技术公布日:2021/10/8