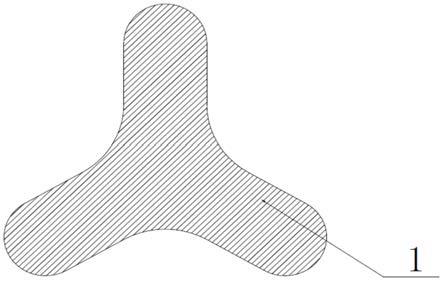
1.本发明涉及非织造布技术领域,尤其用于过滤的双组分非织造布及其制备方法。
背景技术:2.双组分纺粘法非织造布技术是基于复合纤维技术发展起来的,十几年前才出现在中国市场。但在2015年以前,发展缓慢,与国外先进水平比较,在技术装备水平、工艺水平,产品的质量等方面仍存在较大的差距。目前国内双组分纺粘法非织造布多采用“复合纺丝工艺”及“混纤型”两种生产工艺形式,纤维形式多为圆形长丝纤维,该非织造布应用在过滤行业,因为圆形纤维的结构决定了过滤效率和压强降不可兼得。
3.如专利公告号cn106521811b公开了一种水过滤用双组分梯度结构非织造布及其制备方法和应用,由粘合在一起的第一层纤网和第二层纤网组成,其中第一层纤网和第二层纤网均由不同细度的三叶形pet长丝纤维和圆形copet长丝纤维组成。然而,从该专利实施例可以看出,该非织造布两层结构一致,组分一致。专利公告号cn213291578u公开了一种双组份无纺布,该无纺布上无纺布层、下无纺布层均由“y”型皮芯纤维构成,结构单一,上下层组分一致;专利公告号cn102534863a公开了一种双组份无纺布纺丝及其生产方法,该无纺布只体现了无纺布中纤维截面为三叶型。因此,单一的圆形长丝纤维或三叶型纤维,导致该非织造布应用领域受到一定限制,也是非织造布应用在过滤领域难题之一。
技术实现要素:4.本发明目的是提供一种用于过滤的双组分非织造布及其制备方法,所制成的非织造布强力高、压强小、透气率高、过滤效率高、表面光滑、使用寿命长,纤维之间的空隙率小,可提高非织造布的过滤效率,可提高纤网的粘合效果,不同纤度的纤维交叉分布,为纤网提供了更多的空隙,从而提高非织造布的过滤性能;可提高非织造布的透气率;表面光滑可提高非织造布的剥离性能,从而提高非织造布的使用寿命。
5.用于过滤领域的双组分纺粘法非织布,该非织造布由两层纤网组成,第一层纤网由不同纤度的三叶形pet长丝纤维和三叶形“低熔点聚合物”长丝纤维组成;第二层纤网由pet/“低熔点聚合物”“皮芯”型长丝纤维组成。
6.第一层纤网三叶形长丝纤维,单丝纤度2~7dtex,三叶形pet长丝纤维质量占纤网质量比为60~90%。
7.第一层纤网三叶形“低熔点聚合物”长丝纤维,其组份为co-pet、pp、pe、pa6。
8.第一层纤网质量与纤网质量比为30~70%。
9.第二层纤网“皮芯”型长丝纤维,单丝纤度4~12dtex。
10.第二层纤网“皮芯”型长丝纤维,其皮层“低熔点聚合物”组份为co-pet、pp、pe或pa6。
11.第二层纤网质量与纤网质量比为70~30%。
[0012]“皮芯”型长丝纤维,其芯层为pet,皮层组份为co-pet、pp、pe、pa6。
[0013]
优选的,用于过滤的双组分非织造布克重为15~140g/m2,产品厚度0.1~0.6mm。
[0014]
优选的,用于过滤的双组分非织造布透气率为1400~6100 1/m2.s@200pa。
[0015]
本发明的具体制备方法步骤如下:
[0016]
步骤1、原料:pet粘度0.65~0.72dl/g,熔点255~260℃;
[0017]
co-pet粘度0.65~0.72dl/g,熔点190~230℃,或pp熔指15~26g/10min,熔点148~176℃,或pe熔指15~26g/10min,熔点120~136℃,或pa6相对粘度2.65~2.75dl/g,熔点215~225℃。
[0018]
