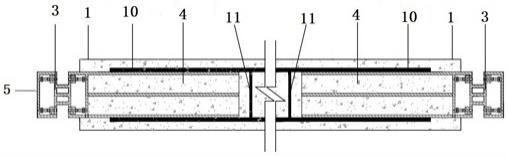
1.本实用新型属于建筑技术领域,具体涉及一种承插式预制混凝土梁。
背景技术:2.我国正处于快速推进“新型城镇化”的进程,随着我国对建筑产业的绿色低碳、节能环保、健康生态、可持续发展要求越来越高,同时伴随着劳动力日益短缺等社会问题的不断呈现,国家大力推行“建筑工业化、住宅产业化”,促进我国建筑行业的结构调整及可持续发展。而预制装配式建筑与传统现浇建造方式相比,具有具有施工方便、工程进度快、对周围环境影响小、可标准化设计、工厂化生产、现场湿作业少、环保节约能源且建筑构件的质量容易得到保证等优点,从国内外建筑业发展来看,推广和发展预制装配式混凝土结构是最便捷的途径。过去我国主要在工业建筑中应用的较多,近年来开始在民用建筑特别是住宅建筑中采用。随着我国城市化进程的加快,预制装配式建筑也迎来了新的发展契机。虽然预制装配式建筑与传统现浇建造方式具有较为宽广的前景,且工厂预制这一环节也较为成熟,预制装配式建筑相对于传统建筑具有安装速度快、节水、节地、降低噪音、节材等诸多优点。但苦于构件安装时由于存在如下问题:1、节点多为湿作业,节点内力复杂,节点的附加钢筋多,存在在钢筋绑扎、钢筋避让难度大,混凝土浇筑振捣难以达到要求,2、预制梁柱安装时,节点不能承受梁本身重量,需要另外搭设模板支架和脚手架;3、现场浇筑后要等混凝土达到一定强度后才能进行下一道施工工序,技术间歇时间长,影响施工工期,4、受以上等因素的影响,外加施工习惯和熟练程度的影响下,预制装配式建筑与传统现浇建造方式在工程造价和施工周期上并无明显优势,因此,预制装配式建筑推行并不广泛。
技术实现要素:3.为了解决上述存在的技术问题,本实用新型提供一种承插式预制混凝土梁,能够减少施工过程中的物料无辜损耗,同时减少施工现场的建筑垃圾;构件是由生产车间完成后直接运到现场装配,减少了人力需求,并且让施工人员的劳动强度有所下调。所以施工进度也会比较快,工期相对就会缩短;可在短期内交使用,劳动力减少,交叉作业方便有序;每道工序都可以像设备安装那样检查精度,保证质量;施工现场噪音小,散装物料减少。
4.为了实现上述目的,本实用新型采用的技术方案为:
5.一种承插式预制混凝土梁,承插式预制混凝土梁包括梁头抗剪传力桶、承插式梁头连接件、梁预制混凝土、传力桶现浇连接端、梁头锚固连通孔、梁头锚固连通孔侧弯部、梁头锚固连通孔侧弯部挡板包裹的空间、连接插口、梁受力主筋、梁箍筋、端连接板、自调正紧固装置、承插式梁头连接板、梁头加强连接板和传力桶预埋端,所述梁头抗剪传力桶上设有梁头锚固连通孔、所述梁头锚固连通孔两侧设有向内弯曲的梁头锚固连通孔侧弯部,所述梁头抗剪传力桶前部为端连接板,所述端连接板为u字型或平行板,所述端连接板置于柱头连接件容纳缺口内固定相连,所述梁头抗剪传力桶上设有梁头锚固连通孔,所述梁头锚固连通孔两侧设有向内弯曲的梁头锚固连通孔侧弯部,所述梁头抗剪传力桶前部为传力桶预
埋端,所述传力桶预埋端为长方形加劲传力板,位于承插式梁头连接件每侧端部,在承插式梁头连接件上设有梁连接插口,所述自调正紧固装置包括调正装置槽、内纹顶紧块、加强刚度灌浆孔、顶紧块导槽,所述调正装置槽位于承插式梁头连接件的传力桶现浇连接端,由传动丝杆支承板、顶紧块导槽板、顶紧块导槽和侧连接档板围合而成,所述顶紧块导槽板上设有内纹顶紧块,所述内纹顶紧块在垂直于顶紧块导槽板的方向上中心位置设有通孔,通孔内壁上设有顶紧块内螺纹与传动丝杆外螺纹相互配套,两个调正装置槽之间设有两个加强刚度灌浆孔,所述的加强刚度灌浆孔由承插式梁头连接板、梁头加强连接板和顶紧块导槽板围合而成,所述传动丝杆与固定螺母固定连接;所述的梁头抗剪传力筒预埋于承插式预制混凝土梁内,与梁受力主筋固定相连,梁箍筋绑扎后,经梁预制混凝土浇筑形成装配式混凝土梁整体;所述传力桶预埋端预埋在承插式预制混凝土梁()内。
