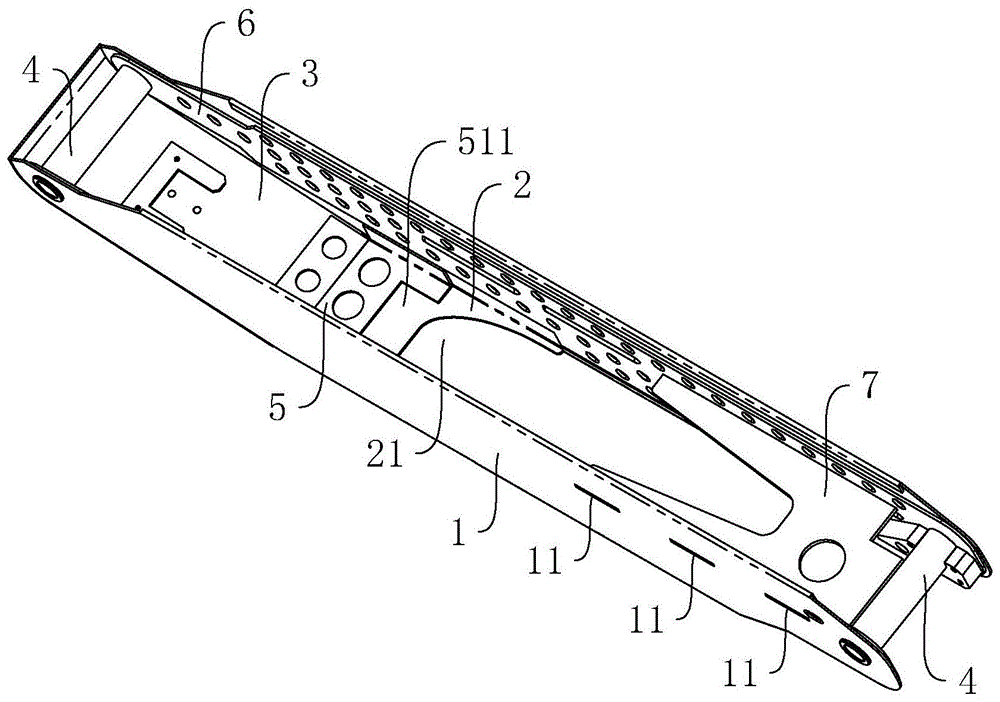
本申请涉及医疗器械技术领域,尤其是涉及一种折臂上盖及其加工工艺。
背景技术:
移动式x射线仪是用于临床医学领域的医学科研仪器,其具有活动自如的折臂结构,可以实现多个运动方向的自由度,以更好地满足各种特殊场景下的拍片要求。
为满足对移动式x射线仪的折臂有效控制,以使得折臂可以完成指定命令,折臂上通常固定有各类控制线路。相关技术中,移动式x射线仪的折臂通常设置呈多根转动连接的柱状结构,各控制线路则通过辅助固定结构、卡接结构等固定在折臂的外侧壁上,并跟随折臂进行运动。
针对上述中的相关技术,发明人认为各控制线路裸露在折臂外,易致使控制线路在外部因素的作用下受到磨损,从而致使移动式x射线仪无法正常使用。
技术实现要素:
为了使得折臂的各控制线路不易在外部因素的作用下受损,本申请提供一种折臂上盖及其加工工艺。
第一方面,本申请提供一种折臂上盖,采用如下的技术方案:
一种折臂上盖,包括两块正对且间隔设置的翼板以及固定在两块翼板之间的腹板一和腹板二,所述翼板与腹板一和腹板二均相互垂直,两块翼板、腹板一和腹板二围合形成设有开口的槽体,所述腹板一设在翼板的中部,所述腹板二倾斜设在翼板的一端,所述翼板的两端均设有轴套,所述轴套穿设在两块翼板之间。
通过采用上述技术方案,控制线路可以穿设固定在槽体的内部空间内,以使得两块翼板、腹板一和腹板二可以对控制线路形成防护,从而使得外部因素不易将控制线路损坏。
可选的,所述腹板一远离腹板二的一端设有通槽,所述腹板一和腹板二相互靠近的一端设有支架板,所述支架板抵接于槽体的内侧壁,所述支架板靠近通槽的一端设有嵌接槽。
通过采用上述技术方案,支架板用作两块翼板与腹板一和腹板二的加强筋结构,支架板对两块翼板、腹板一和腹板二均形成支撑,以使得折臂上盖整体的结构强度和抗压强度得以提高,从而使得折臂上盖可以对控制线路形成更好的防护。
可选的,两块翼板相互靠近的一侧均设有侧加强板。
通过采用上述技术方案,侧加强板用于对翼板进行增厚,以增强翼板的结构强度和抗变形能力,并进一步提高折臂上盖整体的稳定性。
可选的,两块侧加强板之间设有底加强板,所述翼板和侧加强板的同一位置均设有定位槽,所述底加强板的两端均设有穿设在定位槽内的定位凸起(71)。
通过采用上述技术方案,底加强板用于提高两块翼板之间的连接效果,并使得两块翼板不易沿相互靠近的方向变形,从而使得折臂上盖整体的结构强度进一步提高;定位块穿设在定位槽内,可以实现底加强板和侧加强板之间的定位,以使得底加强板的固定更加精准。
第二方面,本申请提供一种折臂上盖的加工工艺,采用如下的技术方案:
一种折臂上盖的加工工艺,其特征在于:包括以下步骤:
s1.将两块翼板、腹板一和腹板二均下料成型在单张板材上;下料时,在翼板上轴套的对应处加工出轴套基准孔,所述轴套基准孔的直径小于轴套的外径,并将翼板上的定位槽加工成型,将腹板一上的通槽加工成型;同时将支架板、侧加强板和底加强板分别下料成型;支架板在下料时,将支架板上的嵌接槽加工成型;并将轴套加工成型;
