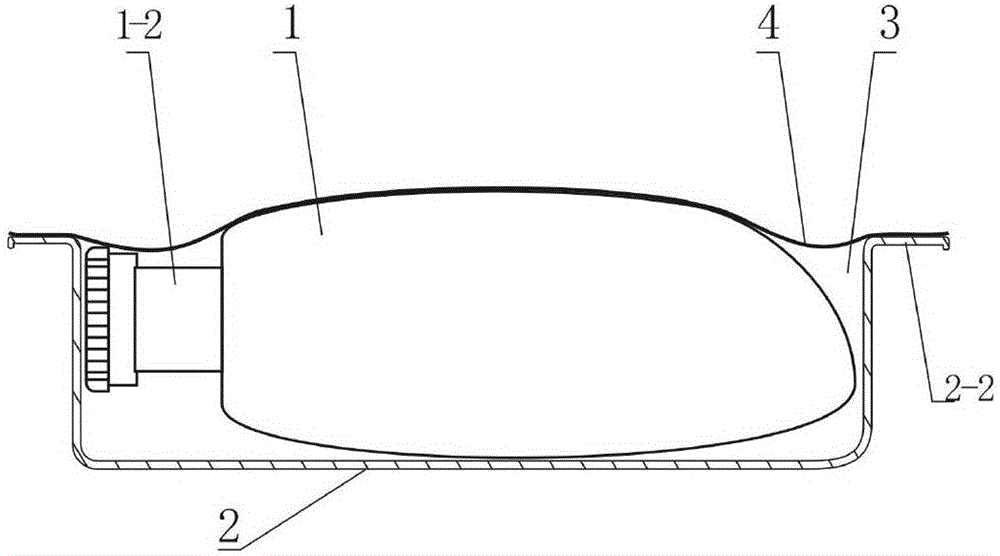
本实用新型涉及到一种制药生产企业的液体制剂产品包装。
背景技术:
:安全用药是关乎人民生命健康安全的重要事项,也是关系到用药的医院及制药企业生存的重要事项。因此,药品安全是医院与制药企业的重中之重,是医院与制药企业的生命。液体制剂为药品中的一种,常用的液体制剂包括:口服制剂、冲洗消毒制剂、输液制剂、针剂等。液体制剂通常采用玻璃瓶、塑料瓶及软膜制袋包装,软膜制袋包装或质地非常软的塑料瓶包装称之为软性包装,软性包装通常采用装药部分与盖体焊接为一体的包装形式。上述制剂在生产包装、仓库搬运、运输、使用过程中,都要防止包装中的药剂与外界接触而被污染。但如果包装本身存在破损的情况下,则需要将被破坏了包装的制剂剔除,而破坏的原因与破坏的部位是多样性的。查找已被破坏包装,目前存在一种方法:在软性包装的外面再套上一个软胶外袋,然后在软胶外袋中抽取负压并密封胶袋,利用负压对软性包装的作用,将软性包装内的制剂从破坏处压出并形成肉眼可见的水斑,从而用肉眼发现被破坏的包装,以便将此产品剔除。但是,经过申请人长期对上述技术进行研究与试验,发现上述方法难以实现,尤其是根本无法运用于工业自动化生产,原因如下:一、破坏产品,使产品合格率低。在上述方法中,需要软胶外袋内有足够的负压作用力。负压作用力却存在极大负面影响:1、软胶外袋收缩产生极大变形;变形后极其不美观;变形后极易被撕裂。2、抽负压后软胶外袋的袋口向内急剧收缩挤压,产生大量的折皱,使袋口难以封边焊接,造成所焊接不良,产生漏气孔,无法保证软胶外袋内的负压值。3、软胶外袋收缩变形后,对内装的软性包装产生极大作用力,压迫、扭曲、拉扯软性包装,软性内袋的盖体与软膜焊合处则可能被撕裂。尤其是盖体的颈部容易被折断。因此,以提高产品出厂合格率为目的包装方式则有可能演变为对产品的主动破坏。二、无法自动化。由于需要将软性包装套入软胶外袋中,该步骤必须采用工人手工撕开软胶袋口,然后将软性包装套入软胶外袋中,因此难以找到合适的机械设备自动化完成。将软胶袋摆放于负压机(真空机)平台上的动作必须由人工完成,因为胶袋外形随机且柔软,目前是没有自动化的设备能完成对软胶袋的摆放的。对该产品的成品装箱也无法自动化,因为该产品变形极大,形状扭曲,必须使用人工装箱。因此,该技术实现生产自动化难度大。而药剂包装必须能实现自动化生产,否则该技术便没有意义,其原因在于:自动化生产减少人工干预,提高合格率,保证用药安全。并且该产品生产量极大,即使一个中小型企业每天生产量也达到3万只(袋),年产1000万;中大型企业日产量则可达100万只(袋)以上,年产10亿以上,如果该技术无法实现自动化生产则根本无意义。因此,如果不能实现自动化,则不能满足市场用量,并造成人工成本高,工人劳动量大,从而产品的总体成本高。三、合格率低,成本高。因抽取负压后,内装的软性包装受到挤压和扭曲,产生较强的应力。如果盖体较脆(某些药剂须将盖体设计成易拆断式),在后期的运输和搬运、码放时则较易拆断,产生大量废品,降低了产品合格率,提高成本。四、使用现场不好码放。在医院的药房、药品柜、护士台上需要摆放大量的药剂。因为该产品变形极大,形状扭曲,所以无法进行有效整齐地摆放,造成医疗现场混乱,影响医疗。五、软胶外袋中抽取负压后负压所保存时间不够。因外袋为软胶性质材料,塑性变形量大,在抽取负压后,经过一段时间,外袋在负压向内的拉伸下,使外袋产生塑性变形,外袋中的空间收缩,空间中的负压因此而变小或者消失。