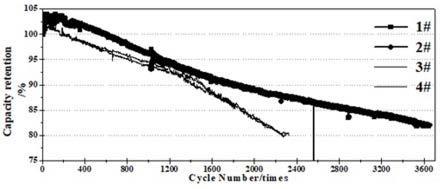
1.本发明属于锂离子电池技术领域,涉及一种改善锂离子电池浸润性的方法。
背景技术:2.目前储能和动力电池主要分为磷酸铁锂电池和三元电池两大主流,能量密度、循环寿命和安全性能是锂离子电池的三大关键指标。其中磷酸铁锂电池所具有的高安全和长循环等特性逐渐成新能源领域的目标。
3.尽管如此,磷酸铁锂电池能量密度低的特点也制约了其在新能源领域的发展,磷酸铁锂理论比容量低,目前实际比容量较理论比容量差距小,比容量提升空间有限,磷酸铁锂电池提升能量密度的路线主要向极片高压实方向发展,高压实磷酸铁锂材料以及高压实极片的吸液和保液能力大幅降低,电性能下降,尤其是循环寿命随着吸液和保液能力的降低而大幅度降低,阻碍了磷酸铁锂电池在高能量长寿命需求领域的发展,改善高压实磷酸铁锂电池的吸液和保液能力,可以大幅度提高磷酸铁锂电池的应用范围。
技术实现要素:4.本发明的目的是提供一种改善锂离子电池浸润性的方法,解决的高能量磷酸铁锂电池吸液和保液能力问题,从而提高高能量磷酸铁锂电池循环性能。
5.本发明改善锂离子电池浸润性的方法,包括如下步骤,1)将辊压后的磷酸铁锂正极片拉平后定位;2)用激光进行极片正反面纵向刻蚀,在极片表面构建出磷酸铁锂极片电解液传输微通道;3)激光刻蚀过程中对极片刻蚀部位进行抽真空除尘;4)利用静电植绒技术将活性炭材料植入微通道中。
6.根据所述的改善锂离子电池浸润性的方法,刻蚀控制微通道宽度5μm~10μm,微通道深度10μm-20μm。
7.根据所述的改善锂离子电池浸润性的方法,刻蚀微通道纵向垂直贯穿极片表面,极片表面微通道间距5cm-10cm。
8.根据所述的改善锂离子电池浸润性的方法,活性炭植入厚度5μm-10μm,活性炭比表面积1500m2/g-2500 m2/g,细孔容积0.7 ml/g
ꢀ‑
1.0ml/g。
9.根据所述的改善锂离子电池浸润性的方法,激光刻蚀时极片正反面对齐,且刻蚀位置相同。
10.根据所述的改善锂离子电池浸润性的方法,所述锂离子电池为圆柱锂电池电池,磷酸铁锂正极片的箔材厚度12μm
±
1μm,磷酸铁锂材料单面厚度μm
±
2μm。
11.根据所述的改善锂离子电池浸润性的方法,控制微通道宽度8μm
±
1μm,微通道深度15μm
±
1μm,刻蚀微通道纵向垂直贯穿极片,极片表面微通道间距6cm
±
0.2cm。
12.根据所述的改善锂离子电池浸润性的方法,活性炭植入厚度8μm
±
1μm,活性炭比
表面积1800m2/g
±
200 m2/g,细孔容积0.7ml/g
ꢀ‑
1.0ml/g。
13.本发明的优点与效果是:1、该发明将辊压后的磷酸铁锂正极片拉平后定位,用激光进行极片正反面对齐同时纵向刻蚀,对极片进行正反面对齐同时纵向刻蚀,刻蚀效率高,且极片正反面刻蚀位置相同,避免了极片因正反面张力不均引起极片打皱。
14.2、利用静电植绒技术将活性炭材料植入微通道,电解液以活性炭为载体传输到微通道供给极片足够的电解液,活性炭比表面积大,吸液和保液能力强,大幅度提高极片浸润性。
附图说明
15.图1为实施例中未经激光刻蚀和活性炭植入的正极片以及经过激光刻蚀和活性炭植入的正极片制作电池1c充放电循环性能曲线。
16.图1中,1#、2#为经过激光刻蚀和活性炭植入的正极片制作电池,3#、4#为未经过激光刻蚀和活性炭植入的正极片制作电池。
具体实施方式
17.下面对本发明的具体内容进行进一步的说明:本发明改善锂离子电池浸润性的方法,其步骤是:首先将辊压后的磷酸铁锂正极片拉平后定位,用激光进行极片正反面对齐同时纵向刻蚀,在极片表面构建出磷酸铁锂极片电解液传输微通道,控制微通道宽度5μm~10μm,微通道深度10μm-20μm,刻蚀微通道纵向垂直贯穿极片,极片表面微通道间距5cm-10cm。
18.激光刻蚀过程需要对极片进行正反面对齐,然后同时纵向刻蚀,刻蚀效率高,且极片正反面刻蚀位置相同,避免了极片因正反面张力不均引起极片打皱。
19.激光刻蚀过程中对极片刻蚀部位进行抽真空除尘,保证极片表面粉尘合格。
20.然后利用静电植绒技术将活性炭材料植入微通道,活性炭植入厚度5μm-10μm,活性炭比表面积1500m2/g-2500 m2/g,细孔容积0.7 ml/g
