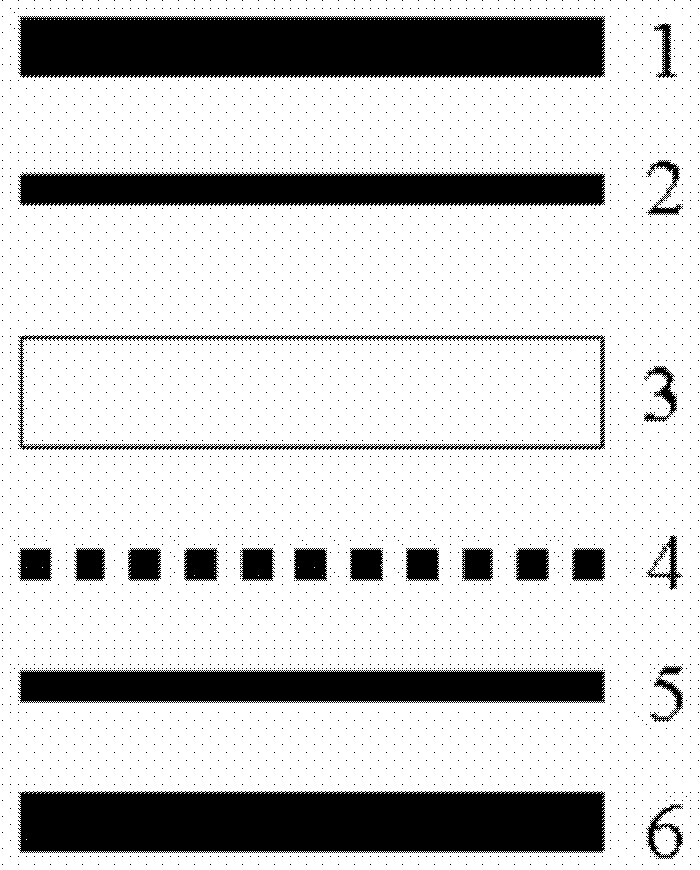
本发明涉及地板技术领域,尤其是涉及一种工业用复合地板及其制备方法。
背景技术:目前工业用的地板主要包括胶合板和钢制地板。传统的胶合板一般是将木材切割成若干毫米级的薄木片,再通过热压机将其热压胶合而成,但木质胶合板一般要将二十几层木质单板经过数十道工序完成,工序繁琐、劳动强度高、生产效率低下,且人为因素较大,不利于产品质量稳定性的提高。另外,木质胶合板的原材料主要以原始森林的阔叶木为主,并掺杂少部分速生林软木材,表面均为木质材料或类似无纺布贴膜材料,容易被破坏,影响使用寿命。钢制地板生产简单,但存在钢材太重、能源消耗高、不耐腐蚀、易变形等诸多问题,已逐步被淘汰。中国专利201020272078.6,一种纤维强化集装箱底板,公开了一种采用玄武岩纤维网/布作为木质胶合板的表面增强材料的集装箱底板。中国专利96232232.6,纤维强化复合集装箱底板,公开了一种采用玻纤布、尼龙布、锦纶布做为表面增强的夹芯复合集装箱底板。上述发明专利所用基材部分的木质胶合板为常规胶合板生产方法制成,工艺相对比较落后,效率低,属于劳动力密集型产业,可操作性较差,且没有提出复合材料与木质部分的界面进行胶结的有效解决方案。
技术实现要素:本发明的目的在于解决上述现有技术存在的问题和不足,提供一种复合地板及其制备方法,有利于生产效率的提高和地板表观质量的控制,且所用原材料具有优异的环保性能、加工性能和表面性能。为解决上述技术问题,本发明采用的技术方案为:一种复合地板,包括相胶合的基板和设置于该基板上表面、下表面至少之一上的面板层,所述基板由至少一层定向结构OSB板与至少一层单板组坯后热压而成,所述单板为顺纹木质单板或横纹木质单板或纤维预浸布或纤维毡中的至少一种,所述面板层为纤维增强树脂基复合材料FRP。所述的复合地板,其中,所述基板包括至少两层所述定向结构OSB板,相邻两层所述定向结构OSB板之间设置有一层所述的顺纹木质单板或横纹木质单板或纤维预浸布或纤维毡,所述基板的面层和底层均为顺纹木质单板。所述的复合地板,其中,所述基板的面层、或底层、或面层和底层沿其木纹方向开设有多个槽口,所述槽口的截面形状为半圆形或方形。所述的复合地板,其中,所述槽口的半径或宽度为1~3mm,槽深为0.5~3mm,相邻两所述槽口之间的间距为20~50mm。所述的复合地板,其中,所述基板与所述纤维增强树脂基复合材料FRP板之间采用双组分聚氨酯胶黏剂相胶合。所述的复合地板,其中,所述定向结构OSB板采用速生杨木、松木、硬杂木、软杂木或枝桠材中的至少一种制成,厚度为8~25mm。所述的复合地板,其中,所述的纤维增强树脂基复合材料FRP板是由连续纤维、短切毡及食品级树脂采用连续复合材料板材制备工艺制成,所述连续纤维经编单向或多轴向布制成,所用连续纤维为玻璃纤维、碳纤维、芳纶纤维或其他人造或合成纤维中的至少一种,所述食品级树脂为不饱和聚酯树脂、乙烯基树脂、环氧树脂或聚氨酯中的至少一种;所述FRP板的纤维质量含量为40~70%。所述的复合地板,其中,所述复合地板的组坯方式可以为:FRP板、顺纹木质单板、定向结构OSB板、横纹木质单板、顺纹木质单板、FRP板。