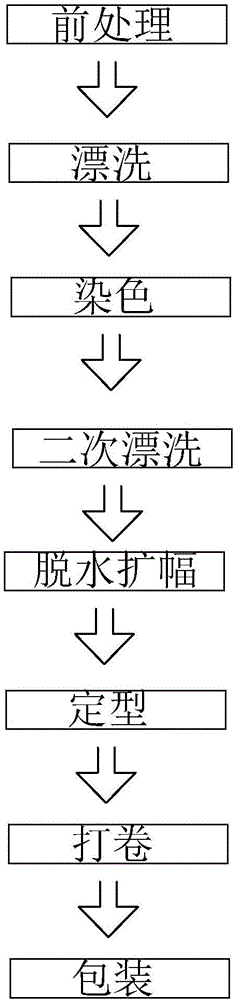
本发明涉及纺织加工工艺,特别涉及一种涤纶布加工工艺。
背景技术:
涤纶的生产过程包括缩聚和熔体纺丝两部分。原料主要从石油裂解获得,也可从煤和天然气取得。聚酯纤维,俗称涤纶。在化纤中属于合成纤维。合成纤维制造业是化纤行业中规模最大、分支最多的子行业,除了涤纶外,其产品还包括腈纶、锦纶、氨纶等。
公开号为CN104947462A,公告日为2015.09.30的中国专利《一种涤纶布料的加工工艺》,公开了一种涤纶布料的加工工艺,该布料经纱为涤纶,纬纱为棉纱,生产工序为:坯布配缸→前处理退浆→热水清洗坯布→升温染色→降温清洗→面料出机防水定型→成品检验→成品打卷,所述前处理退浆温度为80-90℃,其退浆助剂配方为:纯碱15-20kg/L,草酸4-6kg/L;所述升温染色温度控制在105-120℃,其染色助剂配方:825匀染剂2.5-5kg/L、冰醋1.5-4kg/L、元明粉30-35kg/L,本发明所述的一种涤纶布料的加工工艺,退浆助剂的配方以及染色助剂的配方使涤纶面料的强度提高,而且使上色的色牢度更好,使染色达到了“匀、透”的最佳效果。
上述发明通过坯布配缸→前处理退浆→热水清洗坯布→升温染色→降温清洗→面料出机防水定型→成品检验→成品打卷的工序,并且通过退浆助剂和染色助剂的配方提升涤纶布的强度,但是根据现有技术对于涤纶布的染色工序,在对涤纶布染色以及漂洗后需要脱水并且定型,其中脱水工序大多使用脱水机进行,并且在脱水完成后还需要进行对涤纶布的扩幅作用,期间对涤纶布进行转移时会消耗大量的时间,导致工作效率较低。综上所述,现有技术存在需要改进之处。
技术实现要素:
本发明的目的是提供一种加工效率高的涤纶布生产工艺,该加工工艺通过在布料染色并且漂洗后,脱水以及扩幅的工序之间直接连接,脱水以及扩幅同时进行,无需对布料进行集体转移,减少了加工时间。
本发明的上述技术目的是通过以下技术方案得以实现的:一种涤纶布加工工艺,其特征在于,包括以下步骤:
步骤(a)前处理,将涤纶布放入到退浆机内,在退浆机内加入1-3g/L的精炼退浆剂,4-6g/L的渗透剂,12-15g/L的烧碱,1-3g/L的螯合分散剂以及1-3g/L的高效除油剂,温度控制在80-90℃,保温时间为20-30分钟;
步骤(b)漂洗,通过漂洗机对涤纶布进行漂洗,在漂洗机中加入5-8g/L的柔软剂;
步骤(c)染色,通过高温高压溢流染色机对涤纶布进行染色,控制温度在120-180℃,持续时间40-60分钟,在染色过程中加入5-25g/L的非离子渗透剂;
步骤(d)二次漂洗,通过漂洗机对涤纶布进行二次漂洗,并在漂洗机中加入7-10g/L的柔软剂;
步骤(e)脱水扩幅,通过轧水机对涤纶布进行脱水处理,使涤纶布的含水率低于20%,通过扩幅机对轧干的布料进行扩幅作用,扩幅机连接在轧水机的尾端,布料经过轧水机脱水后直接进入到扩幅机中进行扩幅作用;
步骤(f)定型,通过高温定型机对涤纶布进行定型加工,温度控制在150-200℃,车速控制在50-60米/分钟,并加入10-12g/L的柔软剂;
