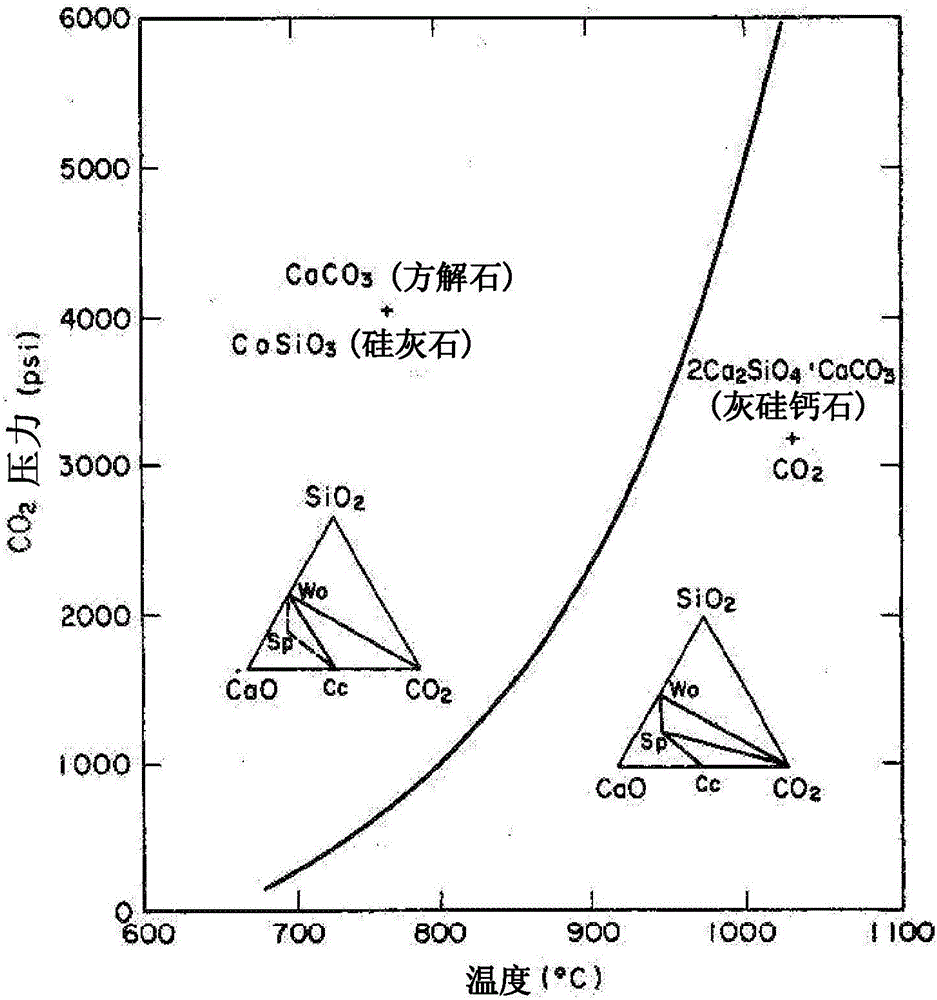
本申请要求2013年8月21日提交的美国临时申请序列号61/868,155的权益,其全部内容以其整体通过引用并入本文。
技术领域:
本发明大体涉及充气复合材料和充气混凝土。更具体地,本发明涉及新型的充气复合材料,以及其配方、制造方法和用途。该充气复合材料适于建筑、耐火和隔热、景观、以及基础结构等多种应用。
背景技术:
:热压充气混凝土是一类轻质预制混凝土,该预制混凝土是使用诸如水泥的原材料、诸如砂或其他填充材料的细集料、石灰、水及充气剂在高温及高压下形成的。充气剂使基质中形成气隙并且提高材料的孔隙率,同时使材料体积增加并且使密度降低。充气混凝土制品提供许多优于传统混凝土的优势,包括强度良好、重量轻、耐火、耐腐蚀、耐白蚁及耐霉菌,以及良好的隔热和消音特性。充气混凝土由于其重量轻及尺寸精确,能够在废料最少的情况下装配,从而在建筑及装配时减少对其他设备的需要。充气混凝土提供高耐久性,并且需要的维护最少。充气混凝土的重量轻还有助于降低货运成本。虽然与混凝土相比是有利的,但是大部分传统充气混凝土是通过具有许多缺陷的方法制备的。传统充气混凝土的制造方法涉及特殊设备、大量能量消耗及过度的二氧化碳排放,留下不利的碳足迹。例如,充气混凝土通常在高压釜中、在150℃至190℃范围内的温度以及110psi至180psi范围内的压力下固化,从而产生稳定形式的雪硅钙石。雪硅钙石是充气混凝土中的主要接合单元。另外,充气混凝土由于精加工成本高、回收困难等原因而相对昂贵。对于满足或超过充气混凝土的物理及性能特性的新颖充气复合材料存在持续性的需要,所述充气混凝土能够以较低的成本、改善的能量消耗及更合乎需要的碳足迹大量生产。发明概述本发明部分地基于出乎意外地发现的新型充气复合材料,所述充气复合材料具有充气混凝土的优秀物理及性能特性。该复合材料能够容易地从可广泛获得的低成本原材料、利用适于大规模生产的方法生产,具有减少的设备需要、改进的能量消耗以及更合乎需要的碳足迹。本发明的充气复合材料配方需要最容易获得且成本低的材料,其具有最小的环境影响。原材料包括成为接合单元的前体材料,诸如微粒硅酸钙(例如,研磨硅灰石(CS)、假硅灰石、硅钙石(C3S2)、钙铝黄长石(C2AS)、斜硅钙石(C2S)和硅酸三钙石(C3S),其中根据水泥化学家标记法(CCN),“C”代表氧化钙或石灰、“S”代表二氧化硅或硅土、“A”代表氧化铝或矾土)与某些成为接合单元的痕量杂质,以及微粒填充材料(例如,含氧化钙材料,诸如石灰石、硬硅钙石、硅粉和石英;轻质集料,诸如珍珠岩或蛭石;或者甚至工业废料,诸如飞灰、底灰和炉渣)。为了获得高度多孔的材料,使用充气剂(例如,铝粉或铝浆)。还提供流体组分作为反应介质,所述流体组分包含液态水和/或水蒸汽及试剂二氧化碳(CO2),所述二氧化碳在生产中作为反应性物种而消耗并且最后固存于最终产品中。接合单元在受控的温度和压力下,使用反应在水和水蒸汽之间发生的水化过程或者使用水蒸汽和CO2进行反应。取决于最终使用者需求,还能够添加各种其他添加剂,诸如分散、流变改性掺混剂(用以提高混合物的一致性)、着色颜料、缓凝剂和促凝剂。添加剂材料可以包括天然或回收材料,富碳酸钙材料和富碳酸镁材料,以及流体组分的添加剂,诸如水溶性分散剂。另外,能够使用高效的气体辅助式热液液相烧结(HLPS)方法、以低成本、较少的设备需求以及大为改善的能量消耗和碳足迹生产本发明的充气复合材料。在一个方面中,本发明大体涉及一种充气复合材料制品的制造方法。所述方法包括:(1)形成湿混合物,其中湿混合物包含:水、研磨硅酸钙、填料颗粒和充气剂;(2)在模具中浇铸湿混合物;(3)使充气剂产生气态产物,从而使湿混合物产生体积膨胀;(4)在水和CO2的气氛下、在约20℃至约100℃范围内的温度下预固化膨胀的混合物足够的时间,从而得到具有适于实现脱模和/或切割所需的足够的早期强度的预固化物;(5)脱模和/或切割预固化物至期望的尺寸;以及(6)在水蒸汽和CO2的气氛下、在约20℃至约100℃范围内的温度下进一步固化脱模和/或切割的预固化物约6小时至约60小时,从而生产制品。研磨硅酸钙具有约0.25μm至约5μm范围内的比粒度d10、约5μm至约20μm范围内的比粒度d50、以及约25μm至约100μm范围内的比粒度d90。填料颗粒包含氧化钙或二氧化硅,并且具有约0.25μm至约200μm范围内的粒度(d50)。研磨硅酸钙包括合成硅灰石、假硅灰石、硅钙石、钙铝黄长石、斜硅钙石和硅酸三钙石的一种以上。在另一个方面中,本发明大体涉及由根据本发明公开的方法生产的制品。在又一个方面中,本发明大体涉及一种充气复合材料,该充气复合材料包含:(1)多个接合单元,所述接合单元的特征为具有约0.25μm至约5μm范围内的比粒度d10、约5μm至约20μm范围内的比粒度d50、以及约25μm至约100μm范围内的比粒度d90;(2)多个填料颗粒,所述填料颗粒具有约0.5μm至约500μm范围内的粒度;(3)多个孔隙。每个接合单元包含:主要包含硅酸钙的核心,富二氧化硅的第一层或内层,以及富碳酸钙的第二层或外层。多个接合单元与多个填料颗粒一起形成一个以上接合基质,并且接合单元与填料颗粒大致均匀地分散于其中并且接合在一起。多个孔隙为鼓泡状和/或互连通道,占充气复合材料的约50vol.%至约80vol.%。充气复合材料展现约300kg/m3至1500kg/m3的密度、约2.0MPa至约8.5MPa的压缩强度、以及约0.4MPa至约1.7MPa的挠曲强度。附图说明通过参考以下描述的附图以及权利要求书,能够更好地理解本发明的目标和特征。附图未必是按比例的,用于强调而不是一般地说明本发明的原理。在附图中,相似的数字用于在各种视图中代表相似的部分。图1是示出可逆反应中存在的相的压力-温度相图。图2是示出可逆反应中存在的相的压力-温度相图。图3是1千巴压力下的CaO-SiO2-CO2系统的相图。图4是示出可逆反应中存在的相的压力-温度相图。图5是示出可逆反应中,惰性气体中CO2的比例的函数的平衡曲线的压力-温度相图。图6是说明CaCO3-MgCO3系统中各个相的稳定区域的温度-组成相图。图7是说明化合物CaO、MgO、SiO2和CO2之间的相关系的四面体图,并且示出Cc-Di-Wo和Cc-Wo-Mo平面下方的CO2缺陷区域(阴影),其中Cc代表方解石、Wo代表硅灰石、Ak代表钙镁黄长石、Di代表透辉石、并且Mo代表钙镁橄榄石(CaMgSiO4)。图8是说明化合物CaO、MgO、SiO2和CO2之间的相关系的压力-温度相图,以及从四元不变点发出的涉及方解石(Cc)、透辉石(Di)、镁橄榄石(Fo)、钙镁橄榄石(Mo)、钙镁黄长石(Ak)和CO2的单变量曲线。嵌入图是CaCO3、MgO和SiO2的三化合物系统的相图。图9是根据本发明的原理提供加湿的CO2复合材料固化腔室的示意图。图10是固化腔室的示意图,该固化腔室具有多种湿度控制方法以及使用恒定流量或压力调控来控制并补充CO2,并且能够根据本发明的原理控制温度。图11(a)-11(c)是根据本发明的例示性实施例的接合单元的横截面的示意性说明,包括三种例示性核心形态:(a)纤维状,(b)椭圆形,以及(c)等轴晶状。