所述的复合地板,其中,所述复合地板的组坯方式可以为:FRP板、顺纹木质单板、定向结构OSB板、纤维预浸布或纤维毡、定向结构OSB板、横纹木质单板、顺纹木质单板、顺纹木质单板。所述的复合地板,其中,所述复合地板的组坯方式可以为:FRP板、顺纹木质单板、定向结构OSB板、横纹木质单板、定向结构OSB板、横纹木质单板、顺纹木质单板、顺纹木质单板、FRP板。所述的复合地板,其中,所述复合地板的组坯方式可以为:顺纹木质单板、定向结构OSB板、横纹木质单板、定向结构OSB板、横纹木质单板、定向结构OSB板、顺纹木质单板、顺纹木质单板、FRP板。所述的复合地板,其中,所述复合地板的组坯方式可以为:FRP板、顺纹木质单板、顺纹木质单板、定向结构OSB板、纤维预浸布或纤维毡、定向结构OSB板、纤维预浸布或纤维毡、定向结构OSB板、顺纹木质单板、顺纹木质单板、FRP板。所述的复合地板,其中,所述复合地板的上表面上喷涂有一层聚氨酯(脲)表面材料。一种复合地板的制备方法,包括基板制备步骤、FRP板制备步骤、FRP板与基板的热压复合步骤,其中。A、所述基板制备步骤为:按所述复合地板的组坯方式组坯并采用热压工艺胶合制成。B、所述FRP板制备步骤为:将一层至多层连续纤维、短切毡及食品级树脂进行铺层,并采用连续复合材料板材制备工艺制成。C、所述FRP板与基板的热压复合步骤包括:c1、所述基板的表面处理:对所述基板的上表面、下表面或上下表面进行砂光,并在所述基板的上表面、下表面或上下表面沿木纹长度方向开设多个槽口,所述槽口的截面形状为半圆形或方形槽;c2、所述FRP板的粘接面的粗糙化处理:采用专用砂光机对所述FRP板的粘接面进行粗糙化处理;c3、布胶及冷压处理:将双组分聚氨酯按照一定的比例混合,均匀涂覆在所述FRP板和基板的粘接面上,涂覆量为300~800g/m2,两者粘接后进行冷压得毛坯板,冷压压力为0.5~2MPa,冷压时间为5~20min;c4、热压固化:将经过冷压的所述毛坯板进行热压,热压压力为0.5~2MPa,热压时间为15~40min,热压温度为60℃~80℃;热压完成后进行冷却1~3小时即得成品。所述的复合地板的制备方法,其中,所述FRP板制备步骤中,所述连续纤维经编单向或多轴向布制成;所述连续纤维为玻璃纤维、碳纤维、芳纶纤维或其他人造或合成纤维中的至少一种;所述食品级树脂为不饱和聚酯树脂、乙烯基树脂、环氧树脂或聚氨酯中的至少一种;所述FRP板的纤维质量含量为40~70%。所述的复合地板的制备方法,其中,所述制备方法还包括所述复合地板的上表面处理步骤:所述复合地板的上表面采用高压无溶剂喷涂技术喷涂聚氨酯(脲),喷涂厚度为0.5~2mm。所述的复合地板的制备方法,其中,所述制备方法还进一步包括所述复合地板的封边处理步骤:所述复合地板用环保水性漆或聚氨酯进行封边处理。所述的复合地板的制备方法,其中,所述FRP板的厚度为1~2mm,所述基板的厚度为24~27mm。与现有技术相比,本发明的复合地板及其制备方法,具有以下优点。