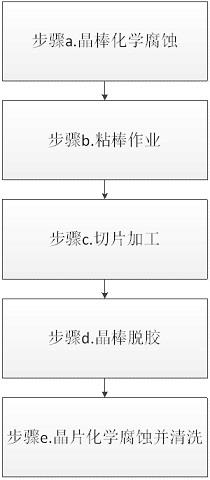
1.本发明涉及铌酸锂晶体材料,特别是一种大尺寸超薄铌酸锂晶片的切片方法。
背景技术:2.铌酸锂(linbo3,以下简称ln)是一种化学物质,属三方晶系,钛铁矿型(畸变钙钛矿型)结构,相对密度4.30g/cm3,莫氏硬度5,居里点1140℃,是集压电、铁电、热释电、非线性、光电、光弹、光折变等功能于一体的多功能材料。ln因其卓越的物理特性,得到了越来越多的关注,在航空、航天、民用光电产品等领域得到广泛应用。其中,作为压电晶体材料,经过退火、极化、定向、切割、滚圆、做基准面、多线切割、研磨、抛光等工序制作的晶片具有优良的压电性能,可作为衬底片制作声表面波(saw)和体波(baw)器件。由于目前大尺寸超薄铌酸锂晶片更能满足电子元器件小型化、片式化的需求,因此为了获得高质量的电子元器件,对大尺寸超薄铌酸锂晶片的加工工艺提出了更高的要求。
3.与硅晶体和蓝宝石晶体相比,铌酸锂的断裂韧性和硬度更低,例如其断裂韧性是硅的三分之一、蓝宝石的十分之一,因此铌酸锂晶体在加工过程中比硅晶体和蓝宝石晶体更易受损,特别是在切割工艺中,更易发生晶片碎裂、切割面平整度低、晶向偏差大、加工线痕深等问题,严重影响了研磨、抛光等后续加工工艺。另外,由于晶片尺寸越大,厚度越小,晶片加工难度就越高,这进一步加大了大尺寸超薄铌酸锂晶片在加工过程中的受损概率,从而导致晶片废品率高、加工效率低,大幅度增加了企业的生产成本。
4.公开号为cn110281408a的发明专利公开了一种硅棒的多线切割方法,在多线切割装置的切割线上附着混合酸液,解决了硅棒切割效率低的问题,但在实际情况中,切片设备都为金属材料,酸液很容易侵蚀设备,而且加工切割过程中酸液极易挥发,对环境和人体均存在安全隐患。
5.公开号为cn109808093a的发明专利公开了一种硅片切片方法,主要采用晶锭清洗,粘棒,切片机加工等方法获得完整的切割晶片,但在实际操作中铌酸锂与硅的物理性质差异很大,硅片的加工方式不适用于铌酸锂加工,加工碎片率高。
6.公开号为cn105849872b的发明专利公开了一种切片方法,主要通过镀有铜合金的钢线对晶体切割,获得切割晶片,但在实际操作中,此种切割大尺寸晶体时,晶片品质低,碎片率高。
7.因此,现有技术中缺乏一种获得高质量的大尺寸超薄铌酸锂晶片的切片方法。
技术实现要素:8.针对以上技术问题,本发明所要提供的是一种大尺寸超薄铌酸锂晶片的切片方法,该方法加工过程稳定,所获得的晶片表面平坦度高,晶向偏差小,线痕深度小,加工碎片率低。
9.本发明解决问题所采用的技术方案是:一种大尺寸超薄铌酸锂晶片的切片方法,加工工艺流程如图1所示,具体包括下列步骤:
a)将铌酸锂晶棒置于盛有硝酸和氢氟酸均匀混合溶液的密封容器中进行化学腐蚀,腐蚀温度为15℃~25℃,腐蚀时间为12~60小时,获得充分释放应力的铌酸锂晶棒;b)使用纯水和酒精依次清洗步骤a获得的充分释放应力的铌酸锂晶棒,再将晶棒与玻璃条用粘合剂固定在一起,放入夹具内,使用晶向仪校对晶棒晶向偏差,并通过机床加工对晶棒晶向进行修整,再将修整晶向后的晶棒用粘合剂固定在基准块上,最后在晶棒头尾粘上树脂片,在晶棒正上端及两侧粘上树脂条,获得待切片的铌酸锂晶棒;c)将步骤b获得的铌酸锂晶棒固定在切片机内,金刚线布置在槽间距为280μm的槽轮上,晶棒以0.05mm/min~0.20mm/min的速度缓慢下降,设备管路内切削液以80l/min~100l/min流量流出,同时携带切削液的金刚线以1500m/min~2500m/min的线速度对晶棒