图12(a)-12(f)是根据本发明的示例性实施例的复合材料的侧视图及横截面视图的示意性说明,示出(a)处于稀接合基质中的1D取向纤维状接合单元(接合单元未接触);(b)处于稀接合基质中的2D取向片状接合单元(接合单元未接触);(c)处于稀接合基质中的3D取向片状接合单元(接合单元未接触);以及(d)处于稀接合基质中的随机取向片状接合单元(接合单元未接触),其中复合材料包括接合基质和填料组分,诸如聚合物、金属、无机颗粒、集料等;(e)接合单元的浓缩接合基质(具有足以建立渗滤网络的体积分数),其中基质3D取向;以及(f)随机取向接合单元的浓缩接合基质(具有足以建立渗滤网络的体积分数),其中可以包含填料组分,诸如聚合物、金属、无机颗粒、集料等。图13示出使用合成硅灰石制得的充气混凝土的切割样品(4英寸×4英寸×4英寸,用于展示目的)的实例。具体实施方式本发明提供了新型的充气复合材料和由其制造的制品,所述充气复合材料及制品不仅具有充气混凝土的优秀物理及性能特性,而且容易由可广泛获得的低成本原材料经适于大规模生产的方法生产,具有改善的能量消耗、减少的设备需要(例如,无需高压釜)以及更合乎需要的碳足迹。本发明的充气复合材料可以用于承重或非承重应用中。与传统充气混凝土相比,本发明的充气复合材料的孔结构的均质性质还赋予其优越的隔热及隔音性能。另外,本发明的充气复合材料能够容易地以较大尺寸制备,诸如大型墙壁、地板或屋面板及景观块体。本发明的充气复合材料展现优秀的隔离质量(隔热与隔音)以及耐火性。相比传统的充气混泥土,其能够以大为改善的能量效率以及更合乎需要的碳足迹大规模生产。充气复合材料的生产消耗CO2,从而获得净CO2固存,由此使充气复合材料的生产为碳中性并且从经济与环境保护观点来看均异常高效。另外,这些充气复合材料的固态和均质孔结构产生气密的建筑围护结构,在帮助维持期望的室内温度的同时最小化不可控的气体交换,同时最大化HVAC设备的效率。本发明的独特的充气复合材料所带来的额外益处为减少材料的使用、能够使用回收产品、以及避免毒物排放。在一个方面中,本发明大体涉及一种充气复合材料制品的制造方法。所述方法包括:(1)形成湿混合物,其中湿混合物包含:水、研磨硅酸钙、填料颗粒和充气剂;(2)在模具中浇铸湿混合物;(3)使充气剂产生气态产物,从而使湿混合物产生体积膨胀;(4)在水和CO2的气氛下、在约20℃至约100℃范围内的温度下预固化膨胀的混合物足够的时间,从而得到具有适于实现脱模和/或切割所需的足够的早期强度的预固化物;(5)脱模和/或切割预固化物至期望的尺寸;以及(6)在水蒸汽和CO2(如果需要)的气氛下、在约20℃至约100℃范围内的温度下进一步固化脱模和/或切割的预固化物约6小时至约60小时,从而生产制品。研磨硅酸钙具有约0.25μm至约5μm范围内的比粒度d10、约5μm至约20μm范围内的比粒度d50、以及约25μm至约100μm范围内的比粒度d90。填料颗粒包含氧化钙或二氧化硅,并且具有约0.25μm至约200μm范围内的粒度(d50)。研磨硅酸钙包括合成硅灰石、假硅灰石、硅钙石、钙铝黄长石、斜硅钙石和硅酸三钙石的一种以上。在某些实施方式中,湿混合物还包括:硬化控制剂、气泡稳定剂和分散/粘度改性剂。在某些实施方式中,湿混合物还包括选自分散、流变改性掺混剂、颜料、缓凝剂和促凝剂的添加剂。在某些实施方式中,形成湿混合物包括以指定的添加顺序混合下列配料:添加预定份量的水;添加并且混合硬化控制掺混剂;添加并且混合分散/粘度改性剂;添加并且混合研磨硅酸钙;添加并且混合填料颗粒以形成均一浆料;以及添加并且混合充气剂。在某些实施方式中,湿混合物包含以指定百分比(湿混合物的wt%)混合的下列配料:研磨硅酸钙占约40wt%至约95wt%(例如,约40wt%至约95wt%、约50wt%至约95wt%、约60wt%至约95wt%、约70wt%至约95wt%、约40wt%至约90wt%、约40wt%至约80wt%、约40wt%至约70wt%、约40wt%至约60wt%),填料颗粒占约0wt%至约30wt%(例如,约0wt%至约25wt%、约0wt%至约20wt%、约0wt%至约15wt%、约0wt%至约10wt%、约5wt%至约30wt%、约10wt%至约30wt%、约15wt%至约30wt%、约20wt%至约30wt%),硬化控制掺混剂占约0wt%至约0.05wt%(例如,约0wt%至约0.03wt%、约0wt%至约0.02wt%、约0.01wt%至约0.05wt%、约0.02wt%至约0.05wt%、约0.03wt%至约0.05wt%),分散/粘度改性剂占约0.05wt%至约0.25wt%(例如,约0.05wt%至约0.20wt%、约0.05wt%至约0.15wt%、约0.05wt%至约0.10wt%、约0.10wt%至约0.25wt%、约0.15wt%至约0.25wt%、约0.20wt%至约0.25wt%),以及充气剂占约0.05wt%至约0.30wt%(例如,约0.05wt%至约0.25wt%、约0.05wt%至约0.20wt%、约0.05wt%至约0.15wt%、约0.05wt%至约0.10wt%、约0.15wt%至约0.30wt%、约0.20wt%至约0.30wt%、约0.25wt%至约0.30wt%)。在某些实施方式中,第一份水占湿混合物总水含量的约60%至约95%(例如,约60%至约90%、约60%至约80%、约60%至约70%、约70%至约95%、约80%至约95%、约90%至约95%),并且第二份水占湿混合物总水含量的约5%至约40%(例如,约5%至约30%、约5%至约20%、约5%至约10%、约10%至约40%、约15%至约40%、约20%至约40%、约30至约40%)。在某些实施方式中,第一份水占湿混合物总水含量的约90%,并且第二份水占湿混合物总水含量的约10%。在某些实施方式中,预固化膨胀的混合物在从环境压力至高于环境约30psi、以及约25%至约99.5%范围内(例如,约50%至约99.5%、约60%至约99.5%、约70%至约99.5%、约80%至约99.5%、约90%至约99.5%、约25%至约99%、约25%至约90%、约25%至约80%、约50%至约90%、约50%至约80%、约50%至约60%)的CO2浓度下进行,从而生产充气复合材料。在某些实施方式中,预固化步骤在包含水和CO2的蒸汽下、在约20℃至约80℃范围内(例如,约20℃至约70℃、约20℃至约60℃、约30℃至约80℃、约40℃至约80℃、约50℃至约80℃、约60℃至约80℃)的温度下进行约1小时至约10小时(例如,约1小时至约8小时、约1小时至约6小时、约1小时至约4小时、约2小时至约10小时、约4小时至约10小时、约6小时至约10小时)。在某些实施方式中,预固化步骤在包含水和CO2的蒸汽下、在约60℃的温度下进行约1小时至约5小时(例如,约2、3、4、5小时)。