ꢀ‑
1.0ml/g,电解液以活性炭为载体传输到微通道供给极片足够的电解液,活性炭比表面积大,吸液和保液能力强,大幅度提高极片浸润性。
21.通过具体实时参数对本发明进行实施例说明;1)首先将辊压后的18650-2000mah-3.2v磷酸铁锂正极片拉平后定位,正极片箔材厚度12μm
±
1μm,磷酸铁锂材料单面厚度140μm
±
2μm;2)用激光进行极片正反面对齐同时纵向刻蚀,在极片表面构建出磷酸铁锂极片电解液传输微通道;3)控制微通道宽度8μm
±
1μm,微通道深度15μm
±
1μm,刻蚀微通道纵向垂直贯穿极片,极片表面微通道间距6cm
±
0.2cm。
22.4)激光刻蚀过程中对极片刻蚀部位进行抽真空除尘。
23.5)然后利用静电植绒技术将活性炭材料植入微通道,活性炭植入厚度8μm
±
1μm,活性炭比表面积1800m2/g
±
200 m2/g,细孔容积0.7ml/g
ꢀ‑
1.0ml/g。
24.电解液以活性炭为载体传输到微通道供给极片足够的电解液,活性炭比表面积
大,吸液和保液能力强,大幅度提高极片浸润性。
25.经过激光刻蚀和活性炭植入的正极片制备18650-2000mah-3.2v,1c充放循环寿命提高30%以上,未经激光刻蚀和活性炭植入的正极片以及经过激光刻蚀和活性炭植入的正极片制作电池1c充放循环寿命曲线如图1所示。
26.图1中,1#、2#为经过激光刻蚀和活性炭植入的正极片制作电池,3#、4#为未经过激光刻蚀和活性炭植入的正极片制作电池。
27.本发明利用激光进行极片正反面对齐同时纵向刻蚀,对极片进行正反面对齐同时纵向刻蚀,刻蚀效率高,且极片正反面刻蚀位置相同,避免了极片因正反面张力不均引起极片打皱。
28.本发明利用静电植绒技术将活性炭材料植入微通道,电解液以活性炭为载体传输到微通道供给极片足够的电解液,活性炭比表面积大,吸液和保液能力强,大幅度提高极片浸润性。
技术特征:1.一种改善锂离子电池浸润性的方法,其特征是,包括如下步骤,将辊压后的磷酸铁锂正极片拉平后定位;用激光进行极片正反面纵向刻蚀,在极片表面构建出磷酸铁锂极片电解液传输微通道;激光刻蚀过程中对极片刻蚀部位进行抽真空除尘;利用静电植绒技术将活性炭材料植入微通道中。2.根据权利要求1所述的改善锂离子电池浸润性的方法,其特征是,刻蚀控制微通道宽度5μm~10μm,微通道深度10μm-20μm。3.根据权利要求1所述的改善锂离子电池浸润性的方法,其特征是,刻蚀微通道纵向垂直贯穿极片表面,极片表面微通道间距5cm-10cm。4.活性炭植入厚度5μm-10μm,活性炭比表面积1500m2/g-2500 m2/g,细孔容积0.7 ml/g
ꢀ‑
1.0ml/g。5.根据权利要求1所述的改善锂离子电池浸润性的方法,其特征是,激光刻蚀时极片正反面对齐,且刻蚀位置相同。6.根据权利要求1所述的改善锂离子电池浸润性的方法,其特征是,所述锂离子电池为圆柱锂电池电池,磷酸铁锂正极片的箔材厚度12μm
±
1μm,磷酸铁锂材料单面厚度140μm
±
2μm。7.根据权利要求6所述的改善锂离子电池浸润性的方法,其特征是,控制微通道宽度8μm
±
1μm,微通道深度15μm
±
1μm,刻蚀微通道纵向垂直贯穿极片,极片表面微通道间距6cm
±
0.2cm。8.根据权利要求4所述的改善锂离子电池浸润性的方法,其特征是,活性炭植入厚度8μm
±
1μm,活性炭比表面积1800m2/g
±
200 m2/g,细孔容积0.7ml/g
ꢀ‑
1.0ml/g。
技术总结本发明属于锂离子电池技术领域,涉及一种改善锂离子电池浸润性的方法。将辊压后的磷酸铁锂正极片拉平后定位,用激光进行极片正反面对齐同时纵向刻蚀,在极片表面构建出磷酸铁锂极片电解液传输微通道,然后利用静电植绒技术将活性炭材料植入微通道,电解液以活性炭为载体传输到微通道供给极片足够的电解液,活性炭比表面积大,吸液和保液能力强,大幅度提高极片浸润性。片浸润性。片浸润性。
技术研发人员:王勇 张敬捧 邵长旺
受保护的技术使用者:山东精工电子科技股份有限公司
技术研发日:2022.12.08
技术公布日:2023/1/19