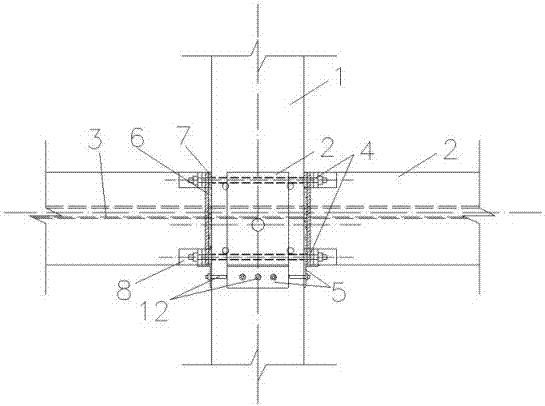
本发明涉及一种预制装配式混凝土结构节点连接技术,尤其是涉及一种具有震后低损伤自主复位特点的装配式混凝土双向框架梁柱连接节点。
背景技术:
自2008年汶川大地震以来,国内外大地震频发,许多建筑倒塌或严重损毁无法修复,导致受灾人员长期居住在帐篷或临时建筑中,这对其心理创伤的恢复十分不利。历次大地震的善后工作中也发现,幸存人员的心理创伤除了缘于失去亲人的伤痛外,还在很大程度上来自于失去家园、无家可归的感受。因此,研究并开发震后低损伤、可修复性好的新型建筑是当前工程抗震领域迫切需要解决的重要课题。建筑的抗震设防除了要满足规范的“小震不坏,中震可修,大震不倒”外,更应考虑提高其抗震设防水准,减轻地震损伤,提高震后可修复性。
另外,以住宅产业化为标志的预制装配式混凝土结构技术由于符合绿色环保低碳的可持续发展理念,有着极为广泛的应用前景。然而,预制装配式混凝土结构的构件在工厂预制,现场通过特定的节点构造组装连接,其抗震性能一直是普遍关注的问题。当前国内的相关规范主要推荐装配整体式等同现浇的连接方式,虽能满足现行规范抗震设防的基本要求,但很难满足减轻地震损伤,震后可快速修复的要求。
因此,研究开发新型的具有良好震后可修复性的预制装配式建筑体系既符合可持续发展的绿色环保理念,更符合国家中长期科技发展纲要有关公共安全的重点领域中重大自然灾害监测与防御的优先主题,如能够将取得的研究成果在工程中推广应用,势必可以有效改善建筑结构的安全性能,提高房屋的安全性,实现对地震灾害的有效防御,保证人民生命财产的安全。
技术实现要素:
本发明设计了一种具有震后低损伤自主复位特点的装配式混凝土双向框架梁柱连接节点,其解决的技术问题是当前装配整体式的框架梁柱连接节点采用湿式连接节点,现场施工较为复杂,施工质量较难控制,且无法实现减轻地震损伤,提高震后可修复性的问题。
为了解决上述存在的技术问题,本发明采用了以下方案:
一种预制装配式钢筋混凝土双向框架梁柱节点,其特征在于:预制框架柱(1)在节点区域连续,双向预制框架梁(2)在节点区域间断,梁端与柱侧形成接触面。框架柱(1)内对应双向框架梁(2)上、下钢筋标高处预留孔道(10),穿入钢筋(4),钢筋两端固定于对应方向框架梁(2)侧的预埋钢件(8)上,该钢筋在地震作用下可以耗散地震能量,在震后易于更换。双向框架梁(2)内中和轴附近位置预留孔道(11),框架柱也沿两方向(1)对应位置预留孔道(9),孔道(9)、(11)内设置无粘结预应力筋(3),通过张拉双向无粘结预应力筋(3)使梁端与柱侧之间产生摩阻力以抵抗框架梁端剪力。同时,无粘结预应力筋(3)设计为在罕遇地震作用下保持弹性,可以保证该节点在地震后自主复位。采用该节点连接的预制装配式钢筋混凝土框架结构体系可实现在罕遇地震下零损伤或轻微损伤,且震后自主复位,抗震能力大幅度提高。
进一步,框架柱(1)内对应双向框架梁(2)上、下钢筋标高处预留的孔道(10)内预埋钢管,并穿入钢筋(4),钢管内径比钢筋(4)外径大2-3mm,钢管内填充无粘结微膨胀材料,保证钢筋(4)在孔道(10)内可自由滑动。钢筋(4)端部套丝,采用螺母固定于框架梁(2)侧面的预埋钢件(8)上。框架柱(1)孔道(10)的位置应能保证孔道内的热轧钢筋(4)可以较为容易地安装或拆卸,必要时可通过在框架梁端对应位置局部减小梁的宽度来实现。