在某些实施方式中,进一步固化预固化物在具有约环境大气压力至高于环境大气压力约30psi(例如,约环境大气压力至高于环境大气压力约20psi、约环境大气压力至高于环境大气压力约10psi、高于环境大气压力约10psi至高于环境大气压力约30psi)的范围内的压力的包含水和CO2的蒸汽下、在约20℃至约80℃范围内(例如,约20℃至约70℃、约20℃至约60℃、约30℃至约80℃、约40℃至约80℃、约50℃至约80℃、约60℃至约80℃)的温度下进行约5小时至约40小时(例如,约5小时至约30小时、约5小时至约20小时、约5小时至约15小时、约10小时至约40小时、约15小时至约40小时、约20小时至约40小时)。在某些实施方式中,进一步固化预固化物在具有约环境大气压力至高于环境大气压力约60psi(例如,约环境大气压力至高于环境大气压力约60psi、约环境大气压力至高于环境大气压力约50psi、约环境大气压力至高于环境大气压力约40psi、约环境大气压力至高于环境大气压力约30psi、约环境大气压力至高于环境大气压力约20psi、高于环境大气压力约10psi至高于环境大气压力约60psi、高于环境大气压力约20psi至高于环境大气压力约60psi、高于环境大气压力约30psi至高于环境大气压力约60psi、高于环境大气压力约40psi至高于环境大气压力约60psi)的范围内的压力的包含水和CO2的蒸汽下、在约30℃至约70℃范围内(例如,约30℃至约60℃、约30℃至约50℃、约30℃至约40℃、约40℃至约70℃、约50℃至约70℃、约60℃至约70℃、约30℃至约60℃)的温度下进行约10小时至约30小时(例如,约10小时至约25小时、约10小时至约20小时、约10小时至约15小时、约15小时至约30小时、约20小时至约30小时)。在某些实施方式中,预固化以及进一步固化在动态CO2循环流动状态下进行。为了符合期望的结果,可以调节固化过程的相对湿度环境,例如,约50%至约98%范围内(例如,约60%至约98%、约70%至约98%、约80%至约98%、约90%至约98%、约50%至约90%、约50%至约80%、约50%至约70%)的相对湿度,以生产展现均一、均质并且高度多孔结构的充气复合材料。在某些实施方式中,方法还包括在固化预固化物之后,在约20℃至约110℃范围内(例如,约20℃至约100℃、约20℃至约90℃、约20℃至约80℃、约20℃至约70℃、约20℃至约60℃、约30℃至约110℃、约40℃至约110℃、约50℃至约110℃、约60℃至约100℃)的温度下干燥固化物约12小时至约96小时(例如,约12小时至约72小时、约12小时至约60小时、约12小时至约48小时、约12小时至约36小时、约12小时至约24小时、约24小时至约96小时、约36小时至约96小时、约36小时至约48小时),以去除残留的水。在某些实施方式中,在固化过程结束时强度赋予组分主要由碳酸钙(CaCO3或方解石)和无定形硅酸钙相,以及少量水化硅酸钙(C-S-H)凝胶和氢氧化钙(CH)构成。由此,可以制定固化条件的各种组合,包括可变的反应温度、压力和反应长度,从而实现期望的生产方法。在某些实施方式中,研磨硅酸钙选自硅灰石、假硅灰石、硅钙石、斜硅钙石和硅酸三钙石。在某些实施方式中,研磨硅酸钙或合成硅灰石由研磨硅灰石(CS)以等同的、1:1或2:1的比例与假硅灰石、硅钙石(C3S2)、钙铝黄长石(C2AS)、斜硅钙石(C2S)和硅酸三钙石(C3S)以及某些痕量杂质构成,其中根据水泥化学家标记法(CCN),“C”代表氧化钙或石灰、“S”代表二氧化硅或硅土、“A”代表氧化铝或矾土。研磨硅酸钙的特征为d10在约0.25μm至约5μm的范围内(例如,约0.25μm至约4μm、约0.25μm至约3μm、约0.25μm至约2μm、约0.25μm至约1μm、约0.5μm至约5μm、约1μm至约5μm、约2μm至约5μm),d50在约5μm至约20μm的范围内(例如,约5μm至约15μm、约5μm至约10μm、约10μm至约20μm、约15μm至约20μm),d90在约25μm至约100μm的范围内(例如,约25μm至约80μm、约25μm至约70μm、约25μm至约60μm、约25μm至约50μm、约40μm至约100μm、约50μm至约100μm、约60μm至约100μm、约70μm至约100μm)。可以使用任何适合的填料颗粒,例如含氧化钙材料或含二氧化硅材料。示例性的填料颗粒包括石灰、石英(包括砂)、硅灰石、硬硅钙石、煅烧油页岩、飞灰或火山灰、窑炉烟尘、研磨粘土、浮石粉尘。还可以使用诸如工业废料(例如飞灰、炉渣、硅灰)的材料作为填料。在某些优选实施例中,还可以使用诸如珍珠岩或蛭石的轻质集料作为填料。在某些优选实施例中,填料颗粒由诸如研磨石灰的富氧化钙材料制成。本文中使用的术语“石灰”指代以氧化钙或氢氧化钙为主的天然存在的无机材料或合成无机材料。本文中使用的术语“石英”指代任何SiO2系材料,包括普通砂(建筑及石工)以及玻璃和回收玻璃。该术语还包括含有大量SiO2的任何其他回收的天然材料及合成材料(例如,有时化学式为KAl2(AlSi3O10)的云母)。包含氧化钙或二氧化硅的填料颗粒的粒度(d50)在约0.25μm至约200μm的范围内(例如,约0.25μm至约150μm、约0.25μm至约100μm、约0.25μm至约50μm、约0.25μm至约20μm、约0.25μm至约10μm、约0.5μm至约200μm、约1μm至约200μm、约5μm至约200μm、约10μm至约200μm、约20μm至约200μm、约50μm至约200μm)。在某些实施方式中,填料颗粒选自粒度在约0.5μm至约300μm范围内(例如,约1μm至约300μm、约5μm至约300μm、约10μm至约300μm、约50μm至约300μm、约100μm至约300μm、约0.5μm至约200μm、约0.5μm至约100μm、约0.5μm至约50μm、约0.5μm至约20μm、约0.5μm至约10μm、约0.5μm至约5μm)的飞灰、底灰、炉渣。在某些实施方式中,填料颗粒选自粒度在约1μm至约500μm范围内(例如,约1μm至约400μm、约1μm至约300μm、约1μm至约200μm、约1μm至约100μm、约1μm至约50μm、约1μm至约30μm、约5μm至约500μm、约10μm至约500μm、约20μm至约500μm、约50μm至约500μm、约100μm至约500μm、约200μm至约500μm)的石灰石、硅粉和石英。在某些实施方式中,填料颗粒选自粒度在约20μm至约500μm范围内(例如,约20μm至约400μm、约20μm至约300μm、约20μm至约200μm、约20μm至约100μm、约50μm至约500μm、约100μm至约500μm、约200μm至约500μm、约300μm至约500μm)的轻质集料。在某些实施方式中,硬化控制掺混剂选自葡萄糖酸盐和蔗糖。在某些实施方式中,分散/粘度改性剂是聚羧酸盐系材料。在示例性实施方式中,研磨硅酸钙是研磨硅灰石,填料颗粒包含研磨石灰石和二氧化硅,活化剂是研磨石灰,硬化控制掺混剂是葡萄糖酸盐,粘度改性剂是聚羧酸盐系材料,并且充气剂是铝浆。多个孔隙用以降低充气复合材料的整体密度,同时提供促进复合材料的均一且加速固化的三维多孔网络。取决于期望的特性及要进行的应用,多个孔隙可以占充气复合材料的总体积中的任何适合的分数。例如,多个孔隙可以占充气复合材料总体积的约50vol.%至约80vol.%(例如,约60vol.