一、全新的生产方式:本发明以定向结构OSB板为基板,以纤维增强树脂基复合材料FRP板和/或一层聚氨酯(脲)表面材料为面板层,实现了传统地板的原材料替代,为自然环境的保护开创了新的思路。另外,采用FRP板与定向结构OSB板胶合,再加上聚氨酯(脲)表面处理,不仅弥补了OSB板强度和模量低等力学性能的不足,还大大提高了产品的表观质量。二、环保性:本发明的基板采用定向结构OSB板,其原料主要为软针、阔叶树材的小径木、速生间伐材等,如桉树、杉木、杨木间伐材等,来源广泛,其树脂采用MDI(二苯基甲烷二异氰酸酯)胶且不含甲醛,确保了OSB板的环保性能。纤维增强树脂基复合材料FRP板采用食品级树脂。而本发明所用的主要材料玻璃纤维的主要原料是:石英砂、氧化铝和叶蜡石、石灰石、白云石、硼酸、纯碱、芒硝、萤石等,因此无论从原料来源和使用性能上,本发明的复合地板环保性都是原工艺无法比拟的。而所用表面材料聚氨酯(脲)弹性体及基板与FRP面板层之间所用的聚氨酯胶黏剂、OSB板都是世界上公认的环保材料。三、加工性:本发明的制备方法优良的加工性能主要体现在木质基板复合、FRP板制备及表面处理等三个方面。木质基板方面:大幅度减少了地板的复合层数,如果是用于集装箱底板,由原来的21层减为3~10层,大大的减少了布胶层数,并可根据实际情况进行完全流水线操作,生产效率是一个重大突破。FRP板方面:采用已经成熟的连续复合材料板材生产线流水线制作而成。③聚氨酯(脲)弹性体喷涂方面:采用高压无溶剂喷涂技术,可实现流水线作业、技术先进、固化快、操作简单。上述过程均可实现流水线生产作业,有效解决了生产效率、降低劳动强度、减少人力成本等问题。四、表面性能:本发明的复合地板根据需要在其上表面采用FRP板或喷涂聚氨酯(脲)弹性体,具有优异的防水、防火、防滑、耐磨、耐腐蚀、抗冲击等性能,产品表面为非亲油性物质,有优良的自洁功能,且不会生菌变腐;可以根据客户要求调整各种颜色,且颜色稳定好。原材料环保、制备方法环保、产品无污染物释放;优良的静曲强度和弹性模量;⑤表面涂料聚氨酯具有反应速度快,凝胶时间短,喷涂层无接缝,防滑表面自然形成,还具有优异的物理化学性能。附图说明图1是本发明实施例1的复合地板采用包括单层定向结构OSB板的基板与FRP板双面复合的结构示意图。图2是本发明实施例2的复合地板采用包括双层定向结构OSB板的基板与FRP板单面复合的结构示意图。图3是本发明实施例3的复合地板采用包括双层定向结构OSB板的基板与FRP板双面复合的结构示意图。图4是本发明实施例4的复合地板采用包括三层定向结构OSB板的基板与FRP板单面复合的结构示意图。图5是本发明实施例5的复合地板采用包括三层定向结构OSB板的基板与FRP板双面复合的结构示意图。图6是本发明的复合地板中基板所开槽口的结构示意图。图中:代表“FRP板”。代表“定向结构OSB板”。代表“纤维预浸布或纤维毡”。代表“顺纹木质单板”。代表“横纹木质单板”。具体实施方式以下结合附图与实施例,对本发明予以进一步地详尽阐述。本发明的复合材料地板包括相胶合的基板和设置于该基板上表面、下表面至少之一上的面板层。其中,基板是由定向结构OSB板与单板组坯后热压而成的。