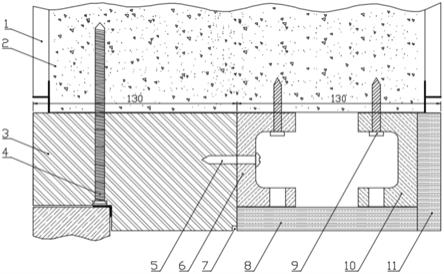
1.本实用新型涉及竹门框领域,尤其涉及一种模块化竹门框。
背景技术:2.随着近年环保理念的不断推行,竹产品行业作为木制产品的替代开始发展。竹制门框有其比大部分木门框更高的强度、硬度和更好的外观、质感,而且无门套实竹门框的设计更符合业主的简洁、厚实的审美需求,因而逐渐为高端业主和设计师接受和应用。但在实际应用过程中,业主提供安装的实际墙体厚度会因为墙体预制、粉刷找平、贴瓷砖等过程中的多种因素,产生很多尺寸规格。这样势必要求有很多种宽度的竹门框型号。现有的设计和组装方法是按照墙体的标准尺寸预先设计出竹门框的宽度,但因为墙预制施工后现场墙体实际尺寸和预先设计尺寸的不一致,导致按照预先设计尺寸生产出来的门框在宽度方向和墙体厚度有明显差异而无法匹配。进而导致偏宽的门框需要返厂拆除后再加工,偏薄的门框只能通过再改造墙体变薄后安装、或者干脆报废重新生产符合最新尺寸的门框。这在成本和时效性上都影响了整体工程项目指标的达成。也有方法是待墙体和贴瓷砖等工序全部完成后,再通过为每种不同规格的竹门框配置不同尺寸的定制刀具来加工这些竹门框以达到实际需求。这种方法无法事先生产导致工程项目周期延长,而且会占用大量昂贵的四面刨设备机台数(如果利用少数机台却要不断的切换刀具、工装夹具并需要不断的调试校准,进而导致生产周期进一步延长)。影响了加工的生产效率和工程项目进度及成本。
3.因此,本领域的技术人员致力于开发一种模块化竹门框,利用不同宽度竹门框的规律,将无门套的竹门框设计成统一宽度的标准竹门框、竹板及可调结构,通过模块化的组合达到不同竹门框宽度匹配不同墙体厚度的要求。
技术实现要素:4.有鉴于现有技术的上述缺陷,本实用新型所要解决的技术问题是:如何解决竹门框的适配问题,以符合不同墙体厚度的需求。
5.为实现上述目的,本实用新型提供了一种模块化竹门框,包括:标准门框模块、左内撑模块、右内撑模块和l型板;所述标准门框模块固定连接在所述左内撑模块的左侧,所述右内撑模块设置在所述左内撑模块的右侧,所述l型板连接在所述右内撑模块的右侧和外侧。
6.进一步地,所述右内撑模块和所述左内撑模块之间具有间隙,所述间隙可调。
7.进一步地,所述l型板包括可截宽平竹板和侧竹板模块;所述可截宽平竹板位于所述右内撑模块和所述左内撑模块的下侧,所述侧竹板模块位于所述右内撑模块的右侧。
8.进一步地,所述可截宽平竹板设置在所述准门框模块的右侧,所述准门框模块和可截宽平竹板之间设有工艺缝。
9.进一步地,所述标准门框模块通过钢钉安装在墙体上,使得所述标准门框模块上侧面与所述墙体的下侧面重合。
10.进一步地,所述墙体设有粉刷墙面,所述标准门框模块的左侧面与所述粉刷墙面的左侧面处于同一平面。
11.进一步地,所述左内撑模块和所述右内撑模块均通过小钢钉固定在所述墙体的下侧面。
12.进一步地,所述左内撑模块通过自攻木螺丝和所述标准门框模块固定。
13.进一步地,所述可截宽平竹板的上侧面与所述左内撑模块和所述右内撑模块下侧面用胶水粘合。
14.进一步地,所述侧竹板模块的左侧面与所述右内撑模块和所述可截宽平竹板的右侧面用胶水粘合。
15.与现有技术相比,本实用新型至少具有如下有益技术效果:
16.本实用新型在整体竹门框高度、宽度和款式一致的情况下,实现不同宽度的竹门框生产和组装的互换;机械化生产竹门框的过程中,大幅减少刀具和工装的配置和投入;降低了在机械化生产竹门框的过程中切换、调试、校准刀具的频次,提高生产效率;适合施工现场墙体厚度的多样化,杜绝因门框宽度导致的返厂返工、返修甚至报废;确保强度等功能和外观的同时,从设计上减少大尺寸竹材的使用量;机械化生产竹门框的过程中,从技术上实现连续生产,降低对昂贵的四面刨设备的需求量;机械化生产竹门框的过程中,实现连续生产并提高对昂贵的四面刨设备的利用率。本实用新型实现竹门框由项目制的定制化生产向标准化的批量化生产的跨越;缩短竹门框材料的生产周期;具备事先备安全库存应对紧急需求的条件;直接或间接降低材料、刀具工装、设备、加工、组装、安装等成本。
17.以下将结合附图对本实用新型的构思、具体结构及产生的技术效果作进一步说明,以充分地了解本实用新型的目的、特征和效果。
附图说明
18.图1是本实用新型的模块化竹门框示意图;
19.图2是本实用新型的可调内撑和l型板的部件示意图;
20.图3是本实用新型的整体竹门框示意图;
21.其中:1
‑
粉刷墙面;2
‑
墙体;3
‑
标准门框模块;4
‑
钢钉;5
‑
自攻木螺丝;6
‑
左内撑模块;7
‑
工艺缝;8
‑
可截宽平竹板;9
‑
小钢钉;10
‑
右内撑模块;11
‑
侧竹板模块。
具体实施方式
22.以下参考说明书附图介绍本实用新型的优选实施例,使其技术内容更加清楚和便于理解。本实用新型可以通过许多不同形式的实施例来得以体现,本实用新型的保护范围并非仅限于文中提到的实施例。
23.在附图中,结构相同的部件以相同数字标号表示,各处结构或功能相似的组件以相似数字标号表示。附图所示的每一组件的尺寸和厚度是任意示出的,本实用新型并没有限定每个组件的尺寸和厚度。为了使图示更清晰,附图中有些地方适当夸大了部件的厚度。
24.如图1所示,本实用新型实施例提供的一种模块化竹门框,包括标准门框模块3、可调内撑和l型板,可调内撑包括左内撑模块6和右内撑模块10,l型板包括可截宽平竹板8和侧竹板模块11,其中标准门框模块3、左内撑模块6、可截宽平竹板8、右内撑模块10、侧竹板
模块11作为竹门框模块化设计和组装的核心部分。墙体2设有粉刷墙面1,左内撑模块6通过自攻木螺丝5固定安装在标准门框模块3上,标准门框模块3通过钢钉4安装在墙体上;左内撑模块6和右内撑模块20均通过小钢钉9 固定在所述墙体的下侧面。右内撑模块10和左内撑模块6之间具有可调间隙,通过调节右内撑模块10的位置,起到对竹门框宽度的无级调节作用,并且预设计和加工了工艺缝7,避免标准门框模块3和可截宽平竹板8的加工高度公差引起的目视效果。
25.单侧门框安装步骤如下:
26.通过钢钉4将标准门框模块3安装在墙体2上,使得标准门框模块3左侧面与粉刷墙面1的左侧面在相同平面,并且使得标准门框模块3上侧面与墙体2的下侧面重合;
27.通过自攻木螺丝5将左内撑模块6和标准门框模块3固定,通过小钢钉9将左内撑模块6和墙体2固定;
28.调节左内撑模块6与右内撑模块10之间的间隙,通过小钢钉9将右内撑模块10 和墙体2固定;
29.将可截宽平竹板8与左内撑模块6及右内撑模块10用胶水粘合,将侧竹板模块 11与右内撑模块10及可截宽平竹板8用胶水粘合。