%至约80vol.%、约65vol.%至约80vol.%、约60%、约65%、约70%、约75%、约80%)。多个孔隙由充气剂所产生的气态材料生成。在某些优选实施方式中,充气剂包含能够与酸反应产生气态氢的金属。示例性的充气剂包括:铝粉或铝浆、铁粉、锌粉、碳化钙粉以及过氧化氢,或其混合物。充气剂可以具有任何适合的尺寸,例如约10μm至约50μm范围内(例如,约10μm至40μm、约10μm至30μm、约10μm至20μm、约15μm至40μm、约15μm至30μm、约20μm至40μm、大于约40μm)的尺寸。在另一个方面中,本发明大体涉及由根据本发明公开的方法生产的制品。充气复合材料和/或制品的特征可以密度为约300kg/m3至约1500kg/m3(例如,约300kg/m3至约1200kg/m3、约300kg/m3至约1000kg/m3、约300kg/m3至约900kg/m3、约400kg/m3至约1200kg/m3、约400kg/m3至约1000kg/m3、约400kg/m3至约900kg/m3、约500kg/m3至约1200kg/m3、约500kg/m3至约1000kg/m3)。本发明的充气复合材料展现优秀的压缩强度。例如,充气复合材料和/或制品的特征可以是压缩强度为约2.0MPa至约8.5MPa(例如,约2.0MPa至约6.0MPa、约2.0MPa至约5.0MPa、约3.0MPa至约8.5MPa、约3.0MPa至约6.0MPa、约3.0MPa至约5.0MPa、约4.0MPa至约8.5MPa)。本发明的充气复合材料还展现优秀的挠曲强度。例如,充气复合材料和/或制品的特征可以是挠曲强度为约0.4MPa至约1.7MPa(例如,约0.7MPa至约1.7MPa、约1.0MPa至约1.7MPa、约1.2MPa至约1.7MPa、约1.0MPa至约1.5MPa、约1.2MPa至约1.5MPa)。在某些示例性实施方式中,充气复合材料展现约400kg/m3至1200kg/m3的密度、约3.0MPa至约6.0MPa的压缩强度、以及约0.66MPa至约1.32MPa的挠曲强度。在某些实施方式中,充气复合材料展现约500kg/m3至1000kg/m3的密度、约4.0MPa至约6.0MPa的压缩强度、以及约0.88MPa至约1.32MPa的挠曲强度。可以制备展现期望的密度及机械特性(例如满足或超过根据ASTMC1693-11的充气混凝土强度分级规范)的充气复合材料。表1ASTM分级在又一个方面中,本发明大体涉及一种充气复合材料,该充气复合材料包含:(1)多个接合单元,所述接合单元的特征为具有约0.25μm至约5μm范围内的比粒度d10、约5μm至约20μm范围内的比粒度d50、以及约25μm至约100μm范围内的比粒度d90;(2)多个填料颗粒,所述填料颗粒具有约0.5μm至约500μm范围内的粒度;(3)多个孔隙。每个接合单元包含:主要包含硅酸钙的核心,富二氧化硅的第一层或内层,以及富碳酸钙的第二层或外层。多个接合单元与多个填料颗粒一起形成一个以上接合基质,并且接合单元与填料颗粒大致均匀地分散于其中并且接合在一起。多个孔隙为鼓泡状和/或互连通道,占充气复合材料的约50vol.%至约80vol.%。充气复合材料展现约300kg/m3至1500kg/m3的密度、约2.0MPa至约8.5MPa的压缩强度、以及约0.4MPa至约1.7MPa的挠曲强度。在某些实施方式中,多个接合单元由除硅灰石之外的前体硅酸钙经化学转化而成,所述化学转化是经由受控热液液相烧结方法使所述除硅灰石之外的前体硅酸钙与CO2发生反应。在某些实施方式中,多个接合单元由包含铝、镁和铁中一个以上的前体硅酸钙经化学转化而成。充气复合材料可以进一步包括一种以上添加剂,以调整产物的外观、物理或机械性质。示例性的添加剂包括流变改性掺混剂、颜料、缓凝剂和促凝剂。在某些实施方式中,取决于期望的复合材料,颜料可以均匀地分散或大致不均匀地分散于接合基质中。颜料可以是任何适合的颜料,包括例如各种金属的氧化物(例如黑色氧化铁、氧化钴及氧化铬)。颜料可以是任何颜色,例如选自黑色、白色、蓝色、灰色、粉红色、绿色、红色、黄色及褐色的颜色。取决于期望的复合材料,颜料可以以任何适合量存在,例如约0.0重量%至约10重量%范围内(例如,约0.0%至约8%、约0.0%至约6%、约0.0%至约5%、约0.0%至约4%、约0.0%至约3%、约0.0%至约2%、约0.0%至约1%、约0.0%至约0.5%、约0.0%至约0.3%、约0.0%至约2%、约0.0%至约0.1%)的量。本发明的充气复合材料可以用于制造各种大小及尺寸的多种产品,包括例如标准块、核心块、护墙块、井壁及防火块、横梁块、榫槽块、墙板、地板、屋面板、板材、边板、框架、围栏、装饰性及景观产品、停车挡块等。多种产品能够由可广泛获得的低成本原材料、通过不需要高压釜并且适于连续大规模生产的方法生产。在经济学与环境影响方面,所述生产方法与传统充气混凝土相比已大大改良。接合单元、接合基质以及复合材料化学讨论本发明提供了用于制造主要通过CO2消耗反应固化的新型复合材料的装置和方法。该材料展现了有用的性质,并且能够容易地从可广泛获得的低成本前体材料、利用适于大规模生产的方法生产,具有最小的环境影响。前体材料包括来源丰富且价格低廉的富硅酸钙材料、细颗粒和粗颗粒。富硅酸钙材料可以包含研磨硅灰石。细颗粒和粗颗粒可以包含研磨石灰石或其他碳酸钙系材料、研磨石英或其他SiO2系材料、砂和压碎岩。细颗粒和粗颗粒也可以包含压碎矿物,所述矿物诸如花岗岩、云母和长石。其他过程组分包括水和CO2。为了对所得复合材料的物理外观和/或机械特性进行改变和微调,能够使用各种添加剂,诸如选自颜料(例如,黑色氧化铁、氧化钴和氧化铬)、有色玻璃和/或有色石英中的一种以上。还可以使用关于减少用水量和改变流变能力的添加剂。如本文中所公开,能够使用高能效的热液液相烧结(HLPS)方法,通过产生将复合材料的各种组分保持在一起的结合单元,来生产复合材料。复合材料能够以低成本及有利的环境影响来制造。例如,在本发明的优选实施方式中,CO2用作反应性物种,在生产的复合材料中获得了CO2的固存以及接合单元的形成,并且其碳足迹是任何现有的生产技术无法比拟的。HLPS过程由化学反应的自由能和晶体生长导致的表面能(面积)减少热力学地驱动。因为使用溶液(水溶液或非水溶液)代替高熔点流体或高温固态介质来输送反应性物种,所以HLPS过程的动力学在低温下以合理的速率进行。关于HLPS的各种方面的论述可见于美国专利号8,114,367、美国公开号US2009/0143211(申请序列号12/271,566)、美国公开号US2011/0104469(申请序列号12/984,299)、美国公开号2009/0142578(申请序列号12/271,513)、美国公开号2013/0122267(申请序列号13/411,218)、美国公开号2012/0312194(申请序列号13/491,098)、WO2009/102360(PCT/US2008/083606)、WO2011/053598(PCT/US2010/054146)、WO2011/090967(PCT/US2011/021623)、2012年10月1日提交的美国临时申请号61/708,423、以及2013年10月3日提交的美国专利申请号14/045,758、14/045,519、14/045,766、14045540;2014年3月12日提交的美国专利申请号14/207,413、14/207,421;2014年3月13日提交的美国专利申请号14/207,920、14/209,238;2014年6月4日提交的美国专利申请号14/295,601,14/295,402,各案通过引用以其整体用于所有目的特此并入本文。