步骤2、结晶、干燥:pet预结晶温度155~185℃,干燥温度145~175℃,切片含水率≤30ppm;co-pet预结晶温度135~165℃,干燥温度125~155℃,切片含水率≤30ppm,或pa6干燥温度75~95℃,切片含水率≤50ppm。
[0019]
步骤3、熔融纺丝:pet螺杆长径比23~28,螺杆挤压机温度275~292℃,组件压力120~180bar;co-pet螺杆长径比23~28,螺杆挤压机温度245~272℃,组件压力100~160bar,纺丝温度285~292℃,熔融纺丝时需加入co-pet专用防滑母粒;或pp螺杆长径比28~35,螺杆挤压机温度220~260℃,组件压力100~160bar;纺丝温度285~292℃,熔融纺丝时需加入pp专用防滑母粒,或pe螺杆长径比28~35,螺杆挤压机温度210~260℃,组件压力100~160bar,纺丝温度285~292℃,熔融纺丝时需加入pe专用防滑母粒;或pa6螺杆长径比23~28,螺杆挤压机温度255~275℃,组件压力100~160bar,纺丝温度285~292℃,熔融纺丝时需加入pa6专用抗静电母粒。
[0020]
步骤4、侧吹风冷却:侧吹风送风温度10~22℃,送风相对湿度60~70%rh,风速0.3~1.6m/s。
[0021]
步骤5、牵伸:采用管式气流牵伸,气流牵伸压力4.0~6.0bar,牵伸速度≥4500m/min。
[0022]
步骤6、分丝铺网:采用机械分丝铺网,摆丝器频率500~800n/min。
[0023]
步骤7、热风粘合:粘合温度低于pet熔点高于co-pet熔点,温度控制在190℃~255℃;或粘合温度低于pet熔点高于pp熔点,温度控制在148℃~255℃;或粘合温度低于pet熔点高于pe熔点,温度控制在120℃~255℃;或粘合温度低于pet熔点高于co-pet熔点,温度控制在215℃~255℃。
[0024]
步骤8、收卷、分切:通过收卷机对半成品收卷,根据客户要求对半成品进行分切,形成成品,并对成品进行包装。
[0025]
本发明与现有技术相比具有如下优点:
[0026]
(1)纤网由两层组成,一层为三叶形长丝纤维,一层为圆形“皮芯”型长丝纤维,所制成的非织造布强力高、压强小、透气率高、过滤效率高、表面光滑、使用寿命长等优点;
[0027]
(2)本发明非织造布,三叶形长丝纤维层采用“混纤”型,利用三叶形纤维的比表面积的特性,改善纤维之间的抱合性;独特的三叶形结构,使纤维之间的空隙率小,提高了非织造布的过滤效率;
[0028]
(3)三叶形长丝纤维层,单丝纤度2~7dtex,“低熔点聚合物”长丝纤维,其组份为co-pet、pp、pe、pa6等,可以提高纤网的粘合效果,不同纤度的纤维交叉分布,为纤网提供了更多的空隙,从而提高非织造布的过滤性能;
[0029]
(4)本发明的非织造布,第二层为“皮芯”型长丝纤维组成,为非织造布提供了更多
的粘合点,采用此结构可以改善非织造布分层情况;
[0030]
(5)“皮芯”型长丝纤维层,单丝纤度4~12dtex,单丝较粗,经热粘合后,非织造布表面更加光滑,同时因纤维纤度较粗,可以提高非织造布的透气率;表面光滑可以提高非织造布的剥离性能,从而提高非织造布的使用寿命。
[0031]
(6)本发明的非织造布,“低熔点聚合物”其组份为co-pet、pp、pe、pa6等,根据不同的应用领域,采用不同的“低熔点聚合物”,克服了采用单一“低熔点聚合物”应用领域狭窄的弊端。
附图说明
[0032]
图1为本发明的三叶形纤维截面图。
[0033]
图2为本发明的“皮芯”型纤维截面图。
[0034]
图3为本发明的非织造布剖视图。
