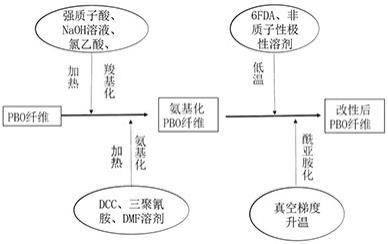
一种表面接枝改性pbo纤维的制备方法
技术领域
1.本发明属于高性能纤维改性领域,具体涉及一种表面接枝改性pbo纤维的制备方法。
背景技术:2.pbo纤维具有高强、高模、高耐热和高阻燃的优异性能,被誉为21世纪的“超级纤维”。pbo纤维增强复合材料可广泛用于建筑增强材料,体育用品等民用领域,还有防弹抗冲击材料、武器装备等军用、航空航天领域,促进了装备的轻量化、小型化和高性能化的发展。因此,pbo纤维增强复合材料成为材料领域近来研究的热点。
3.众所周知,纤维增强复合材料的机械性能的高低与界面的性质息息相关,界面的损坏是复合材料破坏的关键因素。良好的界面粘结力可以将基质受到的载荷转移到纤维上,减少内部的应力集中,可有效提高复合材料的性能。对于pbo纤维而言,纤维表面没有极性基团,大都被包裹在了内部,表面呈现惰性和光滑,不能与树脂进行很好的粘结,界面强度低,制约了pbo纤维在先进复合材料中的广泛应用。同时pbo分子中的噁唑环容易在紫外光照射下开环断裂,pbo纤维抗紫外老化性能差也是影响纤维及其复合材料使用寿命的不可忽略的重要因素。
4.pbo纤维的表面改性方法包括表面刻蚀、接枝反应、偶联剂处理、等离子体改性、辐射法、涂覆法等。表面接枝技术改性pbo纤维是化学改性方法中研究最多的技术之一,是一种低损伤的处理技术,而且具有可设计性。通过含活性官能团的试剂与纤维表面生成化学键以改变本体性能的一种技术,材料自身不发生反应并保持原状,因此本体属性不发生改变或者损失。
5.目前,很多研究人员通过一系列的改性方法仅仅单独改善了pbo纤维与聚合物基质的界面活性,对改善纤维的综合性能研究的较少。因此,采用一种合适改性方法可以同时提升pbo纤维的表面粘结性和抗紫外老化性,具有重要意义和应用价值。
技术实现要素:6.针对现有技术不足,本技术提供了一种表面接枝改性pbo纤维的制备方法。将pbo纤维清洗,再经过真空干燥得到洁净的pbo纤维。通过对洁净pbo纤维预处理得到表面含有氨基的纤维;将4,4-六氟亚异丙基-邻苯二甲酸酐(6fda)加入到有机溶剂中溶解,然后将表面含氨基的pbo纤维再加入到混合溶液中,接枝反应结束后经去离子水清洗、真空梯度升温加热,得到一种表面接枝有极性基团和酰亚胺环结构的改性pbo纤维。本发明制备的改性pbo纤维表面含有大量的极性基团和抗紫外辐照性强的基团,表面粗糙度增加,明显改善纤维与树脂基体的界面粘结性能,并且在一定程度上改善了纤维的抗紫外老化性能。
7.本发明的具体技术方案是:一种表面接枝改性的pbo纤维及其制备方法,包括如下步骤:(1)pbo纤维进行表面羧基化处理:将适量的洁净pbo纤维加入到强质子酸中,在70
~100℃下搅拌反应2~10h,再将纤维置于适量naoh溶液中,加入氯乙酸,超声处理,优选处理4h,用去离子水洗涤几次,优选6次,真空干燥,得到表面带有羧基的pbo纤维。
8.步骤(1)所述强质子酸为硫酸、甲烷磺酸、硝酸、多聚磷酸中一种或者它们的任意组合。
9.其中pbo纤维的加入量为强质子酸质量的0.2~2%,强质子酸的质量分数为30~65%,优选使用60wt%强质子酸。
10.步骤(1)所述氢氧化钠溶液质量分数为2~15%;氯乙酸的加入量为naoh溶液质量的1~10%。
11.质子酸的主要作用是与纤维作用产生质子化效应,质子酸浓度增加有明显作用;氯乙酸的作用是通过乙酸部分的共轭作用将羟基转化为羧基,氯乙酸量过少形成的羧基少,过量的氯乙酸效果也不会很明显。
12.作为优选技术方案,pbo纤维进行表面羧基化处理前,先采用有机溶剂清洁pbo纤维,清洗纤维表面杂质和油剂。具体清洁方法为:将适量的pbo纤维置于有机溶剂中,加热回流一段时间,优选5h,然后用去离子水洗涤几次(优选6次),再将清洗后的纤维真空干燥,得到洁净pbo纤维。所述有机溶剂优选为乙醇、丙酮、石油醚、乙酸乙酯中一种或者它们的任意组合。
13.(2)将表面带有羧基的pbo纤维置于n,n-二甲基甲酰胺(dmf)中,然后将n,n-二环己基碳二亚胺(dcc)和三聚氰胺加入反应体系中,在70~140℃下反应6~48h;然后将纤维用去离子水洗涤,真空干燥,得到表面带有氨基的pbo纤维。