本文中使用的术语“硅酸钙”指代包含一组含钙硅化合物中的一种以上的天然存在的矿物质或合成材料,该含钙硅化合物包括CS(硅灰石或假硅灰石,并且有时化学式为CaSiO3或CaO·SiO2)、C3S2(硅钙石,并且有时化学式为Ca3Si2O7或3CaO·2SiO2)、C2S(斜硅钙石(belite,β-Ca2SiO4)、斜硅钙石(larnite,β-Ca2SiO4)或变硅灰石(bredigite,α-Ca2SiO4或γ-Ca2SiO4),并且有时化学式为Ca2SiO4或2CaO·SiO2)、富硅酸钙无定形相,其中各个材料可以包括一种以上其他金属离子和氧化物(例如铝、镁、铁或锰氧化物)或其共混物,或者可以包括一定量的呈天然存在的形式或合成形式的硅酸镁,其量的范围为痕量(1重量%)至约50重量%以上。图1至图8是示出一些上述材料的各种相之间的相互关系的相图。含硅钙化合物还可以包括晶体硅酸钙相和无定形硅酸钙相两者,其还可以包含其他离子、氧化镁、钾、钠和铝系化合物。应该理解,能够采用本文中公开的组合物及方法来使用硅酸镁代替硅酸钙或除硅酸钙之外还使用硅酸镁。本文中使用的术语“硅酸镁”指代包含一组含镁硅化合物中的一种以上的天然存在的矿物质或合成材料,该含镁硅化合物包括例如Mg2SiO4(还称为“镁橄榄石”)、Mg3Si4O10(OH)2(还称为“滑石”)和CaMgSiO4(还称为“钙镁橄榄石”),其中各个材料可以包括一种以上其他金属离子和氧化物(例如钙、铝、铁或锰氧化物)或其共混物,或者可以包括一定量的呈天然存在的形式或合成形式的硅酸钙,其量的范围为痕量(1重量%)至约50重量%以上。本文中使用的术语“石英”指代任何SiO2系材料,包括普通砂(建筑及石工)以及玻璃和回收玻璃。该术语还包括含有大量SiO2的任何其他回收的天然材料及合成材料(例如,有时化学式为KAl2(AlSi3O10)(OH)2的云母)。在某些优选实施方式中,多个接合单元由研磨硅酸钙组合物经化学转化而成,所述化学转化是经由气相HLPS方法使所述研磨硅酸钙组合物与CO2发生反应。在某些实施方式中,复合材料的特征是压缩强度为约90MPa至约175MPa(例如,约90MPa至约150MPa、约90MPa至约140MPa、约90MPa至约130MPa、约90MPa至约120MPa、约90MPa至约110MPa、约100MPa至约175MPa、约120MPa至约175MPa、约130MPa至约175MPa、约140MPa至约175MPa、约150MPa至约175MPa、约160MPa至约175MPa)。在某些实施方式中,复合材料的特征是挠曲强度为约5MPa至约30MPa(例如,约5MPa至约25MPa、约5MPa至约20MPa、约5MPa至约15MPa、约5MPa至约10MPa、约10MPa至约30MPa、约20MPa至约30MPa、约25MPa至约30MPa)。在某些实施方式中,复合材料的特征是吸水率小于约10%(例如,小于约8%、5%、4%、3%、2%或1%)。复合材料可以显示期望的纹理、图案和物理性质的一种以上,特别是属于天然石材的特性的纹理、图案和物理性质。在某些优选实施方式中,复合材料展现与天然石材相似的视觉图案。其他特性包括颜色(例如,黑色、白色、蓝色、粉红色、灰色(浅灰至深灰)、绿色、红色、黄色、褐色、青色(蓝绿色)或紫色)和纹理。仪器和过程讨论CO2控制在所描述的实施方式中,使用由各个不同的工业气体公司(诸如,Praxair,Inc.、LindeAG、AirLiquide及其他公司)提供的约99%的纯度的工业级CO2。此供应能够以液态二氧化碳的形式储存于大型加压储料罐中,将液态二氧化碳调控在使其保持约300PSIG的气压的温度下。然后将此气体管送至CO2固化壳体(enclosure)或腔室。在最简单的系统中,CO2以足以置换壳体中的环境空气的速率流过壳体。一般来说,吹扫(purge)时间取决于壳体的大小和供应CO2气体的速率。在许多系统中,吹扫壳体内空气的过程以按分钟计的多次进行,以得到能够在其后进行固化的合理水平的CO2浓度。在简单系统中,随后以预定速率向系统中供给CO2气体,从而保持足以驱动固化反应的CO2浓度。作为实例,现在描述用于在反应期间维持二氧化碳浓度的方法,该方法非常适合于保持高度一致的浓度,尽管其是“闭环”过程,是趋向于最昂贵的技术。该方法直接使用在系统中测量的CO2浓度,并且使用诸如PLC的控制器、通过电子/自动控制阀将CO2浓度控制在设定点。应当优选地采用诸如NDIR的直接测量CO2的测量技术。在NDIR测量方法中,经由低流量泵将气体样品流从系统抽出。在气流由NDIR设备取样前,冷却器用于从气流抽取出湿气。因此,由分析器提供的测量漏算气流的水蒸汽组分,并且需要调整为包括已从测试样品移除的湿度。系统气流中的湿度测量能够使用干球湿球湿度技术、使用干球湿球湿度测量装置、或使用不同类型的湿度传感器进行。能够使用计算机控制系统或PLC计算真正的CO2浓度。一旦得知真正的CO2浓度,当CO2已经消耗并且低于当时所需的设定点时,致动比例控制阀能够将干燥CO2添加至系统中。在各种实施方式中,如果需要的话,设定点可以基于复合材料样本固化的具体组成、形状及尺寸的经验而随时间变化。湿度控制图9是根据本发明的原理进行加湿的CO2复合材料固化腔室的示意图。在图9中,提供水供应器,并且将水蒸汽加入在固化腔室内循环的气氛。水可以是任意方便的饮用水源。在一些实施方式中,使用普通自来水。在一些实施方式中,水能够通过流过雾化喷嘴或雾化喷雾喷嘴、电蒸汽产生器、燃气蒸汽产生器、或者通过加热至高于腔室的气体温度而转化成蒸汽,从而从液态水供应器产生蒸发,实例为具有浸没加热器的鼓式反应器。在又一实施方式中,CO2供应可以在通过加热水供应器鼓泡之后流入系统中,以增加进入的气流的相对湿度,实例为构造成用于“流过”或“开环”过程的鼓式反应器。相对湿度是传统混凝土固化和CO2复合材料固化两者中的重要参数。在传统固化腔室中,存在主要由氮气、氧气及水蒸汽组成的湿气气氛。在这些系统中,相对湿度最常由标准电容式传感器技术测量。然而,CO2固化腔室具有主要由与这些传感器的一些类型不兼容的二氧化碳组成的气氛。传感技术,诸如利用二氧化碳与水蒸汽的湿度比的干球湿球技术、或偶极子极化水蒸汽测量设备、或冷镜式湿度计、或电容式湿度传感器,能够用于本文中描述的CO2复合材料固化系统。取决于固化的产物的类型及几何形状、腔室的设计及腔室中的产物的充填效率,湿度可能需要降低或提高并调节至特定设定点。设定点可以在从1%至99%的相对湿度的任意范围。在能够组合至单个系统的CO2复合材料固化过程中,可存在三种不同的用于湿度控制的方法。在CO2固化系统的一个实施例中加湿的方法表示于图9中。