[0035]
1-第一层纤网三叶形长丝纤维、2-第二层纤网“皮芯”型长丝纤维、3-芯层、4-第一层纤网、5-第二层纤网。
具体实施方式
[0036]
用于过滤领域的双组分纺粘法非织布,该非织造布由两层纤网组成,第一层纤网4由不同纤度的三叶形pet长丝纤维和三叶形“低熔点聚合物”长丝纤维组成;第二层纤网5由pet/“低熔点聚合物”“皮芯”型长丝纤维组成。
[0037]
第一层纤网三叶形长丝纤维1,单丝纤度2~7dtex,三叶形pet长丝纤维质量占纤网质量比为60~90%。第一层纤网质量与纤网质量比为30~70%。
[0038]
第一层纤网三叶形“低熔点聚合物”长丝纤维2,其组份为co-pet、pp、pe、pa6。第二层纤网“皮芯”型长丝纤维,单丝纤度4~12dtex。
[0039]
第二层纤网“皮芯”型长丝纤维,单丝纤度4~12dtex。第二层纤网“皮芯”型长丝纤维,其皮层“低熔点聚合物”组份为co-pet、pp、pe、pa6。第二层纤网质量与纤网质量比为70~30%。“皮芯”型长丝纤维,其芯层3为pet,皮层组份为co-pet、pp、pe、pa6。
[0040]
用于过滤的双组分非织造布克重为15~140g/m2,产品厚度0.1~0.6mm。用于过滤的双组分非织造布透气率为1400~6100 1/m2.s@200pa。
[0041]
实施例1
[0042]
在图1、图2、图3所示的本发明的示意简图中,本发明的具体制备方法步骤如下:
[0043]
步骤1、原料:pet粘度0.65~0.72dl/g,熔点255~260℃;co-pet粘度0.65~0.72dl/g,熔点190~230℃。
[0044]
步骤2、结晶、干燥:pet预结晶温度155~185℃,干燥温度145~175℃,切片含水率≤30ppm;co-pet预结晶温度135~165℃,干燥温度125~155℃,切片含水率≤30ppm。
[0045]
步骤3、熔融纺丝:pet螺杆长径比23~28,螺杆挤压机温度275~292℃,组件压力120~180bar;co-pet螺杆长径比23~28,螺杆挤压机温度245~272℃,组件压力100~160bar;纺丝温度285~292℃,熔融纺丝时需加入co-pet专用防滑母粒。
[0046]
步骤4、侧吹风冷却:侧吹风送风温度16~22℃,送风相对湿度60~70%rh,风速0.3~0.8m/s。
[0047]
步骤5、牵伸:采用管式气流牵伸,气流牵伸压力4.0~6.0bar,牵伸速度≥4500m/min,
[0048]
步骤6、分丝铺网:采用机械分丝铺网,摆丝器频率500~800n/min。
[0049]
步骤7、热风粘合:粘合温度低于pet熔点高于co-pet熔点,温度控制在190~255℃之间。
[0050]
步骤8、收卷、分切:通过收卷机对半成品收卷,根据客户要求对半成品进行分切,形成成品,并对成品进行包装。
[0051]
实施例2
[0052]
在图1、图2、图3所示的本发明的示意简图中,本发明的具体制备方法步骤如下:
[0053]
步骤1、原料:pet粘度0.65~0.72dl/g,熔点255~260℃;pp熔指15~26g/10min,熔点148~176℃。
[0054]
步骤2、结晶、干燥:pet预结晶温度155~185℃,干燥温度145~175℃,切片含水率≤30ppm。
[0055]
步骤3、熔融纺丝:pet螺杆长径比23~28,螺杆挤压机温度275~292℃,组件压力120~180bar;pp螺杆长径比28~35,螺杆挤压机温度220~260℃,组件压力100~160bar;纺丝温度285~292℃,熔融纺丝时需加入pp专用防滑母粒。