本发明所用的定向结构OSB板,又称为“定向刨花板(OrientedStrandboard,OSB,简称OSB)”,国内称之为欧松板。是采用经干燥、筛选,施加胶粘剂和添加剂的扁平窄长刨花,经定向铺装后热压而成的一种结构板材。由于是由许多木片层层交叉叠压在一起,所以具有很高的强度。其所用材料为软针、阔叶树材的小径木、速生间伐材等,如杨木、松木、硬杂木、软杂木及其枝桠材中的一种或多种制备而成,一般厚度为8~25mm,密度为0.65g/cm3左右。而单板为木质单板或纤维预浸布或纤维毡中的至少一种。其中,木质单板采用具有FSC森林认证木材中的一种,如杨木、榉木等,单板厚度为0.8~2mm。在基板的组成中,至少包括一层定向结构OSB板与至少一层单板,单板层数根据具体需要而定。当基板包括至少两层定向结构OSB板时,相邻的两层定向结构OSB板之间会设置有顺纹木质单板、横纹木质单板、纤维预浸布或纤维毡的一种,而基板的面层和底层则为顺纹木质单板。而面板层采用以下两种结构。第一种:面板层设置在基板上表面或者下表面上,或者在上下表面同时设置。面板层为纤维增强树脂基复合材料FRP板,纤维增强树脂基复合材料FRP(FiberReinforcedPlastics)即纤维强化塑料,是由连续纤维、短切毡及食品级树脂采用连续复合材料板材制备工艺制成,连续纤维经编单向或多轴向布制成,所用连续纤维为玻璃纤维、碳纤维、芳纶纤维或其他人造或合成纤维中的至少一种,其纤维质量含量为40~70%,厚度为0.5~2mm。纤维采用450g/m2的平纹布和200g/m2的纤维毡。在现有复合地板中,基板与面板层界面间的粘接问题一直是妨碍其整体性能提高的重要因素,由于两者自身不同的热膨胀系数和化学反应特性,在受力时最主要的破坏形式就是分层,特别是FRP板与木质材料两种不同材质进行粘接复合。而本发明的复合地板的基板与FRP板之间采用双组分聚氨酯胶黏剂相胶合,胶黏剂涂覆量为300~800g/m2,该双组分聚氨酯可操作时间可根据工艺需求进行调节,与FRP板和木材有良好的粘接性能,且其机械强度大、耐老化、耐候性强、弹性好,在承受动态载荷时具有优良的复原记忆性,使用寿命可达15~20年,解决了基板与面板层界面间的粘接问题。第二种:面板层设置在基板上表面或者下表面上,或者在上下表面同时设置。然后在上面板层的上表面再喷涂一层具有高耐磨、耐腐蚀性能的聚氨酯(脲)弹性体,这样不对称结构的地板在受载荷作用时,上表面/下表面提供强大的抗冲击力、压应力,下表面/上表面提供强大的拉应力,可最大限度的发挥增强纤维高强、高模的性能,以抵抗地板的弯曲变形,有效弥补OSB板力学性能的不足。另外,如图6所示,在基板的面层或底层,或同时在面层和底层沿其自身的木纹方向上(如图中箭头所示)开设有多个槽口20,槽口20的截面形状可为半圆形或方形,图中所示的为半圆形,槽口20的半径或宽度为1~3mm,槽深为0.5~3mm,相邻的两槽口之间的间距为L为20~50mm,槽口20的长度可与基板的长度相同。这样有利于增大胶黏剂与基板表面的粘接面积和相互抓紧力,提高粘接强度。下面列出几种典型的基板与FRP板复合地板组坯方式的实施例(图1~5中数字标号代表组成地板的不同层数)。