另一方法,需要从系统移除湿气以用CO2固化复合材料产物。降低相对湿度的简单方法是通过用干燥气体,例如二氧化碳,代替系统中的湿气。在还有一个实施方式中,能够通过非吹扫方法降低相对湿度并因此从气体移除水蒸汽,该方法在一个优选实施例中为进行水萃取的冷却热交换器。图10是固化腔室的示意图,该固化腔室具有多种湿度控制方法以及使用恒定流量或压力调控来控制并补充CO2,并且能够根据本发明的原理控制温度。此系统是能够提供闭环控制或者使用反馈控制的系统,其中设置了诸如CO2浓度、湿度和温度的运行参数在过程周期中特定时间期望的设定值,并且进行测量,以判断受控参数的真实值是否是期望值。如果测量到与期望值的偏差,则进行校正措施以使参数的值与期望值相一致。这样的控制系统昂贵且复杂,对于高价值产品或者需要非常精密的加工条件的产品可能是有用的。温度控制在一些实施例中,使用诸如热电偶或RTD的传感器测量温度。测量信号导回至能够调控进入热交换器的能量的控制器或计算机,从而随时间调整整个系统的温度。鼓风机是加热系统的重要组件,因为鼓风机能够帮助将热能传送至气体,该气体自身传送至产物和腔室,并且是样品的受控水分的重要部分。加热方法可以是电热或气体燃烧。护套加热器可以用于控制流过与加热套接触的腔室的CO2的温度,能够使用任何方便的热源。外部加热的方式可以包括但不限于电加热、热水加热或热油加热。对于CO2固化腔室,迄今为止利用间接燃气系统,并且避免直接燃气燃烧器,因为直接燃气燃烧器会将空气及燃烧产物吸入系统中,从而稀释CO2并使CO2浓度控制出现问题。诸如鼓式反应器的一些更小规模的系统利用电护套加热器而非腔室内的加热元件加热腔室的整个表面。气流控制另一控制参数为跨过系统中待固化材料的气体速度。该气体速度极为依赖于加工设备的变量,包括但不限于腔室设计、挡板设计、风扇尺寸、风扇速度/功率、风扇数目、系统内的温度梯度、系统内的机架设计和系统内的样品几何形状。控制腔室内的气体速度的最简单方法是通过调整鼓风机速度(RPM的),该方法通常通过利用变频驱动来控制鼓风机马达速度而进行。鼓风机可以用于在固化腔室中以所需速度循环气体。系统中的气体速度在系统中经由各种不同技术测量,包括但不限于皮托管测量和激光多普勒检测系统。气体速度的测量信号可以发送回电脑系统或可编程逻辑控制器,并且可以用作固化线型中的控制参数。复合材料的制备方法这里描述复合材料的制备方法。所述方法包括:混合微粒组成物与液体组成物以形成浆料混合物;通过在模具中浇铸浆料、在模具中压制浆料、在振动模具中压制浆料、挤出浆料、滑动成型浆料或使用混凝土生产中常见的任意其他成型方法将浆料混合物形成为所需形状,并且在约20℃至约150℃范围内的温度下、在包含水和CO2的蒸汽下将所形成的浆料混合物固化约1小时至约80小时,以生产展现纹理和/或图案以及涉及压缩强度、挠曲强度、密度、耐降解性等的期望的物理性质的复合材料,该蒸汽具有约环境大气压力至高于环境大气压力约50psi范围内的压力、并且具有从10%至约90%范围内的CO2浓度。微粒组成物包括中值粒径在约1μm至约100μm范围内的研磨硅酸钙。除此之外,微粒组成物可以包括中值粒径在约3μm至约25mm范围内的研磨碳酸钙或含SiO2材料。液体组成物包括水及水溶性分散剂。方法可进一步包括在固化浇铸的混合物之前干燥浇铸的混合物的步骤。微粒组成物进一步包含如本文中所论述的颜料或着色剂。在某些实施方式中,在约30℃至约120℃范围内的温度下、在包含水和CO2的蒸汽下对形成的浆料混合物进行固化约1小时至约70小时,该蒸汽具有约环境大气压力至高于环境大气压力约30psi的范围内的压力。在某些实施方式中,在约60℃至约110℃范围内的温度下、在包含水和CO2的蒸汽下对形成的浆料混合物进行固化约1小时至约70小时,该蒸汽具有约环境大气压力至高于环境大气压力约30psi的范围内的压力。在某些实施方式中,在约80℃至约100℃范围内的温度下、在包含水和CO2的蒸汽下对形成的浆料混合物进行固化约1小时至约60小时,该蒸汽具有约环境大气压力至高于环境大气压力约30psi的范围内的压力。在某些实施方式中,在等于或小于约60℃的温度下、在包含水和CO2并且具有环境大气压力的蒸汽下对形成的浆料混合物进行固化约1小时至约50小时。例如,在一些实施方式中,研磨硅酸钙的中值粒度为约1μm至约100μm(例如,约1μm、10μm、15μm、20μm、25μm、30μm、40μm、50μm、60μm、70μm、80μm、90μm、100μm),容积密度为约0.5g/mL至约3.5g/mL(疏松,例如0.5g/mL、1.0g/mL、1.5g/mL、2.0g/mL、2.5g/mL、2.8g/mL、3.0g/mL、3.5g/mL)以及约1.0g/mL至约1.2g/mL(密实),布莱恩(Blaine)表面积为约150m2/kg至约700m2/kg(例如,150m2/kg、200m2/kg、250m2/kg、300m2/kg、350m2/kg、400m2/kg、450m2/kg、500m2/kg、550m2/kg、600m2/kg、650m2/kg、700m2/kg)。在某些优选实施方式中,液体组成物包含水和包含聚合物盐(例如,丙烯酸均聚物盐)的水溶性分散剂,该聚合物盐的浓度为液体组成物的约0.1%至约2%w/w。根据本文中公开的方法制备的复合材料能够展现约3.0MPa至约30.0MPa(例如,约3MPa、5MPa、10MPa、15MPa、20MPa、25MPa、30MPa)的压缩强度,以及约0.3MPa至约4.0MPa(例如,约0.3MPa、0.5MPa、1.0MPa、1.5MPa、2.0MPa、2.5MPa、3.0MPa、3.5MPa、4.0MPa)的挠曲强度。还描述了由复合材料制成的制品。可以使用任何适合的前体材料,包括例如由CS(硅灰石或假硅灰石,并且有时化学式为CaSiO3或CaO·SiO2)、C3S2(硅钙石,并且有时化学式为Ca3Si2O7或3CaO·2SiO2)、C2S(斜硅钙石(belite,β-Ca2SiO4)、斜硅钙石(larnite,β-Ca2SiO4)或变硅灰石(bredigite,α-Ca2SiO4或γ-Ca2SiO4),并且有时化学式为Ca2SiO4或2CaO·SiO2)、以及富硅酸钙无定形相形成的硅酸钙组成物颗粒。据信,钙阳离子从硅酸钙组成物颗粒溶出并且将硅酸钙组成物颗粒的周边部分转化成钙缺陷状态。随着钙阳离子继续从核心的周边部分溶出,周边部分的结构最终变得不稳定并且碎裂,从而将核心的缺钙硅灰石周边部分转化成主要富二氧化硅的第一层。同时,主要为碳酸钙的第二层从水中沉淀。更具体地,第一层及第二层可由前体颗粒根据下列反应(1-3)形成,其中能够使用水作为反应介质而不是反应物(即,不消耗水):CaSiO3(s)+CO2(g)→CaCO3(s)+SiO2(s)(1)Ca3Si2O7(s)+3CO2(g)→3CaCO3(s)+2SiO2(s)(2)Ca2SiO4(s)+2CO2(g)→2CaCO3(s)+SiO2(s)(3)例如,在诸如硅酸钙组成物的硅酸盐矿物的碳酸化反应中,引入气相CO2,其溶解于诸如水的浸渗液中。CO2溶解形成酸性碳物种(诸如碳酸,H2CO3),导致溶液中的pH值降低。弱酸性溶液从硅酸钙相中非全等溶解钙物种。