14.步骤(2)中dcc质量是表面带有羧基的pbo纤维质量的0.5~3倍,三聚氰胺质量是表面带有羧基的pbo纤维质量的0.2~2.5倍。
15.(3)在氮气气体保护下,将4,4-六氟亚异丙基-邻苯二甲酸酐(6fda)加入到非质子极性溶剂中溶解,加入表面带有氨基的pbo纤维后在0~15℃反应12~36h,使6fda充分与pbo纤维表面发生反应,反应完成后用去离子水洗涤接枝后pbo纤维6~10次,接枝后pbo纤维采用阶梯升温进行真空加热。
16.其中6fda质量是表面带有氨基的pbo纤维质量的0.5~3倍。
17.上述步骤(3)所述非质子极性溶剂为n,n-二甲基甲酰胺(dmf)、二甲基乙酰胺(dmac)、二甲基亚砜(dmso)、n-甲基吡咯烷酮(nmp)等。
18.步骤(1)和(2)中真空干燥的温度优选为100℃,时间优选8h;步骤(3)所述的阶梯升温真空加热温度优选采用三阶升温,具体温度段分别为:90~120℃、180~210℃、270~320℃;每阶段真空加热时间优选为1h。
19.在低温条件下6fda与pbo纤维表面形成的酰胺酸结构在常温下十分不稳定且容易发生降解,因此采用阶梯升温将酰胺酸进行酰亚胺化,形成更为稳定的结构。有利于提高纤维的抗紫外老化性能。
20.除此之外,本发明所述的其他技术方案均采用的是常规现有技术,发明人不再赘述。
21.与现有技术相比,本发明所具有的有益效果是:(1)4,4-六氟亚异丙基-邻苯二甲酸酐(6fda)结构直接以化学键的形式键合在pbo纤维表面,结合效果好,避免采用物理方法制备的涂层因与纤维结合力不够及长时间使用
造成使用效果和寿命降低。
22.(2)pbo纤维表面接枝的6fda结构含有大量活性基团,含有-cf2以及大量氧元素,因此反应活性高,纤维表面极性增加,粗糙度增加,可以与多种树脂形成稳定的化学键合,提高纤维增强树脂基复合材料的界面粘结力。
23.(3)该发明所提出的改性方法,操作简单,灵活性高,在纤维本体强度损失很小的前提下,可大幅提高纤维与树脂间的界面结合力。
24.(4)三聚氰胺作为多胺的典型代表,三聚氰胺起到了分子桥结合pbo纤维和与其它改性基团的作用。采用该方法纤维接枝率高,6fda与携带氨基的pbo纤维生成酰亚胺环结构,酰亚胺环上氮氧双键的强烈吸电效应保证了空间内的电荷分布密度,该结构键能大,可有效提高改性pbo纤维的耐紫外老化性能。
附图说明
25.图1为本发明的工艺流程图。
具体实施方式
26.以下通过实施例形式的具体实施方式,对本发明的上述内容做进一步的详细说明,但不应将此理解为本发明上述主题的范围仅限于以下的实例。凡基于本发明上述内容所实现的技术均属于本发明的范围,除特殊说明外,下述实施例中均采用常规现有技术完成。
27.实施例1:一种表面接枝改性的pbo纤维及其制备方法,包括如下步骤:(1)将6gpbo纤维置于300ml丙酮中,加热回流5h,然后用去离子水清洗6次,再将清洗后的纤维在100℃真空干燥8h,得到洁净的pbo纤维。
28.(2)pbo纤维的预处理:将2.4g的洁净pbo纤维放入装有320ml硫酸(质量分数为40%)的三口烧瓶中,在70℃下搅拌反应8h,再将纤维置于280ml质量分数为3%naoh溶液中,再加入12.6g氯乙酸,并超声4h,用去离子水洗涤6次,真空100℃干燥8h得到表面带有羧基的pbo纤维。
29.(3)将0.24g表面带有羧基的pbo纤维添加到装有320ml的n,n-二甲基甲酰胺(dmf)的三口烧瓶中,然后将0.29g n,n-二环己基碳二亚胺(dcc)和0.34g三聚氰胺加入反应体系中。在90℃下反应36小时,然后用去离子水洗涤纤维6次,在100℃下真空干燥8h,得到表面带有氨基的pbo纤维。
30.(4)接枝改性pbo纤维的制备:在氮气保护的条件下,将0.15g6fda加入到装有320mln-甲基吡咯烷酮(nmp)三口烧瓶中溶解,然后将0.12g表面带有氨基的pbo纤维加入到混合溶液中,在温度为8℃条件下反应34h。反应完成后用去离子水洗涤接枝后pbo纤维6次,然后在90℃真空加热1h,190℃真空加热1h,280℃真空加热1h。