进一步,双向框架梁(2)内中和轴附近位置沿全跨采用波纹管或薄壁钢管预留孔道(11),框架柱(1)两方向对应位置采用波纹管或薄壁钢管预留孔道(9),孔道(9)、(11)内设置无粘结预应力筋(3),无粘结预应力筋通长设置,并锚固于建筑两端柱侧。无粘结预应力筋(3)的数量及张拉控制应力根据计算确定,应保证预应力筋在对应设防烈度的罕遇地震下保持弹性。
进一步,预制框架柱(1)在节点区域连续,预制框架梁(2)在节点区域间断,梁端与柱侧形成接触面。所述梁端外包钢板(6),梁端与柱侧预留宽度20mm左右的缝隙,浇筑高强无收缩灌浆材料(7)。
进一步,在预制框架柱(1)侧对应框架梁(2)底标高处设置角钢(5),通过锚栓(12)或预埋钢筋固定在框架柱(1)侧,用于预制框架梁(2)吊装时的临时支撑。
进一步,所述框架柱内预留的双向孔道(9)和(10)应在高度上相互错开,确保两方向的钢筋(4)和无粘结预应力筋(3)顺利通过。相应地,两方向框架梁内预留的孔道(11)也应在高度上相互错开,确保预应力筋通过。
进一步,所述无粘结预应力筋(3)为外包防腐润滑脂和聚乙烯护套的无粘结高强低松弛钢绞线,所述钢筋(4)为普通热轧钢筋。
该预制装配式混凝土框架结构梁柱连接节点与传统的装配整体式的框架连接节点相比,具有以下有益效果:
(1)本发明提出的预制装配式混凝土框架结构梁柱连接节点,可以有效提高预制装配式混凝土框架结构的抗震性能,减轻结构的地震损伤,且结构震后变形可以自主恢复,大幅度提高了结构的震后可修复性。
(2)本发明中预应力筋采用外包防腐润滑脂和聚乙烯护套的无粘结高强低松弛钢绞线,因而预应力筋相对于框架梁、柱可以产生相对滑移,同时预应力筋用量也根据在罕遇地震下保持弹性的设防标准确定,从而确保震后结构的自主复位。
(3)本发明中采用安装于框架柱中预留孔道内的普通热轧钢筋耗散地震能量,成本明显低于屈曲约束支撑,同时该钢筋易于更换,可以成为结构在地震作用下的耗能“保险丝”。
(4)本发明属于干式连接节点,可以实现现场无湿作业或很少湿作业,施工简便,施工现场噪音低,扬尘少,绿色环保,是值得大力推广的新型预制装配式混凝土框架梁柱连接技术。
附图说明
图1:本发明一种低损伤自复位装配式混凝土框架梁柱节点的立面结构示意图;
图2:图1的横向剖面结构示意图;
图3:图1中的预制框架柱侧立面示意图;
图4:图1中的预制框架梁截面示意图。
附图标记说明:
1—预制混凝土框架柱;2—预制混凝土框架梁;3—无粘结预应力筋;4—普通钢筋;5—角钢;6—框架梁端钢板;7—高强无收缩灌浆料;8—梁侧预埋钢件;9—柱内预留预应力筋孔道;10—柱内预留普通钢筋孔道;11—梁内预留预应力筋孔道;12—固定角钢用锚栓。
具体实施方式
下面结合图1至图4,对本发明做进一步说明:
如图1、2所示,该连接节点包括预制混凝土框架柱(1)、双向预制混凝土框架梁(2)。混凝土框架柱(1)可以多层预制或单层预制,框架柱(1)沿高度的接缝部位设置在楼层内,在梁柱节点区域则连续通过,两个方向的混凝土框架梁(2)均为单跨预制,预制框架梁(2)在节点区域间断,梁端与柱侧作为节点连接的接触面。梁端预埋钢板(6),一方面可以在吊装过程中对梁端起到保护作用,另一方面可以增强提高梁端的承压能力,减轻其在地震作用下的损坏程度。梁端钢板外侧与柱接触面之间预留20mm左右的缝隙,浇筑高强无收缩灌浆材料(7),可以使预制梁、柱在节点部位紧密贴合,并在预应力的作用下提高抗剪能力。