进行反复切割,将晶棒加工成晶片,厚度<200μm,平坦度<5μm,线痕深度<5μm,获得切片后的铌酸锂晶片;d)将步骤c获得的铌酸锂晶片置于盛有脱胶剂的溶液中,然后将溶液由常温缓慢加热至60℃~80℃进行脱胶作业,脱胶时间为0.5~2小时,获得脱胶处理后的铌酸锂晶片;e)将步骤d获得的铌酸锂晶片置于盛有硝酸和氢氟酸均匀混合溶液的密封容器中进行化学腐蚀,腐蚀温度为15℃~25℃,腐蚀时间为1~24小时,使铌酸锂晶片的翘曲度<25μm,然后将腐蚀后的晶片进行超声清洗,获得最终的大尺寸超薄铌酸锂晶片。
10.上述步骤a)中,化学腐蚀是指铌酸锂晶棒在混合酸中进行腐蚀,快速释放机械加工应力,修复晶棒表面损伤。
11.上述步骤b)中,在晶棒头尾两侧粘上树脂片,改善了晶棒在切割最后10mm过程中,最外侧晶片由于弯曲过大而碎裂及由此引发的连续碎片情况。树脂片作为一种非晶体材料,再大的弯曲也不会碎裂,同时紧贴晶棒的树脂片作为一种阻挡,防止了晶片因弯曲过大而碎裂的问题。
12.上述步骤b)中,在晶棒上端粘上树脂条,树脂条作为一种切割过渡材料,改善了金刚线切入晶棒瞬间位置偏差造成的平坦度偏差大的情况;在晶棒两侧粘树脂条,缓解了切片第一阶段金刚线切入晶棒处,由于切削液过多堆积晶片边缘所造成的晶片边缘厚度薄,平坦度偏差大的情况。
13.作为一种优选,所述步骤b)中晶棒头尾粘的树脂片厚度为3mm~5mm,晶棒正上端及两侧粘的树脂条厚度为3mm~5mm。
14.作为一种优选,上述步骤c)中,金刚线线径为60μm~80μm,制作金刚线的金刚砂粒径为6μm~8μm,切削液加工温度为15℃~25℃,铌酸锂晶棒进行切片的具体过程如下:第一阶段,晶棒以0.13mm/min速度下降,切削液流量为80l/min,金刚线以1500m/min的线速度对晶棒进行切割,随着金刚线切割面积的增加,晶棒切割超过80mm后,进入第二阶段,降低晶棒下降速度至0.08mm/min,同时将金刚线的线速度逐步提升至2000m/min以增加切割能力,并提升切削液流量至100l/min,增加切割过程中的润滑性及加速导出切割所产生的热量,铌酸锂晶棒切割过120mm后,随着切割面积的减小,进入第三阶段,增加晶棒下降速度至0.11mm/min,并将金刚线的线速度逐步降低至1700m/min,切削液流量降低至90l/min,直至完成切割。
15.上述步骤c)中,所用切削液由环烷油,石蜡油,聚乙二醇单油酸酯,膨润土,磺酸钡盐混合形成。
16.作为一种优选,所述步骤c)中组成切削液的各成分质量分数为环烷油25%~50%,石蜡油15%~35%,聚乙二醇单油酸酯15%~30%,膨润土15%~30%,磺酸钡盐5%~10%。
17.上述步骤e)中,化学腐蚀是指铌酸锂晶片在混合酸中进行腐蚀,以致快速释放机械加工应力,修复表面损伤,改善晶片翘曲度。由于晶片相对于晶棒更薄,化学腐蚀覆盖率更高,化学作用效果更好,所以所需的腐蚀时间大大降低。
18.本发明的大尺寸超薄铌酸锂晶片,晶片直径≥200mm,厚度<200μm,平坦度<5μm,翘曲度<25μm,晶向偏差<0.1
°
,线痕深度<5μm,加工碎片率<1%。
19.本发明与传统铌酸锂切片方法相比,具有的有益效果为:第一方面,在晶棒切割前进行化学腐蚀,充分释放机械应力,改善了切片过程中晶片易碎裂的问题,提升了加工良率。
20.第二方面,由于本发明粘棒时在晶棒两侧增加了树脂条,缓解了晶棒切片端切削液堆积所造成的平坦度偏差大的问题。
21.第三方面,由于本发明粘棒时在晶棒头尾两端增加了树脂片,铌酸锂晶片在切片后期不会出现因晶片弯曲大而造成批量性碎片的问题,大大提升了加工良率。