因此,从现有技术上看,利用负压检查破损包装是无法实现的,更无法量产上市。为解决上述题,有本领域技术人员重新设计了负压的真空度,或者向软性包装内部冲入压力,或者提高软性包装材质的办法,以图改善软性包装变形情况。但又存在效果不佳和生产效率不佳等结果。利用负压检查破损包装的技术对于提升医疗水平,保证病人用药安全有着极大的意义,但因上述原因而无法应用与推广,是对人类健康事业的极大阻碍。技术实现要素:为解决上述问题,本实用新型提供了一种药用液体制剂,能够让利用负压检查破损包装的技术得以推广实现,能够实现工业自动化生产。本实用新型的一种液体制剂产品包装,包括内包装1与外包装容器,内包装用于灌装液体制剂,内包装置于外包装容器中,并在外包装容器与内包装之间形成小于大气压力的负压,当内包装出现漏孔时,所述负压的作用力使液体制剂从所述漏孔渗出。所述外包装容器由腔体2与盖体4组成;腔体用于装入内包装,并在腔体内形成负压3;所述的腔体设置有在腔体内抽取负压后支撑腔体保持形状的腔体支撑部分,及阻隔外界空气进入到腔体内的空气阻隔部分;盖体对腔体内进行密封,盖体与腔体组成密封结构。如上所述的一种液体制剂产品包装,具体为,所述的腔体支撑部分为具备强度的若干支撑结构,支撑结构分布在腔体的壁面,所述的空气阻隔部分设置在各支撑结构之间的空隙处;腔体边缘上还设置有与所述盖体热合密封的热合平面。如上所述的一种液体制剂产品包装,更进一步说明为,所述的腔体内设置有凸出的限位块2-3,限位块用于对内包装进行固定。如上所述的一种液体制剂产品包装,更进一步说明为,所述的内包装1与盖体4为透明软膜材料;所述腔体由硬质透明塑料制成,厚度为0.3~3mm。如上所述的一种液体制剂产品包装,更进一步说明为,所述的热合平面2-2宽度为3mm以上。如上所述的一种液体制剂产品包装,更进一步说明为,所述的腔体的深度为内包装1厚度的50%~130%,所述的腔体的深度为构成腔体的若干个面中的面积最大的面作为底部至与围绕底部构成的壁的高度;所述的内包装厚度为内包装平放时下壁面至上壁面的高度。如上所述的一种液体制剂产品包装,更进一步说明为,所述的腔体的容积为内包装总体积的70%~300%。所述的内包装外表面除内包装平放时与外包装容器接触的下壁面与上壁面外的其余表面与外包装容器间隔最小距离为1.5mm。如上所述的一种液体制剂产品包装,更进一步说明为,所述的腔体为盒体形状,所述的腔体边缘为盒体的口部边缘。所述的空气阻隔部分为阻隔膜;支撑结构为支撑块。如上所述的一种液体制剂产品包装,更进一步说明为,所述的盖体与热合平面热合,盖体与内包装接触处向外部凸出,其余部分向腔体内凹入。本实用新型的有益效果为:本实用新型使利用负压检查破损包装的技术可行。1、本实用新型的设计的外包装容器结构能有效抵抗抽取负压所带来的产品变形,极好地保护了内包装,尤其是对一些盖体易折断的内包装产生了有效保护,抽取负压后外包装容器结构平整完好,不会对内包装产生新的破坏,提高了整体合格率,降低了生产浪费,降低了成本。2、本实用新型设计的外包装容器形状规则,形状固定,在生产线上将内包装放入外包装容器的动作、抽取负压的动作、成品装箱的动作等全部过程中,能达到自动化动作的可选设备非常多,因此本实用新型可实现全自动化生产实施,提高了产量,降低了劳动强度。全自动化生产中,避免了人工干预,因此进一步提高了产品合格率。3、在产品下线后,外包装容器能为内包装提供更可靠的保护,防止产品搬运、运输过程中损坏。