该可以通过类似的机理从含钙无定形相中析出。释放的钙阳离子及解离的碳酸盐物种引起不溶性碳酸盐的沉淀。富二氧化硅层被认为作为钙耗乏层保留于矿物质颗粒上。因此,根据本发明的优选实施方式,CO2优选与硅酸钙组成物前体核心的钙阳离子反应,从而将前体核心的周边部分转化成富二氧化硅的第一层和富碳酸钙的第二层。另外,第一层和第二层存在于核心上充当硅酸钙与二氧化碳之间的进一步反应的屏障,从而产生具有核心、第一层及第二层的接合单元。在一些实施方式中,具有不同于Ca或除Ca之外的金属的硅酸盐材料,例如,镁橄榄石(Mg2SiO4)、透辉石(CaMgSi2O6)和滑石(Mg3Si4O10(OH)2),能够以与硅酸钙的反应相似的方式与溶于水的二氧化碳反应,如上所述。据信,根据本发明的原理这样的硅酸盐材料能够单独、组合和/或与硅酸钙组合用作接合单元的前体。优选地,气体辅助HLPS方法利用部分浸渗的孔空间以实现气体扩散,从而快速浸渗多孔预成型坯并且用溶解的CO2使孔中的稀液界面溶剂膜饱和。CO2系物种在纯水中具有低溶解度(在25℃、1atm下为1.5g/L)。因此,必须向多孔预成型坯连续供应大量CO2并且使CO2遍布于多孔预成型坯中以实现明显的碳酸盐转化。与可溶性CO2在液相中扩散相同时间的扩散长度相比,利用气相扩散使扩散长度获得巨大的增加(约100倍)。("Handbookofchemistryandphysics",编者:D.R.Lide,第6章和第8章,第87版2006-2007,CRC.)。该部分浸渗状态能够使反应在固定的时段内进行至高碳酸化程度。孔中的液态水使反应速率加快,原因在于液态水提供了碳酸和钙物种两者的离子化介质。然而,水含量必需足够低,以使CO2气体能够在溶于孔结合水相之前扩散进入多孔基质中。此外,主动溶解的多孔预成型坯充当扩展反应性晶体生长的模板。因此,接合单元和基质能够在最小的变形及残余应力下形成。除了许多其他应用之外,此方法能够得到大型复杂形状,诸如基础结构及建筑材料所需要的形状。由此,可以制定固化条件的各种组合,包括可变的反应温度、压力和反应长度,从而实现期望的生产方法。在第一示例性实施例中,在前体材料中存在水(例如,作为先前的混合步骤的残留水),并且将液体水与CO2一起供应至前体材料(例如,保持水含量和/或控制水的蒸发损失),在约90℃及约20psig(即,高于环境压力20psi)下进行固化过程,时间在约2至90小时的范围内。在第二示例性实施例中,在前体材料中存在水(例如,作为先前的混合步骤的残留水),并且将水蒸汽与CO2一起供应至前体材料(例如,保持水含量和/或控制水的蒸发损失),在约90℃及约20psig(即,高于环境压力20psi)下进行固化过程,时间在约2至90小时的范围内。在第三示例性实施例中,在前体材料中存在水(例如,作为先前的混合步骤的残留水),并且将水蒸汽与CO2一起供应至前体材料(例如在保持水含量和/或控制水的蒸发损失),在约25至90℃及0psig(环境大气压力)下进行固化过程约2至72小时。在上述实施方式中,固化复合材料物体所需的时间由水蒸汽和CO2气体扩散通过物体的能力来判定。一般来说,较厚的物体比较薄的物体需要更长的时间来固化。类似地,密度高(开放孔空间较少)的物体比密度低(开放孔空间较多)的物体需要更长的时间来固化。下表提供了固化时间如何随着所制造的物体的三维最小厚度(或壁厚或截面厚度)以及容积密度而变化的实例。表2固化时间和最小厚度的实例所制造的微观结构讨论如图11(a)-11(c)中示意性说明,接合单元包括核心(由黑色内部部分表示)、第一层(由白色中间部分表示)和第二层或囊封层(由外部部分表示)。第一层可以包括单独一个层或多个子层并且可以完全或部分地覆盖核心。第一层可以以结晶相、无定形相或其混合相存在,并且可以呈连续相或离散颗粒形式。第二层可以包括单独一个层或多个子层并且还可以完全或部分地覆盖第一层。第二层可以包括多个颗粒或者可以是离散颗粒最少的连续相。取决于预期的应用,接合单元可以展现任意大小及任意规则或不规则、固体或中空形态。示例性形态包括:立方体、长方体、棱柱体、圆盘、棱锥体、多面体或多面颗粒、圆柱体、球体、圆锥体、环、管、新月体、针、纤维、细丝、薄片、球体、亚球体、珠粒、葡萄状、颗粒状、椭圆形、棒状、波纹状等。一般而言,如本文更详细论述的,接合单元由反应性前体材料(例如前体颗粒)经过转化过程而产生。前体颗粒可以具有任意大小和形状,只要所述前体颗粒满足预期应用的需要即可。转化过程一般产生具有与前体颗粒相似的大小和形状的相对应的接合单元。在接合基质内,接合单元可以相对于彼此以诸多取向中的任一取向定位。图12(a)-12(f)示意性说明一种示例性接合基质,所述接合基质包括呈不同取向的纤维状或片状接合单元,所述接合单元可以通过并入填充材料来稀释,如接合单元之间的间距所示。例如,图12(a)示出一种接合基质,所述接合基质包括以单向(“1-D”)取向排列(例如相对于x方向排列)的纤维状接合单元。图12(b)示出一种接合基质,所述接合基质包括以双向(“2-D”)取向排列(例如相对于x和y方向排列)的片状接合单元。图12(c)示出一种接合基质,所述接合基质包括以三方向(“3-D”)取向排列(例如相对于x、y和z方向排列)的片状接合单元。图12(d)示出一种接合基质,所述接合基质包括呈随机取向的片状接合单元,其中接合单元不相对于任何特定方向排列。图12(e)示出一种接合基质,所述接合基质包括浓度相对较高的、以3-D取向排列的片状接合单元。图12(f)示出一种接合基质,所述接合基质包括浓度相对较低的、以随机取向定位的片状接合单元(渗滤网络)。图12(f)的复合材料达到渗滤阈值,原因在于大部分接合单元彼此接触,从而从材料一端至另一端形成连续的接点网络。渗滤阈值为临界浓度,高于临界浓度则接合单元显示长程连通性,其中接合单元呈有序取向,例如图4(e),或呈随机取向,例如图4(f)。连通模式的实例可见于例如Newnham等,"Connectivityandpiezoelectric-pyroelectriccomposites",Mat.Res.Bull.第13卷,第525页至第536页,1978。多个接合单元可以由任何适合的前体材料、例如由任何适合的硅酸钙组成物前体经化学转化而成。前体硅酸钙组成物还可以包含铝、镁和铁中的一种以上化学元素。取决于期望的复合材料,多个接合单元可以具有任何适合的中值粒度和粒度分布。在某些实施方式中,多个结合单元的中值粒度在约1μm至约100μm的范围内(例如,约1μm至约80μm、约1μm至约60μm、约1μm至约50μm、约1μm至约40μm、约1μm至约30μm、约1μm至约20μm、约1μm至约10μm、约5μm至约90μm、约5μm至约80μm、约5μm至约70μm、约5μm至约60μm、约5μm至约50μm、约5μm至约40μm、约10μm至约80μm、约10μm至约70μm、约10μm至约60μm、约10μm至约50μm、约10μm至约40μm、约10μm至约30μm、约10μm至约20μm)。在一些情形中,复合材料包括:多个接合单元和多个填料颗粒。每个接合单元包含:主要包含硅酸钙的核心,富二氧化硅的第一层或内层,以及富碳酸钙的第二层或外层。