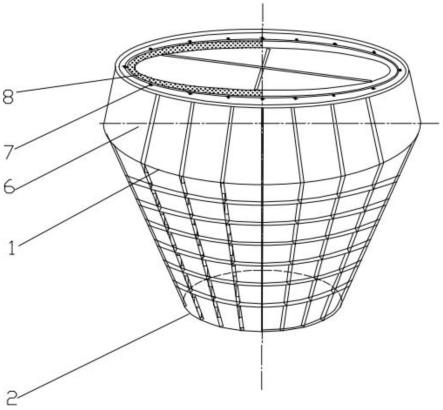
1.本实用新型涉及建筑施工领域,具体是一种锥形花池柱薄壳筒体。
背景技术:2.为了满足现代建筑功能及建筑风格的需要,曲面筒体结构得到了日益广泛的应用,但是现有情况制作曲线支架构件不仅对施工操作人员的技术要求很高,难以保证施工质量,而且工效极低,无法满足现代化的建筑施工进度要求。
技术实现要素:3.本实用新型所要解决的技术问题是提供一种锥形花池柱薄壳筒体,可以有效解决上述背景技术中提出的问题。
4.为解决上述问题,本实用新型所采取的技术方案是:一种锥形花池柱薄壳筒体,包括第一筒体、第二筒体和内衬模板,其特征在于,所述第一筒体的底部和顶部设有环形模板;所述第二筒体的底部和顶部也设有环形模板;所述第一筒体顶部的环形模板与第二筒体底部的环形模板连接;所述第一筒体和第二筒体均设有外壁挡板模板;所述外壁挡板模板分别环绕设置在第一筒体和第二筒体的内侧,且外壁挡板模板的内壁处设有曲面造型模板;所述内衬模板套接在第一筒体和第二筒体内。
5.作为本实用新型的进一步优选方案,所述第一筒体底部和顶部的环形模板通过第一支撑筋连接,且第一支撑筋预定间隔倾斜分布;所述第二筒体底部和顶部的环形模板通过第二支撑筋连接,且第二支撑筋预定间隔倾斜分布。
6.作为本实用新型的进一步优选方案,所述第一支撑筋与第二支撑筋的倾斜角度为水平对称;所述第一支撑筋设有环形箍楞。
7.作为本实用新型的进一步优选方案,所述内衬模板位于曲面造型模板旁,且内衬模板与外壁挡板模板形成封闭的空腔。
8.作为本实用新型的进一步优选方案,所述外壁挡板模板为胶合板。
9.作为本实用新型的进一步优选方案,所述环形模板的宽度为5cm-30cm,厚度为10cm-30cm。
10.与现有技术相比,本实用新型提供了一种锥形花池柱薄壳筒体,具备以下有益效果:
11.该装置施工简便、可以在保证施工质量前提下显著提高工效、降低施工成本,混凝土结构成型观感好,能够循环利用。
附图说明
12.图1为第一筒体形成方法之一示意图。
13.图2为第一筒体形成方法之二示意图。
14.图3为本发明一个实施例的筒体外支撑安装示意图。
15.图4为实施例的第一筒体曲面造型模板定位示意图。
16.图5为图4曲面造型模板安装示意图。
17.图6为第一筒体与第二筒体连接安装示意图。
18.图7为整体薄壳筒体外支撑安装完成示意图。
19.图8为整体薄壳筒体体内钢筋安装示意图。
20.图9为内支撑安装完成示意图。
具体实施方式
21.下面将结合本实用新型实施例中的附图,对本实用新型实施例中的技术方案进行清楚、完整地描述,显然,所描述的实施例仅仅是本实用新型一部分实施例,而不是全部的实施例。
22.参照图1-9,本实用新型提供一种锥形花池柱薄壳筒体,包括第一筒体和第二筒体,其特征在于,包括第一筒体、第二筒体和内衬模板,其特征在于,所述第一筒体的底部和顶部设有环形模板;所述第二筒体的底部和顶部也设有环形模板;所述第一筒体顶部的环形模板与第二筒体底部的环形模板连接;所述第一筒体和第二筒体均设有外壁挡板模板;所述外壁挡板模板分别环绕设置在第一筒体和第二筒体的内侧,且外壁挡板模板的内壁处设有曲面造型模板;所述内衬模板套接在第一筒体和第二筒体内。
23.作为本实用新型的进一步优选方案,所述第一筒体顶部的环形模板的直径与第二筒体底部的环形模板的直径相等;所述第一筒体底部的环形模板的直径比第一筒体顶部的环形模板的直径小;所述第二筒体顶部的环形模板的直径比第二筒体底部的环形模板的直径小,比第一筒体底部的环形模板的直径大。
24.作为本实用新型的进一步优选方案,所述第一筒体的底部和顶部的环形模板通过第一支撑筋连接,且第一支撑筋预定间隔倾斜分布;所述第二筒体的底部和顶部的环形模板通过第二支撑筋连接,且第二支撑筋预定间隔倾斜分布。
25.作为本实用新型的进一步优选方案,所述第一支撑筋与第二支撑筋的倾斜角度为水平对称;所述第一支撑筋设有环形箍楞。