实施例1如图1所示,本发明实施例1的复合地板采用包括单层定向结构OSB板的基板与FRP板双面复合,面板层为对称结构,表面层为纤维增强复合材料FRP板。具体组坯方式为(按由上至下1、2、3、4、5、6层的顺序排列):FRP板、顺纹木质单板、定向结构OSB板、横纹木质单板、顺纹木质单板、FRP板,总层数为6层。其中FRP板的厚度为1~2mm,基板的厚度为24~26mm。实施例2如图2所示,本发明实施例2的复合地板采用包括双层定向结构OSB板的基板与FRP板单面复合,面板层为非对称结构,上面板层为纤维增强复合材料FRP板。具体组坯方式为(按由上至下1、2、3、4、5、6、7、8层的顺序排列):FRP板、顺纹木质单板、定向结构OSB板、纤维预浸布或纤维毡、定向结构OSB板、横纹木质单板、顺纹木质单板、顺纹木质单板,总层数为8层。其中,FRP板的厚度为1~2mm,基板的厚度为26~27mm。实施例3如图3所示,本发明实施例3的复合地板采用包括双层定向结构OSB板的基板与FRP板双面复合,面板层为对称结构,上下面板层均为纤维增强复合材料FRP板。具体组坯方式为(按由上至下1、2、3、4、5、6、7、8、9层的顺序排列):FRP板、顺纹木质单板、定向结构OSB板、横纹木质单板、定向结构OSB板、横纹木质单板、顺纹木质单板、顺纹木质单板、FRP板,总层数为9层。其中,FRP板的厚度为1~2mm,基板的厚度为24~26mm。实施例4如图4所示,本发明实施例4的复合地板采用包括三层定向结构OSB板的基板与FRP板单面复合,面板层为非对称结构,下面板层为纤维增强复合材料(FRP)板。具体组坯方式为(按由上至下1、2、3、4、5、6、7、8、9层的顺序排列):顺纹木质单板、定向结构OSB板、横纹木质单板、定向结构OSB板、横纹木质单板、定向结构OSB板、顺纹木质单板、顺纹木质单板、FRP板,总层数为9层。其中,FRP板的厚度为1~2mm,基板的厚度为26~27mm。实施例5如图5所示,本发明实施例5的复合地板采用包括三层定向结构OSB板的基板与FRP板双面复合,面板层为为对称结构,上下面板层均为纤维增强复合材料FRP板。具体组坯方式为(按由上至下1、2、3、4、5、6、7、8、9、10、11层的顺序排列):FRP板、顺纹木质单板、顺纹木质单板、定向结构OSB板、纤维预浸布或纤维毡、定向结构OSB板、纤维预浸布或纤维毡、定向结构OSB板、顺纹木质单板、顺纹木质单板、FRP板,总层数为11层。其中FRP板的厚度为1~2mm,基板的厚度为24~26mm。需要说明的是,由以上实施例可以看出,FRP板的厚度为1~2mm,基板的厚度在24~27mm之间。本发明的复合地板的FRP板与基板的组坯方式包括但不限于以上几种实施例,可根据用途不同或不同客户对性能的要求和原材料的不同,进行优化设计。下面详细说明以上实施例中的复合地板的制备方法,其包括基板制备步骤、FRP板制备步骤、FRP板与基板的热压复合步骤,其中。A、基板制备步骤:采用传统胶合板的制备工艺,根据复合地板的组坯方式组坯并采用热压工艺胶合制成。由于传统胶合板的制备工艺已经为现有技术,故在此不再详述。