多个接合单元与多个填料颗粒一起形成一个以上接合基质,并且接合单元与填料颗粒大致均匀地分散于其中并且接合在一起,从而使复合材料展现一种以上的纹理、图案和物理性质。在一些情形中,接合单元可以具有硅酸镁的核心,富二氧化硅的第一层或内层,以及富碳酸镁的第二层或外层。硅酸镁可以包含铝、钙、铁或锰氧化物。多个填料颗粒可以具有任何适合的中值粒度和粒度分布。在某些实施方式中,多个填料颗粒的中值粒度在约5μm至约7mm的范围内(例如,约5μm至约5mm、约5μm至约4mm、约5μm至约3mm、约5μm至约2mm、约5μm至约1mm、约5μm至约500μm、约5μm至约300μm、约20μm至约5mm、约20μm至约4mm、约20μm至约3mm、约20μm至约2mm、约20μm至约1mm、约20μm至约500μm、约20μm至约300μm、约100μm至约5mm、约100μm至约4mm、约100μm至约3mm、约100μm至约2mm、约100μm至约1mm)。在某些优选实施例中,填料颗粒由诸如石灰石的富碳酸钙材料制成(例如,研磨石灰石)。在某些材料中,填料颗粒由一种以上诸如石英、云母、石墨和长石的SiO2系或硅酸盐系材料制成(例如,研磨石英、研磨云母、研磨石墨、研磨长石)。在某些实施方式中,填料颗粒可以包括天然材料、合成材料和回收材料,诸如玻璃、回收玻璃、煤渣、富碳酸钙材料和富碳酸镁材料。取决于期望的复合材料,(接合单元:填料颗粒)的重量比可以是任何合适的比率,例如在约(10至50):约(50至90)的范围内。在某些实施方式中,这些复合材料可以显示各种图案、纹理和其他特性,诸如各种颜色的视觉图案。除此之外,本发明的复合材料展现与传统混凝土或相应的天然材料相似的压缩强度、挠曲强度和吸水性质。在某些实施方式中,复合物还包括颜料。取决于期望的复合材料,颜料可以均匀地分散或大致不均匀地分散于接合基质中。颜料可以是任何适合的颜料,包括例如各种金属的氧化物(例如氧化铁、氧化钴、氧化铬)。颜料可以是任何颜色,例如选自黑色、白色、蓝色、灰色、粉红色、绿色、红色、黄色及褐色的颜色。取决于期望的复合材料,颜料可以以任何适合量存在,例如约0.0重量%至约10重量%范围内(例如,约0.0%至约8%、约0.0%至约6%、约0.0%至约5%、约0.0%至约4%、约0.0%至约3%、约0.0%至约2%、约0.0%至约1%、约0.0%至约0.5%、约0.0%至约0.3%、约0.0%至约2%、约0.0%至约0.1%)的量。实施例实施例1使用合成硅灰石制造的充气复合材料原材料合成硅灰石(SC-C2),DonghaiGoldenResourcesIndustries,中国东海;氧化钙,Austin,TX(CapitolBrand);铝浆,EckratAmericaCorporation,新泽西州;Glenium7500,BASF,新泽西州;填充材料和葡萄糖酸盐,多个来源。表3混合物比例(13.56kg批量)固体组分:70.64%9.356kg合成硅灰石(SC-C2)63.62%8.630kg石灰(氧化钙)5.17%0.702kg葡萄糖酸盐0.03%0.005kg铝浆0.14%0.028kg液体组分:29.36%4.210kg自来水29.23%4.310kgGlenium75000.123%0.016kg混合步骤1.测量并且向实验室规模的混合机中装载液体组分。2.添加0.016kg的水中的粘度改性掺混剂(Glenium7500),轻轻搅拌。3.测量并且向湿混合物中装载8.630kg第一固体组分,该第一固体组分是合成硅灰石(SC-C2)。4.测量并且向混合机中装载0.702kg第二固体组分,该第二固体组分是石灰(氧化钙),并且以大约40RPM混合两种组分五分钟以上的时间,直到形成均一浆料。5.测量并且向浆料中装载剩余的0.005kg葡萄糖酸盐,并且以相同的速率继续混合大约两分钟。6.测量并且向浆料中装载0.028kg铝浆(最终固体组分),并且以较低的速率(30RPM)继续混合约三十秒,随后以较高rpm速率(50RPM)再混合三十秒。这样产生湿混合物。浇铸步骤1.使用WD-40或油脂润滑各个模具的内表面以降低湿混合物与模具内表面之间的摩擦力,并且避免湿混合物在脱模期间粘在模具表面的可能性。2.将湿混合物从混合机倒入模具内大约模具高度的一半。在大部分情况下,不需要外部振动;但是,如果模具尺寸小,则需要轻微摇动或扰动,使混合物平整。3.将装有湿混合物的模具转移至预固化腔室反应。固化步骤1.样品在设定为60℃和0.3psi的CO2气体的预固化腔室中反应3小时。2.固化3小时后,将样品从预固化腔室中取出,脱模并且置于直径7ft、长12ft的水平的固化腔室中。固化腔室用CO2吹扫12分钟。然后将固化腔室的温度设定为60℃,将70℃的热水在固化腔室的底部循环以保持腔室被水蒸汽饱和。然后将固化腔室内的样本在这些条件下固化或反应20小时,从而产生硬化的或固化的陶瓷体。3.将固化的样本从固化腔室中移出。然后将样本置于设定为90℃的烘箱内,以去除任何残留水。基于反应期间的重量增加计算反应的程度。对于使用表3中提及的混合比例制备的样品,假设铝与粘合剂和石灰完全反应,反应程度为大约40%至大约60%。照片:图13示出使用合成硅灰石制得的充气混凝土的切割样品(4英寸×4英寸×4英寸,用于展示目的)的实例。性能特性:从初步试验和配方研究中,已经使用前述原材料和方法制造了最小密度为约525至725kg/m3、相应的压缩强度高至4MPa的充气混凝土。而且,对于大约850kg/m3的密度,已经证实了高至5.0MPa的压缩强度。尽管这些密度和压缩强度对于充气混凝土是常见的,但是基于特定强度级别对这些材料的分组是有限制的。能够进一步优化反应条件,从而实现改进的机械和性能的特性。用于进行材料性能评价的数个试验的样品尺寸为2英寸和4英寸立方体,以及4英寸×4英寸×14英寸的棱柱体样本。在本说明书和随附的权利要求书中,单数形式“一(a)”、“一(an)”和“所述(the)”包括复数的指代,除非上下文另有明确指示。除非另有定义,本文中使用的所有技术和科学术语都与本领域普通技术人员普遍理解的意义相同。尽管也能够在所公开的实施方式的实践和测试中使用与本公开的方法和材料类似或等同的方法和材料,现在描述了优选的方法和材料。除所公开的特定顺序之外,本文中叙述的方法可以以逻辑上可行的任意顺序进行。通过引用并入在本公开中,已经对诸如专利、专利申请、专利公开、期刊、书记、论文、网页内容的其他文件进行了参考和引用。所有这些文件通过引用以其整体用于所有目的并入本文。通过引用并入本文的任何材料或其部分,在其与本文中明确阐明的现有定义、陈述或其他公开材料相冲突时,仅以并入的材料和本公开的材料之间不出现冲突的程度并入。在冲突的情形中,以有利于本公开的实施方式作为优选公开来解决。等同性本文中公开的代表性实例意在帮助说明本发明,并且无意于也不应被理解为限制本发明的范围。除本文中描述并示出的实施例之外,从本文件的全部内容及后续实例,以及本文中引用参考的科学和专利文献,本发明的各种修改以及许多其他实施例对于本领域技术人员确实将是明显的。这些后续实例以其各种实施方式及其等同物,包含了能够适用于本发明的实践的重要附加信息、范例和指导。当前第1页1 2 3