26.作为本实用新型的进一步优选方案,所述内衬模板位于曲面造型模板旁,且内衬模板与外壁挡板模板形成封闭的空腔。
27.作为本实用新型的进一步优选方案,所述外壁挡板模板为胶合板;所述胶合板的宽度为30mm~150mm。
28.作为本实用新型的进一步优选方案,所述环形模板的宽度为15cm-20cm,厚度为10cm-20cm。
29.作为本实用新型的进一步优选方案,所述第一筒体和第二筒体的外壁支撑均采用木楞板垂直交叉固定;薄壳筒体的整体内、外壁支撑的倾斜方向一致,所述外壁挡边条固定间距、倾斜方向一致。
30.作为本实用新型的一个具体实施例: 一种锥形花池柱薄壳筒体的施工方法,其制作按如下步骤进行:
31.第一步、设计构造线—参考图1,在待建锥形薄壳筒体的三维几何图形上建立环绕且位于锥形筒体上、按预定间隔分布、由两组不同方向空间直线垂直交叉形成的环形网格
构造线;本步骤借助solidworks等三维机械制图软件,可建立锥形筒体的仿真三维模型,并确定筒体上垂直方向任一点均可延伸至桶底投影中心点,从而形成作为锥形筒体施工放线控制依据的网格构造线。
32.第二步、环形模板制作定位—参考图2,用10-20cm厚模板条制作第一筒体底部的环形模板1和顶部的环形模板2,定位楞板3等分作中间部位环撑定位线,按等分线制作安装筒壁的环形模板结构,环形模板宽度在15-20cm,纵向固定的楞板也应均匀分布,保证有足够的支撑力,如图3所示。
33.第三步、安装薄壳筒体外壁挡边模板—按所述网格构造线方向,参照图5纵向间隔铺设附着在环形模板上且与之垂直相交的条块状外壁挡边模板5,挡边采用宽度在50~100mm的胶合板,铺设时应注意拼缝应符合要求,并采用镀锌铁皮封盖,防止浇筑砼时漏浆;外壁挡边模板5的支撑均采用木楞板垂直交叉固定,外壁挡边条固定间距、倾斜方向一致。
34.第四步、安装第一筒体壁外造型模板—如图4所示,将第一筒体底部的环形模板1和顶部的环形模板2等分,根据曲面构造要求铺设附着在内壁上的曲面造型模板4,参照图5,直至第一筒体内形成完整的曲面构造,曲面造型模板4的表面均采用镀锌铁皮包封,保证拆模后观感和周转率。
35.第五步、安装第二筒体构造—如图6所示,根据标高要求,按所述第一筒体安装步骤三、四、五对应安装第二筒体6,与第一筒体形成整体的薄壳筒体-参考图7。
36.第六步、绑扎薄壳筒体内壁钢筋—如图8所示,根据整体薄壳筒体内部的曲面造型模板4的形状,等距制作内壁模板7,将内壁模板7套接到薄壳筒体内,且在内壁模板7上按第一筒体的厚度要求绑扎钢筋,构成双曲面钢筋层,并放置厚度与筒壁厚度要求相同控制件,厚度控制件用a12钢筋点焊而成,在曲面造型模板4上间隔布置。
37.第七步、安装薄壳筒体内模板—如图9所示,按所述薄壳筒体的构造,参照图8制作内衬模板8,直至形成完整的薄壳筒体内表面,内衬模板8表面8均采用镀锌铁皮包封,保证拆模后观感和周转率;内衬模板8的作用在于与外壁挡板模板形成封闭空腔,保证混凝土浇筑成型。
38.第八步、安装薄壳筒体内支撑—在薄壳筒体内模板中横向固定支撑固连的木支撑,木支撑环形布置保证整体性;其中薄壳筒体的内、外壁支撑的倾斜方向一致。
39.第九步、浇筑混凝土—在内衬模板8和外壁挡板模板5之间浇筑混凝土并振捣密实、养护;为了保证支撑系统稳定性,应选用天泵进行混凝土浇筑,浇筑过程中振捣持续时间应使混凝土表面产生浮浆,无气泡,不下沉为止,混凝土浇筑应振捣密实。
40.第十步、拆除模板—模板拆除时的混凝土强度应能保证其表面及棱角不受损伤。拆除的模板和支架及时清运,以便再用。
41.以上实施例仅用以说明本实用新型的技术方案,而非对其限制;尽管参照前述实施例对本实用新型进行了详细的说明,本领域的普通技术人员应当理解:其依然可以对前述实施例所记载的技术方案进行修改,或者对其中部分技术特征进行等同替换;而这些修改或者替换,并不使相应技术方案的本质脱离本实用新型实施例技术方案的精神和范。