6.进一步的,所述梁头锚固连通孔为原板切割或裁减开孔,为梁头抗剪传力桶侧面切割后向内弯折90
°
而成,所述切割的切割线呈h、、x型,内弯曲半径不小于板材厚度的二分之一,内弯曲长度为钢板厚度的1.5倍。
7.进一步的,所述切割线呈h型时,包括呈h型的竖向切割线、横向切割线,沿竖向切割线、横向切割线切割后梁头抗剪传力桶的侧面形成上下两个矩形弯曲部,所述两个矩形弯曲部沿其上下端部的横向弯折线向内弯折90
°
,形成梁头锚固连通孔。
8.进一步的,所述切割线呈型时,包括呈型的斜向切割线、中部横向切割线,沿斜向切割线、中部横向切割线切割后梁头抗剪传力桶的侧面形成左右两侧的三角形弯曲部一和上下两侧的梯形弯曲部,所述三角形弯曲部一和梯形弯曲部分别沿竖向弯折线及横向弯折线向内弯折90
°
,形成梁头锚固连通孔。
9.进一步的,所述切割线呈x型时,包括呈x型的对角线斜向切割线,对角线斜向切割线切割后梁头抗剪传力桶的侧面形成上下左右四个三角形弯曲部二,所述四个三角形弯曲部二分别沿竖向弯折线及横向弯折线向内弯折90
°
,形成梁头锚固连通孔。
10.进一步的,所述梁头锚固连通孔宽度不超过梁头抗剪传力桶侧面宽度的三分之一,相邻两侧面上的梁头锚固连通孔交错布置;所述梁头锚固连通孔宽度不超过梁头抗剪传力桶侧面宽度的三分之一,相邻两侧面上的梁头锚固连通孔交错布置。
11.进一步的,所述梁头抗剪传力桶为钢板、型钢材料,其截面尺寸和材料厚度依据柱截面尺寸和所承受的内力计算确定,截面为“口”字型或“田”字型或“井”字型。
12.本实用新型的优点及有益效果是:
13.本实用新型构件是由生产车间完成后直接运到现场装配,减少了人力需求,所以施工进度也会比较快,工期相对就会缩短;交叉作业方便有序,每道工序都可以像设备安装那样检查精度,保证质量;施工现场噪音小,散装物料减少,废物及废水排放减少,有利于环境保护;通过设置连接插口、调正装置槽及加强刚度灌浆孔,浇筑后实现梁头构件与柱之间的快速、稳固装配。本实用新型通过在梁头构件的传力筒上开设梁头锚固连通孔,该梁头锚固连通孔为原板切割或裁减开孔,为梁头抗剪传力筒侧面切割后向内弯折90
°
而成,首先开口的设计使整体性提高;第二是内折90度挡板,起到卡榫作用,优点是能提高抗剪能力,受力性能提高;第三是两个或四个内折90度挡板包裹的空间能形成一个有效的剪切键,提高承载力。
附图说明
14.图1为本实用新型梁头与梁连接示意图;
15.图2为梁头连接件结构示意图;
16.图3为梁头抗剪传力桶结构示意图;
17.图4为图3中a
‑
a剖面示意图;
18.图5为自调正紧固装置;
19.图6为图3中b
‑
b剖面示意图;
20.图7为梁头锚固连通孔h型切割示意图;
21.图8为梁头锚固连通孔h型切割后弯曲部示意图;
22.图9为梁头锚固连通孔型切割示意图;
23.图10为梁头锚固连通孔型切割后弯曲部示意图;
24.图11为梁头锚固连通孔x型切割示意图;
25.图12为梁头锚固连通孔x型切割后弯曲部示意图;
26.图13为梁头构件内部浇筑空间示意图。
27.图中:1为承插式预制混凝土梁;2为梁头抗剪传力桶;3为承插式梁头连接件;4为梁预制混凝土;5为传力桶现浇连接端;6为梁头锚固连通孔;6
‑
1竖向切割线、6
‑
2横向切割线、6
‑
3矩形弯曲部、6