22.第四方面,由于本发明所优选切削液具有良好的润滑与冷却作用,改善了切片过程中晶片线痕深的问题,提升了加工品质。
23.第五方面,由于本发明的铌酸锂表面平坦度高,翘曲小,线痕深度小这一特征决定了铌酸锂晶片在研磨抛光加工中不易碎片,成品率高。
附图说明
24.图1为本发明加工流程示意图;图2为本发明实施例1晶棒未粘树脂条与树脂片的正视图;图3为本发明实施例1晶棒未粘树脂条与树脂片的右视图;图4为本发明实施例2晶棒头尾粘树脂片,晶棒上端粘1根树脂条的正视图;图5为本发明实施例2晶棒头尾粘树脂片,晶棒上端粘1根树脂条的右视图;图6为本发明实施例3晶棒头尾粘树脂片,晶棒上端及两侧粘3根树脂条的正视图;图7为本发明实施例3晶棒头尾粘树脂片,晶棒上端及两侧粘3根树脂条的右视图;图8为本发明实施例1、2、3不同粘棒方式与平坦度及碎片率的关系示意图;图9为本发明实施例4、5、6不同比例混合切削液与线痕深度及碎片率的关系示意图。
25.其中,1
‑
晶棒、2
‑
玻璃条、3
‑
基准块、4
‑
树脂片、5
‑
树脂条。
具体实施方式
26.下面结合实施例对本发明作进一步说明,但不应以此限制本发明的保护范围。
27.实施例1:a)将铌酸锂晶棒置于盛有硝酸和氢氟酸均匀混合溶液的密封容器中进行化学腐蚀,腐蚀温度为20℃,腐蚀时间为24小时,获得应力充分释放的铌酸锂晶棒;b)使用纯水和酒精依次清洗充分释放应力的铌酸锂晶棒,再将晶棒1与玻璃条2用粘合剂固定在一起,放入夹具内,使用晶向仪校对晶棒晶向偏差,并通过机床加工对晶棒晶
向进行修整,再将修整晶向后的晶棒1用粘合剂固定在基准块3上,在晶棒头尾不粘树脂片,上端及两侧不粘树脂条,详见图2和图3,获得待切片的铌酸锂晶棒;c)按照下述各成分的质量分数配制切削液,即环烷油40%,石蜡油30%,聚乙二醇单油酸酯15%,膨润土10%,磺酸钡盐5%,将待切片的铌酸锂晶棒进行切片作业,切片时,晶棒进给平均速度0.12mm/min,金刚线线速度1500m/min~2000m/min,切削液温度20℃,槽轮间距280μm,金刚线线径60μm,制作金刚线的金刚砂粒径6μm,钢线张力5n,切削液平均流量90l/min,获得晶片厚度195.8μm,平坦度13.2μm,表面线痕深度8.2μm,晶向偏差0.03
°
,理论投入623片,碎裂32片,碎片率5.14%,详见图8;d)将切片后的铌酸锂晶片置于20℃的脱胶溶液中,然后缓慢加热至60℃进行脱胶作业,获得脱胶处理后的铌酸锂晶片;e)将脱胶处理后的晶片置于盛有硝酸和氢氟酸均匀混合溶液的密封容器中进行化学腐蚀,腐蚀温度为20℃,腐蚀时间为3小时,使铌酸锂晶片的翘曲度18.8μm,然后将晶片进行超声清洗,获得最终的大尺寸超薄铌酸锂晶片。
28.实施例2:a)同实施例1;b)使用纯水和酒精依次清洗充分释放应力的铌酸锂晶棒1,再将晶棒1与玻璃条2用粘合剂固定在一起,放入夹具内,使用晶向仪校对晶棒晶向偏差,并通过机床加工对晶棒晶向进行修整,再将修整晶向后的晶棒1用粘合剂固定在基准块3上,最后在晶棒头尾粘上树脂片4,晶棒正上端粘1根树脂条5,详见图4和图5,获得待切片的铌酸锂晶棒;c)同实施例1,获得晶片厚度196.1μm,平坦度10.3μm,晶片表面线痕深度7.6μm,晶向偏差0.05
°
,理论投入631片,碎裂12片,碎片率1.90%,详见图8;d)同实施例1;e)同实施例1,获得翘曲度20.6μm大尺寸超薄铌酸锂晶片。