30.如图2所示的可调内撑及l型板模块化结构,调节左内撑模块6和右内撑模块10 之间间隙为wδmm,并配合侧竹板模块11及截取75+wδmm宽的可截宽平竹板8,即能与标准门框模块3组装成总宽为220+wδmm的竹门框,进而可以和粉刷墙面1 及墙体2组成的整体厚度220+wδmm的墙很好的匹配。参见表1,为适配现场任意的墙总厚度220+wδmm,wδ可以从0至70mm间的任意值调整。
31.表1.竹门框尺寸调节对照表(单位mm)
32.序号门框总宽度标准门框宽模块宽度应调节间隙可截宽平竹板宽度1220+wδ13090+wδwδ75+wδ2220130900753260130130401154275.5130145.555.5120.5529013016070145
33.适配整体厚度220mm墙的实施案例:调节左内撑模块6和右内撑模块10之间间隙为0,并配合75mm宽的可截宽平竹板8及侧竹板模块11,即能与标准门框模块3 组装成总宽为220mm的竹门框,进而可以和粉刷墙面1及墙体2组成的整体厚度 220mm的墙很好的匹配。
34.适配整体厚度290mm墙的实施案例:调节左内撑模块6和右内撑模块10之间间隙为70mm,并配合145mm宽的可截宽平竹板8及侧竹板模块11,即能与标准门框模块3组装成总宽为290mm的竹门框,进而可以和粉刷墙面1及墙体2组成的整体厚度290mm的墙很好的匹配。
35.适配整体厚度260mm墙的实施案例:调节左内撑模块6和右内撑模块10之间间隙为40mm,并配合115mm宽的可截宽平竹板8及侧竹板模块11,即能与标准门框模块3组装成总宽为260mm的竹门框,进而可以和粉刷墙面1及墙体2组成的整体厚度 260mm的墙很好的匹配。
36.适配整体厚度277.5mm墙的实施案例:调节左内撑模块6和右内撑模块10之间间隙为55.5mm,并配合120.5mm宽的可截宽平竹板8及侧竹板模块11,即能与标准门框模块3组装成总宽为277.5mm的竹门框,进而可以和粉刷墙面1及墙体2组成的整体厚度277.5mm的墙很
好的匹配。
37.如图3所示的整体竹门框示意图,另一侧门框及顶部门框结构和安装方式相同,参照上述单侧门框安装步骤完成安装即可。
38.本实用新型整体竹门框高度和宽度一致的情况下,实现了针对不同墙体厚度的模块化竹门框生产和组装的互换性。以我公司402扇门框的一个项目为例(本实用新型均以此项目为例),因现场墙体实际厚度尺寸和预先设计的尺寸不一致,原竹门框的设计是在220~290mm之间每隔5mm定制生产一种宽度规格的竹门框共15种,即便这样每边墙和门框仍然有
±
1.25mm(=5/2/2)的平面落差;为了掩盖此肉眼明显可见的落差,需额外预埋铝合金条制造出宽和深各10mm的工艺缝。本实用新型将此15种不同规格的竹门框,设计成130mm的标准宽度的标准门框模块3和侧竹板模块11及可供现场截取宽度的可截宽平竹板8。通过模块化的组合用标准门框模块3和可截宽平竹板8及侧竹板模块11形成的可调内撑及l型竹板模块化结构(尺寸只受加工精度影响
±
0.5mm),使每边墙和门框的平面落差减少到
±
0.25mm(=0.5*2/2/2),从技术上实现了与不同墙体厚度的完好匹配。因为使用了标准门框模块3宽度统一为130mm,从而实现了竹门框生产和组装的互换。