‑
4横向弯折线、6
‑
5斜向切割线、6
‑
6中部横向切割线、6
‑
7三角形弯曲部一、6
‑
6梯形弯曲部、6
‑
9对角线斜向切割线、6
‑
10三角形弯曲部二、6
‑
11竖向弯折线;7为梁头锚固连通孔侧弯部;8为梁头锚固连通孔侧弯部挡板包裹的空间;9为连接插口;10为梁受力主筋;11为梁箍筋;12为端连接板;13为自调正紧固装置;13
‑
1为调正装置槽;13
‑
2为内纹顶紧块;13
‑
3为加强刚度灌浆孔;13
‑
4顶紧块导槽;13
‑
5为调正装置槽底挡板;13
‑
6为侧连接挡板;13
‑
7为传动丝杆支承板;13
‑
8为顶紧块导槽板;13
‑
9为顶紧块内螺纹;13
‑
10为传动丝杆外螺纹;14为承插式梁头连接板;15为梁头加强连接板;16为传力桶预埋端。
具体实施方式
28.为了进一步说明本实用新型,下面结合附图及实施例对本实用新型进行详细地描述,但不能将它们理解为对本实用新型保护范围的限定。
29.一种承插式预制混凝土梁,承插式预制混凝土梁1包括梁头抗剪传力桶2、承插式梁头连接件3、梁预制混凝土4、传力桶现浇连接端5、梁头锚固连通孔6、梁头锚固连通孔侧弯部7、梁头锚固连通孔侧弯部挡板包裹的空间8、连接插口9、梁受力主筋10、梁箍筋11、端连接板12、自调正紧固装置13、承插式梁头连接板14、梁头加强连接板15和传力桶预埋端16,所述梁头抗剪传力桶2上设有梁头锚固连通孔6、所述梁头锚固连通孔6两侧设有向内弯曲的梁头锚固连通孔侧弯部7,所述梁头抗剪传力桶2前部为端连接板12,所述端连接板12为u字型或平行板,所述端连接板12置于柱头连接件容纳缺口内固定相连,所述梁头抗剪传力桶2前部为传力桶预埋端16,所述传力桶预埋端16为长方形加劲传力板,位于承插式梁头连接件3每侧端部,在承插式梁头连接件3上设有梁连接插口9,所述自调正紧固装置13包括调正装置槽13
‑
1、内纹顶紧块13
‑
2、加强刚度灌浆孔13
‑
3、顶紧块导槽13
‑
4,所述调正装置槽13
‑
1位于承插式梁头连接件3的传力桶现浇连接端5,由传动丝杆支承板13
‑
7、顶紧块导槽板13
‑
8、顶紧块导槽13
‑
4和侧连接档板13
‑
6围合而成,所述顶紧块导槽板13
‑
8上设有内
纹顶紧块13
‑
2,所述内纹顶紧块13
‑
2在垂直于顶紧块导槽板13
‑
8的方向上中心位置设有通孔,通孔内壁上设有顶紧块内螺纹13
‑
9与传动丝杆外螺纹13
‑
10相互配套,两个调正装置槽13
‑
1之间设有两个加强刚度灌浆孔13
‑
3,所述的加强刚度灌浆孔13
‑
3由承插式梁头连接板14、梁头加强连接板15和顶紧块导槽板13
‑
8围合而成,所述内纹顶紧块13
‑
2与固定螺母固定连接;所述的梁头抗剪传力桶2预埋于承插式预制混凝土梁1内,与梁受力主筋10固定相连,梁箍筋11绑扎后,经梁预制混凝土4浇筑形成装配式混凝土梁整体;所述传力桶预埋端16预埋在承插式预制混凝土梁内。
30.所述梁头锚固连通孔6为原板切割或裁减开孔,为梁头抗剪传力桶2侧面切割后向内弯折90
°
而成,所述切割的切割线呈h、、x型,内弯曲半径不小于板材厚度的二分之一,内弯曲长度为钢板厚度的1.5倍;本技术通过在梁头构件的传力筒上开设梁头锚固连通孔,该梁头锚固连通孔为原板切割或裁减开孔,为梁头抗剪传力筒侧面切割后向内弯折90
°
而成,首先开口的设计使整体性提高;第二是内折90度挡板,起到卡榫作用,优点是能提高抗剪能力,受力性能提高;第三是两个或四个内折90度挡板包裹的空间能形成一个有效的剪切键,提高承载力。