31.本实施例得到的表面接枝改性前后的pbo纤维采用astm-d3379标准测试单丝的拉伸强度,其中标距为20mm,速度为10mm/min,每组纤维样品测30个取平均值。
32.利用改性前后的pbo纤维分别与环氧树脂制备了复合材料,制备方法为将质量比
为3.31:1的环氧树脂e51和固化剂h256配胶并混合均匀,然后均匀滴加到单纤维表面,在烘箱中70℃固化2h,100℃固化2h,150℃固化3h,测试小球从单根纤维摆脱的力值(ifss)来评价纤维表面的界面粘结性能,每种条件测30个树脂球取平均值。
33.初始pbo纤维的ifss值为22.63mpa,接枝改性后的pbo纤维的pbo纤维的ifss值为35.35 mpa,界面剪切强度提高了56.2%。
34.初始pbo纤维及改性后纤维分别经过800w/m2紫外光照射100h后,初始pbo纤维强度保持率为49.1%,改性后pbo纤维强度保持率为63.4%。
35.实施例2:一种表面接枝改性的pbo纤维及其制备方法,包括如下步骤:(1)将6gpbo纤维置于300ml乙醇中,加热回流5h,然后用去离子水清洗6次,再将清洗后的纤维在100℃真空干燥8h,得到洁净的pbo纤维。
36.(2)pbo纤维的预处理:将2.4g的洁净pbo纤维放入装有255ml甲烷磺酸(质量分数为60%)的三口烧瓶中,在93℃下搅拌反应7.5h,再将纤维置于250ml质量分数为9.6%naoh溶液中,再加入20.5g氯乙酸,并超声4h,用去离子水洗涤6次,真空100℃干燥8h得到表面带有羧基的pbo纤维。
37.(3)将0.35g表面带有羧基的pbo纤维添加到装有255ml的n,n-二甲基甲酰胺(dmf)的三口烧瓶中,然后将0.84gn,n-二环己基碳二亚胺(dcc)和0.74g三聚氰胺加入反应体系中。在115℃下反应35小时,然后用去离子水洗涤纤维6次,在100℃下真空干燥8h,得到表面带有氨基的pbo纤维。
38.(4)接枝改性pbo纤维的制备:在氮气保护的条件下,将0.65g6fda加入到装有255ml二甲基乙酰胺(dmac)三口烧瓶中溶解,然后将0.31g表面带有氨基的pbo纤维加入到混合溶液中,在温度为4℃条件下反应26h。反应完成后用去离子水洗涤接枝后pbo纤维7次,然后在110℃真空加热1h,200℃真空加热1h,300℃真空加热1h。
39.本实施例得到的表面接枝改性前后的pbo纤维采用astm-d3379标准测试单丝的拉伸强度,其中标距为20mm,速度为10mm/min,每组纤维样品测30个取平均值。利用改性前后的pbo纤维分别与环氧树脂制备了复合材料,制备方法为将质量比为3.31:1的环氧树脂e51和固化剂h256配胶并混合均匀,然后均匀滴加到单纤维表面,在烘箱中70℃固化2h,100℃固化2h,150℃固化3h,测试小球从单根纤维摆脱的力值(ifss)来评价纤维表面的界面粘结性能,每种条件测30个树脂球取平均值。
40.初始pbo纤维的ifss值为22.63mpa,接枝改性后的pbo纤维的pbo纤维的ifss值为37.48mpa,界面剪切强度提高了65.6%。
41.初始pbo纤维及改性后纤维分别经过800w/m2紫外光照射100h后,初始pbo纤维强度保持率为49.1%,pbo纤维强度保持率为72.7%。
42.实施例3:一种表面接枝改性的pbo纤维及其制备方法,包括如下步骤:(1)将5.3gpbo纤维置于300ml石油醚中,加热回流5h,然后用去离子水清洗6次,再将清洗后的纤维在100℃真空干燥8h,得到洁净的pbo纤维。
43.(2)pbo纤维的预处理:
将2.6g的洁净pbo纤维放入装有280ml硝酸(质量分数为50%)的三口烧瓶中,在82℃下搅拌反应7.5h,再将纤维置于220ml质量分数为7%naoh溶液中,再加入14.1g氯乙酸,并超声4h,用去离子水洗涤6次,真空100℃干燥8h得到表面带有羧基的pbo纤维。