[0056]
步骤4、侧吹风冷却:侧吹风送风温度10~18℃,送风相对湿度60~70%rh,风速0.6~1.2m/s。
[0057]
步骤5、牵伸:采用管式气流牵伸,气流牵伸压力4.0~6.0bar,牵伸速度≥4500m/min,
[0058]
步骤6、分丝铺网:采用机械分丝铺网,摆丝器频率500~800n/min。
[0059]
步骤7、热风粘合:粘合温度低于pet熔点高于pp熔点,温度控制在148~255℃之间。
[0060]
步骤8、收卷、分切:通过收卷机对半成品收卷,根据客户要求对半成品进行分切,形成成品,并对成品进行包装。
[0061]
实施例3
[0062]
在图1、图2、图3所示的本发明的示意简图中,本发明的具体制备方法步骤如下:
[0063]
步骤1、原料:pet粘度0.65~0.72dl/g,熔点255~260℃;pe熔指15~26g/10min,熔点120~136℃。
[0064]
步骤2、结晶、干燥:pet预结晶温度155~185℃,干燥温度145~175℃,切片含水率≤30ppm。
[0065]
步骤3、熔融纺丝:pet螺杆长径比23~28,螺杆挤压机温度275~292℃组件压力120~180bar;pe螺杆长径比28~35,螺杆挤压机温度210~260℃,组件压力100~160bar;纺丝温度285~292℃,熔融纺丝时需加入pe专用防滑母粒。
[0066]
步骤4、侧吹风冷却:侧吹风送风温度14~18℃,送风相对湿度60~70%rh,风速1.0~1.6m/s。
[0067]
步骤5、牵伸:采用管式气流牵伸,气流牵伸压力4.0~6.0bar,牵伸速度≥4500m/min,
[0068]
步骤6、分丝铺网:采用机械分丝铺网,摆丝器频率500~800n/min。
[0069]
步骤7、热风粘合:粘合温度低于pet熔点高于pe熔点,温度控制在120~255℃之间。
[0070]
步骤8、收卷、分切:通过收卷机对半成品收卷,根据客户要求对半成品进行分切,形成成品,并对成品进行包装。
[0071]
实施例4
[0072]
在图1、图2、图3所示的本发明的示意简图中,本发明的具体制备方法步骤如下:
[0073]
步骤1、原料:pet粘度0.65~0.72dl/g,熔点255~260℃;pa6相对粘度2.65~2.75dl/g,熔点215~225℃。
[0074]
步骤2、结晶、干燥:pet预结晶温度155~185℃,干燥温度145~175℃,切片含水率≤30ppm;pa6,干燥温度75~95℃,切片含水率≤50ppm。
[0075]
步骤3、熔融纺丝:pet螺杆长径比23~28,螺杆挤压机温度275~292℃,组件压力120~180bar;pa6螺杆长径比23~28,螺杆挤压机温度255~275℃,组件压力100~160bar;纺丝温度285~292℃,熔融纺丝时需加入pa6专用抗静电母粒。
[0076]
步骤4、侧吹风冷却:侧吹风送风温度20~24℃,送风相对湿度60~70%rh,风速0.3~0.6m/s。
[0077]
步骤5、牵伸:采用管式气流牵伸,气流牵伸压力4.0~6.0bar,牵伸速度≥4500m/min,
[0078]
步骤6、分丝铺网:采用机械分丝铺网,摆丝器频率500~800n/min。
[0079]
步骤7、热风粘合:粘合温度低于pet熔点高于co-pet熔点,温度控制在215~255℃之间。
[0080]
步骤8、收卷、分切:通过收卷机对半成品收卷,根据客户要求对半成品进行分切,形成成品,并对成品进行包装。