31.所述切割线呈h型时,包括呈h型的竖向切割线6
‑
1、横向切割线6
‑
2,沿竖向切割线6
‑
1、横向切割线6
‑
2切割后梁头抗剪传力桶2的侧面形成上下两个矩形弯曲部6
‑
3,所述两个矩形弯曲部6
‑
3沿其上下端部的横向弯折线6
‑
4向内弯折90
°
,形成梁头锚固连通孔6。
32.所述切割线呈型时,包括呈型的斜向切割线6
‑
5、中部横向切割线6
‑
6,沿斜向切割线6
‑
5、中部横向切割线6
‑
6切割后梁头抗剪传力桶2的侧面形成左右两侧的三角形弯曲部一6
‑
7和上下两侧的梯形弯曲部6
‑
8,所述三角形弯曲部一6
‑
7和梯形弯曲部6
‑
8分别沿竖向弯折线6
‑
11及横向弯折线6
‑
4向内弯折90
°
,形成梁头锚固连通孔6。
33.所述切割线呈x型时,包括呈x型的对角线斜向切割线6
‑
9,对角线斜向切割线6
‑
9切割后梁头抗剪传力桶2的侧面形成上下左右四个三角形弯曲部二6
‑
10,所述四个三角形弯曲部二6
‑
10分别沿竖向弯折线6
‑
11及横向弯折线6
‑
4向内弯折90
°
,形成梁头锚固连通孔6。
34.所述梁头锚固连通孔6宽度不超过梁头抗剪传力桶2侧面宽度的三分之一,相邻两侧面上的梁头锚固连通孔6交错布置。
35.所述梁头抗剪传力桶2为钢板、型钢材料,其截面尺寸和材料厚度依据柱截面尺寸和所承受的内力计算确定,截面为“口”字型或“田”字型或“井”字型。
36.实施例:
37.施工时,承插式预制混凝土梁1能与预制混凝土柱采用承插式柔性连接方法,承插式预制混凝土梁1包括梁预制混凝土4、梁受力主筋10、梁箍筋11、承插式梁头连接件3及所述梁头构件上的自调正紧固装置13组成,承插式预制混凝土梁1两端的承插式梁头连接件3的预埋端与梁预制混凝土4锚固连接、梁受力主筋10焊接、锚固连接等方式连接,然后浇筑,分别于装配后的调正装置槽13
‑
1、连接插口9、加强刚度灌浆孔13
‑
3及筒体内均浇筑混凝土。连接板间缺口装配后形成梁头连接端浇筑部位、浇筑后的传力筒内的梁头锚固连通孔弯曲部挡板形成包裹的空间8,构成一个有效的剪切键,提高承载力;将梁受力主筋10焊接和梁箍筋11所承受的内力和剪力传递给承插式梁头连接件3,在现浇区节点内通过其两端的承插式梁头连接件3,承插式柱头连接件3采用承插式的连接方法,并通过其自调正紧固
装置13调正梁与柱的相对位置、紧固和限位,保证在安装和结构在使用受力时的稳固和安全可靠性。
38.所述的承插式梁头连接件3,包括梁头抗剪传力桶2、梁头锚固连通孔6、梁头锚固连通孔侧弯部7、梁连接板12、梁连接插口9、自调正紧固装置13组成,所述承插式梁头连接件3的传力桶预埋端16预埋在承插式预制混凝土梁1内,与梁预制混凝土4锚固连接,与梁受力主筋10焊接或锚固连接,其作用是传递梁受力主筋10所承受的内力,并代替箍筋承受构件及节点所受到的剪力,所述的承插式梁头连接件3预埋在承插式预制混凝土梁1外的传力桶现浇连接端的梁连接板12有连接插口和设有自调正紧固装置13,能够在现浇节点的处,与承插式柱头连接件的承口止档健和调正限位槽相互配合,进行承插式连接,并能够通过自调正紧固装置13和调正限位槽的相互配合,调正承插式预制混凝土梁1与承插式预制混凝土柱相对位置并紧固,使承插式预制混凝土梁1和承插式预制混凝土柱在安装和使用受力时均不产生位移和脱落,因而也提供了良好的抗震锚固。
39.以上所述仅是本实用新型的优选实施方式,应当指出,对于本技术领域的普通技术人员来说,在不脱离本实用新型原理的前提下,还可以做出若干改进和润饰,这些改进和润饰也应视为本实用新型的保护范围。