4、外包装容器形状规则,形状固定,在医疗场所便于堆码,码放整齐,堆码层数高,使医疗场所整齐,提高医疗效率。5、本实用新型的内包装的厚度与腔体的深度之比例、本实用新型的腔体总容积与内包装总体积之比例、内包装与腔体之间的间隔,上述设计参数保证了腔体内的负压的总量值在设计有效范围内,使利用负压检查破损包装的技术可行。6、本实用新型的外包装容器具备在负压力的作用下仍然最大程度保持形状的能力,在负压抽取后,外包装容器的变形量小,不因负压作用力而过多向内收缩,因此外包装容器中的容积空间大小尽量保持,当空间大小保持时,也可以保持空间内的负压。附图说明图1为本产品结构图。图2为本产品的b-b向剖面图。图3为实施形态示例图。图4为实施形态的a-a向剖视图。图中附图编号说明:1、内包装;1-1、内包装焊接封边;1-2、内包装盖;2、腔体;2-1、撕边口;2-2、热合平面;2-3、限位块;3、负压;4、盖体。具体实施方式为使本实用新型的目的、技术方案和优点更加清楚,下面将结合本实用新型具体实施例及相应的附图1、附图2、附图3、附图4对本实用新型技术方案进行清楚、完整地描述。本实用新型的一种液体制剂产品包装,包括内包装1与外包装容器,液体制剂灌装于内包装中,内包装置于外包装容器中。本实用新型使用的内包装一般是指软袋包装,由透明的软膜制成,然后在内包装中灌装一定的液体药剂,在内包装的上部设置有质地相对较硬的内包装盖1-2,内包装周边为内包装焊接封边1-1。本实用新型所指的外包装容器为分两部分:腔体及盖体;腔体必须为有一定强度的材质做成,并必须具有一定的硬度,材料厚度为0.3~3mm,可选材料包括PVC片膜,或者其它硬片型的透明材料,如透明钢化玻璃材料、透明钢化塑料、硬质透明塑料、复合透明材料等。可通过吹塑、冲压、热加工等方法加工成盘状、碗状、盒体状,然后在边缘留置与盖体热合焊接的热合平面。热合平面2-2宽度为3mm以上,可选择的平面宽度为3mm~40mm。例如腔体为盒状的情况,本实用新型所述的空气阻隔部分为阻隔膜,也就是PVC片膜;本实用新型所述的支撑结构为支撑块,也就是为增加PVC片膜强度的加强筋,当然,支撑结构的形状不限,可以为点阵状、条状、柱状、块状、横向状、纵向状、下凹状、外凸状;位置不限,可以在腔体侧壁、腔体底部。如果加工材料本身就是高强度材料,那么材料自身则认为是支撑块,例如采用钢化玻璃制造,钢化玻璃本身具备强度,则采用钢化玻璃自身为支撑块。本实用新型的外包装容器为密封结构且在负压作用下能保持原有形状;其中所述的在负压作用下能保持原有形状是指:在外包装容器抽取负压后,负压产生将外包装容器向内收缩变形的作用力,而本实用新型的外包装容器能抵御所述的作用力,使外包装容器保持不变形,或者变形量控制在一定的范围;所述的变形量控制在一定的范围其要求和原理参照下表3、表4。为了将内包装在腔体内进行有效的固定,以进一步防止内包装在外包装容器内扭曲变形,可以适当在外包装容器内设置有凸出的限位块2-3,内包装盖1-2或其它部分与限位块2-3配合,用于对内包装进行固定。所述的盖体为硬质透明材料。外包装容器的边角处均倒圆角。在不影响密封效果的情况下,在热合平面上留一小块位置不进行热合,便于使用时揭开盖体。为了达到本实用新型的最佳效果,腔体优选PVC片膜制作;并选择PVC软膜制作盖体,盖体通过热合方式焊接在腔体上。将腔体内抽取负压,盖体对腔体内进行密封,使腔体内的负压保持作用到内包装上。PVC片膜为材质较硬的材料,在制作时易成型,能制作成较为理想的形状,能达到生产所需要。