44.(3)将0.42g表面带有羧基的pbo纤维添加到装有280ml的n,n-二甲基甲酰胺(dmf)的三口烧瓶中,然后将0.76g n,n-二环己基碳二亚胺(dcc)和0.72g三聚氰胺加入反应体系中。在100℃下反应41小时,然后用去离子水洗涤纤维6次,在100℃下真空干燥8h,得到表面带有氨基的pbo纤维。
45.(4)接枝改性pbo纤维的制备:在氮气保护的条件下,将0.43g6fda加入到装有280ml n,n-二甲基甲酰胺(dmf)三口烧瓶中溶解,然后将0.26g表面带有氨基的pbo纤维加入到混合溶液中,在温度为8℃条件下反应34h。反应完成后用去离子水洗涤接枝后pbo纤维7次,然后在100℃真空加热1h,195℃真空加热1h,290℃真空加热1h。
46.本实施例得到的表面接枝改性前后的pbo纤维采用astm-d3379标准测试单丝的拉伸强度,其中标距为20mm,速度为10mm/min,每组纤维样品测30个取平均值。利用改性前后的pbo纤维分别与环氧树脂制备了复合材料,制备方法为将质量比为3.31:1的环氧树脂e51和固化剂h256配胶并混合均匀,然后均匀滴加到单纤维表面,在烘箱中70℃固化2h,100℃固化2h,150℃固化3h,测试小球从单根纤维摆脱的力值(ifss)来评价纤维表面的界面粘结性能,每种条件测30个树脂球取平均值。
47.初始pbo纤维的ifss值为22.63mpa,接枝改性后的pbo纤维的pbo纤维的ifss值为36.28 mpa,界面剪切强度提高了60.3%。
48.初始pbo纤维及改性后纤维分别经过800w/m2紫外光照射100h后,初始pbo纤维强度保持率为49.1%,pbo纤维强度保持率为68.3%。
49.实施例4:一种表面接枝改性的pbo纤维及其制备方法,包括如下步骤:(1)将4.5gpbo纤维置于300ml体积比为1:1丙酮和石油醚混合液中,加热回流5h,然后用去离子水清洗6次,再将清洗后的纤维在100℃真空干燥8h,得到洁净的pbo纤维。
50.(2)pbo纤维的预处理:将2.1g的洁净pbo纤维放入装有230ml体积比为1:1硫酸和甲烷磺酸的混合液(质量分数为60%)的三口烧瓶中,在100℃下搅拌反应7h,再将纤维置于240ml质量分数为12.3%naoh溶液中,再加入22.8g氯乙酸,并超声4h,用去离子水洗涤6次,真空100℃干燥8h得到表面带有羧基的pbo纤维。
51.(3)将0.55g表面带有羧基的pbo纤维添加到装有230ml的n,n-二甲基甲酰胺(dmf)的三口烧瓶中,然后将1.54g n,n-二环己基碳二亚胺(dcc)和1.32g三聚氰胺加入反应体系中。在120℃下反应42小时,然后用去离子水洗涤纤维6次,在100℃下真空干燥8h,得到表面带有氨基的pbo纤维。
52.(4)接枝改性pbo纤维的制备:在氮气保护的条件下,将1.04g6fda加入到装有230ml n,n二甲基甲酰胺(dmf)三口烧瓶中溶解,然后将0.40g表面带有氨基的pbo纤维加入到混合溶液中,在温度为0℃条件下反应28h。反应完成后用去离子水洗涤接枝后pbo纤维8次,然后在120℃真空加热1h,210
℃真空加热1h,310℃真空加热1h。
53.本实施例得到的表面接枝改性前后的pbo纤维采用astm-d3379标准测试单丝的拉伸强度,其中标距为20mm,速度为10mm/min,每组纤维样品测30个取平均值。利用改性前后的pbo纤维分别与环氧树脂制备了复合材料,制备方法为将质量比为3.31:1的环氧树脂e51和固化剂h256配胶并混合均匀,然后均匀滴加到单纤维表面,在烘箱中70℃固化2h,100℃固化2h,150℃固化3h,测试小球从单根纤维摆脱的力值(ifss)来评价纤维表面的界面粘结性能,每种条件测30个树脂球取平均值。
54.初始pbo纤维的ifss值为22.63mpa,接枝改性后的pbo纤维的pbo纤维的ifss值为38.06 mpa,界面剪切强度提高了68.2%。
55.初始pbo纤维及改性后纤维分别经过800w/m2紫外光照射100h后,初始pbo纤维强度保持率为49.1%,pbo纤维强度保持率为75.4%。