B、FRP板制备步骤:将一层至多层连续纤维、短切毡及食品级树脂进行铺层,并采用连续复合材料板材制备工艺制成,由于续复合材料板材制备工艺也为传统制备工艺,故在此也不再详述。C、FRP板与基板的热压复合步骤包括:c1、基板的表面处理:对基板的上表面、下表面或上下表面进行砂光,并在基板的上表面、下表面或上下表面沿木纹长度方向开设多个槽口,槽口的截面形状为半圆形或方形槽,槽口的半径或宽度,相邻两间的间距为25~50mm,槽深为0.5~3mm;c2、FRP板的粘接面的粗糙化处理:采用专用砂光机对所述FRP板的粘接面进行粗糙化处理;c3、布胶及冷压处理:将双组分聚氨酯按照一定的比例混合,均匀涂覆在FRP板和基板的粘接面上,其涂覆量为300~800g/m2,两者粘接后进行冷压,冷压压力为0.5~2.0MPa,冷压时间为5~20min;c4、热压固化:将经过冷压的毛坯板进行热压,热压压力为0.5~2.0MPa,热压时间为15~40min,热压温度为60℃~80℃;热压完成后进行冷却1~3小时即得成品。在上述FRP板制备步骤中,所述连续纤维经编单向或多轴向布制成;所述连续纤维为玻璃纤维、碳纤维、芳纶纤维或其他人造或合成纤维中的至少一种;所述食品级树脂为不饱和聚酯树脂、乙烯基树脂、环氧树脂、聚氨酯中的至少一种;所述FRP板的纤维质量含量为40~70%。进一步地,本发明的复合地板的制备方法还包括复合地板的上表面处理步骤:即在复合地板的上表面采用高压无溶剂喷涂技术喷涂聚氨酯(脲)弹性体,该弹性体为无溶剂双组份聚氨酯,喷涂厚度为0.5~2mm。本发明首次将该技术用于复合地板中。聚氨酯(脲)弹性体各项性能卓越:成膜后邵氏硬度在50~90之间;撕裂强度大于等于560N/cm;拉伸强度大于10MPa;凝胶时间为10~90s;同时还具有优异的耐腐蚀性和耐磨性,可耐98%的浓硫酸和50%的氢氧化钠,根据GB/T17657-1999中耐磨性能的测试方法,在转速为70r/min转数为10000r条件下,表面涂料无明显损伤。更进一步地,本发明的复合地板的制备方法还包括封边处理:考虑到OSB板的吸潮膨胀影响地板的性能,本发明工艺上专门设计了用环保水性漆或聚氨酯进行封边,其防水性能比普通木地板更优秀。需要进一步说明的是,上述实例1~5种结构的复合地板表面采用高压无溶剂喷涂技术喷涂聚氨酯(脲)弹性体的处理方式,具体采用了高压无空气自动化喷涂技术,该喷涂技术是目前全世界最先进的喷涂方式,其原理是将A、B两组份涂料分别置于两料筒,根据需要分别进行加温处理,再经由高压计量泵和喷枪喷涂到地板表面,喷涂压力一般大于10MPa,地板则以流水线形式匀速通过喷枪完成表面的喷涂过程,其喷涂厚度为0.5~2mm,该高压喷涂技术具有雾化粒子细、飞散物料损失少的优点。本发明的复合地板可广泛运用于集装箱地板、车辆用地板和海洋工程用地板等。只要根据具体使用的强度、厚度要求采用不同的组坯方式即可。上述内容,仅为本发明的较佳实施例,并非用于限制本发明的实施方案,本领域普通技术人员根据本发明的主要构思和精神,可以十分方便地进行相应的变通或修改,故本发明的保护范围应以权利要求书所要求的保护范围为准。