在制作后,通过一定的材料处理,比如增加空气阻隔的铝膜后,对空气的阻隔能力增加,不透气,保持腔体内的负压效果。当然,也可以采用其它办法增加对空气的阻隔能力。对空气的阻隔能力根据产品的质量要求而定。PVC片膜在成型后,其形状固定,在搬运、取拿过程中不会变形(变形非常小,完全不影响生产、使用)。为了增加PVC的强度,腔体的硬度,在腔体上设计了加强筋。示例1:内包装1为PP透明软膜材料,盖体4为硬质透明材料制成。外包装容器为硬质透明塑料PVC制成,厚度为0.3mm,其整体形状为盒体形状,盒体的各菱角折弯处具备支撑能力,便作为腔体侧壁支撑面与腔体底部支撑面;为了进一步增加腔体支撑部分的支撑能力,可以在盒体各处增加加强筋;其余部分为空气阻隔部分。并在盒体的边缘设计热合平面2-2宽度为3mm。本示例1中以下描述内容中的盒体代表外包装容器。盒体的深度为内包装1厚度的50%。上述的盒体的深度为腔体内的深度,为构成盒体的若干个面中的面积最大的面作为底部至与围绕底部构成的壁的高度;例如盒体为常见的抽屉状时,盒体的深度则为底板到边壁上边缘的高度;如盒体为烟盒状时,盒体的深度则为前、后两壁之间的间距。所述的内包装厚度为内包装平放时下壁面至上壁面的高度;例如软袋制成的内包装,其厚度则为灌装了药剂后水平放置时的所放置的水平面与内包装上表面的垂直高度;本实施例中的内包装厚度与内包装盖的直径约等。盒体的容积为内包装总体积的70%。内包装外表面除内包装平放时下壁面与上壁面外的其余表面与盒体间隔距为1.5mm。内包装的四则边与腔体四侧边留下足够的距离,使得负压作用到腔体时,盒体有足够的空间缓冲,以免对内包装形成挤压。盖体与热合平面热合,盖体与内包装接触处向外部凸出,其余部分向盒体内凹入。该示例中,总体材料成本费用较低,但使用效果未达最佳,质量保持周期非常短。示例2:内包装1与PP透明软膜材料,盖体4为硬质透明材料制成;腔体为硬质透明塑料PVC制成,材料厚度为0.8mm。在腔体的边缘设计热合平面2-2宽度为8mm。腔体的深度为内包装1厚度的60%。腔体的容积为内包装总体积的90%。内包装外表面除内包装平放时下壁面与上壁面外的其余表面与外包装容器间隔距为3mm。盖体与热合平面热合,盖体与内包装接触处向外部凸出,其余部分向腔体内凹入。该示例中,总体材料成本费用较低,使用效果欠佳,质量保持周期很短。示例3:内包装1与PP透明软膜材料,盖体4为硬质透明材料制成;腔体为硬质透明塑料PVC制成,厚度为1mm。在腔体的边缘设计热合平面2-2宽度为10mm。腔体的深度为内包装1厚度的80%。腔体的容积为内包装总体积的180%。内包装外表面除内包装平放时下壁面与上壁面外的其余表面与外包装容器间隔距为3mm。盖体与热合平面热合,盖体与内包装接触处向外部凸出,其余部分向腔体内凹入。该示例中,总体材料成本费用偏高,使用效果佳,质量保持周期很长。示例4:内包装1与PP透明软膜材料,盖体4为硬质透明材料制成;腔体为硬质透明塑料PVC制成,厚度为3mm。在腔体的边缘设计热合平面2-2宽度为20mm。腔体的深度为内包装1厚度的80%。腔体的容积为内包装总体积的180%。内包装外表面除内包装平放时下壁面与上壁面外的其余表面与外包装容器间隔距为3mm。盖体与热合平面热合,盖体与内包装接触处向外部凸出,其余部分向腔体内凹入。该示例中,总体材料成本费用过高,使用效果佳,质量保持周期很长。