步骤(g)打卷,通过打卷机将加工成型的布料进行打卷作用,打卷速度控制在50-70米/分钟,在打卷的过程中对涤纶布进行人工检验;
步骤(h)包装,通过包装机将打卷完成的布料进行包装。
通过采用上述技术方案,在涤纶布进行染色后,通过漂洗机进行漂洗,再通过轧干机轧干,进行脱水处理,然后通过扩幅机进行扩幅作用,扩幅机连接在轧干机的尾部,在涤纶布经过轧干机脱水完成后,直接进入到扩幅机中,中间不需要经过转移,从而提升了对涤纶布的加工效率。并且由于涤纶布不需要转移,所以减少了涤纶布沾染灰尘等杂质的几率,从而提升了涤纶布的整洁度。
本发明进一步设置为:所述步骤(a)中,具体为加入2g/L的精炼退浆剂,5g/L渗透剂,2g/L螯合分散剂,2g/L高效除油剂,温度控制在85℃,保温时间25分钟。
通过采用上述技术方案,在退浆机内加入上述剂量的精炼退浆剂、渗透剂、螯合分散剂以及除油剂,将涤纶布表面的浆料祛除,便于染色,并且可以祛除涤纶布表面的天然杂质、油污等污染物,从而提升布料的整洁度,提升了对于涤纶布的染色效果。
本发明进一步设置为:所述步骤(c)具体为:在染色过程中加入10g/L的非离子渗透剂,控制温度在120-140℃,持续时间10-15分钟,再加入15g/L的非离子渗透剂,升温,控制温度在140-160℃,持续时间10-15分钟,再加入20g/L的非离子渗透剂,升温,控制温度在160-180℃,时间控制在20-30分钟,完成后均匀降温。
通过采用上述技术方案,在染色过程中加入非离子渗透剂能够提升燃料的渗透效果,方便染料进入到涤纶布内部,对涤纶布进行充分的染色作用,提升了染色效果,降低了染色所需的时间。在染色的过程中,逐渐增加非离子渗透剂的量以及提升温度,逐渐提升对于涤纶布的染色效果,并且可以使染色更加均匀,提升了染色效果。
本发明进一步设置为:所述柔软剂为脂基季铵盐。
通过采用上述技术方案,酯基季铵盐是一种新型阳离子表面活性剂,具有优异的柔软、抗静电性能,抗黄变。不含APEO、甲醛,易生物降解,绿色环保。用量少,效果好,配制方便,综合成本低,具有极高的性价比。其作为柔软剂能够在提升涤纶布柔软度的前提下,降低了生产成本,减少了对环境的污染。
本发明进一步设置为:所述步骤(e)中扩幅机上设置有用于烘干布料的热风管,热风的温度控制在60-80℃。
通过采用上述技术方案,在扩幅机上设置的热风管可以在涤纶布扩幅的过程中,通过热风的作用对布料进行烘干的作用,提升布料的干燥度,便于定型机进行定型作用。
本发明进一步设置为:所述步骤(f)中定型机温度控制在180℃,速度控制在55米/分钟,柔软剂为11g/L。
通过采用上述技术方案,在上述的温度以及时间条件下,加上适量柔软剂的作用,能够在保持较好的定型效果的同时,提升涤纶布的柔软度,并且提升了工作效率。
本发明进一步设置为:步骤(g)中打卷机的速度控制在60米/分钟。
通过采用上述技术方案,在打卷机特定的打卷速度下,与人工验布所能接受的速度结合,在保持高效率的情况下能够对布料进行检验,防止有瑕疵的布料不被发现而影响后期的加工。
综上所述,本发明具有以下有益效果:
其一:该涤纶布在进行加工时,通过轧水机和扩幅机的结合,实现对涤纶布脱水以及扩幅的衔接,中间无需对涤纶布进行转移,从而提升了工作效率,并且减少了对涤纶布的污染,提升了整洁度;
其二:在进行染色时,通过逐渐提升非离子渗透剂的浓度以及温度,在不断提升染色效果的同时,提升了染色的均匀度,提升了布料的质量,减少废布的产生,降低了生产成本。
附图说明
图1是实施例一种涤纶布加工工艺的工艺流程图。
具体实施方式
以下结合附图对本发明作进一步详细说明。
如图1所示,一种涤纶布加工工艺,其特征在于,包括以下步骤:
步骤(a)前处理,将涤纶布放入到退浆机内,在退浆机内加入1-3g/L的精炼退浆剂,4-6g/L的渗透剂,12-15g/L的烧碱,1-3g/L的螯合分散剂以及1-3g/L的高效除油剂,温度控制在80-90℃,保温时间为20-30分钟;上述过程中,具体为加入的剂量为2g/L的精炼退浆剂,5g/L渗透剂,2g/L螯合分散剂,2g/L高效除油剂,温度控制在85℃,保温时间25分钟。
步骤(b)漂洗,通过漂洗机对涤纶布进行漂洗,并在漂洗机中加入5-8g/L的柔软剂,漂洗一次,并通过漂洗机对布料进行脱水使含水量低于20%;柔软剂为脂基季铵盐,酯基季铵盐是一种新型阳离子表面活性剂,具有优异的柔软、抗静电性能,抗黄变。不含APEO、甲醛,易生物降解,绿色环保。用量少,效果好,配制方便,综合成本低,具有极高的性价比。
步骤(c)染色,通过高温高压溢流染色机对涤纶布进行染色,控制温度在120-180℃,持续时间40-60分钟,在染色过程中加入5-25g/L的非离子渗透剂;
在染色过程中加入10g/L的非离子渗透剂,控制温度在120-140℃,持续时间10-15分钟,再加入15g/L的非离子渗透剂,升温,控制温度在140-160℃,持续时间10-15分钟,再加入20g/L的非离子渗透剂,升温,控制温度在160-180℃,时间控制在20-30分钟,完成后均匀降温。
步骤(d)二次漂洗,通过漂洗机对涤纶布进行二次漂洗,并在漂洗机中加入7-10g/L的柔软剂;
步骤(e)脱水扩幅,通过轧水机对涤纶布进行脱水处理,使涤纶布的含水率低于20%,通过扩幅机对轧干的布料进行扩幅作用,扩幅机连接在轧水机的尾端,布料经过轧水机脱水后直接进入到扩幅机中进行扩幅作用;扩幅机上设置有用于烘干布料的热风管,热风的温度控制在60-80℃,在热风管的作用下,将布料上的水分吹干,能够提升布料的干燥度,便于后期进行定型加工。
步骤(f)定型,通过高温定型机对涤纶布进行定型加工,温度控制在150-200℃,车速控制在50-60米/分钟,并加入10-12g/L的柔软剂,上述具体为定型机温度控制在180℃,速度控制在55米/分钟,柔软剂为11g/L。
步骤(g)打卷,通过打卷机将加工成型的布料进行打卷作用,打卷速度控制在50-70米/分钟,在打卷的过程中对涤纶布进行人工检验;打卷机的速度控制在60米/分钟。
步骤(h)包装,通过包装机将打卷完成的布料进行包装。
本具体实施例仅仅是对本发明的解释,其并不是对本发明的限制,本领域技术人员在阅读完本说明书后可以根据需要对本实施例做出没有创造性贡献的修改,但只要在本发明的权利要求范围内都受到专利法的保护。