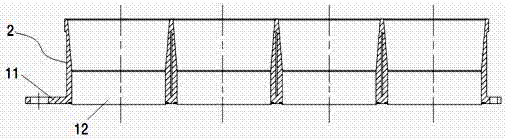
本实用新型涉及汽车发动机安装技术领域,特别涉及一种活塞安装设备。
背景技术:
目前,汽车发动机基本采用手工方式将活塞安装到气缸缸孔内,活塞包括活塞本体及活塞环,手工安装方法为:使用活塞导套作为导向,然后使用橡胶锤逐缸将活塞敲击进入缸套内。这样的安装方式有以下不足:1、使用橡胶锤敲击活塞时因力度不同,容易损坏活塞环及缸套,进而影响活塞、缸套的使用寿命和发动机正常运转;2、逐缸安装效率低、费时费力。
技术实现要素:
本实用新型要解决的问题是将四个活塞同时均匀压进缸套内,避免活塞及缸套在安装过程中因力度不同而受损伤,且提高活塞的安装效率。
针对上述问题,本实用新型采取以下技术方案。活塞安装设备,包括固定板、活塞导套、支架和压进杆,其特征在于,所述固定板并排设置有环体,环体的中间设置有通孔,两端环体的侧边设置有耳片;所述固定板上的环体上面固定连接有活塞导套,且活塞导套与固定板的通孔同轴;所述活塞导套的上段内孔为喇叭口状,内孔的下段内孔为直孔,直孔的内径与缸套的内径相匹配;所述支架呈“П”形,支架的支脚下端与两端的活塞导套外侧固定连接,支架的横梁中间安装有压进杆,压进杆为螺杆结构,压进杆的一端设置有螺杆头,另一端与过渡板中间设置的套筒连接,过渡板的下面并排设置有推进杆,推进杆与活塞导套相对应。
优选地,所述上段内孔的孔壁与轴线的夹角为4.5~7°。
优选地,所述螺杆头为正六边形或方形。
优选地,所述螺杆头设置有通孔,通孔内安装有手柄。
本实用新型的优点是:在安装活塞时,四个活塞可同时均匀的压进缸套内,避免活塞、缸套在安装过程中受损伤,且大大提高安装效率,节省人力。
附图说明
图1是本实用新型的立体结构示意图。
图2是本实用新型中的活塞导套剖视图。
图3是本实用新型中固定板1的立体示意图。
图中:1.固定板,11.耳片,12.通孔,13.环体,2.活塞导套,3.推进杆,4.过渡板,41.套筒,5.支架51.支脚,52.横梁,6.压进杆。
具体实施方式
以下结合附图和实施例对本实用新型作进一步说明。参见图1,活塞安装设备,包括固定板1、活塞导套2、支架5和压进杆6,其特征在于,所述固定板1并排设置有环体13,环体13的中间设置有通孔12,两端环体13的侧边设置有耳片11;所述固定板1上的环体13上面固定连接有活塞导套2,且活塞导套2与固定板1的通孔12同轴对应;所述活塞导套2的上段内孔为喇叭口状,上段内孔的孔壁与轴线的夹角α为4.5~7°,下段内孔为直孔,直孔的内径与缸套的内径相匹配;所述支架5呈“П”形,支架5的支脚51下端与两端的活塞导套2外侧固定连接,支架5的横梁52中间安装有压进杆6,压进杆6为螺杆结构,压进杆6的一端设置有螺杆头,螺杆头为正六边形、方形或在螺杆头加工一通孔,通孔内安装有手柄;另一端与过渡板4中间设置的套筒41连接,过渡板4的下面并排设置有推进杆3,推进杆3与活塞导套2相对应。
实施例:本实用新型固定板1并排设置有环体13,环体13的中间设置有通孔12,两端的侧边设置有耳片11;固定板1上面的环体13并排固定焊接有活塞导套2,活塞导套2与固定板1上的通孔12同轴对应,活塞导套2的内孔上段为喇叭口状,上段内孔的孔壁与轴线的夹角α为5°,通孔12的孔径与活塞导套2的内孔下段直径相等,通孔12的孔径与缸套的内径相匹配;所述支架5呈“П”形,支架5的支脚51下端与两端的活塞导套2外侧固定焊接连接,支架5的横梁52中间安装有压进杆6,压进杆6为螺杆结构,压进杆6的一端头设置有螺杆头;另一端头与过渡板4中间设置的套筒41连接,过渡板4的下面并排设置有推进杆3,推进杆3与活塞导套2同轴线相对应。在安装活塞时,通过螺栓将固定板1的耳片11固定在缸体上,将四个活塞同时放入活塞导套2内,然后使用气动扳手转动螺杆6,螺杆6转动使过渡板4及推进杆3向下运动,实现四个活塞同时均匀压进缸套内。与以前安装活塞方式对比:避免了安装过程中因敲击力不同而损坏活塞、缸套,且四个活塞同时安装进缸,大大的提高了安装效率。