从上述示例效果可见,外包装容器为硬质透明塑料制成;其可选材料厚度为0.3~3mm;其效果如下表1:真空度-90KPa-90KPa-90KPa-90KPa-90KPa-90KPa-90KPa-90KPa-90KPa厚度0.30.61.01.31.62.02.32.63宽度101010101010101010保持期3月5月8月10月14月18月22月24月24月表2:热合平面2-2宽度。真空度-90KPa-90KPa-90KPa-90KPa-90KPa-90KPa-90KPa-90KPa-90KPa厚度1.01.01.01.01.01.01.01.01.0宽度0.30.61.01.31.62.02.32.63保持期1月3月6月9月13月18月23月24月24月上上述表格1、2中,所述的真空度为腔体内形成负压时,腔体内的真空度,其单位为:相对真空度。所述的厚度为腔体的材料原度。单位:mm。所述的宽度为热合平面宽度,即腔体的边缘与盖体热合在一起的面积。所述的保持期是指在抽取负压后,真空度值在腔体内衰减不超过20%。从上述表格可见,要有更好的保持期,需要使用到厚度更高的材料和更好的热合效果。腔体的深度与内包装厚度之比,能够控制在抽取负压之后,腔体被负压作用所作的收缩形状。即:当内包装全部没入腔体内,且腔体内上部还留置一段空间时,负压力将全部作用到腔体与盖体上,盖体下压扯动腔体的四壁将向中心收缩,产生变形。当内包装仅一半被没入腔体,另一半完全凸出在腔体外部时,负压力作用到腔体与盖体上,作用到盖体上时,会被内包装凸出部分支撑,盖体下压的辐度小,腔体的四壁不会向中心收缩,产生变形极小。然因为内包装平放时其凸出部分仅为软膜部分,所述下压的盖体仅挤压在软膜部分,不会对内包装产生任何破坏的影响,不会扭曲和撕拉内包装。因此,腔体的深度与内包装厚度之比反应在腔体变形量情况如下:例如,内包装内装有250ml液体。表3:真空度-90KPa-90KPa-90KPa-90KPa-90KPa-90KPa-90KPa-90KPa-90KPa总厚度30mm30mm30mm30mm30mm30mm30mm30mm30mm深度10mm14mm18mm22mm26mm30mm34mm37mm39mm比例33%47%60%73%87%100%113%123%130%变形量5mm6mm8mm9mm11mm16mm19mm20mm20mm表3所述的总厚度为内包装1的厚度。真空度为相对真空度,深度为腔体深度。比例为腔体深度与内包装厚度之比。上述的变形量是指:在外包装容器为长方形体的情况下,长方形的两侧长边被盖体向中心拉动的产生位移的总距离,也就是两侧壁的变形量。变形量太大,会直接挤压到内包装的侧壁,也会挤压到内包装盖,对内包装产生质量影响,甚至可能会挤坏内包装盖。而内包装所能接受并不影响质量的挤压应该在变形量10mm以内。但如果深度过低,在抽取负压后,盖体对内包装的挤压力又会过高,腔体无法对内包装形成有效的保护,因此腔体最低深度取50%总厚度。腔体的容积与内包装总体积的比例能够确定负压含量。即:当腔体的总容积为10个体积单位,内包装体积为5个体积单位,则比例为10:5,腔体内则有一半为空气。在抽取负压后,空气被抽走腔体收缩。因此腔体内的空间越大,为了满足真空度,则空气被抽走的越多,空气被抽走越多,其腔体变形则越大。反应到表4如下:例如,内包装内装有250ml液体。