s2.将侧加强板和翼板焊接固定;
s3.然后将翼板进行弯折,以使得两块翼板均与腹板一和腹板二相垂直;
s4.对轴套基准孔进行扩孔,以形成轴套孔,所述轴套孔的直径等于轴套的直径;
s5.将支架板与槽体的内侧壁相抵接,并将支架板与槽体的内侧壁焊接固定;
s6.将侧加强板与翼板相抵接,然后将底加强板固定在两块侧加强板之间,并将底加强板的定位凸起(71)穿设在侧加强板和翼板的定位槽内;
s7.将轴套穿设在翼板的扩孔处,并将轴套与两块翼板均焊接固定;
s8.将腹板二进行弯折,以使得腹板二与两块翼板均相抵接,并将腹板二与两块翼板均焊接固定,以加工形成出槽体;
s9.将折臂上盖进行电镀;
s10.将折臂上盖进行喷涂。
通过采用上述技术方案,可以顺利加工得到折臂上盖,并在后续的具体加工步骤中,将控制线路穿设固定在折臂上盖的内部空间,即可使得折臂上盖对控制线路形成有效防护。
可选的,s2中,将底加强板的定位凸起穿设在侧加强板和翼板的定位槽内后,再将侧加强板和翼板焊接固定。
通过采用上述技术方案,定位凸起同时与侧加强板和翼板的定位槽相配合,可以实现侧加强板在翼板上的定位,以提高侧加强板与翼板焊接固定时位置的精准度。
可选的,s4中,通过定位工装一对轴套孔进行定位,所述定位工装一为长方体状的开口槽体,所述定位工装一侧壁在轴套基准孔的对应处设有过孔,所述过孔的直径小于轴套基准孔的直径;
定位时,所述腹板一和腹板二均与定位工装一的底壁相抵接,所述翼板与定位工装一的侧壁相抵接,所述过孔投影在轴套基准孔的对应区域内;扩孔时,对两块翼板上的轴套基准孔以及定位工装一两侧壁上的过孔同时进行扩孔。
通过采用上述技术方案,定位工装一首先可以翼板与腹板一弯折加工后的尺寸进行检验,其次可以对侧加强板和翼板的焊接变形进行检验,再者可以减小两块翼板上扩孔后形成的轴套孔之间的同心度,进而提高轴套焊接固定时位置的精准度。
可选的,s5中,通过定位工装二对支架板进行定位,所述定位工装二包括沿厚度方向固定连接的定位外板和定位内板;
定位时,所述定位外板的一端嵌设在通槽内,所述定位内板靠近通槽的一端嵌设在嵌接槽内。
通过采用上述技术方案,定位工装二不仅可以对腹板二的焊接变形进行检验,并且还可以对支架板进行定位,以使得支架板的焊接位置更加准确。
综上所述,本申请包括以下至少一种有益技术效果:
1.折臂上盖加工后形成有槽体,控制线路可以穿设固定在槽体的内部空间内,以使得两块翼板、腹板一和腹板二可以对控制线路形成防护,从而使得外部因素不易将控制线路损坏;
2.通过设置侧加强板,侧加强板用于对翼板进行增厚,以增强翼板的结构强度和抗变形能力,并进一步提高折臂上盖整体的稳定性。
附图说明
图1是本申请实施例折臂上盖整体的结构示意图;
图2是本申请实施例中支架板的结构示意图;
图3是本申请实施例中侧加强板的结构示意图;
图4是本申请实施例中底加强板的结构示意图;
图5是本申请实施例中翼板、腹板一和腹板二下料时的示意图;
图6是本申请实施例中定位工装一的结构示意图;
图7是本申请实施例中定位工装二的结构示意图。