框架柱(1)与双向框架梁(2)通过钢筋(4)和无粘结预应力筋(3)相连接。钢筋(4)沿两个方向布置,每根钢筋穿过框架柱(1),两端固定于对应方向框架梁(2)侧,该钢筋(4)在地震作用下可以耗散地震能量,在震后易于更换。无粘结预应力筋(3)在双向框架梁(2)内通长布置,也穿过框架柱(1),并锚固于建筑两端柱侧。通过张拉双向无粘结预应力筋(3)使梁端与柱侧之间产生摩阻力以抵抗框架梁端剪力。无粘结预应力筋(3)的数量及张拉控制应力根据计算确定,应保证预应力筋(3)在相应设防烈度的罕遇地震下保持弹性。
如图1、3所示,钢筋(4)端部套丝,穿过框架柱(1)内预留的孔道(10),采用螺母固定于框架梁(2)侧面的预埋钢件(8)上。框架柱的孔道(10)内预埋钢管,钢管内径比钢筋(4)外径大2-3mm,并填充无粘结微膨胀材料,保证钢筋(4)在孔道(10)内可自由滑动。框架柱(1)孔道(10)的位置应能保证孔道内的热轧钢筋(4)可以较为容易地安装或拆卸,必要时可通过在框架梁端对应位置局部减小梁的宽度来实现。
双向框架梁(2)内中和轴附近位置沿全跨采用波纹管或薄壁钢管预留孔道(11),框架柱(1)两方向对应位置采用波纹管或薄壁钢管预留孔道(9),孔道(9)、(11)内设置无粘结预应力筋(3)。孔道(9)和(11)的内径应根据能容纳所设置的无粘结预应力筋(3)的原则确定。
如图3所示,所述框架柱内预留的双向孔道(9)和(10)应在高度上相互错开,确保两方向的钢筋(4)和无粘结预应力筋(3)顺利通过。相应地,如图1、4所示,两方向框架梁内预留的孔道(11)也应在高度上相互错开,确保预应力筋通过。
如图1所示,在预制框架柱(1)侧对应框架梁(2)底标高处设置角钢(5),通过锚栓(12)或预埋钢筋固定在框架柱(1)侧,用于预制框架梁(2)吊装时的临时支撑。当为双向框架时,该角钢(5)应沿柱的四周设置。锚栓的规格和数量根据计算确定。
具体实施步骤如下:
第一步:预制装配式框架结构的施工安装自下而上,首先吊装就位本层预制框架柱(1),然后依次吊装各跨预制框架梁(2),框架梁(2)可临时就位于柱侧角钢(5)上,同时应保证梁端与柱侧留有20mm左右的缝隙,为保证稳定性,宜采用必要的临时支撑;
第二步:无粘结预应力筋(3)现场下料,并沿两方向依次从端柱侧面的预留孔(9)中穿入无粘结预应力筋;
第三步:在每个梁柱节点部位,将事先加工好的热轧钢筋(4)穿过柱上预留孔(10),并进一步穿过框架梁的预埋钢件(8)上的孔。预留孔(10)中灌注无粘结微膨胀材料,孔口封闭;
第四步:梁端与柱侧的缝隙中浇筑高强无收缩灌浆材料(7);
第五步:高强无收缩灌浆材料(7)达到设计强度后,安装端部无粘结预应力筋锚具,并按设计控制应力进行张拉;
第六步,安装热轧钢筋(4)两端的螺母,并旋紧;
第七步,外露钢件表面封闭处理;
第八步,本层楼板安装就位;
第九步:重复上述第一步至第八步,按楼层自下而上装配完成整体结构。
上面结合附图对本发明进行了示例性的描述,显然本发明的实现并不受上述方式的限制,只要采用了本发明的方法构思和技术方案进行的各种改进,或未经改进将本发明的构思和技术方案直接应用于其它场合的,均在本发明的保护范围内。