真空度-90KPa-90KPa-90KPa-90KPa-90KPa-90KPa-90KPa-90KPa-90KPa内包装330cm3330cm3330cm3330cm3330cm3330cm3330cm3330cm3330cm3容积300ml330ml400ml500ml600ml700ml800ml900ml990ml比例91%100%121%152%182%212%242%273%300%变形量2mm2mm3mm3mm5mm8mm12mm17mm22mm所述的腔体容积为内包装总体积91%,即腔体容积小于内包装体积的情况为内包装其中一部分凸出在腔体外的情况,因此,当腔体的总容积在内包装的总体积的70%以上均可实施本实用新型。因考虑到内包装所能接受并不影响质量的变形量为10mm以内。因此,腔体的总容积在内包装的总体积的70%以上均为可选参数。上述示例中,外包装容器具备在负压力的作用下仍然最大程度保持形状的能力,在负压抽取后,外包装容器的变形量小,不因负压作用力而过多向内收缩,因此外包装容器中的容积空间大小尽量保持,当空间大小保持时,也可以保持空间内的负压。从负压的形成上分析,在大气环境条件下,在密封的一个确定的容器空间中抽取一部分气体后,因容器中气体减少而低于大气,则形成负压。但如果容器空间不确定,则同样在容器空间中抽取一部分气体,而容器空间跟随向内收缩,则容器空间内的气体含量与收缩后的容器空间比例平衡,容器空间内的气体仍然等于大气,不是负压。因此本实用新型需要在负压下仍然保持外包装容器的形态,使抽取负压后的外包装容器的内容空间大于气体在大气压环境所需空间,外包装容器中则形成负压,并得以保持。本实用新型的生产过程大致如下:1、制作内包装,并向内包装中灌装液体药剂。2、将灌装了药剂的内包装焊接内包装盖。3、将内包装与放入外包装容器,抽取外包装容器内的空气达到要求的真空度。4、在外包装内形成一定的真空度后,若是内包装上有破损,不管破损严重程度如何(不管是较大破损情况还是极其细小肉眼不可见的情况),外包装内形成的负压会迫使内包装内灌装的药剂流入到外包装容器内的外包装容器与内包装之间,形成肉眼可见的水斑。若是内包装上的破损为极其细小情况,则产品在放置一段时间(1至20天)后,外包装内的持续负压状态同样会使内包装的破损形成水斑。因此,剔除有水斑的药用液体制剂,减少其流入到医院被使用的可能性,从而提高出厂产品合格率。以下是对本实用新型效果分析:以下的传统组是指:采用双层包装中,外包装容器为软袋式,内包装容器为软袋式,并在内包装容器中抽取负压的情况。以下的合格率含义为:合格产品(即抽取负压后,外包装容器的有效密封效果,内包装未因抽取负压而损坏,外包装未因抽取负压而损坏)的比例。如在抽取负压前,内包装本身在之前加工步骤受损不计在下表5合格率内。表5,本实用新型效果统计,按中型企业计算,年产量为1亿只(袋)产品产量计算如下:年产量1亿只每日产量每日用工量每日用工成本合格率传统组30万只(袋)160人24000元97.16%本实用新型30万只(袋)6人799元99.95%按年产1亿只计,本实用新型的用工成本减少800万元。按年产1亿只计,从合格率上计算,传统组每年产生不合格产品约284万只,本实用新型每年产生不合格产品约5万只,本实用新型合格产品较传统组合格产品多出279万只,按每只成本4元计,则相当于每年多节约生产成本约1116万元,扣除使用硬质PVC片膜多出的材料成本500万(腔体必须由硬质PVC片膜制成,因此比软胶袋材料的外包装容器多出0.05元/只),全年仍节省生产成本约1416万。上述为本实用新型示例性说明,不代表本实用新型的保护范围。当前第1页1 2 3