附图标记说明:1、翼板;11、定位槽;12、轴套基准孔;2、腹板一;21、通槽;3、腹板二;4、轴套;5、支架板;51、支架底板;511、嵌接槽;52、支架侧板;53、支架靠板;6、侧加强板;61、通孔;7、底加强板;71、定位块;8、定位工装一;81、过孔;9、定位工装二;91、定位外板;92、定位内板。
具体实施方式
以下结合附图1-7对本申请作进一步详细说明。
本申请实施例公开一种折臂上盖。参照图1,折臂上盖包括翼板1、腹板一2和腹板二3。
翼板1、腹板一2和腹板二3均可以采用钢材制成。翼板1正对且间隔设置有两块,腹板一2和腹板二3均固定在两块翼板1之间,且腹板一2和腹板二3均与翼板1相垂直。两块翼板1、腹板一2和腹板二3围合形成设有开口的槽体,槽体上槽口所在的一侧为翼板1远离腹板一2和腹板二3的一侧。控制线路可以穿设固定在槽体的内部空间内,以使得两块翼板1、腹板一2和腹板二3可以对控制线路形成防护,从而使得外部因素不易将控制线路损坏。
腹板一2设在翼板1的中部,腹板二3倾斜设置在翼板1的一端。腹板二3远离腹板一2的一端沿弧线折弯设置,腹板一2远离腹板二3的一端设有通槽21,通槽21呈大小端结构,通槽21的大端为远离腹板二3的一端,通槽21的小端为靠近腹板二3的一端。
翼板1的两端均设有轴套4,轴套4穿设在两块翼板1之间。轴套4用作折臂上盖与折臂上盖上下游零部件的连接结构,以使得折臂上盖可以满足折臂的移动自由度所需。
参照图1和图2,腹板一2和腹板二3相互靠近的一端设有支架板5,支架板5包括支架底板51、支架侧板52和支架靠板53。支架底板51抵接于腹板一2的内侧壁,支架底板51靠近通槽21的一端设有嵌接槽511,嵌接槽511呈矩形。支架侧板52固定在支架底板51的两侧,且支架侧板52抵接于翼板1相互靠近的一侧,支架靠板53抵接于腹板二3的内侧壁。支架板5用作两块翼板1与腹板一2和腹板二3的加强筋结构,支架板5对两块翼板1、腹板一2和腹板二3均形成支撑,以使得折臂上盖整体的结构强度和抗压强度得以提高,从而使得折臂上盖可以对控制线路形成更好的防护。
参照图1和图3,两块翼板1相互靠近的一侧均设有侧加强板6。侧加强板6沿其厚度方向上的投影均位于翼板1内。侧加强板6在轴套4的穿设处设有供轴套4穿过的通孔61,通孔61的直径大于轴套4的外径。侧加强板6用于对翼板1进行增厚,以增强翼板1的结构强度和抗变形能力,并进一步提高折臂上盖整体的稳定性。
参照图1和图4,两块侧加强板6之间固定有底加强板7。结合图3,翼板1和侧加强板6的同一位置均设有定位槽11,定位槽11为矩形槽。定位槽11在翼板1和侧加强板6上均设有三个,三个定位槽11位于同一基准线上。底加强板7靠近侧加强板6的端部上均固定有定位凸起71,定位凸起71呈矩形,定位凸起71与定位槽11一一对应。定位凸起71穿设在定位槽11内,以实现底加强板7和侧加强板6之间固定连接时的定位。底加强板7用于提高两块翼板1之间的连接效果,并使得两块翼板1不易沿相互靠近的方向变形,从而使得折臂上盖整体的结构强度进一步提高。