39.本实用新型刀具配置少,因本实用新型将竹门框设计成130mm的标准宽度,无需根据不同宽度定制不同的成型加工刀具和多种工装,只需要使用同一种130mm的成型刀和一套工装,可截宽平竹板8及侧竹板模块11在价格低的更高效的平面刨设备上完成。最大程度的精简了成型刀具和工装数量(由15把压刨上刀、15把平刨下刀和15 套工装减少为各1套),不但大幅度减少了费用的投入约19376元(=14*2个面*(平均500元每个成型刀具+平均24个刀片每把刀具*8元每个刀片)),而且降低了刀具和工装的维护和管理成本约93%(=14/15*100%)。因只需要使用同一种130mm的成型刀和一套工装,机械化生产竹门框的过程中,大幅度减少了因刀具、工装的多样化而频繁进行的切换、调试、校准工作量约93%(=14/15*100%);而且减少了使用四面刨设备的加工面积约38.8%[=2*130l/(2*75l+2*260l)]。以本项目中常用的门款宽度 260mm为例计算(本实用新型均以此款门款为例计算节约材料、提高效率、缩短周期等),本实用新型的设计方法直接提高了生产效率。
[0040]
本实用新型通过模块化的组合选用标准宽度的标准门框模块3辅以可调内撑及l 型板模块化结构,可以通过现场切割可截宽平竹板8实现宽度不一致的需求,很好的适配施工现场粉刷墙面1和墙体2厚度的多样化。即便墙体上下有小于10mm的倾斜不垂直,本实用新型也可以通过现场斜线切割可截宽平竹板8的方式来确保模块化组装竹门框和粉刷墙面1大平面重合。而现有整体加工竹门框的方案无法现场适配,必须返厂利用大型木工设备进行返工、返修甚至报废。本实用新型通过模块化竹门框分体设计大幅减少了原整体设计对大尺寸竹方的需要,节约了竹材。确保强度等功能及外观要求满足的同时,因本实用新型的模块化设计和组装方法,节约了竹材35.4%[= (130
‑
15)*(75
‑
15)/(260*75)]。机械化生产过程中,因统一了竹门框的标准宽度规格,从技术上实现了单机台连续生产而非多机台平行生产,仅需配置一台四面刨设备就可大量生产标准规格的竹门框用的方竹料,降低了对昂贵的四面刨设备的需求量。因统一了竹门框的标准宽度规格,使标准宽度的竹门框满足单机台连续生产的数量需求。实现连续机械化生产,提高了对昂贵的四面刨设备的利用率33.3%(=2/6*100%)(按照每次切换、校准刀具和工装,并试制首样,共耗时2小时)。因宽度方向可互换等,竹门框材料加工的连续大批量生产,实现了竹门框由项目制的定制化
生产为标准化的批量化生产的跨越,而无需对现场墙体施工提出过高的要求。
[0041]
本实用新型的设计和组装方法,因为设备利用率高、生产效率高、可连续批量生产,在节约管理成本的同时缩短了生产周期11.2天[=2/(8
‑
2)*402*(1+1+0.5)/30],(按照每次切换、校准刀具和工装并试制首样,共耗时2小时;四面刨260mm宽2500mm 长的竹方一班8小时加工产量30根计算);通过竹门框规格减少到一种标准规格,所以具备了提前生产事先备安全库存的条件,可以应对紧急需求。本实用新型减少了竹材使用量、对大截面整竹材的需求、浪费、刀具和工装投入、设备需求量,提高了生产效率、设备利用率,可现场适配等,直接或间接降低了材料、刀具工装、设备、加工、组装、安装、运输等成本,直接成本节约总计约172000.00元。
[0042]
以上详细描述了本实用新型的较佳具体实施例。应当理解,本领域的普通技术无需创造性劳动就可以根据本实用新型的构思作出诸多修改和变化。因此,凡本技术领域中技术人员依本实用新型的构思在现有技术的基础上通过逻辑分析、推理或者有限的实验可以得到的技术方案,皆应在由权利要求书所确定的保护范围内。