29.实施例3:a)同实施例1;b)使用纯水和酒精依次清洗充分释放应力的铌酸锂晶棒,再将晶棒1与玻璃条2用粘合剂固定在一起,放入夹具内,使用晶向仪校对晶棒晶向偏差,并通过机床加工对晶棒晶向进行修整,再将修整晶向后的晶棒1用粘合剂固定在基准块3上,最后在晶棒头尾粘树脂片4,上端及两侧共粘3根树脂条5,详见图6和图7,获得待切片的铌酸锂晶棒;c)同实施例1,获得晶片厚度196.2μm,平坦度4.5μm,表面线痕深度7.1μm,晶向偏差0.04
°
,理论投入611片,碎裂10片,碎片率1.64%,详见图8;d)同实施例1;e)同实施例1,获得翘曲度19.2μm的大尺寸超薄铌酸锂晶片。
30.对比实施例1、2、3,如图8和表1所示,在晶棒头尾粘上树脂片,加工碎片率明显下降,在晶棒上端及两侧共粘3根树脂条,晶片平坦度明显降低。
31.表1 实施例1、2、3的晶片效果数据
实施例4:a)同实施例1;b)同实施例3;c)按照下述各成分的质量分数配制切削液,即环烷油40%,石蜡油25%,聚乙二醇单油酸酯15%,膨润土15%,磺酸钡盐5%,将待切片的铌酸锂晶棒用进行切片作业,切片时,晶棒进给平均速度0.08mm/min,金刚线线速度1500m/min~2000m/min,切削液温度20℃,槽轮间距280μm,金刚线线径60μm,金刚砂粒径6μm,钢线张力5n,切削液流量平均90l/min,使晶棒加工成晶片,厚度195.8μm,平坦度4.4μm,晶片表面线痕深度5.3μm,理论投入623片,碎裂7片,碎片率1.12%,详见图9;d)同实施例1;e)同实施例1,获得翘曲度18.6μm的大尺寸超薄铌酸锂晶片。
32.实施例5:a)同实施例1;b)同实施例3;c)按照下述各成分的质量分数配制切削液,即环烷油35%,石蜡油25%,聚乙二醇单油酸酯20%,膨润土15%,磺酸钡盐5%,将待切片的铌酸锂晶棒用进行切片作业,切片时,晶棒进给平均速度0.08mm/min,金刚线线速度1500m/min~2000m/min,切削液温度20℃,槽轮间距280μm,金刚线线径60μm,制作金刚线的金刚砂粒径6μm,钢线张力5n,切削液平均流量90l/min,使晶棒加工成晶片,厚度195.8μm,平坦度4.6μm,晶片表面线痕深度4.1μm,理论投入616片,碎裂5片,碎片率0.81%,详见图9;d)同实施例1;e)同实施例1,获得翘曲度19.4μm的大尺寸超薄铌酸锂晶片。
33.实施例6:a)同实施例1;b)同实施例3;c) 按照下述各成分的质量分数配制切削液,即环烷油35%,石蜡油20%,聚乙二醇单油酸酯20%,膨润土20%,磺酸钡盐5%,将待切片的铌酸锂晶棒用进行切片作业,切片时,晶棒进给平均速度0.08mm/min,金刚线线速度1500m/min~2000m/min,切削液温度20℃,槽轮
间距280μm,金刚线线径60μm,制作金刚线的金刚砂粒径6μm,钢线张力5n,切削液平均流量90l/min,使晶棒加工成晶片,厚度196.2μm,平坦度4.5μm,晶片表面线痕深度6.8μm,理论投入635片,碎裂6片,碎片率0.94%,详见图9;d)同实施例1;e)同实施例1,获得翘曲度19.2μm的大尺寸超薄铌酸锂晶片。
34.对比实施例4、5、6,如图9和表2所示,使用切削液的成分质量分数为环烷油35%,石蜡油25%,聚乙二醇单油酸酯20%,膨润土15%,磺酸钡盐5%加工的晶片,加工线痕深度最小。
35.表2 实施例4、5、6的晶片效果数据尽管已经示出和描述了本发明的实施例,对于本领域的普通技术人员而言,可以理解在不脱离本发明的原理和精神的情况下可以对这些实施例进行多种变化、修改、替换和变型,本发明的范围由所附权利要求及其等同物限定。