本申请实施例一种折臂上盖实施原理为:具体加工时,将控制线路穿设固定在折臂上盖的内部空间中,当折臂上盖受到外部因素的挤压时,侧加强板6将翼板1加厚,可以使得翼板1不易产生凹坑等形变;底加强板7对两块翼板1形成支撑,可以实现两块翼板1不易沿相互靠近的方向倾斜;支架板5可以两块翼板1、腹板一2和腹板二3均形成支撑,进一步使得折臂上盖难以产生变形;最终使得折臂上盖可以对控制线路形成有效防护。
本申请还公开一种折臂上盖的加工工艺,包括以下步骤:
s1.参照图5,将两块翼板1、腹板一2和腹板二3均下料成型在单张板材上;下料时,在翼板1上轴套4的对应处加工出轴套基准孔12,轴套基准孔12的直径小于轴套4的外径,并将翼板1上的定位槽11加工成型,将腹板一2上的通槽21加工成型;
同时将支架板5、侧加强板6和底加强板7分别下料成型;支架板5在下料时,将支架底板51、支架侧板52和支架靠板53下料在单张板材上,并同时将支架板5上的嵌接槽511加工成型;
并将轴套4加工成型;
s2.将底加强板7的定位凸起71穿设在侧加强板6和翼板1的定位槽11内后,再将侧加强板6和翼板1焊接固定;焊接时,控制侧加强板6和翼板1变形;焊接后将焊接处打磨平整光滑;
s3.然后将翼板1进行弯折,以使得两块翼板1均与腹板一2和腹板二3相垂直;
s4.通过定位工装一8对轴套4进行定位,参照图6,定位工装一8为长方体状的开口槽体,定位工装一8的长度大于翼板1的最大长度;定位工装一8侧壁在轴套基准孔12的对应处设有过孔81,过孔81的直径小于轴套基准孔12的直径;
参照图1和图6,定位时,将腹板一2和腹板二3均与定位工装一8的底壁相抵接,将翼板1与定位工装一8的侧壁相抵接,并使得过孔81投影在轴套基准孔12的对应区域内;
扩孔时,对两块翼板1上的轴套基准孔12以及定位工装一8两侧壁上的过孔81同时进行扩孔,以使得翼板1上形成轴套孔,轴套孔的直径等于轴套4的外径;
s5.将支架板5弯折成型,通过定位工装二9对支架板5进行定位,参照图7,定位工装二9包括沿厚度方向固定连接的定位外板91和定位内板92;定位外板91呈大小端结构,定位外板91大端的形状与通槽21的形状相同;定位内板92为矩形板,定位内板92的宽度等于嵌接槽511的宽度;
参照图1和图7,定位时,将定位外板91的大端嵌设在通槽21内,将定位内板92靠近通槽21的一端嵌设在嵌接槽511内;然后将支架板5与槽体的内侧壁焊接固定;
s6.将底加强板7固定在两块侧加强板6之间,并将底加强板7的定位凸起(71)穿设在侧加强板6和翼板1的定位槽11内;再将底加强板7与侧加强板6和翼板1均焊接固定;
s7.将轴套4穿设在翼板1的扩孔处,并将轴套4与两块翼板1均焊接固定;
s8.将腹板二3进行弯折,以使得腹板二3与两块翼板1均相抵接,并将腹板二3与两块翼板1均焊接固定,以加工形成出槽体;
s9.将折臂上盖进行电镀,以形成环保彩锌镀层;
s10.将折臂上盖进行喷涂,以形成保护涂层。
以上均为本申请的较佳实施例,并非依此限制本申请的保护范围,故:凡依本申请的结构、形状、原理所做的等效变化,均应涵盖于本申请的保护范围之内。